La maintenance préventive est un élément crucial dans la gestion des équipements et des infrastructures industrielles. Elle permet de maintenir les performances optimales des machines, de réduire les coûts de réparation et d’augmenter la durée de vie des équipements. Dans cet article, nous allons explorer en détail la définition, l’importance, les types, les avantages, les inconvénients et les meilleures pratiques guide sur la maintenance préventive.
Table of Contents
Qu’est-ce que la Maintenance Préventive ?
Définition et Importance dans l’Industrie
La maintenance préventive est une approche proactive qui consiste à inspecter et à entretenir régulièrement les équipements pour éviter les pannes et prolonger leur durée de vie opérationnelle. Cette stratégie est essentielle pour maintenir les performances des machines conformément aux spécifications des fabricants, réduire les interruptions de production et optimiser l’efficacité opérationnelle.
Pourquoi la Maintenance Préventive est Cruciale pour la Performance Industrielle ?
La maintenance préventive est cruciale pour plusieurs raisons :
- Réduction des Coûts : En prenant des mesures préventives, les entreprises peuvent éviter les coûts élevés associés aux réparations correctives et aux arrêts de production imprévus.
- Augmentation de la Durée de Vie des Équipements : Les inspections régulières et les tâches de maintenance contribuent à prolonger la durée de vie des machines.
- Optimisation de la Productivité : En minimisant les interruptions, les entreprises peuvent maintenir un niveau de production stable et efficient.
I. Types de Maintenance Préventive
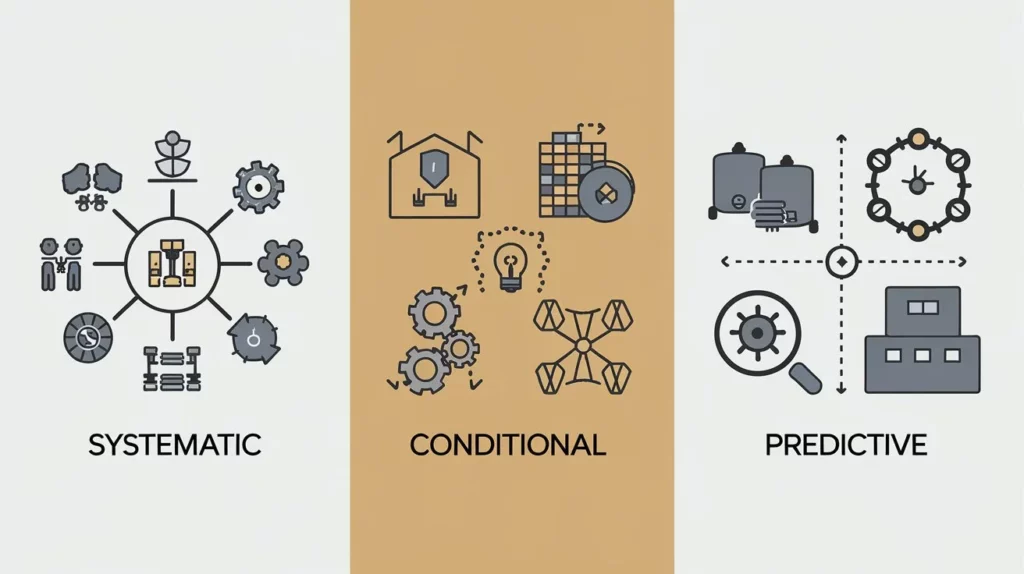
1.1 Maintenance Préventive Systématique
Description, Avantages et Checklists
La maintenance préventive systématique, également appelée maintenance basée sur le calendrier, consiste à planifier des tâches de maintenance à des intervalles réguliers, indépendamment de l’utilisation ou de la performance de l’équipement.
Avantages :
- Prévisibilité : Les tâches de maintenance sont planifiées à l’avance, ce qui permet de gérer les ressources de manière efficace.
- Simplicité : Cette approche est facile à mettre en œuvre, surtout pour les équipements qui nécessitent des inspections et des réglages périodiques.
