Imaginez une usine où les machines ne tombent jamais en panne de façon inattendue, où les techniciens savent exactement quand et comment intervenir, et où la productivité atteint des sommets inégalés. Ce scénario, autrefois du domaine de la science-fiction, devient aujourd’hui réalité grâce aux technologies de maintenance.
La technologie de maintenance peut être définie comme l’ensemble des outils, techniques et méthodologies innovantes utilisés pour optimiser les processus de maintenance industrielle. Elle englobe l’utilisation de l’Internet des Objets (IoT), de l’Intelligence Artificielle (IA), du Big Data et de la réalité augmentée pour améliorer la fiabilité, l’efficacité et la sécurité des équipements.
Ces technologies révolutionnent les pratiques industrielles en transformant radicalement la façon dont les entreprises gèrent leurs actifs et leurs opérations de maintenance. Elles permettent non seulement d’anticiper les pannes, mais aussi d’optimiser les interventions, réduisant ainsi les coûts tout en augmentant la disponibilité des équipements.
Table of Contents
Qu’est-ce que la technologie de maintenance ?
1. Définition et enjeux
La technologie de maintenance intègre des solutions numériques comme l’Internet des Objets (IoT), l’intelligence artificielle (IA), et l’analyse de données pour surveiller et maintenir les équipements. Ces technologies permettent une maintenance proactive, plutôt que réactive, en détectant les anomalies avant qu’elles ne provoquent des pannes.
Importance de la maintenance dans l’industrie
La maintenance est un pilier essentiel dans l’industrie, garantissant la continuité de la production, la qualité des produits, et la sécurité des employés. Une maintenance efficace peut faire la différence entre une entreprise compétitive et une entreprise en difficulté.
Les défis de la maintenance traditionnelle
La maintenance traditionnelle repose souvent sur des intervalles fixes ou des inspections manuelles, ce qui peut entraîner des coûts élevés, des pannes inattendues, et des inefficacités. La technologie de maintenance vient pallier ces limitations en apportant une approche plus flexible et précise.
2. Les piliers de la technologie de maintenance
La technologie de maintenance moderne repose sur des innovations clés qui transforment la gestion des équipements. Cet article explore les piliers essentiels tels que l’Internet des Objets (IoT), l’Intelligence Artificielle (IA), le Big Data, l’Analyse Prédictive et la Réalité Augmentée, qui permettent d’optimiser la performance des machines et d’améliorer l’efficacité opérationnelle.
IoT (Internet des Objets)
- Description : L’Internet des Objets (IoT) permet la connexion et la communication entre divers équipements et systèmes via des capteurs et des dispositifs intelligents. Ces objets recueillent et échangent des données en temps réel.
- Rôle en Maintenance :
- Collecte de Données : Les capteurs IoT installés sur les machines surveillent en permanence les conditions de fonctionnement, comme la température, la pression et les vibrations.
- Surveillance en Temps Réel : Permet la détection précoce des anomalies en fournissant des alertes immédiates en cas de dysfonctionnement.
- Intégration : Les données collectées par les dispositifs IoT sont intégrées aux systèmes de gestion de maintenance (GMAO) pour une analyse et une intervention plus efficaces.
IA (Intelligence Artificielle)
- Description : L’IA implique l’utilisation d’algorithmes et de modèles de machine learning pour analyser les données, prédire les pannes et optimiser les processus.
- Rôle en Maintenance :
- Analyse des Données : Utilisation de l’apprentissage automatique pour analyser les données collectées et identifier des patterns qui peuvent prédire les pannes.
- Prédiction : Anticipation des défaillances des équipements avant qu’elles ne surviennent, permettant une intervention proactive.
- Optimisation des Ressources : Aide à planifier les interventions de maintenance de manière plus précise en optimisant les ressources nécessaires.
Big Data
- Description : Big Data fait référence à l’analyse et à la gestion de vastes ensembles de données complexes provenant de diverses sources.
- Rôle en Maintenance :
- Stockage et Traitement : Gestion de grandes quantités de données générées par les équipements et les systèmes pour identifier des tendances et des anomalies.
- Insights : Fournit des insights détaillés sur les performances des équipements, les causes des pannes, et les opportunités d’amélioration.
- Décisions Basées sur les Données : Aide à prendre des décisions informées sur les stratégies de maintenance en s’appuyant sur des analyses de données approfondies.
Analyse Prédictive
- Description : L’analyse prédictive utilise des techniques statistiques et des algorithmes pour prédire les événements futurs basés sur des données historiques.
- Rôle en Maintenance :
- Prévision des Pannes : Identifie les équipements susceptibles de tomber en panne avant que cela ne se produise, permettant une maintenance préventive.
