Imaginez-vous en train de gérer une usine où une machine essentielle tombe en panne de manière inattendue, paralysant toute la chaîne de production. Les pertes financières s’accumulent, les délais de livraison sont compromis, et les clients deviennent impatients. Cette situation coûteuse aurait pu être évitée grâce à la maintenance conditionnelle, une approche moderne qui permet de surveiller l’état des équipements en temps réel et d’intervenir avant qu’une panne ne survienne. Cet article explore pourquoi la maintenance conditionnelle est cruciale dans l’industrie moderne, ses avantages, les techniques employées, et comment elle transforme la gestion des équipements industriels.
Table of Contents
Partie 1 : Comprendre de l’importance de la Maintenance Conditionnelle
Qu’est-ce que la Maintenance Conditionnelle ?
La maintenance conditionnelle est une stratégie proactive de gestion des équipements, fondée sur la surveillance continue de leur état. Contrairement à la maintenance préventive, qui suit un calendrier fixe, ou à la maintenance corrective, qui intervient après une panne, la maintenance conditionnelle repose sur l’état réel des équipements. Elle utilise des technologies avancées pour détecter les signes de défaillance imminente, permettant une intervention ciblée et efficace.
Exemple concret : Prenons l’exemple d’une ligne de production automobile. Au lieu d’arrêter les machines tous les trois mois pour une maintenance préventive, les capteurs surveillent en continu les vibrations, la température, et l’usure des pièces critiques. Si un capteur détecte une anomalie, une intervention est programmée uniquement si nécessaire, évitant ainsi les arrêts inutiles .
Les Principes de la Maintenance Conditionnelle
La maintenance conditionnelle s’appuie sur trois principes fondamentaux :
- Surveillance en Temps Réel : Utilisation de capteurs et d’outils de diagnostic pour surveiller en permanence les paramètres critiques des équipements. Exemple : Une centrale électrique utilise des capteurs thermographiques pour surveiller les points chauds sur les équipements, ce qui permet d’intervenir avant qu’une surchauffe ne cause une panne .
- Analyse des Données : Collecte et traitement des données pour identifier les tendances, les anomalies, et prédire les défaillances. Exemple : Dans l’industrie pétrolière, les capteurs d’analyse vibratoire sont couramment utilisés pour surveiller les pompes et compresseurs. Les données recueillies permettent d’anticiper les problèmes mécaniques avant qu’ils n’entraînent des arrêts de production coûteux .
- Intervention Basée sur l’État : Les actions de maintenance industrielle sont déclenchées uniquement lorsque les données indiquent un risque de défaillance. Exemple : Les chemins de fer britanniques utilisent la maintenance conditionnelle pour surveiller l’état des rails et des trains. Des interventions sont déclenchées lorsque des dégradations sont détectées, réduisant ainsi les retards et augmentant la sécurité .
Partie 2 : Les Avantages de la Maintenance Conditionnelle
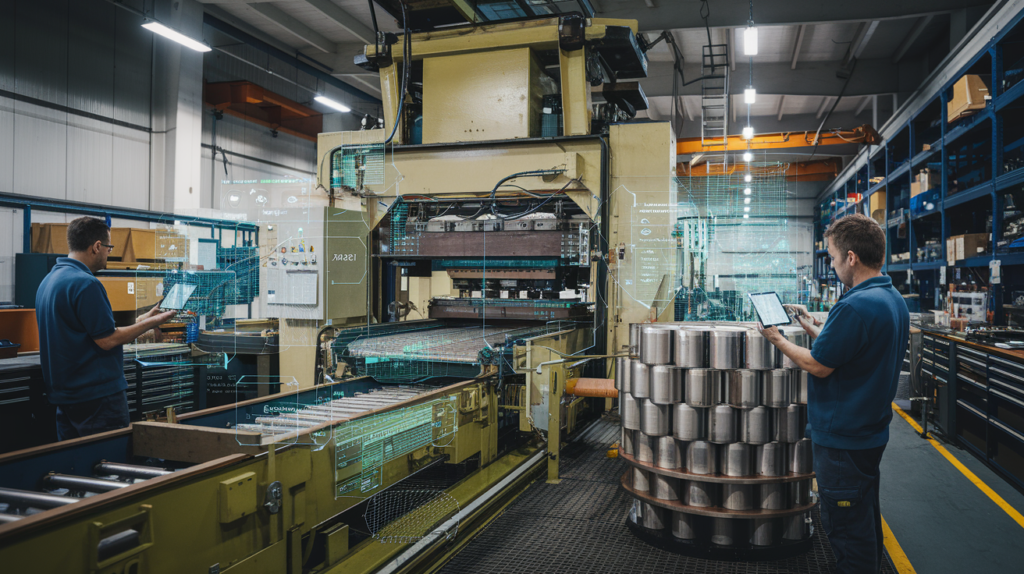
Optimisation de la Production
La maintenance conditionnelle permet de réduire les temps d’arrêt imprévus, augmentant ainsi la disponibilité des équipements. En surveillant les machines en temps réel, les entreprises peuvent planifier les interventions au moment opportun, minimisant ainsi les interruptions de production.
