La maintenance conditionnelle dans les grandes entreprises représente aujourd’hui une solution incontournable pour améliorer l’efficacité de leurs opérations et à optimiser la gestion de leurs actifs. Cette approche repose sur la surveillance continue des conditions réelles des équipements, permettant ainsi d’intervenir uniquement lorsque des signes de dégradation ou des anomalies sont détectés.
Contrairement aux méthodes de maintenance traditionnelles, la maintenance conditionnelle repose sur l’utilisation de capteurs IoT et de technologies avancées d’analyse des données. Les grandes entreprises, confrontées à des parcs machines complexes et à des exigences élevées de disponibilité, trouvent dans la maintenance conditionnelle une stratégie proactive qui réduit les coûts, améliore la sécurité, et prolonge la durée de vie des équipements.
Dans cet article, nous explorerons comment cette approche est mise en œuvre, ses avantages, et les défis spécifiques rencontrés dans des secteurs variés comme l’industrie manufacturière, le transport, et l’énergie.
Table of Contents
Maintenance Conditionnelle dans les Grandes Entreprises
Qu’est-ce que la maintenance conditionnelle ?
La maintenance conditionnelle est une stratégie proactive qui consiste à surveiller en temps réel l’état des équipements pour identifier les signes avant-coureurs de défaillance. Contrairement à la maintenance préventive, qui repose sur un calendrier fixe d’interventions, la maintenance conditionnelle se base sur l’analyse des données recueillies par des capteurs pour déclencher une action corrective uniquement lorsque cela est nécessaire. Cette approche permet de réduire les coûts, d’améliorer la productivité et de prolonger la durée de vie des équipements.
Contexte pour les grandes entreprises : Pour des entreprises de grande taille, qui gèrent des centaines voire des milliers d’actifs critiques, adopter une approche conditionnelle est devenu une nécessité. La complexité des opérations et l’importance stratégique des actifs rendent les arrêts imprévus coûteux, voire catastrophiques. La maintenance conditionnelle permet de minimiser ces risques tout en optimisant les ressources.
Importance stratégique pour les grandes entreprises
Les grandes entreprises investissent massivement dans des équipements coûteux et complexes. Toute panne inattendue peut entraîner des pertes financières significatives, interrompre la production, et nuire à la réputation de l’entreprise. Selon une étude de PwC, les entreprises utilisant une maintenance conditionnelle ont observé une réduction des arrêts de production non planifiés de 50 %, une économie de 30 % sur les coûts de maintenance et une amélioration de la sécurité de 20 % (Source PwC).
Les principes fondamentaux de la maintenance conditionnelle
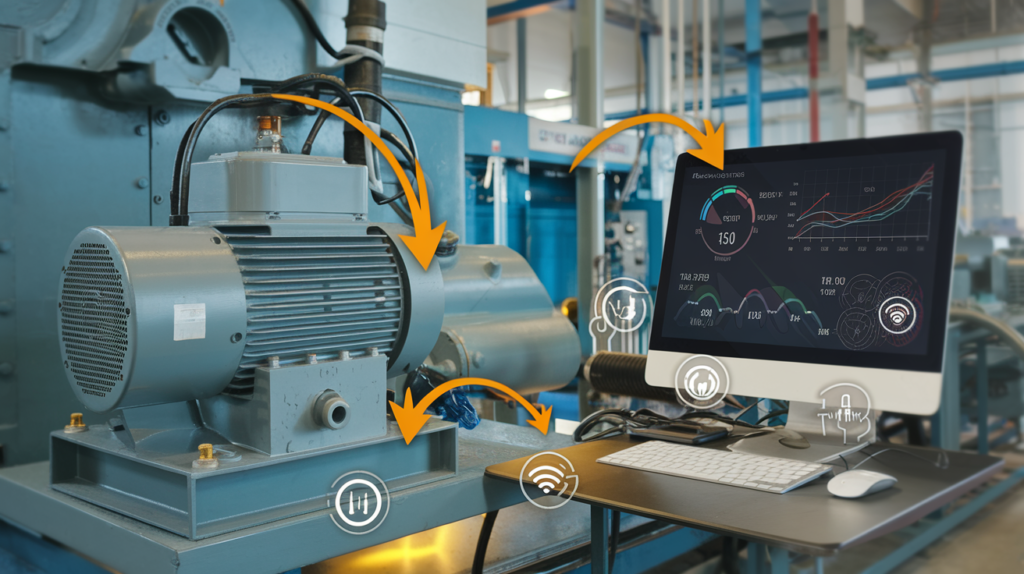
Surveillance des paramètres clés : Les indicateurs à suivre
Les paramètres à surveiller dépendent du type d’équipement et de l’environnement dans lequel il fonctionne. Les plus couramment utilisés sont :
- Vibrations : Les capteurs de vibration sont utilisés pour détecter les anomalies dans les pièces rotatives, telles que les roulements ou les arbres de transmission. Une augmentation anormale des vibrations indique souvent une usure ou un déséquilibre.
