Dans un monde où l’optimisation des performances et la réduction des coûts sont essentielles, les innovations en technologie de maintenance jouent un rôle de plus en plus crucial. Loin des méthodes traditionnelles, la maintenance industrielle a évolué vers des approches plus sophistiquées et prédictives, permettant aux entreprises d’anticiper les pannes, de prolonger la durée de vie des équipements, et d’améliorer la sécurité des opérations. Cet article explore comment ces innovations transforment le paysage industriel, offrant aux entreprises des outils puissants pour rester compétitives et durables.
Table of Contents
Partie 1 : Le Contexte de l’Évolution de Technologie de Maintenance Industrielle
Les Enjeux de la Maintenance Traditionnelle
- Temps d’arrêt coûteux : Dans les approches traditionnelles, les pannes sont souvent découvertes après qu’elles se sont produites, entraînant des arrêts imprévus de la production. Ces interruptions sont non seulement coûteuses, mais elles affectent également la planification et la logistique de l’entreprise.
- Difficulté à planifier les interventions : L’absence de données en temps réel rend difficile la planification efficace des interventions de maintenance. Les équipes de maintenance doivent souvent se baser sur des calendriers fixes ou des inspections visuelles, ce qui peut conduire à des interventions inutiles ou à des pannes non détectées.
- Manque de visibilité sur l’état des équipements : Les méthodes traditionnelles offrent une visibilité limitée sur l’état réel des équipements, rendant difficile la détection des anomalies avant qu’elles ne deviennent des pannes majeures.
L’Émergence de la Maintenance Prédictive
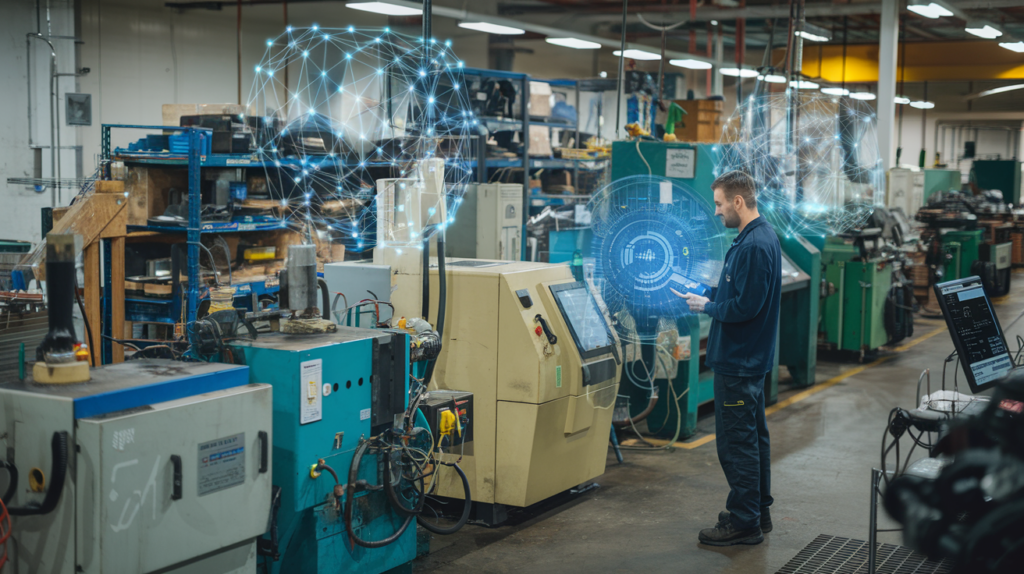
- Concept et avantages : La maintenance prédictive repose sur l’utilisation de capteurs et de technologies avancées pour surveiller en temps réel l’état des équipements. Les données collectées sont analysées pour anticiper les pannes avant qu’elles ne surviennent, permettant ainsi de planifier les interventions de manière optimale.
- Exemple concret : L’entreprise a réussi à réduit ses temps d’arrêt de 30 % en adoptant des technologies de maintenance prédictive, ce qui a conduit à une économie annuelle de 500 000 euros.
- Les facteurs clés de son succès : Le succès de la maintenance prédictive repose sur la qualité des données collectées, la précision des algorithmes d’analyse, et l’intégration des systèmes de maintenance dans l’ensemble de l’écosystème industriel.