Exemple concret : General Electric (GE) utilise la maintenance conditionnelle pour surveiller ses turbines éoliennes. Grâce à cette approche, GE a réussi à réduire les temps d’arrêt de 20%, augmentant ainsi l’efficacité globale de ses parcs éoliens .
Réduction des Coûts
Cette approche permet de diminuer les coûts de maintenance en évitant les interventions inutiles et en prolongeant la durée de vie des équipements. Les entreprises économisent non seulement sur les réparations, mais aussi sur les pertes liées aux temps d’arrêt.
Exemple concret : Airbus a intégré la maintenance conditionnelle pour ses avions, réduisant ainsi de 30% les coûts de maintenance grâce à une gestion optimisée des interventions .
Amélioration de la Sécurité
La détection précoce des anomalies permet de prévenir les accidents, protégeant ainsi les travailleurs et réduisant les risques pour l’entreprise. En identifiant les problèmes avant qu’ils ne deviennent critiques, la maintenance conditionnelle améliore la sécurité globale de l’environnement de travail.
Exemple concret : Dans l’industrie minière, la maintenance conditionnelle est utilisée pour surveiller les équipements lourds, permettant d’éviter les pannes catastrophiques qui pourraient mettre en danger les travailleurs .
Prise de Décision Éclairée
Grâce à des données fiables et en temps réel, les gestionnaires peuvent prendre des décisions mieux informées concernant la planification des interventions, l’affectation des ressources, et l’optimisation des processus.
Exemple concret : Dans l’industrie chimique, les entreprises utilisent des plateformes basées sur l’IA pour analyser les données de maintenance conditionnelle. Cela leur permet de prendre des décisions plus stratégiques, réduisant les coûts et améliorant la performance globale .
Partie 3 : Les Techniques de la Maintenance Conditionnelle
Les Outils de Surveillance
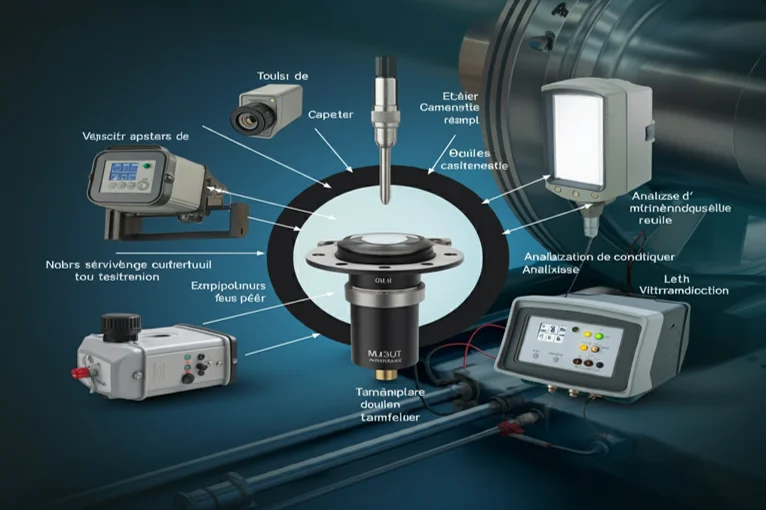
La maintenance conditionnelle utilise divers outils de surveillance pour évaluer l’état des équipements :
- Analyse Vibratoire : Détection des vibrations anormales qui pourraient indiquer des problèmes mécaniques. Exemple concret : Chevron utilise l’analyse vibratoire pour surveiller ses pipelines. Cette technique a permis de prévenir plusieurs incidents majeurs en détectant des vibrations anormales bien avant qu’elles ne causent des dommages .