- Optimisation des Interventions : Permet de planifier les opérations de maintenance de manière à minimiser les temps d’arrêt et les coûts.
- Amélioration Continue : Affine les modèles prédictifs avec les nouvelles données pour améliorer la précision des prévisions.
- Description : La réalité augmentée (RA) superpose des informations numériques sur le monde réel à travers des dispositifs comme des lunettes intelligentes ou des smartphones.
Réalité Augmentée
- Rôle en Maintenance :
- Support Visuel : Fournit des instructions visuelles en temps réel aux techniciens pour faciliter les réparations et les interventions.
- Formation et Assistance : Aide à former le personnel en montrant des processus étape par étape et permet une assistance à distance en cas de besoin.
- Inspection et Diagnostic : Permet d’examiner les équipements et de diagnostiquer les problèmes plus efficacement en intégrant des informations supplémentaires sur l’équipement.
Les avantages de la technologie de maintenance
La technologie de maintenance offre des avantages considérables pour les entreprises en transformant la manière dont les équipements sont surveillés et gérés.
En permettant une détection précoce des anomalies, en optimisant les processus de maintenance, et en améliorant la productivité tout en renforçant la sécurité, ces technologies contribuent à des opérations plus efficaces et à une meilleure performance des équipements. Découvrons en détail comment ces avantages se manifestent et transforment le paysage de la maintenance industrielle.
1. Amélioration de la fiabilité des équipements
La fiabilité des équipements est cruciale pour assurer une production continue et éviter des interruptions coûteuses. En utilisant des technologies avancées telles que la détection précoce des anomalies, la maintenance prédictive, et en réduisant les pannes inattendues, les entreprises peuvent optimiser leurs opérations et réduire les coûts liés aux réparations et aux temps d’arrêt imprévus.
Détection Précoce des Anomalies
- Technologies Utilisées :
- Capteurs IoT : Les capteurs IoT collectent des données en temps réel sur divers paramètres de fonctionnement des équipements, tels que la température, les vibrations et la pression. Ces données sont transmises à des systèmes de surveillance pour une analyse continue.
- Analyse de Données : Les systèmes utilisent des algorithmes d’analyse de données pour identifier des anomalies dans les données collectées. Par exemple, une augmentation anormale des vibrations peut signaler un problème mécanique imminent.
- Exemples d’Application :
- Maintenance des Moteurs : Des capteurs installés sur des moteurs électriques peuvent détecter des vibrations anormales ou une température excessive, permettant une intervention avant une défaillance majeure.
- Surveillance des Pompes : Les capteurs surveillent le débit et la pression des pompes. Les anomalies dans ces mesures peuvent indiquer des obstructions ou des problèmes d’usure.
Maintenance Prédictive
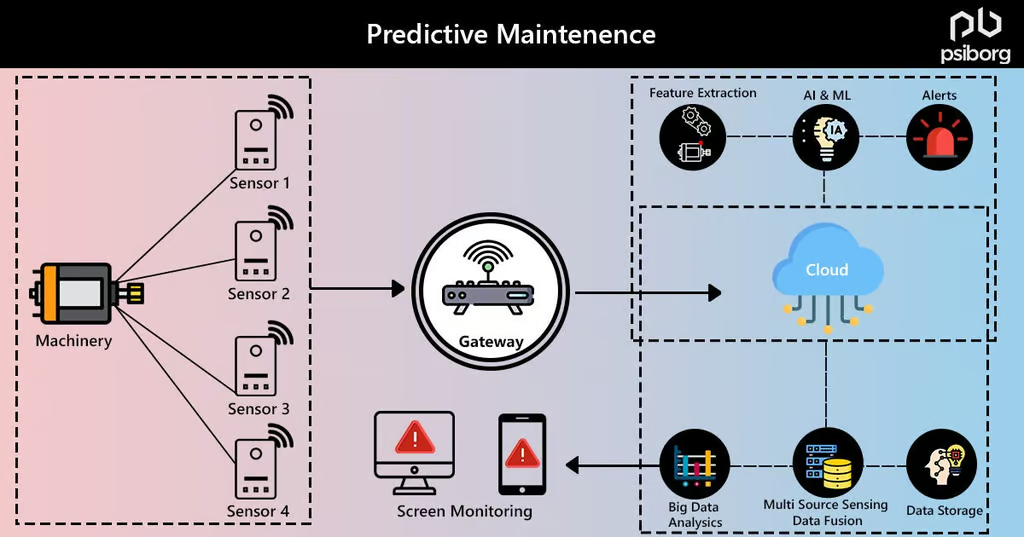
- Concept :
- Définition : La maintenance prédictive utilise les données recueillies en temps réel et historiques pour prévoir les pannes avant qu’elles ne surviennent. Cela permet de planifier des interventions de maintenance basées sur l’état réel des équipements plutôt que sur des calendriers fixes.