Exemple Concret :
- Inspections Régulières : Effectuer des inspections semi-annuelles sur les systèmes de climatisation. Par exemple, une entreprise a pu réduire les arrêts de production dus à des pannes de climatisation en effectuant des inspections régulières, ce qui a permis de maintenir une température stable et de prolonger la durée de vie des systèmes.
Checklists :
- Inspections Régulières : Effectuer des inspections semi-annuelles sur les systèmes de climatisation.
- Réglages et Entretien : Réaliser des réglages et des entretiens périodiques sur les machines.
1.2 Maintenance Préventive Conditionnelle
Comment elle se Différencie, Pourquoi elle est Efficace et Meilleures Pratiques
La maintenance préventive conditionnelle, également appelée maintenance basée sur l’utilisation, est déclenchée lorsque l’équipement atteint un certain seuil d’utilisation, comme un nombre de kilomètres parcourus ou de cycles de production.
Avantages :
- Précision : Cette approche considère l’utilisation réelle de l’équipement, ce qui est plus précis que les calendriers fixes.
- Efficiency : Elle permet de réaliser les tâches de maintenance au moment où elles sont vraiment nécessaires.
Exemple Concret :
- Suivi de l’Utilisation : Utiliser des logiciels pour suivre l’utilisation de l’équipement et planifier les tâches de maintenance en conséquence. Par exemple, inspecter les courroies toutes les 100 heures de production pour éviter les pannes.
Checklists :
- Suivi de l’Utilisation : Utiliser des logiciels pour suivre l’utilisation de l’équipement et planifier les tâches de maintenance en conséquence.
- Entretien Spécifique : Effectuer des réparations et des entretiens spécifiques en fonction de l’utilisation réelle de l’équipement.
1.3 Maintenance Préventive Prédictive
Utilisation des Technologies pour Prévoir les Pannes et Checklists
La maintenance préventive prédictive utilise les données historiques et l’analyse avancée pour prévoir les pannes et planifier les tâches de maintenance en conséquence.
Avantages :
- Précision à Long Terme : Les prédictions deviennent plus précises avec le temps, améliorant l’efficacité des tâches de maintenance.
- Optimisation des Coûts : Même si elle nécessite un investissement initial, cette approche peut réduire les coûts à long terme.
Exemple Concret :
- Analyse de Données : Utiliser des logiciels pour analyser les données historiques et prédire les besoins de maintenance. Par exemple, une surveillance constante de la température d’un serveur permet de prévenir sa surchauffe, évitant ainsi les dommages irréparables à l’équipement.
Checklists :
- Analyse de Données : Utiliser des logiciels pour analyser les données historiques et prédire les besoins de maintenance.
- Planification de Maintenance : Établir un plan de maintenance basé sur les prédictions pour éviter les pannes.
II. Les Avantages de la Maintenance Préventive
2.1 Réduction des Coûts de Réparation
La maintenance préventive permet de réduire significativement les coûts associés aux réparations correctives. En anticipant les pannes, les entreprises peuvent éviter les coûts élevés des réparations d’urgence et des arrêts de production.
Exemple Concret :
- Économies sur le Long Terme : Une entreprise a pu réaliser des économies considérables sur le long terme en effectuant des contrôles et des mises à jour régulières, évitant ainsi les défaillances du système et les pertes de données majeures.
2.2 Augmentation de la Durée de Vie des Équipements
Les inspections régulières et les tâches de maintenance contribuent à prolonger la durée de vie des machines. Cela permet de maximiser l’utilisation des équipements et de réduire la nécessité de remplacement prématuré.
Statistique :
- Augmentation de la Durée de Vie : La maintenance préventive peut prolonger la durée de vie des serveurs de trois ans, ce qui a permis des économies substantielles sur le coût total de possession (TCO).
2.3 Optimisation de la Productivité
La maintenance préventive réduit les interruptions de production en minimisant les pannes et les arrêts de production imprévus. Cela permet de maintenir un niveau stable et efficient de production, ce qui améliore la productivité globale.
Exemple Concret :
- Réduction des Temps d’Arrêt : La maintenance préventive peut éviter les temps d’arrêt imprévus, ce qui augmente la durée d’exploitation et la disponibilité de l’équipement, améliorant ainsi l’efficacité globale de l’équipement (TRS).
