L’évaluation du système de maintenance est un processus crucial pour toute entreprise industrielle cherchant à optimiser ses performances et réduire ses coûts opérationnels. Cet article explore en détail les méthodes et critères pour évaluer efficacement un système de maintenance industrielle, en mettant l’accent sur les meilleures pratiques actuelles et les indicateurs clés de performance.
Table of Contents
1. L’importance de l’évaluation du système de maintenance
1.1 Pourquoi évaluer votre système de maintenance ?
L’évaluation régulière de votre système de maintenance est essentielle pour plusieurs raisons :
- Garantir la fiabilité et la disponibilité des équipements : Garantir la fiabilité et la disponibilité des équipements signifie que les machines et les installations sont toujours prêtes à fonctionner lorsqu’elles sont nécessaires, sans interruption imprévue. Cela est crucial pour maintenir des niveaux élevés de production et de productivité.
- Optimiser les coûts de maintenance : L’optimisation des coûts de maintenance consiste à gérer efficacement les ressources pour réduire les dépenses sans compromettre la qualité ou la performance des équipements. Cela inclut la planification de la gestion de la maintenance préventive, la gestion des pièces de rechange et l’amélioration des processus.
- Améliorer la sécurité des installations : Améliorer la sécurité des installations implique de minimiser les risques d’accidents et de pannes catastrophiques qui pourraient mettre en danger la vie des travailleurs et causer des dommages matériels importants. La sécurité est un aspect critique de la maintenance industrielle.
- Prolonger la durée de vie des actifs : Prolonger la durée de vie des actifs signifie maximiser l’utilisation des équipements avant qu’ils ne nécessitent un remplacement. Cela est possible grâce à des programmes de maintenance préventive et prédictive qui identifient et traitent les problèmes avant qu’ils ne deviennent graves.
- Assurer la conformité réglementaire : Assurer la conformité réglementaire consiste à respecter les lois et les normes en vigueur qui régissent les opérations de maintenance et la sécurité des équipements. La non-conformité peut entraîner des sanctions légales, des amendes et des fermetures temporaires ou permanentes des installations.
Exemple concret : Selon une étude de l’AFIM (Association Française des Ingénieurs et responsables de Maintenance), les entreprises qui mettent en place une évaluation régulière de leur système de maintenance peuvent réduire leurs coûts de maintenance jusqu’à 20% et augmenter la disponibilité de leurs équipements de 5 à 10%.
Source : AFIM – Les enjeux de la maintenance industrielle
1.2 Les moments clés pour réaliser une évaluation
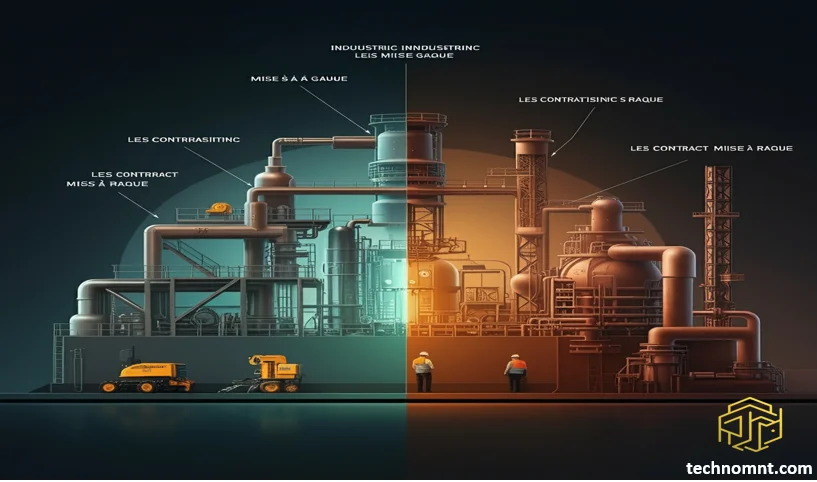
Il est recommandé de procéder à une évaluation du système de maintenance dans les situations suivantes :
- Tout au long du cycle de vie des installations
- Avant la prise en charge ou à la fin d’un contrat de maintenance
- Lors d’un arbitrage technique suite à un dysfonctionnement majeur
- En cas de litige sur l’application des conditions contractuelles
- Dans le cadre d’un projet d’acquisition
- Lors de l’établissement de budgets prévisionnels de maintenance
Exemple concret : Lors de l’acquisition d’une nouvelle usine, la société XYZ a réalisé une évaluation complète du système de maintenance existant. Cette évaluation a permis d’identifier des équipements critiques nécessitant une mise à niveau urgente, évitant ainsi des arrêts de production potentiellement coûteux dans les mois suivant l’acquisition.