- Thermographie Infrarouge : Identification des points chauds sur les équipements électriques ou mécaniques. Exemple concret : Dans une usine de fabrication de semi-conducteurs, la thermographie infrarouge est utilisée pour surveiller les composants critiques, ce qui a permis de réduire de 15% les défaillances liées à la surchauffe .
- Analyse d’Huile : Vérification de la contamination ou de la dégradation des lubrifiants. Exemple concret : Caterpillar utilise l’analyse d’huile pour surveiller l’état de ses engins de construction. Cette méthode a permis de prolonger la durée de vie des machines de 20% en détectant et en traitant les contaminants à temps .
- Analyse Ultrasonique : Détection des fuites ou des anomalies invisibles à l’œil nu. Exemple concret : Boeing utilise l’analyse ultrasonique pour inspecter ses avions. Cette technique a permis de détecter des microfissures avant qu’elles ne deviennent critiques, améliorant ainsi la sécurité des vols .
L’Analyse des Données
L’analyse des données joue un rôle crucial dans la maintenance conditionnelle. Les données collectées par les capteurs sont traitées et analysées pour identifier des tendances ou des anomalies. L’intelligence artificielle (IA) peut être utilisée pour améliorer la précision des diagnostics et prédire les pannes avec une grande fiabilité.
Exemple concret : Rolls-Royce utilise l’analyse de données avancée pour surveiller ses moteurs d’avion en temps réel. L’IA permet de prévoir les pannes des composants critiques avec une précision impressionnante, réduisant ainsi les retards et les coûts de maintenance .
Partie 4 : Mise en Œuvre de la Maintenance Conditionnelle
Les Étapes Clés de la Mise en Œuvre
La mise en œuvre réussie de la maintenance conditionnelle repose sur plusieurs étapes :
- Identification des Équipements Critiques : Priorisation des machines dont la défaillance aurait un impact significatif sur la production. Exemple concret : Dans une usine de production automobile, les robots de soudure sont identifiés comme critiques. La maintenance conditionnelle est d’abord mise en place pour ces machines, réduisant ainsi les interruptions coûteuses de la ligne de production .
- Choix des Technologies Adaptées : Sélection des outils de surveillance les plus appropriés pour chaque type d’équipement. Exemple concret : Dans le secteur de l’énergie, les éoliennes offshore sont équipées de capteurs de vibration et de thermographie pour surveiller leur état en continu, ce qui a permis de réduire les interventions non planifiées .
- Collecte et Analyse des Données : Mise en place d’un système efficace pour capturer et interpréter les données. Exemple concret : Dans une raffinerie de pétrole, les données de plusieurs milliers de capteurs sont centralisées et analysées en temps réel pour prévoir les pannes potentielles et optimiser la maintenance .
- Développement de Modèles Prédictifs : Utilisation de modèles basés sur l’IA pour prévoir les pannes potentielles. Exemple concret : Siemens utilise des modèles prédictifs pour ses systèmes de transport, réduisant les pannes de 30% grâce à une planification plus efficace des interventions .
- Mise en Place d’un Système de Suivi et d’Alertes : Établissement d’un protocole pour notifier les équipes lorsque des actions de maintenance sont nécessaires. Exemple concret : Une usine de fabrication de produits chimiques a mis en place un système d’alertes automatisé qui prévient les ingénieurs dès qu’une anomalie est détectée, permettant ainsi une intervention rapide .
Conclusion
La maintenance conditionnelle représente un atout majeur pour l’industrie, permettant de réduire les coûts, d’optimiser la production, et d’améliorer la sécurité. En adoptant cette approche, les entreprises peuvent non seulement prolonger la durée de vie de leurs équipements, mais aussi renforcer leur compétitivité sur le marché. Pour réussir cette transition, il est essentiel de comprendre les principes clés, de choisir les bonnes technologies, et de s’appuyer sur des données précises et des analyses avancées.
Sources
- General Electric, “How GE’s Digital Wind Farm Can Increase Energy Output by up to 20%,” GE Reports.
- Airbus, “Airbus Pioneers Predictive Maintenance,” Airbus Newsroom.
- Chevron, “Vibration Analysis Prevents Major Incidents in Pipelines,” Chevron Technology.
- Rolls-Royce, “Powering the Future: How Rolls-Royce is Transforming Engine Maintenance with Big Data,” Rolls-Royce.
- Siemens, “Using Predictive Analytics to Keep Trains on Track,” Siemens Mobility.
- Caterpillar, “Extending Machine Life with Oil Analysis,” Caterpillar.