Partie 2 : Les Innovations en technologie de maintenance
L’Internet des Objets (IoT)
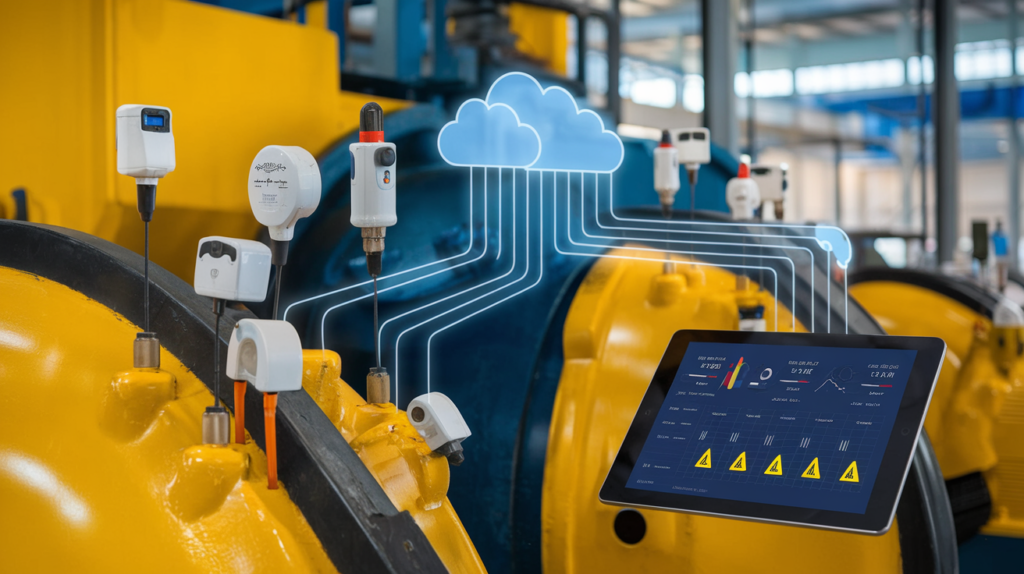
- Les capteurs intelligents et la collecte de données : Les capteurs IoT permettent de collecter des données en temps réel sur des paramètres tels que la température, la vibration, et l’humidité. Ces données sont ensuite transmises à des systèmes centralisés pour une analyse continue.
- Statistique : Selon une étude récente, l’adoption de l’IoT dans l’industrie a permis de réduire les pannes non planifiées de 40 % .
- Applications dans la maintenance (surveillance en temps réel, alertes précoces) : Grâce à l’IoT, il est possible de surveiller en temps réel l’état des équipements et de recevoir des alertes précoces en cas d’anomalies, permettant ainsi d’intervenir avant que la panne ne survienne.
L’Intelligence Artificielle (IA)
- L’analyse prédictive pour anticiper les pannes : L’IA analyse les données collectées par les capteurs pour identifier des schémas de défaillance et prédire les pannes potentielles. Ces analyses permettent de cibler précisément les interventions de maintenance.
- Exemple concret : General Electric (GE) a utilisé l’IA pour prédire une panne majeure sur une ligne de production, économisant ainsi des centaines de milliers d’euros en coûts de réparation.
- L’apprentissage automatique pour améliorer les modèles : Les modèles d’IA s’améliorent continuellement grâce à l’apprentissage automatique, en se basant sur les données historiques et les nouvelles informations recueillies, ce qui permet d’affiner la précision des prédictions.
- Les applications de l’IA dans la maintenance (diagnostic, optimisation) : L’IA est également utilisée pour diagnostiquer les causes profondes des pannes et optimiser les processus de maintenance, réduisant ainsi le temps d’intervention et les coûts associés.