- Température : Les variations de température peuvent signaler des problèmes de friction, des surcharges électriques ou des dysfonctionnements dans le système de refroidissement.
- Pression : Une pression anormale dans les systèmes hydrauliques ou pneumatiques peut indiquer des fuites, des blocages ou des défaillances de valves.
- Niveau sonore : Les changements dans le bruit des machines peuvent être le signe d’un dysfonctionnement, comme une usure des engrenages.
Exemple concret : L’entreprise SKF, spécialisée dans les roulements, utilise des capteurs de vibration pour surveiller en temps réel l’état de ses produits, permettant ainsi de détecter les anomalies avant qu’elles n’entraînent des pannes (SKF Monitoring Solutions).
Utilisation des technologies modernes : L’impact des capteurs IoT et de l’analyse des données
La collecte des données est rendue possible grâce aux capteurs IoT (Internet des Objets) qui transmettent des informations en temps réel aux systèmes de gestion. Ces données sont ensuite analysées par des logiciels de Big Data et d’intelligence artificielle pour prédire les défaillances potentielles.
Exemple d’application : Airbus utilise des capteurs IoT sur ses avions pour surveiller les performances des moteurs en vol. Les données collectées sont analysées pour anticiper les problèmes et planifier les interventions de maintenance lors des escales, réduisant ainsi les retards et augmentant la disponibilité des avions (Airbus Predictive Maintenance).
Avantages de la maintenance conditionnelle
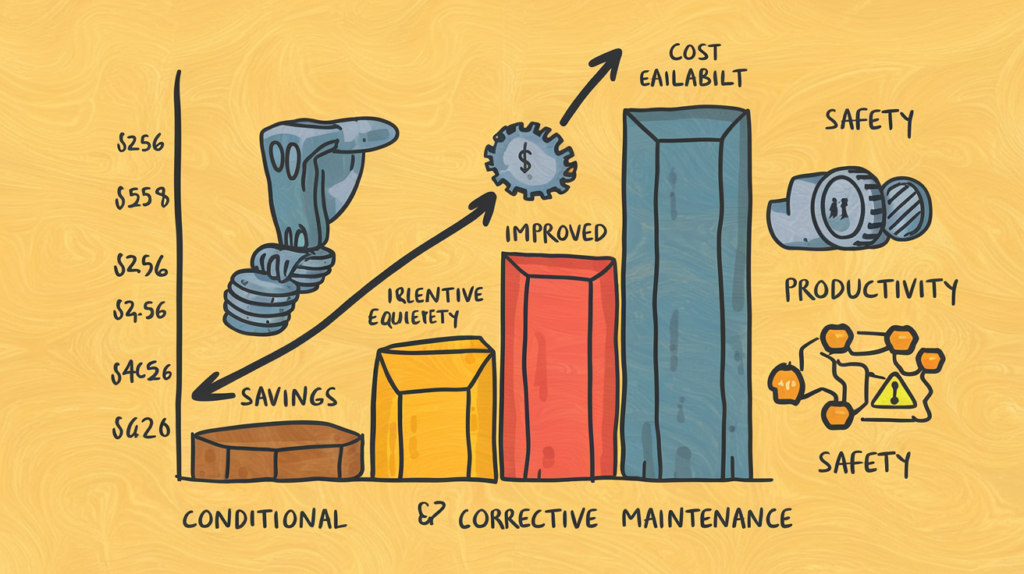
Réduction des coûts de maintenance
L’un des principaux avantages de la maintenance conditionnelle dans les grandes entreprises est la réduction des coûts. En intervenant uniquement lorsque cela est nécessaire, les entreprises évitent les inspections inutiles et les remplacements prématurés de pièces.
