Salut à tous ! Aujourd’hui, on va parler d’un sujet qui peut sembler un peu barbant au premier abord, mais qui est en fait super important : la gestion de la maintenance corrective. Vous savez, c’est ce qu’on fait quand une machine tombe en panne et qu’il faut la réparer vite fait bien fait.
C’est quoi au juste, la gestion de la maintenance corrective ?
Imaginez que vous êtes en train de préparer un gâteau pour l’anniversaire de votre meilleur ami. Tout d’un coup, votre four décide de faire grève. Pas de panique ! Vous appelez un réparateur qui vient remettre votre four en marche. C’est ça, la maintenance corrective. Dans le monde industriel, c’est pareil, mais à plus grande échelle.
Pourquoi c’est important de bien la gérer ?
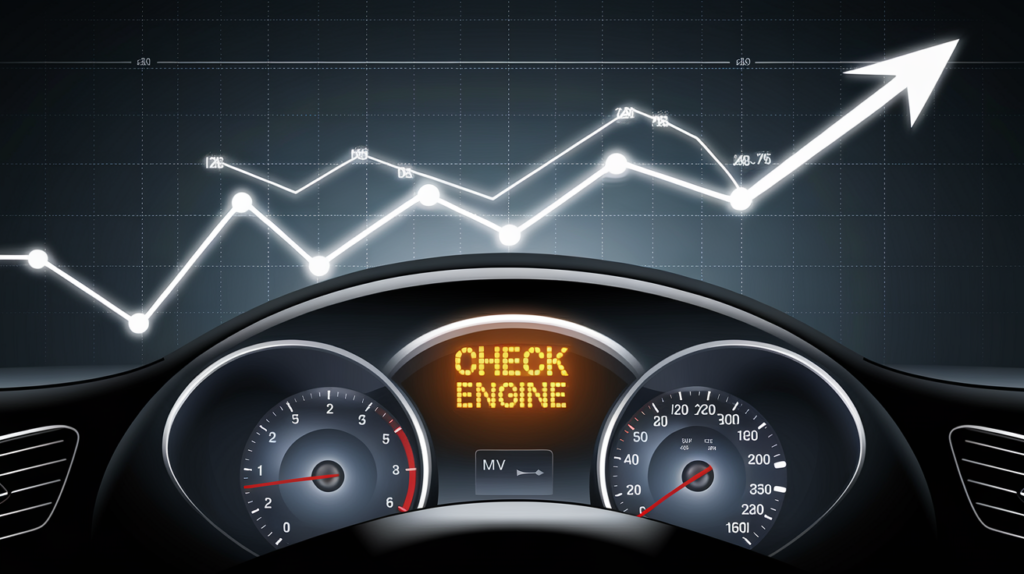
Bien gérer sa maintenance corrective, c’est un peu comme avoir un super-héros toujours prêt à intervenir. Ça vous permet de :
- Gagner du temps : Plus vite on répare, plus vite on reprend la production.
- Économiser de l’argent : Des réparations rapides et efficaces, c’est moins cher que des pannes à répétition.
- Assurer la sécurité : Des machines bien entretenues, c’est moins de risques pour les employés.
- Prolonger la vie de vos équipements : C’est comme prendre soin de sa voiture, ça la fait durer plus longtemps !
Alors, prêts à découvrir comment devenir des as de la maintenance corrective ? C’est parti !