- Outils et Techniques : Utilisation de l’apprentissage automatique et des modèles statistiques pour analyser les tendances et prédire les défaillances.
- Avantages :
- Réduction des Coûts : En intervenant uniquement lorsque nécessaire, la maintenance prédictive réduit les coûts liés aux interventions inutiles et minimise les temps d’arrêt non planifiés.
- Amélioration de la Disponibilité des Équipements : En prévoyant les défaillances, les entreprises peuvent planifier les réparations pendant les périodes de faible activité, améliorant ainsi la disponibilité des équipements.
- Exemples d’Application :
- Industrie Manufacturière : Prédiction des pannes de machines-outils en analysant les cycles de fonctionnement et les signes précurseurs de défaillance.
- Industrie Énergétique : Surveillance des turbines et des générateurs pour prévoir les besoins de maintenance et éviter des interruptions de service coûteuses.
Réduction des Pannes Inattendues
- Stratégies :
- Intégration de la Maintenance Préventive et Prédictive : En combinant la maintenance préventive (basée sur des intervalles réguliers) avec la maintenance prédictive (basée sur l’état), les entreprises peuvent réduire les pannes inattendues en intervenant avant que des problèmes majeurs n’émergent.
- Systèmes de Gestion de Maintenance Assistée par Ordinateur (GMAO) : Les systèmes GMAO permettent de planifier et de suivre les tâches de maintenance, assurant une meilleure gestion des interventions et des historiques de maintenance.
- Avantages :
- Amélioration de la Performance des Équipements : En réduisant les pannes inattendues, les équipements fonctionnent de manière plus fiable et efficace, ce qui améliore la productivité globale.
- Réduction des Interruptions de Production : Les pannes inattendues peuvent entraîner des interruptions de production coûteuses. En prévoyant et en prévenant les défaillances, les entreprises minimisent ces interruptions.
2. Optimisation de la maintenance
Optimiser la maintenance améliore la performance des équipements tout en réduisant les coûts. Cela inclut une planification précise, une gestion efficace des coûts et des actions visant à prolonger la durée de vie des équipements.
- Planification optimisée
Élaborez des programmes de maintenance basés sur des données pour réduire les temps d’arrêt imprévus et améliorer la disponibilité des équipements. - Réduction des coûts de maintenance
Minimisez les dépenses en adoptant des techniques de maintenance préventive industrielle et en utilisant des outils d’analyse pour détecter les problèmes tôt. - Augmentation de la durée de vie des équipements
Prolongez la vie des équipements grâce à une maintenance régulière et à des technologies avancées pour prévenir l’usure prématurée.
3. Amélioration de la productivité
Améliorer la productivité passe par l’optimisation des équipements pour minimiser les interruptions et maximiser leur disponibilité.
- Réduction des temps d’arrêt
Réduisez les interruptions de production grâce à des stratégies de maintenance préventive et à une gestion efficace des pannes. - Augmentation de la disponibilité des équipements
Assurez une disponibilité maximale des équipements en mettant en place des programmes de maintenance adaptés et en surveillant les performances en temps réel.
4. Sécurité renforcée
Assurer une sécurité optimale est crucial pour protéger les employés et les équipements. Voici comment y parvenir :
- Détection des risques potentiels
Identifiez et évaluez les dangers potentiels avant qu’ils ne causent des incidents, grâce à une surveillance continue et une analyse proactive des risques. - Réduction des accidents du travail
Minimisez les accidents en mettant en œuvre des pratiques de maintenance rigoureuses et en formant le personnel aux procédures de sécurité.