Données chiffrées : Une étude réalisée par Deloitte montre que les entreprises qui adoptent une maintenance conditionnelle peuvent économiser jusqu’à 40 % sur leurs coûts de maintenance annuels (Deloitte Maintenance Study).
Amélioration de la disponibilité des équipements
En surveillant l’état réel des machines, les entreprises peuvent planifier les interventions au moment le plus opportun, minimisant ainsi les arrêts de production imprévus.
Exemple concret : Caterpillar, fabricant d’équipements lourds, a intégré des systèmes de maintenance conditionnelle dans ses machines. Les clients ont observé une réduction de 20 % des arrêts imprévus, ce qui a conduit à une augmentation de la productivité globale (Caterpillar Case Study).
Sécurité accrue et réduction des risques
La détection précoce des anomalies réduit le risque de pannes catastrophiques, diminuant ainsi le risque d’accidents graves.
Exemple : Dans l’industrie chimique, l’entreprise Dow Chemical utilise des capteurs de surveillance pour détecter des anomalies dans les systèmes sous pression, réduisant ainsi le risque de fuites dangereuses (Dow Chemical Safety Program).
Mise en œuvre d’une stratégie de maintenance conditionnelle
La mise en œuvre d’une stratégie de maintenance conditionnelle est un processus complexe qui nécessite une planification minutieuse et une approche structurée. Cette phase inclut l’évaluation initiale des besoins, la sélection des technologies et des outils logiciels, ainsi que la formation du personnel. Voici un guide détaillé pour réussir cette transition dans les grandes entreprises.
Évaluation initiale des besoins et analyse des actifs
Avant de se lancer dans l’intégration de la maintenance conditionnelle, il est impératif de réaliser une analyse approfondie des actifs existants. Cette étape permet d’identifier les équipements critiques et de comprendre leurs comportements de défaillance. Pour une grande entreprise, cela implique :
- Collecte des données historiques : Examiner les données des pannes passées pour identifier les modèles de défaillance. Par exemple, les systèmes de ventilation ou les moteurs électriques peuvent montrer des signes de défaillance récurrents à cause de vibrations excessives ou de surchauffe.
- Identification des paramètres à surveiller : Déterminer les indicateurs de performance clés (KPI) pour chaque équipement. Les paramètres typiques incluent la température, les vibrations, la pression, et l’humidité. Par exemple, dans une usine chimique, la surveillance des niveaux de température et de pression est essentielle pour prévenir les accidents.
- Fixation des seuils d’alerte : Établir des seuils basés sur les valeurs normales de fonctionnement et les écarts acceptables. Lorsque ces seuils sont dépassés, des alertes doivent être envoyées automatiquement aux équipes de maintenance. Cela permet une intervention rapide avant que les problèmes ne s’aggravent.
Un exemple concret est celui de BASF, qui a utilisé des capteurs pour surveiller les niveaux de vibration de ses pompes, réduisant ainsi les temps d’arrêt imprévus de 30 %.
Choix des technologies et des logiciels adaptés
La sélection des bonnes technologies est une étape cruciale pour une mise en œuvre réussie de la maintenance conditionnelle. Les grandes entreprises ont besoin de solutions robustes, capables de gérer de vastes quantités de données et d’intégrer divers types de capteurs IoT. Voici quelques options populaires :
- IBM Maximo : Cette solution offre des fonctionnalités avancées de gestion des actifs et de maintenance conditionnelle. Elle permet de collecter des données en temps réel et de les analyser pour identifier les anomalies. IBM Maximo est utilisé par des entreprises comme Caterpillar, qui a pu réduire ses coûts de maintenance de 15 % grâce à cette plateforme.
- SAP Predictive Maintenance : SAP propose une solution intégrée qui s’appuie sur des algorithmes prédictifs pour analyser les données des capteurs et anticiper les défaillances. Par exemple, Siemens utilise SAP pour surveiller ses équipements industriels, réduisant ainsi les interruptions de production imprévues.
- Prisma Predictive Maintenance : Ce logiciel est spécialement conçu pour les grandes infrastructures, permettant une visualisation intuitive des données des capteurs et une analyse prédictive. Prisma a été adopté par General Electric pour surveiller ses turbines, améliorant leur fiabilité de 25 %.
