Dans le monde industriel en constante évolution, la recherche de méthodes plus efficaces pour maintenir les équipements en bon état de fonctionnement est devenue une priorité absolue. Parmi ces méthodes, la maintenance conditionnelle se distingue comme une approche novatrice et prometteuse. Mais qu’est-ce exactement que les avantages de la maintenance conditionnelle et pourquoi gagne-t-elle en importance dans l’industrie moderne ?
Table of Contents
l’avantages de la maintenance conditionnelle
La maintenance conditionnelle est une stratégie proactive qui se base sur l’état réel des équipements pour déterminer quand et comment effectuer les opérations de maintenance. Contrairement aux approches traditionnelles qui suivent un calendrier fixe ou qui interviennent uniquement en cas de panne, la maintenance conditionnelle utilise des données en temps réel pour prédire et prévenir les défaillances avant qu’elles ne se produisent.
Dans un contexte où la compétitivité industrielle repose de plus en plus sur l’efficacité opérationnelle et la réduction des coûts, l’adoption de méthodes de maintenance avancées comme la maintenance conditionnelle devient cruciale. Cette approche permet non seulement d’optimiser les performances des équipements, mais aussi de réaliser des économies substantielles à long terme.
Dans cet article, nous allons explorer en détail sept avantages souvent méconnus de la maintenance conditionnelle, démontrant pourquoi elle représente l’avenir de la gestion des actifs industriels.
1. Amélioration de la Fiabilité des Équipements
Surveillance continue des performances
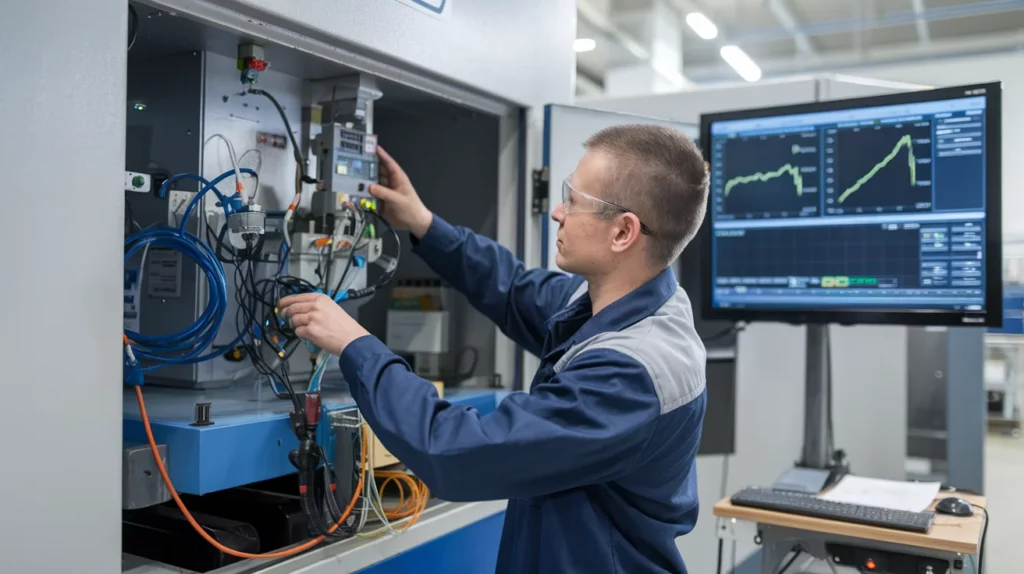
La maintenance conditionnelle repose sur une surveillance constante et en temps réel des équipements. Grâce à des capteurs sophistiqués et à l’Internet des Objets (IoT), il est possible de collecter en permanence des données sur l’état de fonctionnement des machines. Cette collecte continue permet de détecter les moindres variations de performance, offrant ainsi une vision précise et actualisée de l’état de santé des équipements.