1. Bien Comprendre les Différents Types de Maintenance
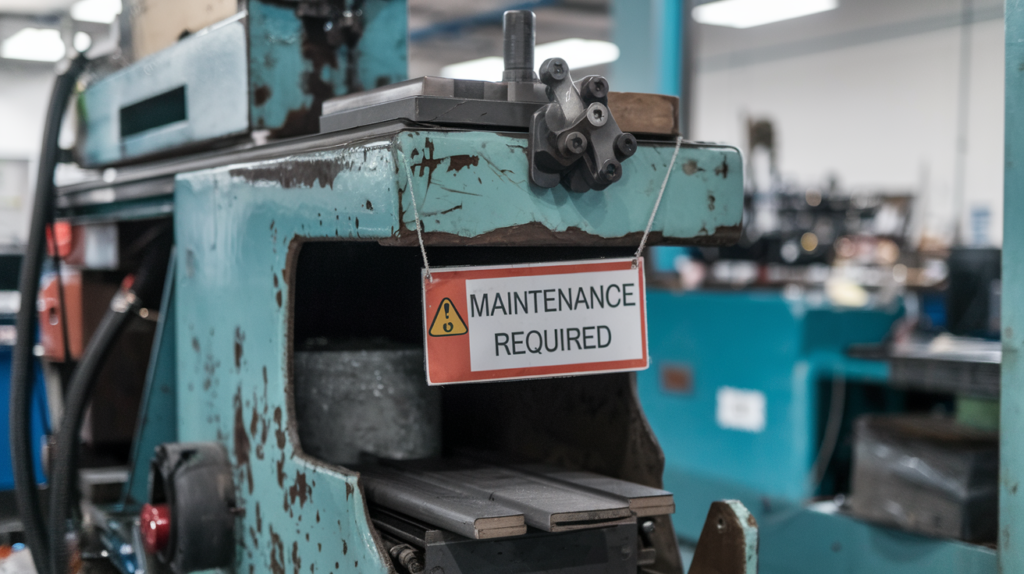
La maintenance corrective planifiée
C’est un peu comme quand vous savez que votre voiture fait un drôle de bruit, mais que vous pouvez encore rouler. Vous prenez rendez-vous chez le garagiste pour la semaine prochaine. Dans l’industrie, c’est pareil.
Par exemple, chez Airbus, ils utilisent cette approche pour certaines pièces d’avion qui ne sont pas critiques. Résultat ? Ils ont réussi à réduire leurs coûts de maintenance de 15% sur certaines flottes. Pas mal, hein ?
Les avantages, c’est que :
- Vous pouvez vous organiser tranquillement
- Vous évitez les mauvaises surprises
- Vous pouvez mieux gérer votre budget et votre personnel
La maintenance corrective non planifiée
Là, c’est le scénario catastrophe. Votre machine s’arrête d’un coup, sans prévenir. C’est comme si votre frigo lâchait en plein été pendant une canicule. Pas le choix, il faut agir tout de suite !
Tesla en a fait l’expérience en 2019. Une grosse panne dans une de leurs usines a entraîné plusieurs jours d’arrêt de production. Imaginez un peu la facture !
Les conséquences sont souvent lourdes :
- La production qui s’arrête net
- Des coûts qui s’envolent
- Du stress pour tout le monde
2. Établir un Plan de Maintenance Corrective
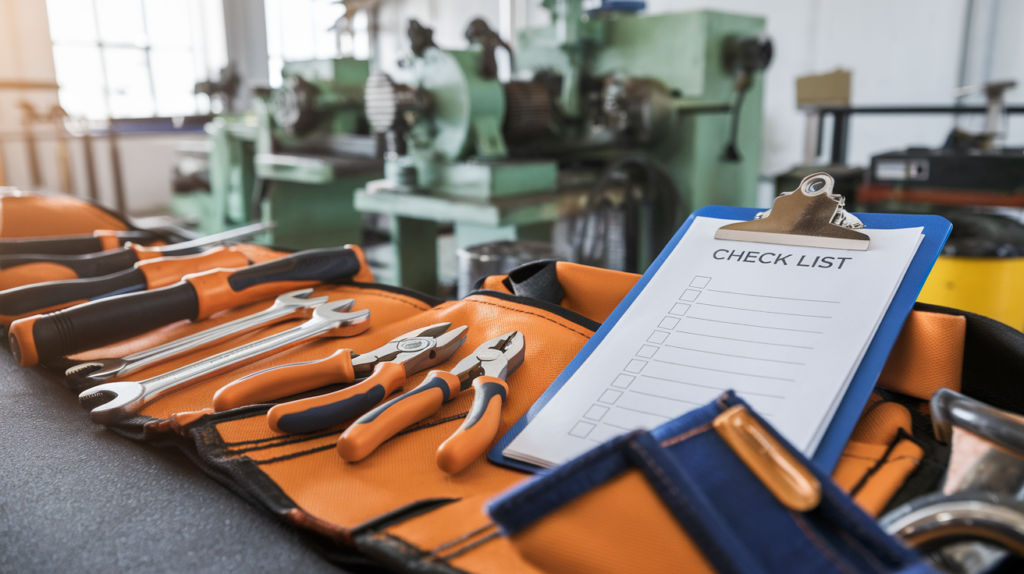
Avoir un bon plan de maintenance corrective, c’est comme avoir une bonne recette de cuisine. Avec les bons ingrédients et les bonnes étapes, vous êtes sûrs de réussir votre plat !