La clé du succès réside dans l’intégration de ces outils avec les systèmes existants de Gestion de Maintenance Assistée par Ordinateur (GMAO), permettant une vue d’ensemble centralisée des données et une meilleure prise de décision.
Formation et adoption par le personnel
Une fois les technologies choisies, l’étape suivante consiste à former le personnel pour assurer une adoption efficace de la maintenance conditionnelle. La résistance au changement est courante, en particulier dans les grandes entreprises où les techniciens sont habitués aux méthodes traditionnelles de maintenance. Voici les actions à entreprendre :
- Programmes de formation ciblés : Les techniciens doivent être formés à l’utilisation des nouveaux outils logiciels et à l’interprétation des données des capteurs. Par exemple, Michelin a lancé un programme de formation complet pour ses équipes, leur apprenant à identifier les signes de défaillance à partir des données en temps réel.
- Simulations et cas pratiques : Organiser des simulations en conditions réelles aide les équipes à se familiariser avec les nouvelles technologies. Les ateliers pratiques permettent aux techniciens de comprendre comment les alertes sont générées et quelles actions correctives doivent être prises.
- Suivi et support continu : Offrir un support technique continu est essentiel pour aider les équipes à surmonter les défis initiaux. Cela inclut un accès aux experts et des mises à jour régulières des logiciels pour intégrer de nouvelles fonctionnalités.
Un exemple de succès est celui de Michelin, qui a mis en place un programme de formation intensif pour ses équipes de maintenance, augmentant l’adoption des nouvelles technologies de 80 % en un an. Grâce à cela, Michelin a réduit ses temps d’arrêt non planifiés de 20 %.
Exemple d’implémentation réussie : Schneider Electric
Schneider Electric a déployé une stratégie de maintenance conditionnelle sur l’ensemble de ses sites industriels, utilisant des capteurs IoT pour surveiller les équipements critiques. L’entreprise a choisi une combinaison de logiciels GMAO intégrés et de capteurs avancés pour analyser les paramètres tels que les niveaux de vibration et de température. En formant ses équipes et en intégrant ces outils dans ses processus, Schneider Electric a pu réduire ses coûts de maintenance de 25 % et augmenter la disponibilité des équipements de 15 %.
Études de cas : Succès dans les grandes entreprises
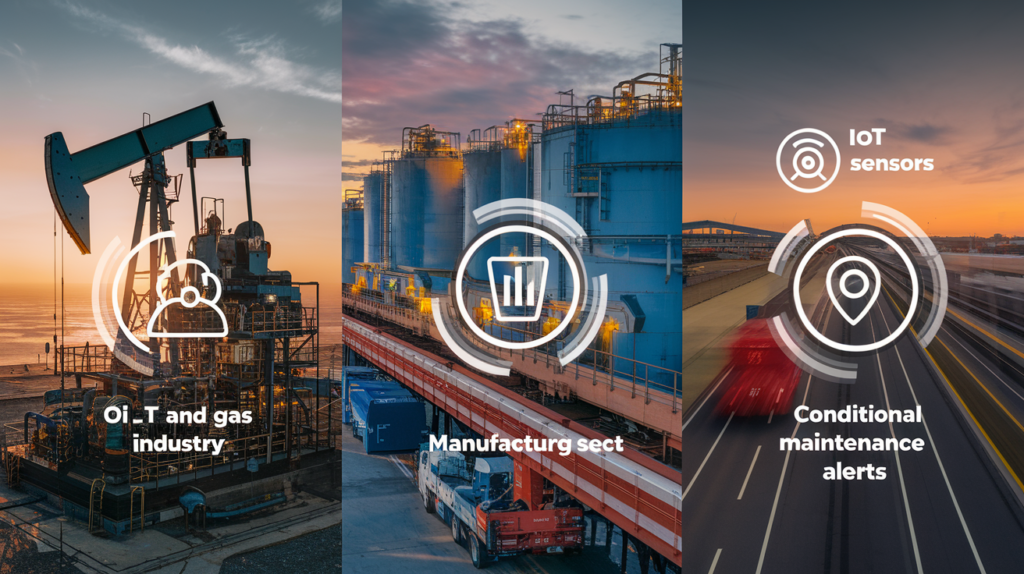
Industrie pétrolière et gazière
Dans l’industrie pétrolière, Shell a intégré des capteurs IoT sur ses plateformes offshore pour surveiller les vibrations et la pression. Grâce à cette approche, Shell a réduit ses coûts de maintenance de 20 % et amélioré la sécurité de 15 % (Shell Oil & Gas Case Study).