Les différentes technologies de maintenance
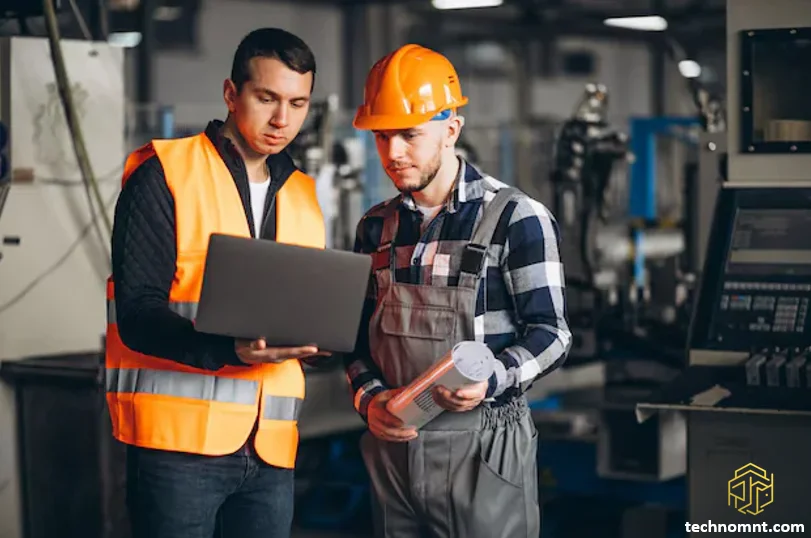
Dans le domaine industriel, les technologies de maintenance ont évolué pour répondre aux besoins croissants de performance, de sécurité, et de durabilité des équipements. Qu’il s’agisse de maintenance préventive, prédictive, ou corrective, chaque technologie offre des avantages spécifiques qui contribuent à l’efficacité des opérations.
1. L’IoT au service de la maintenance
L’un des objectifs majeurs d’une maintenance efficace est de minimiser les temps d’arrêt des machines. Pour ce faire, l’utilisation de l’IoT dans le cadre d’une maintenance prédictive s’avère être un atout considérable, notamment dans l’industrie 4.0.
L’IoT permet de prévoir les pannes avant qu’elles ne surviennent, permettant ainsi des interventions de maintenance ciblées et optimisées. Cette technologie joue un rôle clé dans l’amélioration continue de la productivité et de la compétitivité des entreprises industrielles.
Les capteurs connectés
L’Internet des Objets (IoT) joue un rôle crucial dans la maintenance industrielle, notamment en facilitant la maintenance prédictive. Les capteurs IoT installés sur les machines permettent de surveiller en continu divers paramètres comme les vibrations, la température, la pression, et la consommation d’énergie.
Cette surveillance continue aide à identifier les anomalies avant qu’elles ne provoquent des pannes, permettant ainsi une intervention ciblée et efficace.
La collecte et l’analyse des données
Les données collectées en temps réel par ces capteurs sont ensuite analysées à l’aide de logiciels avancés, souvent intégrés à des systèmes de GMAO (Gestion de Maintenance Assistée par Ordinateur).
L’analyse de ces données permet de détecter des tendances ou des anomalies qui pourraient indiquer une défaillance imminente, offrant ainsi une base solide pour la maintenance prédictive. Grâce à cette technologie, les entreprises peuvent optimiser leurs interventions, réduire les coûts de maintenance, et prolonger la durée de vie de leurs équipements.
Les applications pratiques
L’IoT trouve de nombreuses applications pratiques dans la maintenance industrielle. Par exemple, il permet une gestion avancée des alarmes, en adaptant les seuils d’intervention en fonction des données collectées.
De plus, l’intégration de l’IoT avec l’intelligence artificielle (IA) ouvre la voie à une automatisation accrue des processus de maintenance, permettant de prédire les pannes avec une précision inégalée. Cela se traduit par une réduction significative des temps d’arrêt, une optimisation des ressources, et une amélioration globale de la productivité des entreprises industrielles.
En somme, l’IoT, en partenariat avec des outils comme la GMAO 4.0, représente un atout indispensable pour les entreprises souhaitant adopter une stratégie de maintenance prédictive, tout en restant compétitives dans un environnement industriel de plus en plus exigeant.