III. Les Inconvénients et Limites de la Maintenance Préventive
3.1 Coût Initial Élevé
La mise en place d’un programme de maintenance préventive nécessite souvent des investissements initiaux significatifs, notamment pour l’acquisition de logiciels et d’équipements spécifiques.
3.2 Risque de Sur-Maintenance
Il est possible que trop de maintenance devienne contre-productive. Des tâches de maintenance inutiles peuvent gaspiller des ressources et réduire l’efficacité globale.
Exemple Concret :
- Maintenance Inutile : Une maintenance excessive sur des équipements encore dans un état optimal peut entraîner des coûts trop élevés par rapport aux temps d’arrêt qu’elle permet d’éviter.
Checklists pour Éviter la Sur-Maintenance :
- Analyse des Besoins : Évaluer soigneusement les besoins de maintenance pour éviter les tâches inutiles.
- Planification Optimale : Planifier les tâches de maintenance en fonction des données réelles et non basées sur des calendriers fixes.
3.3 Limitations Technologiques
L’intégration de nouvelles technologies dans l’industrie peut présenter des défis, notamment pour les équipements qui ne disposent pas de capteurs ou de systèmes de surveillance avancés.
IV. Mise en Place d’un Programme de Maintenance Préventive
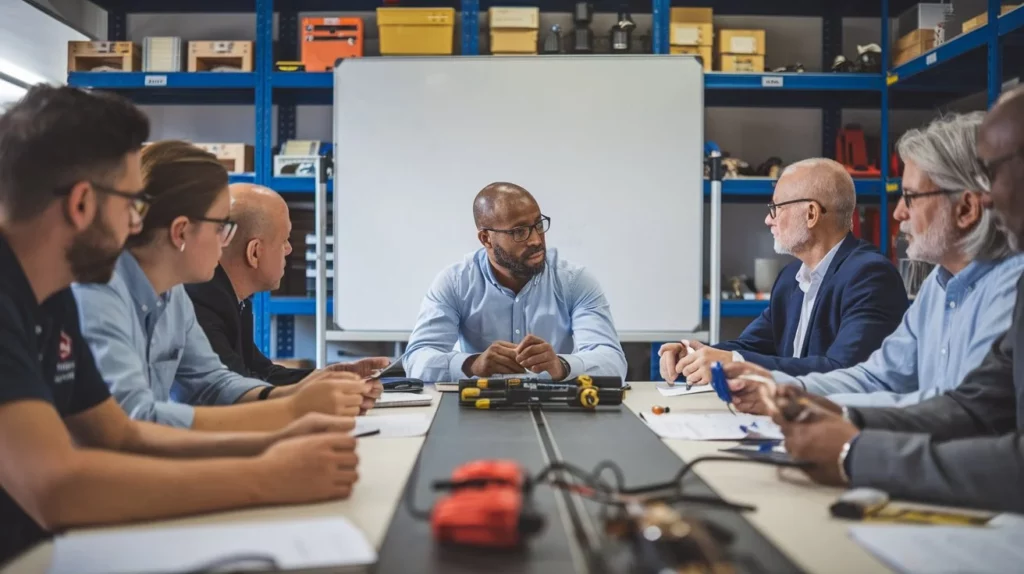
4.1 Identification des Équipements Critiques
Il est essentiel de prioriser les machines les plus importantes pour le fonctionnement de l’entreprise. Cela permet de concentrer les ressources sur les équipements qui ont le plus d’impact sur la production.
Exemple Concret :
- Priorisation des Actifs : Les gestionnaires d’installations utilisent cette approche pour les actifs limités et critiques, tels que les équipements de sécurité incendie et les systèmes CVC.
Checklists pour l’Identification :
- Évaluation de l’Impact : Évaluer l’impact de chaque équipement sur la production et la productivité.
- Priorisation : Prioriser les équipements en fonction de leur importance critique.
4.2 Planification des Interventions
La planification des interventions de maintenance est cruciale pour assurer que les tâches soient exécutées de manière efficace et efficiente.
Méthodologie :
- Utilisation de Logiciels GMAO : Utiliser des logiciels de gestion assistée par ordinateur (GMAO) pour planifier et suivre les tâches de maintenance.