Secteur manufacturier
L’usine Bosch en Allemagne a mis en œuvre une stratégie de maintenance conditionnelle sur ses lignes de production. Les capteurs IoT ont permis de détecter des anomalies, réduisant les temps d’arrêt de 30 % (Bosch Manufacturing Case Study).
Transport et logistique
DHL utilise des capteurs pour surveiller l’état de ses véhicules. Cette stratégie a permis de prolonger la durée de vie des camions de 25 % et de réduire les pannes en cours de livraison de 15 % (DHL Predictive Maintenance).
Défis et perspectives d’avenir
Défis à relever
La mise en œuvre d’une stratégie de maintenance conditionnelle dans les grandes entreprises présente plusieurs défis, qu’il est crucial de surmonter pour garantir son succès. Ces défis incluent des aspects techniques, humains et organisationnels qui nécessitent une attention particulière.
1. Collecte et fiabilité des données
L’un des principaux défis de la maintenance conditionnelle réside dans la collecte de données précises et leur fiabilité. Les capteurs IoT et les systèmes de surveillance en temps réel génèrent d’énormes quantités de données. Cependant, pour que la maintenance conditionnelle soit efficace, ces données doivent être de haute qualité et représentatives des conditions réelles de l’équipement. Les erreurs dans la collecte de données ou l’utilisation de capteurs mal calibrés peuvent entraîner de fausses alertes ou des évaluations erronées de l’état des équipements, ce qui pourrait entraîner des coûts supplémentaires ou des défaillances imprévues.
De plus, pour être vraiment efficaces, ces données doivent être analysées en temps réel. Cela nécessite des infrastructures informatiques puissantes et des solutions logicielles robustes qui peuvent gérer, traiter et analyser rapidement ces informations. L’utilisation d’algorithmes avancés de maintenance prédictive est essentielle pour transformer les données collectées en informations exploitables. Par exemple, un équipement de production dans le secteur manufacturier, tel qu’une presse à injection plastique, pourrait présenter des signes de défaillance en raison de températures et de vibrations anormales. Si ces signaux sont ignorés à cause de données incohérentes, l’équipement pourrait tomber en panne et provoquer une interruption coûteuse de la production.
2. Gestion du changement
La gestion du changement est un autre défi majeur lors de la mise en œuvre de la maintenance conditionnelle. L’introduction de nouvelles technologies et de processus peut entraîner de la résistance au sein des équipes de maintenance, particulièrement dans les grandes entreprises où les employés sont habitués à des méthodes traditionnelles de travail. Les techniciens et ingénieurs, habitués à des stratégies de maintenance préventive ou réactive, peuvent être réticents à adopter de nouvelles pratiques basées sur des données en temps réel.
Pour surmonter ce défi, il est essentiel de mettre en place des programmes de formation adaptés. Ces programmes doivent non seulement enseigner l’utilisation des nouveaux outils et logiciels, mais aussi sensibiliser les équipes aux avantages de la maintenance conditionnelle. Un accompagnement personnalisé, des ateliers pratiques, et un support technique continu peuvent également faciliter l’adoption de cette nouvelle approche. Par exemple, la société Thales a mis en place des sessions de formation pratiques pour ses ingénieurs afin de les rendre à l’aise avec les nouvelles technologies et améliorer leur adoption.
De plus, il est important que les dirigeants montrent l’exemple et appuient le changement. La communication claire sur les avantages économiques et opérationnels de la maintenance conditionnelle est cruciale pour minimiser les résistances et encourager l’adhésion de tous les acteurs impliqués.
Évolutions futures : Vers l’Industrie 4.0
L’intégration de la maintenance conditionnelle dans les grandes entreprises marque une étape importante dans l’évolution vers l’Industrie 4.0, une ère où l’intelligence artificielle (IA), le Big Data, et les jumeaux numériques jouent un rôle fondamental. Ces technologies sont en train de transformer la manière dont les entreprises gèrent la maintenance de leurs équipements et prévoient les défaillances.