Les Jumeaux Numériques
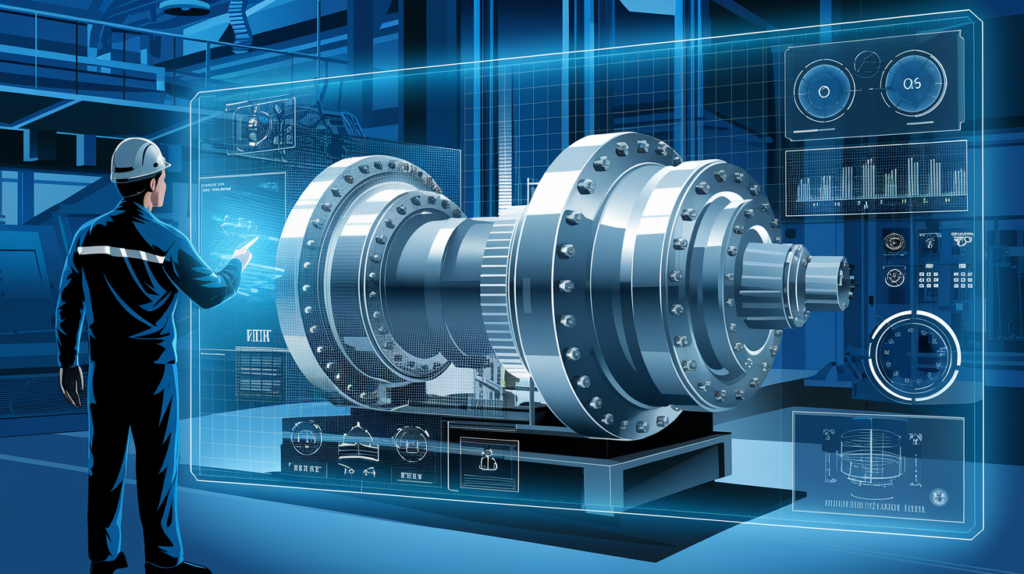
- Concept et avantages : Les jumeaux numériques sont des répliques virtuelles d’équipements physiques, permettant de simuler et d’analyser les conditions réelles de fonctionnement en temps réel. Ils facilitent la prévision des anomalies et l’optimisation des processus.
- Statistique : L’adoption des jumeaux numériques a permis une réduction des coûts de maintenance de 20 % dans certaines entreprises .
- Applications dans la simulation et l’optimisation des processus : En simulant différentes conditions et scénarios, les jumeaux numériques permettent d’anticiper les défaillances potentielles et de tester les solutions avant leur mise en œuvre sur les équipements réels.
Les Technologies d’Inspection Avancées
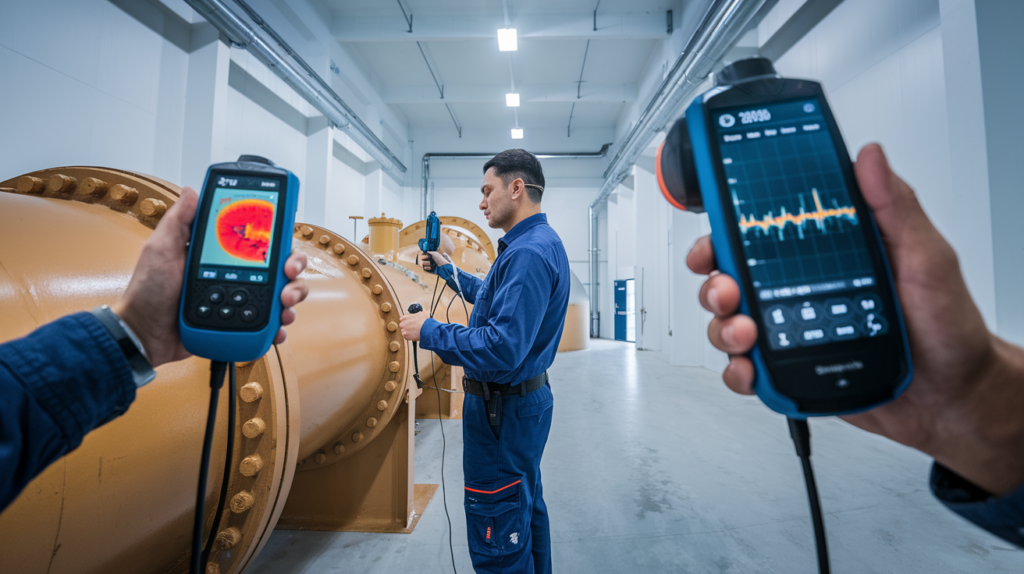
- Thermographie infrarouge, analyse vibratoire, ultrasons : Les technologies d’inspection avancées, comme la thermographie infrarouge, l’analyse vibratoire, et les ultrasons, permettent une évaluation précise et non invasive de l’état des équipements, facilitant ainsi la détection précoce des problèmes.