Par exemple, chez General Electric, l’utilisation de capteurs sur les turbines à gaz a permis d’améliorer leur fiabilité de 99,5% à 99,9%, réduisant considérablement les temps d’arrêt imprévus.
Réduction des pannes imprévues
L’un des principaux avantages de la maintenance conditionnelle est sa capacité à prédire et prévenir les pannes avant qu’elles ne se produisent. En analysant les tendances des données collectées, il devient possible de détecter les signes précoces de défaillance. Cette détection précoce permet d’intervenir de manière ciblée, évitant ainsi les arrêts non planifiés qui peuvent s’avérer coûteux et perturbateurs pour la production.
Une étude menée par l’Université de Tennessee a montré que l’implémentation de la maintenance conditionnelle dans une usine de production d’électricité a réduit les pannes imprévues de 75%, augmentant significativement la disponibilité des équipements.
2. Optimisation des Coûts de Maintenance
Réduction des coûts liés aux interventions d’urgence
La maintenance conditionnelle permet de réduire considérablement les coûts associés aux interventions d’urgence. En anticipant les problèmes, elle évite les réparations effectuées dans l’urgence, généralement plus coûteuses en raison des heures supplémentaires, des pièces express et des pertes de production.
Une étude de cas réalisée par SKF sur une usine de papier a révélé que l’adoption de la maintenance conditionnelle a permis de réduire les coûts de maintenance de 30% sur une période de deux ans.
Économies sur les pièces de rechange
En intervenant uniquement lorsque c’est nécessaire, la maintenance conditionnelle permet d’optimiser l’utilisation des pièces de rechange. Les composants sont remplacés en fonction de leur état réel et non selon un calendrier arbitraire, ce qui réduit les stocks de pièces et les remplacements prématurés.
Airbus a rapporté une réduction de 20% des coûts liés aux pièces de rechange après avoir adopté des techniques de maintenance conditionnelle sur ses lignes d’assemblage.
3. Prolongation de la Durée de Vie des Actifs
Interventions ciblées basées sur l’état réel
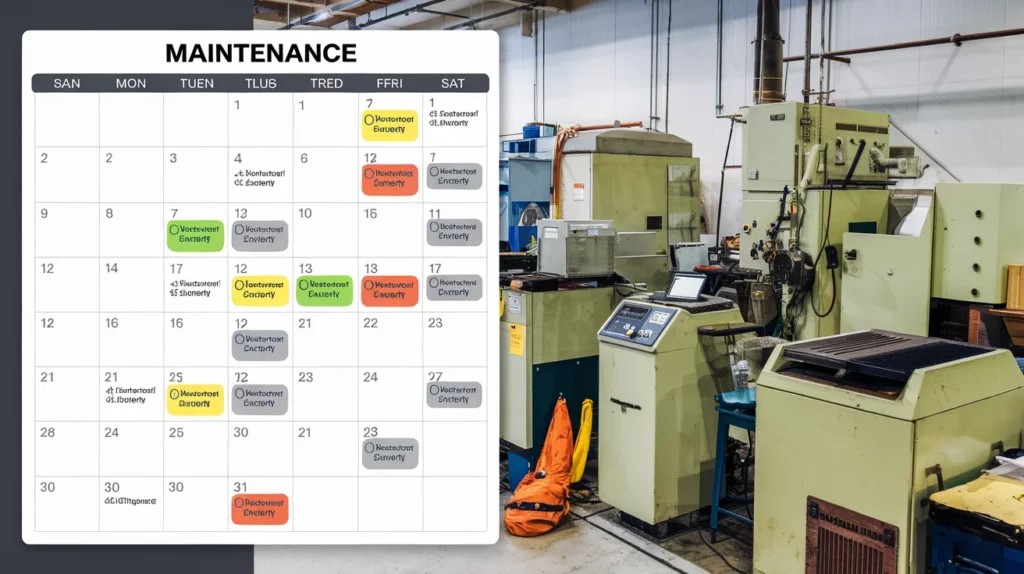
La maintenance conditionnelle permet d’intervenir de manière ciblée et précise, en se basant sur l’état réel des équipements. Cette approche évite les interventions inutiles qui peuvent parfois causer plus de problèmes qu’elles n’en résolvent. En n’intervenant que lorsque c’est vraiment nécessaire, on réduit les risques d’usure prématurée liés à des manipulations trop fréquentes.