2. Les critères d’évaluation d’un système de maintenance industrielle
2.1 L’état des installations techniques
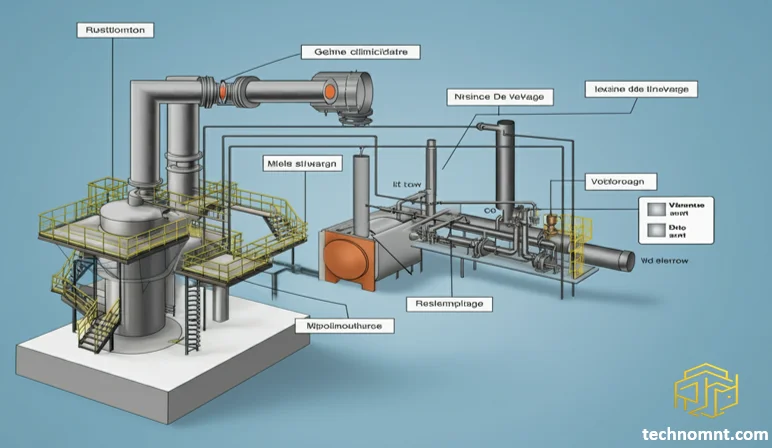
2.1.1 Évaluation par domaine
- Génie climatique
- Équipements de levage
- Installations de sécurité
- Systèmes électriques
Exemple concret : Dans une centrale électrique, l’évaluation du système de maintenance des turbines a révélé que le programme de maintenance préventive était insuffisant, entraînant une usure prématurée des pales. La mise en place d’un nouveau programme de maintenance basé sur l’analyse vibratoire a permis d’augmenter la durée de vie des turbines de 25%.
Source : Power Engineering – Predictive Maintenance for Turbines
2.1.2 Évaluation par famille d’équipements
- Chauffage
- Plomberie
- Ascenseurs
- Groupes électrogènes
Exemple concret : Dans un hôpital, l’évaluation du système de maintenance des ascenseurs a montré que 30% des pannes étaient dues à des problèmes de portes. L’installation de capteurs de mouvement plus sensibles et un programme de maintenance préventive renforcé ont permis de réduire les pannes liées aux portes de 50%.
2.2 Les indicateurs clés de performance (KPI)
2.2.1 Le système KMIS (Key Maintenance Indicators System)
Le KMIS est un référentiel reconnu qui permet d’évaluer de manière objective la qualité de la maintenance. Il se base sur une méthodologie accréditée selon la norme européenne EN 45004.
Source : SOCOTEC – Évaluation de la qualité de la maintenance
2.2.2 Les principaux KPI à surveiller
Ces KPI sont essentiels pour optimiser les opérations de maintenance, améliorer la fiabilité des équipements, et réduire les coûts associés aux temps d’arrêt et aux réparations.
- Taux de disponibilité des équipements
- Définition : Pourcentage de temps pendant lequel les équipements sont opérationnels et disponibles pour la production par rapport au temps total prévu.
- Importance : Indique la fiabilité des équipements et leur capacité à être en service sans interruption.
- Temps moyen entre les pannes (MTBF)
- Définition : Durée moyenne de fonctionnement des équipements entre deux pannes successives.
- Importance : Utilisé pour évaluer la fiabilité des équipements. Un MTBF élevé indique des équipements plus fiables.
- Temps moyen de réparation (MTTR)
- Définition : Durée moyenne nécessaire pour réparer un équipement après une panne.
- Importance : Permet de mesurer l’efficacité des processus de maintenance et la réactivité des équipes de maintenance.
- Coût de maintenance par unité de production
- Définition : Coût total de la maintenance divisé par le nombre d’unités produites.
- Importance : Utilisé pour analyser l’efficacité économique des opérations de maintenance. Un coût plus faible peut indiquer une meilleure gestion de la maintenance.
- Taux de respect du planning de maintenance préventive
- Définition : Pourcentage de tâches de maintenance préventive effectuées dans les délais prévus par rapport au nombre total de tâches planifiées.
