Imaginez une usine automobile où une panne imprévue entraîne des retards de production coûteux. Ce scénario est évité grâce à la maintenance prédictive, une révolution dans le domaine industriel. En utilisant l’analyse des données pour anticiper les pannes, la maintenance prédictive permet aux entreprises de rester en avance sur les problèmes potentiels, réduisant ainsi les coûts et augmentant la fiabilité des équipements. Avec l’évolution rapide des technologies, la maintenance prédictive s’impose comme une solution incontournable pour les entreprises cherchant à optimiser leurs opérations.
Table of Contents
Partie 1 : Comprendre la Maintenance Prédictive
Qu’est-ce que la Maintenance Prédictive ?
La maintenance prédictive est une approche proactive qui utilise des technologies avancées pour surveiller l’état des équipements et prédire les pannes avant qu’elles ne surviennent. Contrairement à la maintenance corrective industrielle, qui intervient après une panne, ou à la maintenance préventive, basée sur des calendriers fixes, la maintenance prédictive se concentre sur l’état réel des équipements.
Différences avec la Maintenance Corrective et Préventive
- Maintenance Corrective : Réagir après qu’une panne se soit produite, entraînant souvent des temps d’arrêt imprévus. Par exemple, si une machine de production tombe en panne pendant un cycle de production, cela peut entraîner un arrêt coûteux et imprévu, perturbant la chaîne de production. Source : Scribbr
- Maintenance Préventive : Planifier des interventions régulières pour éviter les pannes, mais sans tenir compte de l’état actuel des machines. Par exemple, une machine peut être inspectée tous les six mois, même si elle fonctionne parfaitement bien entre les inspections. Source : Plant Services
- Maintenance Prédictive : Basée sur des données en temps réel, elle intervient juste avant qu’une panne ne survienne, maximisant la durée de vie des équipements et minimisant les coûts. Par exemple, des capteurs sur une pompe peuvent détecter une usure anormale, permettant une intervention avant qu’une panne ne se produise. Source : Forbes
Comment Fonctionne la Maintenance Prédictive ?
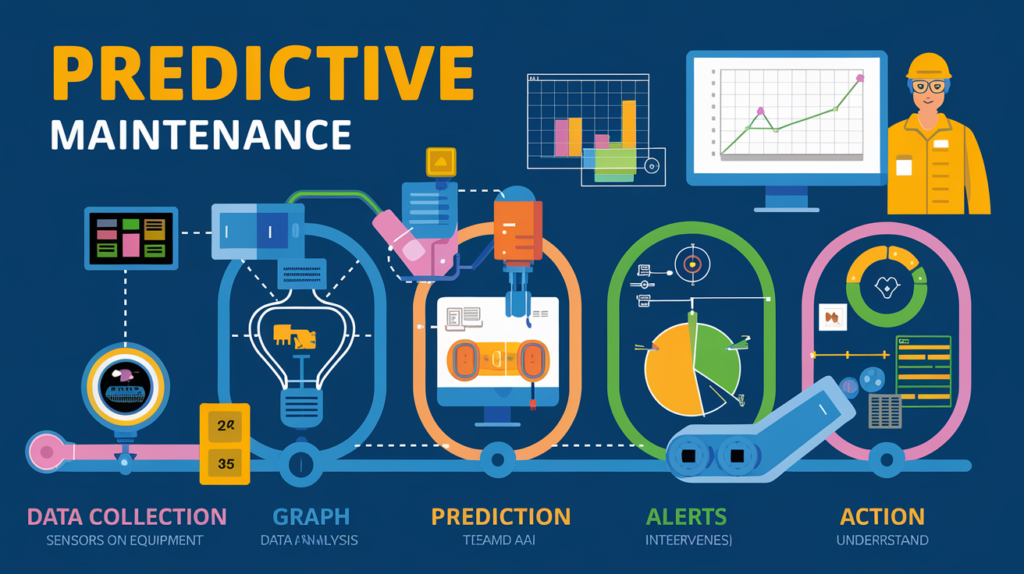
La maintenance prédictive repose sur plusieurs étapes clés, chacune jouant un rôle crucial dans la prévention des pannes.