- Calendrier de Maintenance : Établir un calendrier de maintenance qui inclut les tâches régulières et les inspections.
4.3 Formation du Personnel
La formation continue des équipes de maintenance est essentielle pour garantir que les tâches soient exécutées correctement et en toute sécurité.
Checklists pour la Formation :
- Programmes de Formation : Mettre en place des programmes de formation réguliers pour les équipes de maintenance.
- Documentation des Procédures : Documenter les procédures et les protocoles de sécurité pour une référence facile.
4.4 Utilisation de la Gestion Assistée par Ordinateur (GMAO)
Les outils GMAO sont indispensables pour la gestion efficace des programmes de maintenance.
Checklists pour l’Utilisation de GMAO :
- Sélection du Logiciel : Choisir un logiciel GMAO adapté aux besoins de l’entreprise.
- Formation des Utilisateurs : Former les utilisateurs sur l’utilisation du logiciel pour maximiser son potentiel.
V. Outils et Technologies pour la Maintenance Préventive
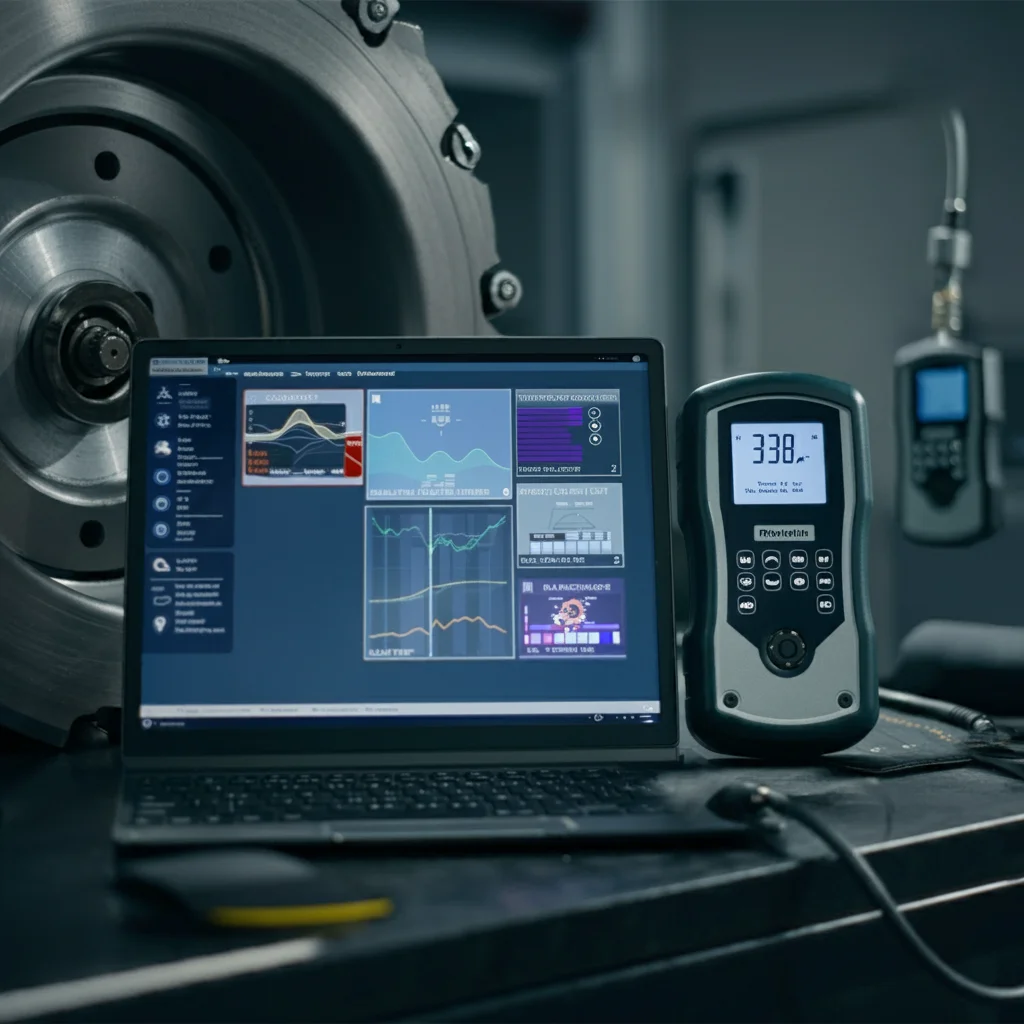
5.1 Les Capteurs IoT pour la Surveillance Continue
Les capteurs IoT permettent une surveillance continue des équipements, détectant les anomalies et les pannes potentielles avant qu’elles ne se produisent.
