Imaginez un monde où vos machines vous informent quand elles ont besoin d’attention, avant même qu’une panne ne survienne. Ce n’est pas de la science-fiction, c’est exactement ce que l’IoT et maintenance industrielle rendent possible aujourd’hui. Grâce à cette technologie, les entreprises, grandes et petites, bénéficient d’une gestion proactive des équipements, transformant leur manière d’aborder la maintenance.
Table of Contents
L’IoT, le nouveau meilleur ami de la maintenance
L’IoT en maintenance, c’est comme avoir un stéthoscope géant sur toute votre usine. Des capteurs surveillent en permanence vos machines, collectant des données sur tout, de la température aux vibrations.
Prenons l’exemple de Michelin. Dans leur usine de Homburg en Allemagne, ils ont mis en place un système IoT pour surveiller leurs machines de production de pneus. Le résultat ? Ils ont réduit les arrêts imprévus de 10% et augmenté la durée de vie de leurs équipements de 8%. C’est du concret : moins de temps perdu et des machines qui durent plus longtemps.
Comment l’IoT booste la productivité industrielle ?
L’ des Objets (IoT) transforme le secteur industriel en améliorant la gestion et l’optimisation des processus de production grâce aux données connectées. Voici comment :
- Moins d’arrêts surprises : Les machines alertent avant de tomber en panne, réduisant les interruptions imprévues.
- Maintenance au bon moment : Grâce à la maintenance prédictive, les interventions sont effectuées au moment optimal, ni trop tôt ni trop tard.
- Qualité constante : Des machines bien entreten assurent une production stable et de qualité.
- Économies d’énergie : La consommation énergétique est surveillée en temps réel, permettant d’identifier et de corriger les équipements gourmands
- Gestion des stocks simplifiée : Les stocks sont suivis en temps réel, et les commandes de pièces sont déclenchées automatiquement lorsque nécessaire.
- Décisions éclairées : L’accès à des données détaillées améliore la prise de décision et l’optimisation de la production.
En résumé, l’IoT permet une surveillance constante et une gestion optimisée des ressources, conduisant à une productivité accrue et des coûts réduits dans l’industrie.
Chez Harley-Davidson, dans leur usine de York en Pennsylvanie, l’IoT a fait des merveilles. Avant, il leur fallait 21 jours pour fabriquer une moto. Maintenant ? Seulement 6 heures. C’est comme passer d’un escargot à une fusée !
Les ingrédients secrets de l’IoT et maintenance industrielle
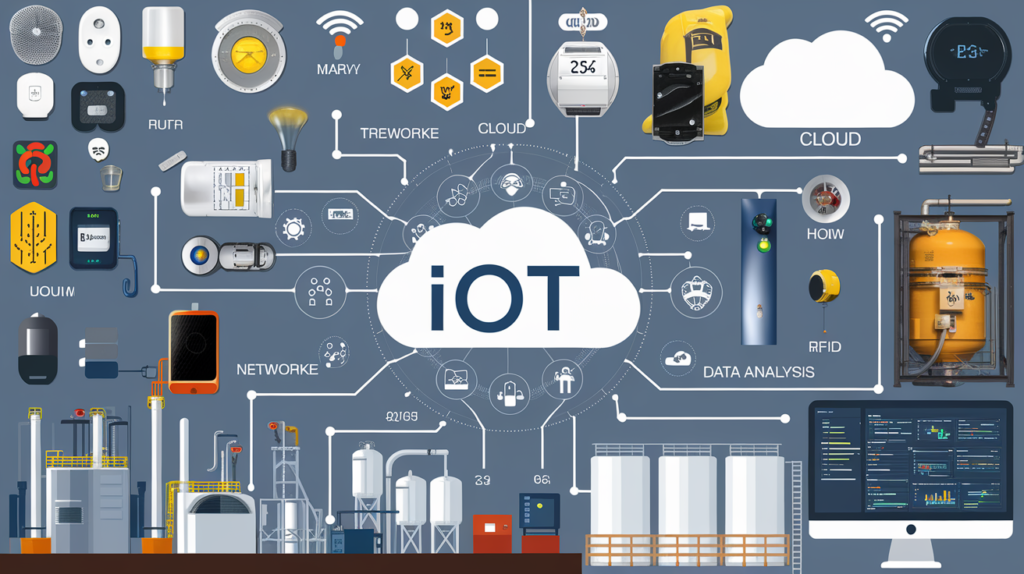
Les technologies qui font la différence
- Capteurs IoT : Les yeux et les oreilles de votre usine, collectant des données en temps réel sur tous les aspects de la production.