- Importance : Indique le niveau de conformité avec le plan de maintenance préventive industrielle, ce qui peut affecter la performance et la durabilité des équipements.
Exemple concret : Une usine automobile a utilisé ces KPI pour évaluer son système de maintenance. Elle a constaté que son MTTR était 30% plus élevé que la moyenne de l’industrie. En analysant les causes, elle a identifié un manque de formation des techniciens sur certains équipements spécifiques. Après avoir mis en place un programme de formation ciblé, le MTTR a été réduit de 25% en six mois.
Source : Plant Engineering – Key Performance Indicators for Maintenance
3. Les méthodes d’évaluation du système de maintenance
3.1 L’audit interne
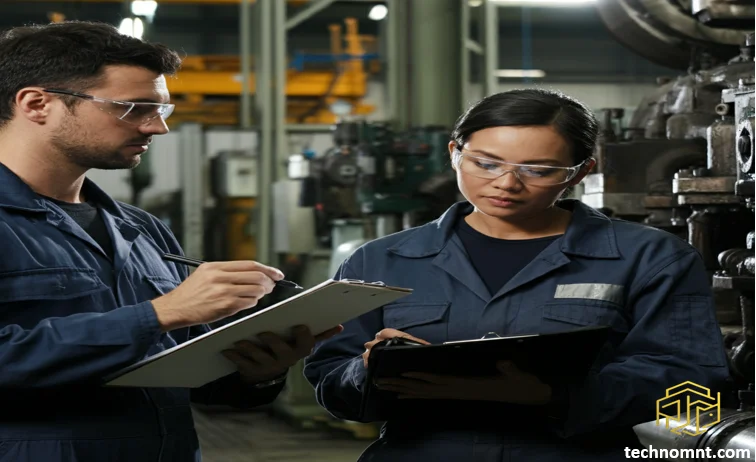
3.1.1 Avantages de l’audit interne
- Connaissance approfondie des installations
- Description : Les auditeurs internes travaillent au sein de l’organisation et possèdent une compréhension détaillée des installations, des processus et des systèmes en place.
- Avantage : Leur connaissance approfondie permet d’identifier plus facilement les problèmes potentiels et les zones d’amélioration, car ils sont déjà familiers avec les spécificités de l’organisation.
- Coût réduit
- Description : Contrairement à l’audit externe, l’audit interne n’implique pas de frais supplémentaires pour engager des consultants ou des auditeurs externes.
- Avantage : Les coûts sont réduits car l’organisation utilise ses propres ressources pour effectuer l’audit de maintenance industrielle, ce qui peut être particulièrement avantageux pour les entreprises ayant des budgets limités.
- Facilité de mise en œuvre
- Description : Les audits internes peuvent être planifiés et exécutés de manière flexible selon les besoins de l’organisation.
- Avantage : Cela permet une mise en œuvre plus rapide et plus souple des audits, car il n’est pas nécessaire de coordonner avec des parties externes. Les ajustements peuvent être faits rapidement en cas de besoin.
Ces avantages font de l’audit interne un outil précieux pour les organisations cherchant à améliorer leurs opérations et à garantir la conformité tout en minimisant les coûts et en maximisant l’efficacité.
Exemple concret : L’entreprise ABC a mis en place un programme d’audit interne trimestriel de son système de maintenance. Cette approche a permis d’identifier rapidement une tendance à la hausse des pannes sur une ligne de production spécifique, conduisant à une intervention préventive qui a évité un arrêt majeur de la production.
3.2 L’audit externe
3.2.1 Avantages de l’audit externe
- Regard neuf et objectif
- Description : Les auditeurs externes viennent de l’extérieur de l’organisation et n’ont pas d’attaches ni de préjugés concernant les opérations internes.
- Avantage : Leur perspective impartiale et objective permet d’identifier des problèmes ou des inefficacités que les employés internes pourraient ignorer ou considérer comme normaux. Cela peut conduire à des recommandations plus impartiales et potentiellement plus efficaces.
- Expertise spécialisée
- Description : Les auditeurs externes sont souvent des experts dans leur domaine avec une vaste expérience et des certifications professionnelles.
- Avantage : Leur expertise spécialisée apporte des connaissances approfondies et des pratiques de pointe, ce qui peut aider à résoudre des problèmes complexes et à mettre en œuvre des améliorations significatives dans l’organisation.
- Benchmarking avec d’autres industries
- Description : Les auditeurs externes travaillent avec diverses organisations et industries, ce qui leur donne une vision globale des pratiques et des standards de performance.