2. L’intelligence artificielle et la maintenance prédictive
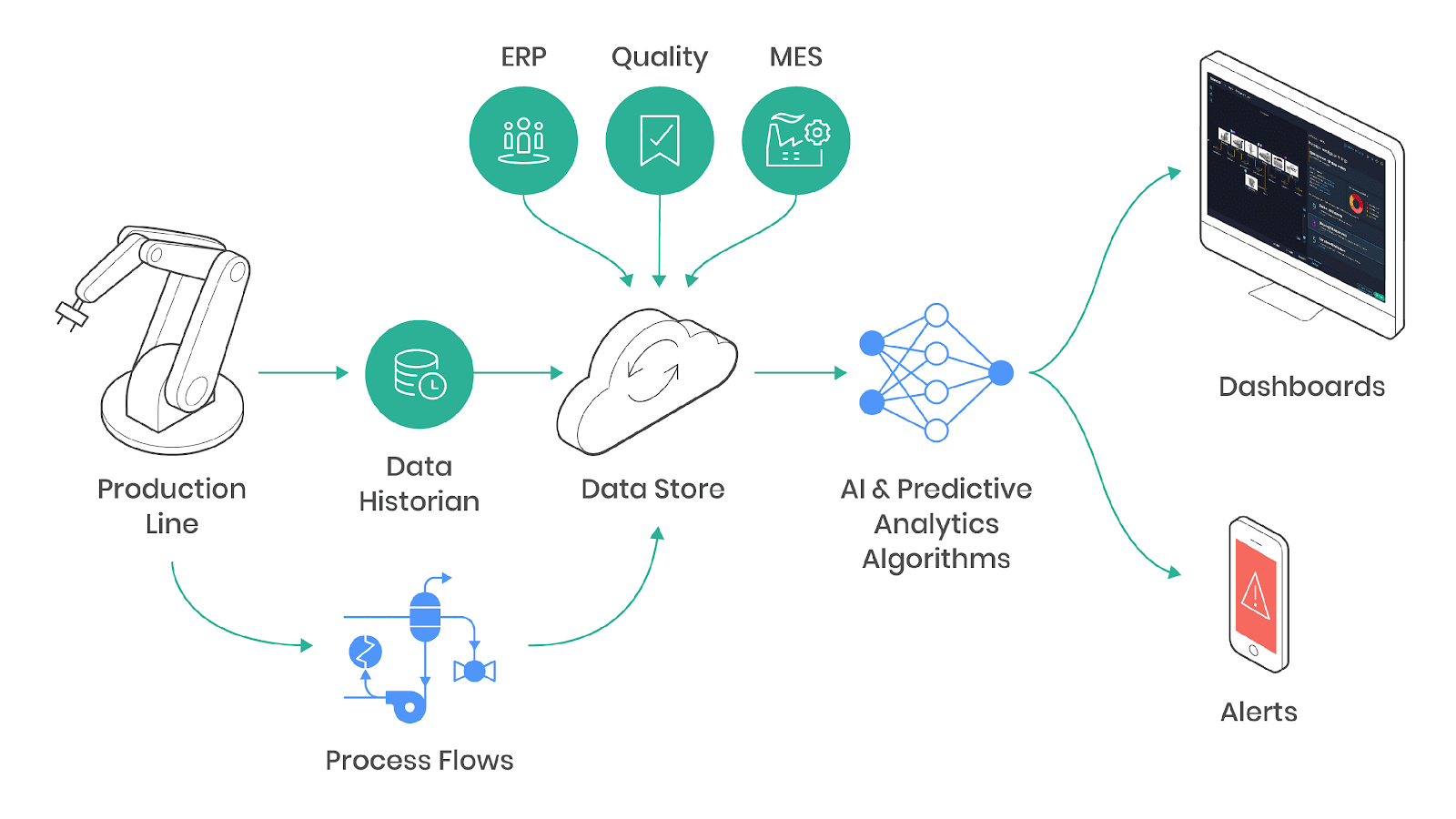
L’intelligence artificielle (IA) joue un rôle crucial dans l’évolution des stratégies de maintenance, notamment en passant d’une approche préventive à une maintenance prédictive. Grâce aux capacités de l’IA, les entreprises peuvent non seulement anticiper les défaillances mais aussi optimiser les opérations de maintenance pour garantir une efficacité maximale.
L’IA, à travers ses algorithmes d’apprentissage automatique, transforme la manière dont les données sont analysées et exploitées, permettant ainsi une prédiction précise des pannes et une meilleure gestion des ressources.
Les algorithmes d’apprentissage automatique
L’intelligence artificielle (IA) a révolutionné le domaine de la maintenance prédictive, notamment grâce aux algorithmes d’apprentissage automatique.
Ces algorithmes, nourris par des volumes massifs de données provenant des capteurs IoT, permettent d’analyser des schémas complexes de défaillance qui échappent souvent à l’œil humain.
Le Machine Learning s’améliore en permanence en apprenant à partir des données historiques, ce qui permet aux systèmes de maintenance de prévoir les pannes avant qu’elles ne surviennent.
La création de modèles prédictifs
La création de modèles prédictifs est au cœur de la maintenance prédictive. Ces modèles sont conçus en analysant les données collectées en temps réel à partir des équipements industriels.
Les experts en IA, en collaboration avec les équipes techniques, développent ces modèles pour détecter les premiers signes de défaillance. Cela permet de planifier des interventions au moment optimal, évitant ainsi des arrêts imprévus et coûteux. La précision de ces modèles est cruciale pour assurer une maintenance efficace et une disponibilité maximale des machines.
Les avantages de la maintenance prédictive
Adopter la maintenance prédictive présente de nombreux avantages pour les industries. Cette approche permet de planifier les interventions de maintenance de manière plus stratégique, réduisant ainsi les temps d’arrêt imprévus et optimisant la production.