Pourquoi c’est important d’avoir un plan ?
Un bon plan, ça vous permet de :
- Réagir plus vite quand il y a un problème
- Mieux utiliser vos ressources (comme le personnel ou les pièces de rechange)
- Limiter le temps où vos machines sont à l’arrêt
Comment créer un plan efficace ?
- Faites l’inventaire de vos équipements : C’est comme faire la liste de tous les ingrédients dans votre cuisine. Vous devez savoir exactement ce que vous avez.
- Identifiez les machines critiques : Certaines machines sont plus importantes que d’autres. C’est comme dans une recette, certains ingrédients sont indispensables, d’autres sont optionnels.
- Évaluez les risques : Pour chaque machine, demandez-vous : “Qu’est-ce qui se passerait si elle tombait en panne ?” C’est comme évaluer les conséquences si vous oubliez un ingrédient dans votre recette.
- Priorisez vos interventions : Décidez quelles machines doivent être réparées en priorité en cas de panne. C’est comme décider quel plat vous allez préparer en premier pour un grand dîner.
- Préparez vos procédures : Pour chaque type de panne possible, préparez une procédure détaillée. C’est comme avoir une fiche recette pour chaque plat que vous cuisinez.
General Electric a mis en place un plan comme celui-ci dans ses usines de turbines. Résultat ? Ils ont réduit leurs temps d’arrêt de 20% en un an. Impressionnant, non ?
3. Utiliser des Outils de Gestion de Maintenance Assistée par Ordinateur (GMAO)
Vous connaissez ces applications qui vous aident à organiser votre vie quotidienne ? Eh bien, la GMAO, c’est un peu la même chose, mais pour la maintenance industrielle.
Pourquoi utiliser une GMAO ?
Une bonne GMAO, c’est comme avoir un assistant personnel super efficace. Elle vous permet de :
- Suivre en temps réel toutes vos interventions de maintenance
- Gérer facilement votre stock de pièces détachées
- Garder un historique de toutes les pannes et réparations
Quelles fonctionnalités rechercher dans une GMAO ?
- Planification automatique : C’est comme avoir un agenda intelligent qui organise vos rendez-vous de maintenance tout seul.
- Alertes en temps réel : Imaginez que votre téléphone vous prévienne dès qu’une machine a un problème. C’est exactement ce que fait une bonne GMAO.
- Rapports d’analyse : C’est comme avoir un détective privé qui analyse toutes vos données de maintenance et vous dit où vous pouvez vous améliorer.
Dassault Systèmes a développé une GMAO appelée DELMIA Apriso. Un constructeur automobile qui l’a utilisée a réussi à améliorer l’efficacité de sa maintenance de 30%. Pas mal, non ?
4. Former le Personnel de Maintenance
Former votre équipe de maintenance, c’est comme entraîner une équipe de sport. Plus ils s’entraînent, meilleurs ils deviennent !
Pourquoi la formation est importante ?
- Des techniciens bien formés, c’est comme avoir des super-héros de la maintenance. Ils trouvent les problèmes plus vite et les résolvent mieux.
- Ils font moins d’erreurs, donc vous avez moins besoin de repasser derrière eux.
- Ils travaillent plus en sécurité, ce qui est bon pour tout le monde.
Quels types de formations proposer ?
- Formation technique : C’est comme apprendre de nouvelles recettes pour un chef cuisinier. Vos techniciens apprennent à utiliser les derniers outils et techniques de réparation.
- Formation à la sécurité : C’est essentiel ! C’est comme apprendre à un enfant à traverser la route en toute sécurité.
- Gestion du temps : Apprenez à vos équipes à travailler efficacement. C’est comme apprendre à un jongleur à gérer plusieurs balles en même temps.
- Formation aux outils numériques : Avec tous ces nouveaux logiciels, il faut que vos équipes sachent s’en servir. C’est comme apprendre à utiliser un nouveau smartphone.