- Réseaux de communication : Permettent aux machines de communiquer entre elles et avec les systèmes centraux, assurant un flux d’informations continu.
- Plateformes cloud : Le cerveau du système, stockant et traitant les vastes quantités de données générées par les capteurs.
- Analyse big data : Extraire des insights précieux à partir des masses de données collectées, révélant des tendances et des opportunités d’optimisation.
- Intelligence artificielle : Utilise les données pour prédire les pannes, optimiser les processus et automatiser la prise de décision.
- Jumeaux numériques : Répliques virtuelles des machines et processus, permettant des simulations et des tests sans risque pour l’équipement réel.
- Réalité augmentée : Superpose des informations numériques au monde réel, aidant les techniciens lors des interventions et de la maintenance.
Ces technologies, travaillant de concert, transforment les usines traditionnelles en usines intelligentes, augmentant significativement l’efficacité et la productivité.
Caterpillar, le géant des engins de chantier, utilise tout ça. Ils ont équipé leurs machines de capteurs qui envoient des données en temps réel. Ces données sont analysées pour prédire quand une machine risque de tomber en panne. Résultat ? Leurs clients économisent des millions en évitant les pannes inattendues.
Les capteurs, ces petits curieux
Voici les types de capteurs qu’on trouve souvent dans l’industrie :
- Capteurs de vibration : Pour sentir quand une machine tremble un peu trop.
- Capteurs de température : Pour repérer les surchauffes avant qu’il ne soit trop tard.
- Capteurs de pression : Pour les systèmes hydrauliques et pneumatiques.
- Capteurs acoustiques : Pour entendre les couinements suspects.
- Capteurs de courant électrique : Pour voir si une machine est trop gourmande.
- Capteurs de débit : Pour les liquides et les gaz.
- Capteurs d’humidité : Parce que parfois, c’est l’humidité qui pose problème.
- Accéléromètres : Pour mesurer les mouvements anormaux.
Chez SKF, fabricant de roulements, ils utilisent des capteurs de vibration pour surveiller les machines tournantes. Ils peuvent ainsi détecter des problèmes mineurs avant qu’ils ne deviennent majeurs. C’est comme avoir un mécanicien qui écoute en permanence le moteur de votre voiture.
Les défis de l’IoT en industrie : pas si simple !
Mettre en place l’IoT, c’est un peu comme rénover une maison tout en y vivant. C’est faisable, mais ça demande de la planification et de la patience.
Les obstacles à surmonter
- Complexité technique : Faire cohabiter le neuf et l’ancien, pas toujours facile.
- Sécurité des données : Avec toutes ces infos qui circulent, il faut être vigilant.
- Formation du personnel : Nouvelles technologies = nouveaux savoir-faire.
- Coûts initiaux : Ça peut coûter cher au début, mais ça rapporte sur le long terme.
- Changement des habitudes : Pas toujours facile de changer sa façon de travailler.
Airbus a rencontré un problème intéressant dans son usine de Hambourg. Quand ils ont voulu installer des capteurs IoT, ils se sont heurtés à un souci : les structures métalliques des avions bloquaient les signaux wifi. Leur solution ? Ils ont créé un réseau de capteurs en cascade, où chaque capteur relaie l’information au suivant. Malin, non ?
Intégrer l’IoT dans l’existant : un vrai casse-tête parfois
- Compatibilité : Faire parler du matériel ancien avec des technologies en maintenances récentes.
- Interruptions de production : Installer tout ça sans trop perturber le travail.
- Problèmes de réseau : Parfois, le wifi ne passe pas partout dans une usine.
- Gestion des données : Que faire de toutes ces infos ?
- Manque de standards : Chacun fait un peu à sa sauce dans l’IoT.
- Trouver les bonnes compétences : Il faut des gens qui comprennent à la fois les machines et l’informatique.
General Electric a relevé ces défis dans ses propres usines. Ils ont créé un système appelé “Brilliant Factory” qui intègre l’IoT à leurs lignes de production existantes. Résultat ? Une augmentation de 25% de leur productivité. Pas mal pour une vieille entreprise de 125 ans !