Rolls-Royce, dans son service de maintenance des moteurs d’avion, a constaté une augmentation de 25% de la durée de vie des composants critiques grâce à l’utilisation de la maintenance conditionnelle.
Maintenance préventive intégrée
La maintenance conditionnelle ne remplace pas la maintenance préventive traditionnelle, mais la complète et l’optimise. En intégrant les données de surveillance en temps réel aux plans de maintenance préventive, il est possible de créer une synergie qui maximise la durée de vie des équipements. Cette approche hybride permet d’ajuster les intervalles de maintenance en fonction de l’utilisation réelle et des conditions de fonctionnement spécifiques de chaque équipement.
La SNCF a rapporté une augmentation de 15% de la durée de vie de ses trains après avoir intégré des techniques de maintenance conditionnelle à son programme de maintenance préventive. (Source : SNCF Innovation & Recherche)
4. Amélioration de la Sécurité au Travail
Réduction des risques liés aux pannes
Les pannes soudaines d’équipements peuvent représenter un danger sérieux pour les travailleurs. La maintenance conditionnelle, en prévenant ces pannes, contribue directement à la réduction des accidents de travail. En détectant les anomalies avant qu’elles ne deviennent critiques, on évite les situations potentiellement dangereuses liées à des défaillances imprévues.
Une étude menée par l’Association Internationale de la Sécurité Sociale (AISS) a montré que l’implémentation de la maintenance conditionnelle dans les industries lourdes a conduit à une réduction de 30% des accidents liés aux défaillances d’équipements.
Environnement de travail plus sûr
Un équipement bien entretenu est un équipement plus sûr. La maintenance conditionnelle, en assurant un fonctionnement optimal des machines, contribue à créer un environnement de travail plus sécurisé. Les employés peuvent travailler avec plus de confiance, sachant que les équipements qu’ils utilisent sont surveillés en permanence et maintenus dans un état optimal.
ArcelorMittal a rapporté une diminution de 45% des incidents de sécurité liés aux équipements après avoir mis en place un système de maintenance conditionnelle dans ses aciéries. (Source : ArcelorMittal Sustainability Report)
5. Flexibilité et Adaptabilité
Capacité à s’adapter aux changements opérationnels
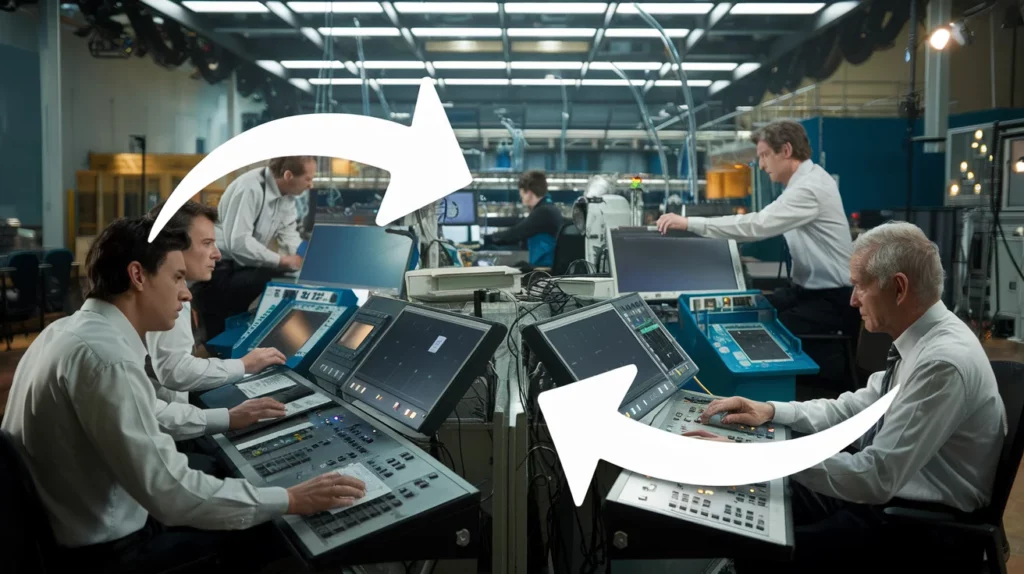
La maintenance conditionnelle offre une flexibilité incomparable en termes d’adaptation aux changements opérationnels. Contrairement aux approches de maintenance rigides, elle permet d’ajuster rapidement les stratégies de maintenance en fonction des variations de production ou des conditions d’exploitation. Cette adaptabilité est particulièrement précieuse dans les industries où les demandes de production peuvent fluctuer rapidement.