Elle prolonge également la durée de vie des équipements en évitant les pannes graves et améliore la gestion des stocks de pièces de rechange en alignant les besoins réels avec les prévisions.
En fin de compte, la maintenance prédictive améliore la satisfaction des clients en assurant une continuité de service et en réduisant les coûts opérationnels. L’intégration de l’IA dans ce processus permet de viser un objectif ambitieux : la “zéro panne”, ce qui devient de plus en plus accessible même pour les PME grâce aux avancées technologiques récentes.
3. La réalité augmentée au service des techniciens
L’évolution des technologies numériques transforme radicalement le quotidien des techniciens de maintenance, notamment grâce à la réalité augmentée (RA). Cette technologie permet aux techniciens d’intégrer des éléments virtuels dans leur champ de vision, offrant ainsi une assistance directe lors des interventions.
Que ce soit pour visualiser en temps réel des informations techniques, bénéficier de l’assistance à distance d’un expert, ou encore anticiper et diagnostiquer les pannes, la réalité augmentée est en train de devenir un outil indispensable pour les professionnels de la maintenance dans divers secteurs tels que l’industrie, la maintenance multi-secteurs, et le transport.
La visualisation des données en temps réel
La réalité augmentée permet aux techniciens de superposer des informations numériques sur le monde réel. Par exemple, en utilisant des casques tels que le HoloLens de Microsoft, les techniciens peuvent voir les modèles 3D des équipements sur lesquels ils travaillent, accéder aux données en temps réel, et recevoir des instructions détaillées sans avoir besoin de consulter des manuels papier ou numériques. Cela améliore non seulement l’efficacité des interventions mais aussi la précision des diagnostics.
L’assistance à distance
Grâce à la réalité augmentée, un technicien sur site peut bénéficier de l’expertise d’un collègue ou d’un spécialiste à distance. En partageant en direct ce qu’il voit à travers son casque, l’expert peut guider le technicien à chaque étape de son intervention.
Cette fonctionnalité est particulièrement utile dans les situations où des compétences spécifiques sont requises, réduisant ainsi le besoin de déplacements et optimisant les ressources humaines disponibles.
Les cas d’utilisation
La réalité augmentée trouve des applications dans de nombreux secteurs. Par exemple, dans l’industrie, elle permet de réduire le temps moyen de réparation (MTTR) en fournissant aux techniciens toutes les informations nécessaires sur les équipements à entretenir.
Dans le domaine des transports, elle aide à planifier les interventions en fonction des données recueillies en temps réel, ce qui minimise les interruptions de service. Enfin, dans le secteur de la maintenance multi-secteurs, la réalité augmentée offre une solution pour gérer efficacement la diversité des équipements et des procédures, tout en améliorant la qualité des interventions.
Mise en œuvre d’une stratégie de maintenance basée sur les technologies
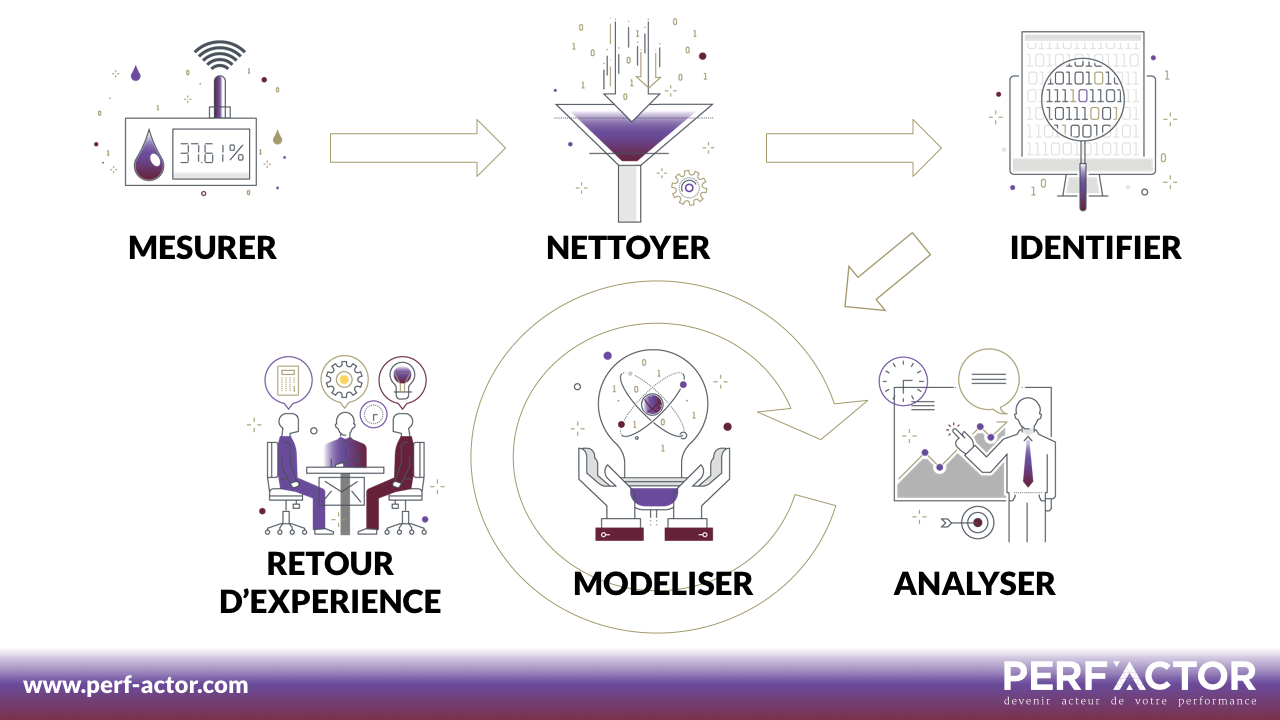
Dans le paysage industriel moderne, l’adoption d’une stratégie de maintenance basée sur les technologies est devenue un impératif pour les entreprises cherchant à optimiser leurs opérations et à rester compétitives. Cette approche innovante va au-delà des méthodes traditionnelles en intégrant des outils numériques avancés, des systèmes d’analyse prédictive et des solutions connectées pour transformer la façon dont les entreprises gèrent et entretiennent leurs équipements.