- Avantage : Ils peuvent comparer les pratiques de l’organisation auditée avec celles d’autres entreprises du même secteur ou d’autres industries, fournissant ainsi des idées et des recommandations basées sur les meilleures pratiques observées ailleurs. Cela peut aider l’organisation à rester compétitive et à adopter des méthodes éprouvées.
Ces avantages font de l’audit externe un complément précieux aux audits internes, apportant des perspectives nouvelles et des compétences spécialisées qui peuvent grandement bénéficier à l’organisation.
Exemple concret : Une raffinerie a fait appel à un cabinet d’audit externe spécialisé dans la maintenance industrielle. L’audit a révélé que leur programme de maintenance prédictive était en retard par rapport aux meilleures pratiques du secteur. La mise en œuvre des recommandations de l’audit a permis de réduire les arrêts non planifiés de 15% sur l’année suivante.
Source : Reliable Plant – Benefits of External Maintenance Audits
4. L’analyse des résultats et la prise de décision
4.1 Interprétation des données d’évaluation
- Identification des points forts et des axes d’amélioration
- Comparaison avec les standards de l’industrie
- Analyse des tendances sur le long terme
Exemple concret : Une entreprise de production alimentaire a utilisé l’analyse des données de son évaluation de maintenance pour identifier que 40% de ses équipements de réfrigération fonctionnaient en dehors des plages de température optimales. Cette découverte a conduit à un programme de remplacement échelonné, réduisant la consommation d’énergie de 20% et améliorant la qualité des produits.
4.2 Élaboration d’un plan d’action
4.2.1 Priorisation des actions correctives
- Hiérarchisation des interventions selon leur urgence et leur impact
- Estimation des coûts et des bénéfices attendus
Exemple concret : Suite à une évaluation complète, une usine chimique a identifié 15 actions d’amélioration potentielles. En utilisant une matrice de priorisation basée sur l’impact sur la sécurité et la production, l’entreprise a sélectionné les 5 actions les plus critiques à mettre en œuvre immédiatement, réduisant ainsi les risques d’incidents de 30% dans les six mois suivants.
Source : Maintenance and Engineering – Prioritizing Maintenance Actions
5. Les enjeux futurs de l’évaluation des systèmes de maintenance
5.1 L’impact de l’industrie 4.0
- Maintenance prédictive basée sur l’intelligence artificielle
- Utilisation de jumeaux numériques pour simuler et optimiser les stratégies de maintenance
Exemple concret : Une entreprise manufacturière a implémenté un système de maintenance prédictive utilisant l’IA pour analyser les données de vibration, de température et de consommation électrique de ses machines. Ce système a permis de prédire avec précision 85% des pannes une semaine à l’avance, réduisant les temps d’arrêt non planifiés de 30%.
Source : McKinsey – The Future of Maintenance
5.2 L’intégration des considérations environnementales
- Évaluation de l’empreinte carbone des activités de maintenance
- Optimisation de la consommation d’énergie et de ressources
Exemple concret : Une entreprise de transport a intégré des critères environnementaux dans son évaluation de maintenance. Elle a découvert que 25% de sa consommation de carburant était due à des véhicules mal entretenus. L’amélioration de son programme de maintenance a permis de réduire les émissions de CO2 de 10% et les coûts de carburant de 15%.
Conclusion
L’évaluation du système de maintenance industrielle est un processus complexe mais essentiel pour garantir la performance et la pérennité des installations. En adoptant une approche structurée et en utilisant les outils et méthodes appropriés, les entreprises peuvent non seulement optimiser leurs coûts de maintenance mais aussi améliorer significativement la fiabilité et la disponibilité de leurs équipements.
La clé du succès réside dans la combinaison d’une expertise technique solide, d’une méthodologie rigoureuse comme le KMIS, et d’une volonté d’amélioration continue. En intégrant les dernières avancées technologiques et en anticipant les enjeux futurs, les industriels pourront transformer leur système de maintenance en un véritable avantage compétitif.
N’oubliez pas que l’évaluation n’est que la première étape. C’est la mise en œuvre effective des actions correctives et l’engagement de toutes les parties prenantes qui permettront de tirer pleinement parti de cette démarche d’optimisation. Investir dans l’évaluation et l’amélioration de votre système de maintenance, c’est investir dans l’avenir de votre entreprise.