Exemple Concret :
- Surveillance de la Température : Utiliser des capteurs pour surveiller la température d’un serveur et prévenir sa surchauffe, prolongeant ainsi sa durée de vie.
Checklists pour l’Utilisation des Capteurs IoT :
- Installation des Capteurs : Installer des capteurs sur les équipements critiques pour une surveillance en temps réel.
- Analyse des Données : Utiliser des logiciels pour analyser les données des capteurs et prédire les besoins de maintenance.
5.2 Intelligence Artificielle et Maintenance Prédictive
L’intelligence artificielle (IA) est utilisée pour analyser les données historiques et prédire les pannes, permettant une planification de maintenance plus efficace.
Exemple Concret :
- Analyse de Données Historiques : Utiliser des algorithmes d’IA pour analyser les données historiques et prédire les besoins de maintenance, évitant ainsi les pannes imprévues.
Checklists pour l’Utilisation de l’IA :
- Implémentation de l’IA : Intégrer des algorithmes d’IA dans les systèmes de maintenance pour améliorer les prédictions.
- Formation des Équipes : Former les équipes à utiliser les outils d’IA pour maximiser leur potentiel.
5.3 Logiciels GMAO et Automatisation des Processus
Les logiciels GMAO sont essentiels pour automatiser les processus de maintenance, permettant une gestion efficace et efficiente des tâches.
Checklists pour l’Utilisation des Logiciels GMAO :
- Sélection du Logiciel : Choisir un logiciel GMAO adapté aux besoins de l’entreprise.
- Automatisation des Tâches : Utiliser le logiciel pour automatiser les tâches de maintenance et les inspections.
VI. Études de Cas : Maintenance Préventive en Action
6.1 Cas d’une Industrie Manufacturière
Une industrie manufacturière a mis en place un programme de maintenance préventive, ce qui a permis de réduire les arrêts de production et les coûts de réparation. Les inspections régulières et les tâches de maintenance planifiées ont amélioré la durée de vie des équipements et augmenté la productivité.
6.2 Cas d’une Centrale Énergétique
Une centrale énergétique a utilisé la maintenance préventive pour réduire les coûts d’arrêt. En utilisant des capteurs IoT et des algorithmes d’IA, l’entreprise a pu prédire les pannes et planifier les tâches de maintenance, minimisant ainsi les interruptions de production.