Siemens a démontré comment sa plateforme de maintenance conditionnelle a permis à une usine de production d’énergie de s’adapter à des variations de charge de 20% sans compromettre l’efficacité ou la fiabilité des équipements. (Source : Siemens Power Generation)
Personnalisation des stratégies de maintenance
Chaque équipement a ses propres caractéristiques et besoins en maintenance. La maintenance conditionnelle permet de personnaliser les stratégies de maintenance pour chaque actif, en tenant compte de ses spécificités. Cette approche sur mesure optimise l’efficacité des interventions et l’allocation des ressources.
Volvo Cars a rapporté une augmentation de 35% de l’efficacité de ses opérations de maintenance après avoir implémenté un système de maintenance conditionnelle personnalisé pour chaque ligne de production. (Source : Volvo Car Group)
6. Accroissement de l’Efficacité Opérationnelle
Amélioration continue grâce aux données collectées
L’un des avantages majeurs de la maintenance conditionnelle est la richesse des données qu’elle génère. Ces données, une fois analysées, offrent des insights précieux pour améliorer non seulement la maintenance, mais aussi les processus opérationnels dans leur ensemble. Cette amélioration continue basée sur des données réelles permet d’optimiser constamment les performances des équipements et des processus.
Procter & Gamble a utilisé les données de maintenance conditionnelle pour améliorer l’efficacité globale de ses équipements (OEE) de 5 à 8% dans plusieurs de ses usines, conduisant à des gains de productivité significatifs.
Réduction du temps d’arrêt non planifié
En prévenant les pannes avant qu’elles ne se produisent, la maintenance conditionnelle réduit drastiquement les temps d’arrêt non planifiés. Cette réduction a un impact direct sur la productivité et le rendement global de l’entreprise. Les interventions peuvent être planifiées de manière à minimiser leur impact sur la production.