- Amélioration de la précision des diagnostics : Ces technologies améliorent considérablement la précision des diagnostics, permettant de cibler avec précision les zones à risque et de planifier des interventions plus efficaces.
Partie 3 : Les Impacts des Innovations sur la Maintenance
Optimisation de la Maintenance
- Réduction des coûts : En prévoyant les pannes et en optimisant les interventions, les technologies de maintenance innovantes permettent de réduire les coûts opérationnels en minimisant les arrêts imprévus et en prolongeant la durée de vie des équipements.
- Statistique : L’utilisation de la maintenance prédictive a réduit les coûts de maintenance de 15 % pour l’entreprise.
- Augmentation de la disponibilité des équipements : La maintenance prédictive augmente la disponibilité des équipements en réduisant le temps d’arrêt non planifié, ce qui améliore la productivité globale de l’usine.
- Amélioration de la sécurité : En détectant les problèmes avant qu’ils ne deviennent critiques, ces innovations contribuent à améliorer la sécurité des opérations en évitant les accidents potentiels liés à des pannes soudaines.
Transformation des Métiers
- Nouvelles compétences requises : L’intégration de nouvelles technologies dans la maintenance industrielle nécessite de nouvelles compétences, notamment en matière de gestion de données, d’analyse prédictive, et de maintenance de systèmes automatisés.
- Exemple concret : Les techniciens de maintenance ont suivi une formation spécialisée en analyse de données pour s’adapter aux nouvelles exigences du métier.
- Collaboration homme-machine : Les innovations technologiques favorisent une collaboration accrue entre l’homme et la machine, où les techniciens de maintenance sont assistés par des outils intelligents et des systèmes automatisés pour une meilleure efficacité.
Développement Durable
- Réduction de l’empreinte environnementale : Les technologies de maintenance innovantes contribuent à réduire l’empreinte environnementale en optimisant l’utilisation des ressources et en minimisant les déchets générés par des pannes et des remplacements non planifiés.
- Statistique : L’adoption de la maintenance prédictive a permis de réduire les déchets industriels de 25 % dans une entreprise de production de pièces automobiles.
Partie 4 : Les Défis et Perspectives
Les Défis de l’Implémentation
- Coût des investissements : L’intégration de technologies de maintenance avancées requiert des investissements initiaux conséquents, ce qui peut constituer un obstacle pour certaines entreprises, notamment les PME.
- Qualité des données : La réussite de la maintenance prédictive repose sur la qualité des données collectées. Des données incomplètes ou incorrectes peuvent entraîner des prédictions erronées et des interventions inappropriées.
- Sécurité des données : Avec l’augmentation de la connectivité et de la collecte de données, la sécurité des informations devient un enjeu crucial. Les entreprises doivent s’assurer que leurs systèmes sont protégés contre les cyberattaques.
- Changement culturel : L’adoption de nouvelles technologies nécessite un changement culturel au sein des entreprises, où les équipes doivent être prêtes à intégrer de nouveaux outils et méthodes de travail.
Les Perspectives d’Avenir
- Maintenance autonome : L’avenir de la maintenance industrielle pourrait voir l’émergence de systèmes entièrement autonomes, capables de surveiller, diagnostiquer, et réparer les équipements sans intervention humaine.
- Intégration de la Blockchain : La blockchain pourrait jouer un rôle crucial dans la sécurisation et la traçabilité des données de maintenance, assurant ainsi une transparence totale dans les interventions et les décisions prises .
- Rôle de l’IA : L’IA continuera à jouer un rôle central, avec des modèles de plus en plus sophistiqués capables de prédire les pannes avec une précision encore plus grande, et même de proposer des solutions de réparation optimisées en temps réel.
Conclusion
Les innovations en technologie de maintenance représentent une révolution pour l’industrie, offrant des possibilités sans précédent pour améliorer l’efficacité, la sécurité, et la durabilité des opérations. Cependant, elles posent également des défis importants, notamment en termes d’investissement et de gestion du changement. Pour les entreprises prêtes à relever ces défis, l’avenir s’annonce prometteur, avec des gains significatifs en termes de compétitivité et de performance.
Sources :
- Siemens Case Study – Siemens Energy
- GE Digital – GE Digital
- Deloitte Insights – Deloitte
- Statista – Statista
- McKinsey & Company – McKinsey
- Forbes – Forbes