VII. Les Meilleures Pratiques pour une Maintenance Préventive Réussie
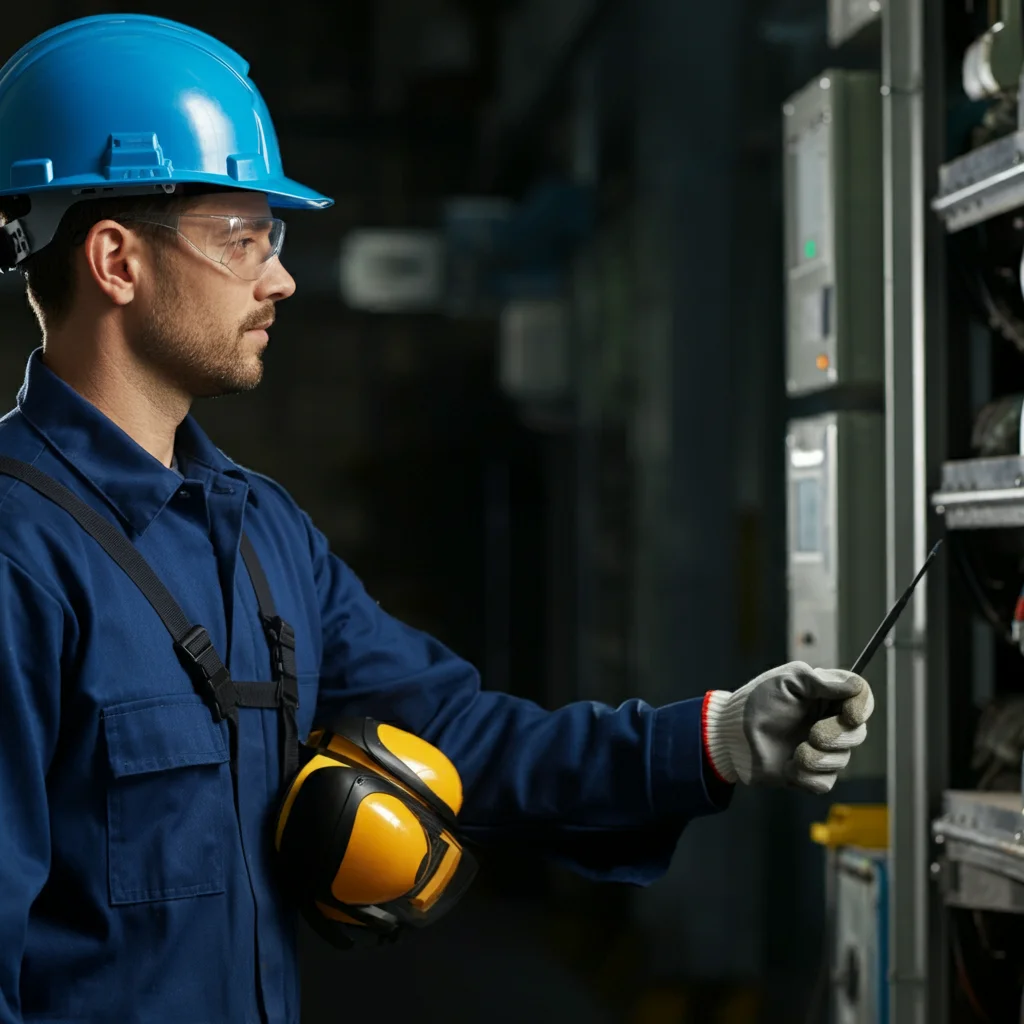
7.1 Suivi Régulier et Contrôles Périodiques
Un suivi constant est nécessaire pour une maintenance optimale. Les inspections régulières et les contrôles périodiques permettent de détecter les anomalies et de prendre des mesures correctives avant que les problèmes ne s’aggravent.
Checklists pour le Suivi :
- Planification des Inspections : Planifier des inspections régulières pour surveiller l’état des équipements.
- Analyse des Données : Analyser les données des inspections pour identifier les tendances et les anomalies potentielles.
7.2 Utilisation de Tableaux de Bord et d’Indicateurs de Performance (KPI)
Les tableaux de bord et les KPI sont essentiels pour mesurer l’efficacité du programme de maintenance. Ils permettent de suivre les performances et de prendre des décisions éclairées.
Checklists pour les KPI :
- Définition des KPI : Définir des KPI pertinents pour mesurer l’efficacité du programme de maintenance, tels que le temps moyen entre les pannes (MTBF) et le temps moyen de réparation (MTTR).
- Suivi des Performances : Utiliser des tableaux de bord pour suivre les performances et ajuster le programme de maintenance en conséquence.
7.3 L’Importance du Feedback des Techniciens
Le feedback des techniciens est crucial pour améliorer continuellement le programme de maintenance. Leur expérience et leurs observations permettent de identifier les meilleures pratiques et les améliorations nécessaires.
Checklists pour le Feedback :
- Collecte de Feedback : Collecter régulièrement le feedback des techniciens et des opérateurs.
- Analyse et Intégration : Analyser le feedback et intégrer les suggestions dans le programme de maintenance.
FAQ sur la Maintenance Préventive
Conclusion
La maintenance préventive est une stratégie essentielle pour les entreprises qui souhaitent maximiser la performance et la durée de vie de leurs équipements. En comprenant les différents types de maintenance préventive, en identifiant les avantages et les inconvénients, et en mettant en place des programmes bien planifiés, les entreprises peuvent réduire les coûts, augmenter la productivité et améliorer l’efficacité opérationnelle.
Sources