Une étude de cas chez Toyota a montré que l’implémentation de la maintenance conditionnelle a réduit les temps d’arrêt non planifiés de 74%, augmentant ainsi la disponibilité des chaînes de production. (Source : Toyota Motor Corporation)
7. Renforcement de la Culture d’Amélioration Continue
Engagement du personnel dans le processus
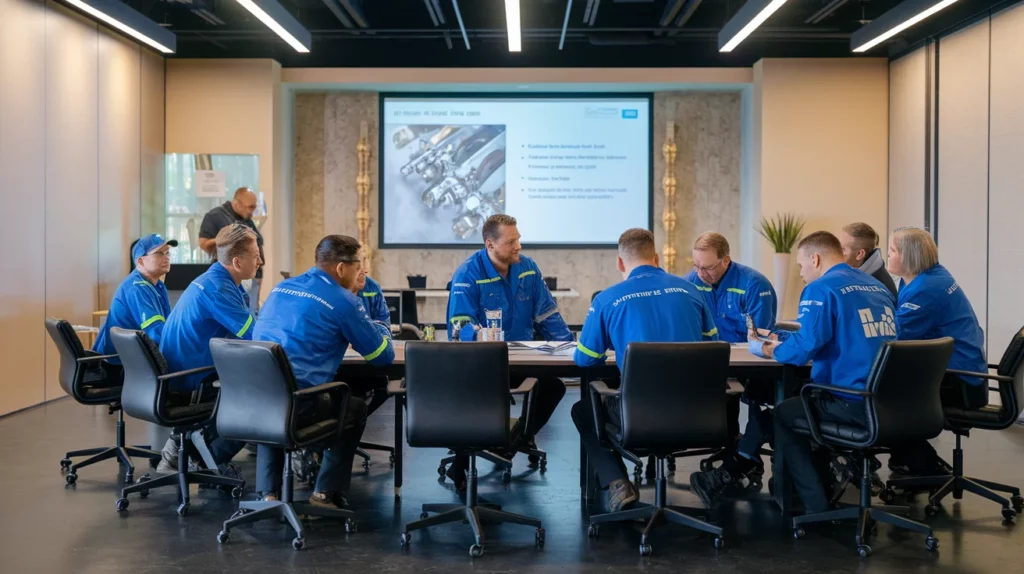
La mise en place d’une stratégie de maintenance conditionnelle nécessite et encourage l’engagement de tout le personnel. Les opérateurs, les techniciens et les ingénieurs doivent être formés à l’utilisation des nouveaux outils et à l’interprétation des données. Ce processus crée une culture d’amélioration continue où chacun est impliqué dans l’optimisation des performances des équipements.
Bosch a constaté une augmentation de 40% de l’engagement des employés dans les processus de maintenance après avoir mis en place un programme de formation et de sensibilisation à la maintenance conditionnelle. (Source : Bosch Rexroth)
Utilisation proactive des données pour l’innovation
Les données générées par la maintenance conditionnelle ne servent pas uniquement à prévenir les pannes. Elles constituent également une source précieuse d’informations pour innover dans les pratiques de maintenance et même dans la conception des équipements. Cette approche proactive encourage l’innovation continue dans tous les aspects de l’entreprise.
General Motors a utilisé les données de maintenance conditionnelle pour repenser certains composants de ses véhicules, conduisant à une amélioration de 15% de la fiabilité sur certains modèles. (Source : GM Authority)
Conclusion
La maintenance conditionnelle représente bien plus qu’une simple évolution des pratiques de maintenance. Elle constitue un véritable changement de paradigme dans la gestion des actifs industriels. Les sept avantages méconnus que nous avons explorés – l’amélioration de la fiabilité des équipements, l’optimisation des coûts, la prolongation de la durée de vie des actifs, l’amélioration de la sécurité, la flexibilité et l’adaptabilité, l’accroissement de l’efficacité opérationnelle, et le renforcement de la culture d’amélioration continue – démontrent clairement la valeur ajoutée de cette approche.
Dans un monde industriel de plus en plus compétitif et exigeant, l’adoption de la maintenance conditionnelle n’est plus un luxe, mais une nécessité. Elle permet non seulement de réduire les coûts et d’améliorer la productivité, mais aussi de créer un environnement de travail plus sûr et plus innovant.
Il est temps pour les entreprises de tous secteurs de considérer sérieusement l’intégration de la maintenance conditionnelle dans leurs stratégies opérationnelles. Les bénéfices à long terme sont indéniables, tant sur le plan financier que sur celui de l’efficacité globale. En embrassant cette approche proactive et data-driven, les entreprises se donnent les moyens de rester compétitives et résilientes face aux défis futurs de l’industrie.
L’avenir de la maintenance industrielle est conditionnel – conditionnel à notre capacité à écouter ce que nos machines ont à nous dire et à agir de manière préventive et intelligente. Êtes-vous prêt à franchir le pas vers cette nouvelle ère de la maintenance industrielle ?