1. Collecte de Données
Des capteurs sont installés sur les machines pour surveiller divers paramètres comme les vibrations, la température, et les niveaux d’huile. Ces données sont ensuite transmises à un système central pour analyse. Par exemple, un capteur de vibration sur un moteur peut mesurer les variations dans les vibrations, détectant des anomalies qui pourraient indiquer un problème imminent. Source : IoT For All
2. Analyse des Données
Les données collectées sont analysées à l’aide de techniques avancées telles que l’intelligence artificielle (IA) et l’apprentissage automatique (ML). Ces technologies identifient les anomalies et prédisent les défaillances potentielles. Par exemple, des algorithmes d’apprentissage automatique peuvent analyser les tendances de température et de vibration pour prédire une défaillance de roulement dans une machine. Source : TechTarget
3. Prédiction et Action
Une fois qu’une anomalie est détectée, une alerte est générée, permettant aux équipes de maintenance industrielle d’intervenir avant qu’une panne ne se produise. Par exemple, si un capteur détecte une augmentation anormale des vibrations, il peut déclencher une alerte pour inspecter la machine avant qu’une panne majeure ne survienne. Source : Harvard Business Review
4. Technologies Utilisées
La maintenance prédictive utilise des technologies comme l’Internet des objets (IoT), l’IA, et le cloud computing. Ces technologies permettent de collecter, analyser, et interpréter les données en temps réel, offrant ainsi une vision précise de l’état des équipements. Par exemple, des systèmes IoT connectent des capteurs à une plateforme cloud où les données sont traitées et analysées en temps réel. Source : Analytics Insight
Partie 2 : Les Avantages de la Maintenance Prédictive
Optimisation de la Production
La maintenance prédictive joue un rôle crucial dans l’optimisation de la production industrielle.
Réduction des Temps d’Arrêt
En anticipant les pannes, la maintenance prédictive réduit les arrêts de production imprévus, garantissant ainsi une continuité des opérations.
- Exemple concret : Dans une usine automobile, la maintenance prédictive a permis de prévenir les pannes de robots de soudage, évitant ainsi des interruptions coûteuses de la chaîne de production. Source : McKinsey & Company
Augmentation de la Disponibilité des Équipements
Les équipements sont disponibles plus longtemps, car les interventions de maintenance sont planifiées de manière optimale, juste avant qu’une panne ne survienne.
- Exemple concret : Une ligne de production équipée de systèmes de maintenance prédictive peut maintenir une disponibilité de 95 % au lieu de 85 %, augmentant ainsi la productivité globale. Source : Deloitte
Réduction des Coûts
La maintenance prédictive est également une stratégie efficace pour réduire les coûts de maintenance et d’exploitation.
Diminution des Coûts de Maintenance
En évitant les pannes majeures et en optimisant les interventions, la maintenance prédictive permet de réduire les coûts associés aux réparations et aux remplacements d’équipements.
- Exemple concret : En prévoyant les défaillances des équipements de chauffage, ventilation et climatisation (CVC), les entreprises peuvent éviter des réparations coûteuses et prolonger la durée de vie des équipements. Source : Frost & Sullivan
Prolongation de la Durée de Vie des Équipements
En surveillant constamment l’état des machines et en intervenant au bon moment, la maintenance prédictive prolonge la durée de vie des équipements, retardant ainsi les investissements en nouveaux matériels.
- Exemple concret : Des analyses de vibrations sur des moteurs électriques permettent de détecter des problèmes mineurs avant qu’ils n’affectent gravement la performance du moteur, prolongant ainsi sa durée de vie. Source : Industrial Maintenance & Plant Operation
Amélioration de la Sécurité
La sécurité des travailleurs est également renforcée grâce à la maintenance prédictive.
Détection Précoce des Anomalies
Les anomalies sont détectées bien avant qu’elles ne deviennent critiques, réduisant ainsi les risques d’accidents sur le lieu de travail.
- Exemple concret : La détection précoce des défauts dans les systèmes de freinage des machines peut prévenir des accidents potentiellement graves. Source : Journal of Safety Research
Réduction des Risques d’Accidents
En intervenant préventivement, les équipes de maintenance peuvent éviter les situations dangereuses, améliorant ainsi la sécurité globale de l’usine.