Siemens a mis en place un super programme de formation pour ses techniciens. Résultat ? Ils ont réduit leur temps moyen de réparation de 25%. Pas mal du tout !
5. Mettre en Place un Système de Suivi et d’Évaluation
Suivre et évaluer vos performances en maintenance, c’est comme tenir un journal de vos progrès à la salle de sport. Ça vous permet de voir ce qui marche bien et ce qu’il faut améliorer.
Pourquoi c’est important de suivre et d’évaluer ?
- Ça vous permet de repérer les problèmes qui reviennent souvent. C’est comme identifier les exercices qui vous font le plus mal à la salle.
- Vous pouvez voir si vos réparations sont efficaces. C’est comme vérifier si vos efforts à la salle donnent des résultats.
- Ça vous aide à prévoir les futures pannes. C’est comme anticiper les courbatures après une séance intense !
Quels indicateurs surveiller ?
- Temps moyen de réparation (MTTR) : C’est comme chronométrer le temps qu’il vous faut pour faire 100 mètres. Plus c’est court, mieux c’est !
- Taux de récurrence des pannes : Si la même panne revient souvent, c’est qu’il y a un problème. C’est comme si vous vous blessiez toujours au même endroit en faisant du sport.
- Coût moyen par intervention : C’est important de savoir combien vous coûtent vos réparations. C’est comme suivre combien vous dépensez en équipement de sport.
- Disponibilité des équipements : C’est le pourcentage de temps où vos machines fonctionnent. Plus c’est élevé, mieux c’est !
Toyota a mis en place un système comme celui-ci et a réussi à améliorer la disponibilité de ses lignes de production de 15% en trois ans. Chapeau !
6. Intégrer la Maintenance Préventive avec la Corrective
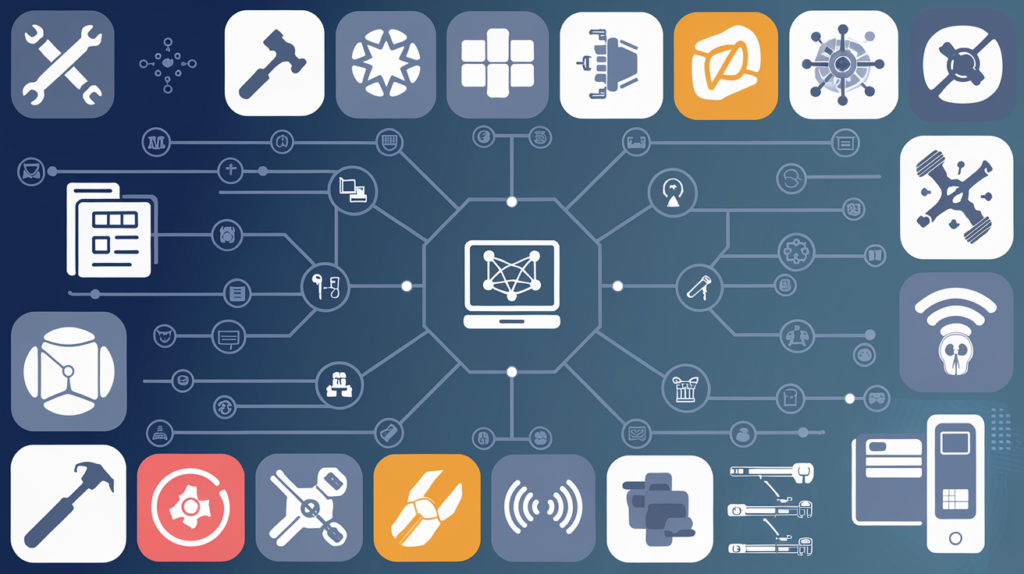
Combiner maintenance préventive et corrective, c’est comme avoir une bonne hygiène de vie et un bon médecin. L’un n’empêche pas l’autre, mais les deux ensemble, c’est encore mieux !
Pourquoi combiner les deux ?
- Ça réduit le nombre de pannes surprises. C’est comme manger sainement pour éviter d’être malade.
- Vous pouvez mieux planifier vos ressources. C’est comme prévoir à l’avance vos rendez-vous chez le médecin.