La mise en œuvre d’une telle stratégie représente un changement paradigmatique, passant d’une approche réactive à une approche proactive et prédictive de la maintenance. Elle promet non seulement de réduire les temps d’arrêt imprévus et les coûts associés, mais aussi d’améliorer la durée de vie des équipements, d’optimiser les performances opérationnelles et de renforcer la sécurité sur le lieu de travail.
Cependant, le passage à une stratégie de maintenance technologique n’est pas sans défis. Il nécessite une planification minutieuse, un investissement dans les bonnes technologies et une transformation culturelle au sein de l’organisation. Dans cette section, nous explorerons les étapes clés pour mettre en œuvre avec succès une stratégie de maintenance basée sur les technologies, en nous concentrant sur l’évaluation des besoins, le choix des technologies appropriées, l’intégration des données et la formation essentielle des équipes.
1. Les étapes clés d’une stratégie de maintenance technologique
La mise en place d’une stratégie de maintenance efficace basée sur les technologies nécessite une approche structurée. Voici les étapes essentielles à suivre :
a. Évaluation des besoins
Cette étape cruciale implique :
- Identification et hiérarchisation des équipements : Cataloguez tous les actifs en notant leur criticité, âge, état et fréquence d’utilisation.
- Analyse des données historiques : Exploitez les données existantes pour identifier les tendances de défaillance et d’usure.
- Évaluation des risques : Identifiez les dangers potentiels et leur impact sur la production et la sécurité.
- Définition des objectifs : Alignez vos objectifs de maintenance avec les priorités stratégiques de l’entreprise.
L’utilisation d’un logiciel de GMAO dès cette étape peut grandement faciliter la collecte et l’analyse des données nécessaires à une évaluation précise des besoins.
B. Choix des technologies adaptées
Sélectionnez les technologies les plus appropriées en fonction de vos besoins spécifiques :
- Systèmes de GMAO : Choisissez une solution qui s’intègre bien à vos processus existants et offre les fonctionnalités nécessaires.
- Capteurs IoT : Identifiez les équipements qui bénéficieraient le plus d’une surveillance en temps réel.
- Outils d’analyse prédictive : Sélectionnez des solutions capables de traiter vos données pour prédire les pannes potentielles.
- Réalité augmentée : Évaluez si cette technologie peut améliorer l’efficacité de vos techniciens sur le terrain.
Le choix des technologies doit se faire en tenant compte de votre budget, de l’expertise de votre équipe et de la compatibilité avec vos systèmes existants.
C. Intégration des données
L’intégration efficace des données est essentielle pour une stratégie de maintenance basée sur les technologies :
- Centralisation des données : Utilisez votre système GMAO comme point central pour toutes les informations de maintenance.
- Standardisation des processus : Établissez des procédures standard pour la collecte et la saisie des données.
- Connexion des systèmes : Assurez-vous que tous vos outils technologiques (capteurs, GMAO, ERP) communiquent efficacement entre eux.
- Qualité des données : Mettez en place des processus pour garantir l’exactitude et la pertinence des données collectées.