- Exemple concret : La maintenance prédictive peut identifier des défaillances potentielles dans les systèmes de sécurité des équipements, réduisant ainsi le risque d’accidents. Source : Safety Science
Prise de Décision Éclairée
La maintenance prédictive fournit des données fiables qui facilitent la prise de décisions stratégiques.
Données Fiables pour une Meilleure Planification
Les informations précises sur l’état des équipements permettent de planifier les interventions de maintenance de manière plus efficace, réduisant ainsi les incertitudes et les erreurs.
- Exemple concret : Une analyse détaillée des performances des équipements permet de planifier les maintenances en fonction des cycles de production, optimisant ainsi l’utilisation des ressources. Source : Gartner
Partie 3 : Mise en Œuvre de la Maintenance Prédictive

Les Étapes Clés de la Mise en Œuvre
La mise en œuvre de la maintenance prédictive nécessite une planification rigoureuse et une sélection judicieuse des technologies.
1. Identification des Équipements Critiques
Il est essentiel de déterminer quels équipements sont les plus critiques pour la production et de les prioriser dans la mise en œuvre de la maintenance prédictive.
- Exemple concret : Une entreprise de production alimentaire peut commencer par les équipements de traitement des aliments, qui sont essentiels à la qualité et à la sécurité des produits. Source : Food Processing
2. Choix des Technologies Adaptées
Sélectionner les technologies et les capteurs appropriés en fonction des besoins spécifiques de chaque équipement.
- Exemple concret : Pour des machines de précision, des capteurs de vibrations haute résolution peuvent être nécessaires, tandis que des capteurs de température peuvent suffire pour des équipements moins sensibles. Source : IEEE Spectrum
3. Collecte et Analyse des Données
Mettre en place un système robuste pour collecter et analyser les données entemps réel.
- Exemple concret : Une plateforme cloud peut être utilisée pour centraliser les données provenant de différents capteurs, facilitant ainsi l’analyse et la prévision des pannes. Source : Cloud Computing Journal
4. Formation du Personnel
Former les équipes de maintenance à l’utilisation des nouvelles technologies et à l’interprétation des données pour maximiser les avantages de la maintenance prédictive.
- Exemple concret : Des sessions de formation sur les outils d’analyse des données et les techniques de maintenance prédictive peuvent être organisées pour garantir que le personnel est bien préparé. Source : Training Industry
Conclusion
En résumé, la maintenance prédictive représente une avancée majeure dans la gestion des équipements industriels. En utilisant des technologies avancées pour surveiller et analyser les données en temps réel, elle permet non seulement de réduire les coûts, mais aussi d’optimiser la production et d’améliorer la sécurité. Alors que les technologies continuent d’évoluer, la maintenance prédictive est appelée à jouer un rôle de plus en plus central dans l’industrie, offrant de nouvelles opportunités pour une gestion proactive et efficace des équipements. À l’avenir, l’intégration de l’IA et des technologies IoT devrait affiner encore davantage les capacités prédictives, offrant ainsi des perspectives prometteuses pour une gestion encore plus optimisée des équipements.
Sources
- Scribbr : Maintenance Corrective
- Plant Services : Maintenance Préventive
- Forbes : Maintenance Prédictive
- IoT For All : Collecte de Données
- TechTarget : Analyse des Données
- Harvard Business Review : Prédiction et Action
- Analytics Insight : Technologies Utilisées
- McKinsey & Company : Réduction des Temps d’Arrêt
- Deloitte : Augmentation de la Disponibilité des Équipements
- Frost & Sullivan : Réduction des Coûts de Maintenance
- Industrial Maintenance & Plant Operation : Prolongation de la Durée de Vie des Équipements
- Journal of Safety Research : Détection Précoce des Anomalies
- Safety Science : Réduction des Risques d’Accidents
- Gartner : Données Fiables pour une Meilleure Planification
- Food Processing : Identification des Équipements Critiques
- IEEE Spectrum : Choix des Technologies Adaptées
- Cloud Computing Journal : Collecte et Analyse des Données
- Training Industry : Formation du Personnel