1. L’intégration de l’IA et du Big Data
L’intelligence artificielle et le Big Data sont des moteurs clés de l’évolution de la maintenance conditionnelle. Grâce à des algorithmes de machine learning, il est désormais possible de prédire avec une grande précision quand un équipement risque de tomber en panne, et ce, bien avant que des signes évidents de défaillance n’apparaissent. Par exemple, un système de surveillance des moteurs électriques pourrait analyser en continu des milliers de points de données — tels que la température, les vibrations et les courants électriques — pour identifier des tendances subtiles qui pourraient passer inaperçues à l’œil nu. Ces systèmes sont capables d’apprendre et de s’adapter aux nouvelles données au fur et à mesure de leur accumulation, offrant ainsi des prévisions de défaillance de plus en plus précises avec le temps.
Le Big Data permet de collecter et d’analyser une immense quantité de données provenant de diverses sources, comme les capteurs IoT, les historiques de maintenance, les rapports de performance, et plus encore. En combinant ces données, les entreprises peuvent non seulement prédire les pannes, mais aussi optimiser les intervalles de maintenance et prolonger la durée de vie de leurs équipements.
2. Les jumeaux numériques : Une révolution pour la maintenance conditionnelle
Les jumeaux numériques sont des répliques virtuelles exactes d’équipements physiques qui permettent aux entreprises de simuler, de surveiller et d’analyser l’état des machines en temps réel. Ces modèles virtuels, intégrés avec des données provenant de capteurs IoT, peuvent être utilisés pour effectuer des simulations et tester des scénarios de maintenance avant d’intervenir physiquement sur les équipements. Par exemple, dans une usine de production automobile, un jumeau numérique d’un robot de soudure peut simuler diverses conditions de fonctionnement pour détecter des anomalies potentielles dans son mouvement ou sa performance avant qu’elles ne causent une défaillance.
L’utilisation des jumeaux numériques permet non seulement de réduire les coûts et de minimiser les risques associés à la maintenance, mais elle offre également une optimisation continue des processus de maintenance. Les entreprises peuvent ajuster leurs stratégies en temps réel, en fonction des données précises recueillies sur l’état de leurs équipements. Cette approche ouvre la voie à une gestion des actifs plus efficace et proactive.
3. Automatisation et maintenance autonome
L’automatisation et la maintenance autonome sont également des tendances fortes de l’Industrie 4.0. À mesure que les technologies de maintenance conditionnelle se perfectionnent, il devient possible d’automatiser les actions de maintenance. Par exemple, une machine peut non seulement détecter une défaillance imminente, mais aussi s’ajuster automatiquement pour éviter la panne, en ajustant les paramètres de fonctionnement. Cela réduit la dépendance à l’intervention humaine et permet une gestion plus efficace des actifs.
Les robots de maintenance autonomes pourraient également être utilisés pour effectuer des réparations simples sans intervention humaine, comme resserrer des vis ou appliquer de la lubrification sur des composants spécifiques. Cette évolution pourrait transformer radicalement le paysage de la maintenance industrielle, permettant une réduction des coûts et une amélioration de la sécurité.
==> Les défis liés à la mise en œuvre de la maintenance conditionnelle sont réels, mais avec les bonnes stratégies et technologies, les grandes entreprises peuvent surmonter ces obstacles. L’avenir de la maintenance conditionnelle semble prometteur, particulièrement avec l’intégration de l’IA, du Big Data, des jumeaux numériques et de l’automatisation. Ces technologies feront de la maintenance conditionnelle une partie intégrante de l’Industrie 4.0, permettant aux entreprises d’améliorer leur efficacité opérationnelle tout en réduisant les coûts et en prolongeant la durée de vie de leurs équipements.
Conclusion
La maintenance conditionnelle est une approche stratégique qui permet aux grandes entreprises d’améliorer la performance de leurs équipements tout en réduisant les coûts. Les études de cas présentées montrent clairement l’impact positif de cette stratégie sur l’efficacité opérationnelle. Les entreprises doivent envisager cette transition pour rester compétitives et tirer parti des technologies de l’Industrie 4.0.
Pour en savoir plus sur la mise en œuvre de la maintenance conditionnelle, explorez nos guides sur la GMAO et les solutions d’analyse prédictive.