Une intégration réussie des données permettra une vision holistique de votre infrastructure de maintenance, facilitant ainsi la prise de décision basée sur des informations précises et actualisées.
d. Formation des équipes
La formation est cruciale pour assurer l’adoption et l’utilisation efficace des nouvelles technologies :
- Évaluation des compétences : Identifiez les lacunes en compétences au sein de votre équipe.
- Programmes de formation : Développez des formations adaptées à chaque rôle (techniciens, managers, analystes).
- Formation continue : Prévoyez des mises à jour régulières pour suivre l’évolution des technologies.
- Culture de l’apprentissage : Encouragez le partage des connaissances et l’amélioration continue au sein de l’équipe.
Investir dans la formation de votre personnel maximisera le retour sur investissement de vos technologies de maintenance et favorisera une culture d’innovation et d’efficacité.
En suivant ces étapes clés, votre entreprise sera bien positionnée pour mettre en œuvre une stratégie de maintenance technologique efficace, capable d’améliorer la fiabilité des équipements, d’optimiser les coûts et d’augmenter la productivité globale.
2. Les défis et les limites de la technologie de maintenance
La mise en œuvre des technologies de maintenance avancées, bien que prometteuse, s’accompagne de plusieurs défis et limites que les entreprises doivent surmonter pour en tirer pleinement parti.
Coût d’investissement élevé
L’adoption des technologies de maintenance modernes représente un investissement initial conséquent pour les entreprises, en particulier pour les PME aux budgets limités. Ces coûts comprennent :
- L’acquisition de nouveaux équipements et capteurs
- L’implémentation de logiciels spécialisés
- La formation du personnel
- L’intégration avec les systèmes existants
Pour gérer ces coûts, les entreprises peuvent :
- Adopter une approche progressive, en commençant par des projets pilotes à petite échelle
- Privilégier les solutions offrant un retour sur investissement rapide
- Explorer les options de financement ou de leasing pour répartir les coûts dans le temps
Sécurité des données et cybersécurité
L’interconnexion croissante des systèmes de maintenance expose les entreprises à de nouveaux risques en matière de sécurité :
- Vulnérabilités aux cyberattaques et au piratage
- Risques de fuite ou de vol de données sensibles
- Perturbations potentielles des opérations en cas de brèche
Pour renforcer la sécurité, les entreprises peuvent :
- Implémenter des protocoles de cybersécurité robustes
- Utiliser des solutions cloud sécurisées pour le stockage et le traitement des données
- Former régulièrement le personnel aux bonnes pratiques de sécurité
- Mettre en place des systèmes de détection et de réponse aux incidents
Changement culturel et organisationnel
L’adoption des technologies de maintenance avancées nécessite souvent un changement culturel profond au sein de l’entreprise :
- Résistance au changement de la part du personnel habitué aux méthodes traditionnelles
- Nécessité de développer de nouvelles compétences et d’adopter de nouvelles façons de travailler
- Besoin de repenser les processus et les structures organisationnelles
Pour faciliter cette transition, les entreprises peuvent :
- Communiquer clairement sur les avantages des nouvelles technologies
- Impliquer les employés dans le processus de transformation
- Offrir des formations continues et un accompagnement personnalisé
- Célébrer les succès et récompenser l’adoption des nouvelles pratiques
En relevant ces défis, les entreprises peuvent maximiser les bénéfices des technologies de maintenance modernes, améliorant ainsi leur efficacité opérationnelle, leur compétitivité et leur capacité d’innovation dans un marché en constante évolution.
Conclusion
Les technologies de maintenance représentent une véritable révolution dans le monde industriel. En permettant une approche proactive et prédictive, elles transforment radicalement la façon dont les entreprises gèrent leurs actifs et leurs opérations.
Les avantages sont nombreux : fiabilité accrue des équipements, optimisation des coûts, amélioration de la productivité et renforcement de la sécurité. Ces technologies offrent aux entreprises un avantage compétitif significatif dans un marché de plus en plus exigeant.
Il est crucial pour les entreprises d’aujourd’hui d’investir dans ces technologies de maintenance. Non seulement elles améliorent les performances actuelles, mais elles préparent également l’entreprise aux défis futurs. Avec l’émergence de concepts comme les jumeaux numériques, qui permettent de simuler et d’optimiser les processus industriels dans un environnement virtuel, l’avenir de la maintenance s’annonce encore plus prometteur.
En embrassant ces technologies, les entreprises ne font pas que moderniser leurs opérations de maintenance ; elles se positionnent à l’avant-garde de l’industrie 4.0, prêtes à relever les défis d’un monde en constante évolution.
Source :