- Vos machines durent plus longtemps. C’est comme prendre soin de sa santé pour vivre plus longtemps !
Comment intégrer les deux approches ?
- Planifiez ensemble : Faites un planning qui inclut à la fois la maintenance préventive et la maintenance corrective. C’est comme avoir un agenda qui combine vos rendez-vous chez le médecin et vos séances de sport.
- Partagez les informations : Utilisez ce que vous apprenez lors des réparations pour améliorer votre maintenance préventive. C’est comme adapter votre régime alimentaire en fonction des recommandations de votre médecin.
- Utilisez l’analyse prédictive : C’est un peu de la magie moderne ! Des ordinateurs peuvent prédire quand une machine va tomber en panne. C’est comme avoir un médecin qui pourrait prédire quand vous allez tomber malade.
Rolls-Royce a développé un système comme ça pour ses moteurs d’avion. Résultat ? Ils ont réduit les temps d’arrêt non planifiés de 40% pour leurs clients. Pas mal du tout !
7. Analyser les Données pour Améliorer les Processus
Analyser vos données de maintenance, c’est comme être un détective qui cherche des indices pour résoudre une énigme. Ces données peuvent vous dire beaucoup de choses sur vos machines et vos processus.
Pourquoi analyser les données ?
- Ça vous aide à identifier les machines qui posent le plus de problèmes. C’est comme repérer le joueur le plus faible dans une équipe de foot.
- Vous pouvez mieux gérer votre stock de pièces détachées. C’est comme savoir exactement quels ingrédients acheter pour votre prochain repas.
- Ça vous permet d’améliorer vos procédures de maintenance. C’est comme affiner une recette de cuisine à chaque fois que vous la faites.
Quels outils utiliser pour analyser les données ?
- Logiciels d’analyse prédictive : Ces logiciels sont un peu comme des boules de cristal high-tech. Ils peuvent prédire quand une machine risque de tomber en panne.
- Tableaux de bord interactifs : C’est comme avoir un grand écran qui vous montre en temps réel l’état de santé de toutes vos machines.
- Rapports automatisés : Imaginez que votre ordinateur vous prépare automatiquement un résumé de toutes vos activités de maintenance. C’est exactement ce que font ces rapports.
IBM a développé un système d’analyse de données pour la maintenance industrielle. Une entreprise qui l’a utilisé a réussi à réduire ses coûts de maintenance de 25%. Pas mal, non ?
8. Communiquer Efficacement avec les Équipes et les Parties Prenantes
Une bonne communication en maintenance, c’est comme avoir un bon arbitre dans un match de foot. Ça permet à tout le monde de jouer ensemble efficacement.
Pourquoi la communication est importante ?
- Ça permet de réagir plus vite quand il y a un problème. C’est comme quand l’arbitre siffle une faute, tout le monde est au courant immédiatement.
- Ça améliore la coordination entre les équipes. C’est comme quand les joueurs d’une équipe se font des passes parfaites.
- Ça rend tout le monde plus satisfait du travail accompli. C’est comme quand une équipe gagne grâce à une bonne stratégie.
Comment améliorer la communication ?
- Faites des réunions régulières : C’est comme le briefing avant un match. Tout le monde sait ce qu’il a à faire.
- Utilisez des rapports d’avancement : C’est comme donner le score du match en temps réel. Tout le monde sait où on en est.
- Encouragez le feedback : C’est comme faire un debriefing après le match. On parle de ce qui a bien marché et de ce qu’on peut améliorer.
Procter & Gamble a mis en place un système de communication en temps réel pour sa maintenance. Résultat ? Ils ont réduit le temps de réponse aux pannes de 30% dans leurs usines. Impressionnant, non ?
Conclusion
Voilà, on a fait le tour de nos 8 stratégies pour améliorer la gestion de la maintenance corrective. C’est un peu comme avoir une boîte à outils bien garnie : avec tous ces outils à votre disposition, vous êtes prêts à affronter n’importe quelle panne !
N’oubliez pas que la maintenance corrective est un processus continu qui demande une attention constante. En adaptant vos pratiques et en vous appuyant sur les outils et les informations à votre disposition, vous pourrez créer un système de maintenance efficace qui garantit la performance et la fiabilité de vos opérations.