L’intelligence artificielle et l’IoT : le duo gagnant
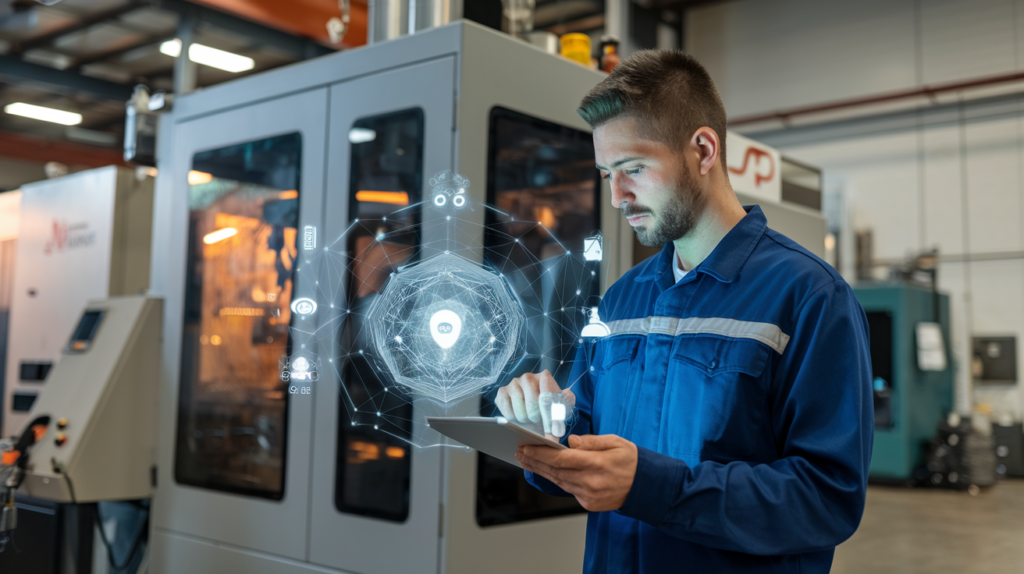
L’IA dans l’IoT, c’est comme avoir un super-cerveau qui analyse toutes les données des capteurs. Et ça donne des résultats impressionnants.
Comment l’IA rend les capteurs plus intelligents
- Analyse en temps réel : L’IA traite les données directement sur le capteur.
- Apprentissage continu : Les capteurs deviennent de plus en plus précis avec le temps.
- Détection d’anomalies : L’IA repère les comportements bizarres des machines.
- Prédictions : Elle peut dire quand une panne risque de se produire.
- Fusion de données : Elle combine les infos de plusieurs capteurs pour une vue d’ensemble.
- Auto-diagnostic : Les capteurs peuvent détecter leurs propres problèmes.
- Économie d’énergie : L’IA optimise le fonctionnement des capteurs.
Chez Siemens, ils ont créé des turbines à gaz “intelligentes”. Ces turbines apprennent en permanence à partir des données qu’elles génèrent. Résultat ? Elles produisent plus d’électricité tout en consommant moins de carburant. C’est bon pour le portefeuille et pour la planète !
Le nerf de la guerre : le retour sur investissement
Parler de retour sur investissement, c’est bien beau, mais voyons des chiffres concrets.
Comment mesurer si ça vaut le coup
- Moins de temps d’arrêt : Combien d’heures de production gagnées ?
- Économies sur les pièces : Moins de stock, moins d’argent immobilisé.
- Machines qui durent plus longtemps : Moins besoin de racheter du matériel.
- Productivité en hausse : Plus de production avec les mêmes ressources.
- Moins de main-d’œuvre pour la maintenance : Les techniciens interviennent moins souvent.
- Meilleure qualité : Moins de produits défectueux, moins de gaspillage.
L’usine de Petrobras à Henrique Lage, au Brésil, a mis en place un système IoT pour surveiller ses équipements. En un an, ils ont économisé 1,5 million de dollars rien qu’en évitant les pannes imprévues. C’est comme si chaque dollar investi dans l’IoT en rapportait plusieurs en retour !
Les avantages économiques, c’est du concret !
- Moins de dépenses en maintenance : On répare moins souvent et plus efficacement.
- Production plus stable : Moins d’interruptions imprévues.
- Gestion des stocks optimisée : On commande les bonnes pièces au bon moment.
- Équipements qui durent plus longtemps : On repousse les gros investissements.
- Facture d’énergie réduite : On repère vite les gaspillages.
- Qualité améliorée : Moins de rebuts, clients plus satisfaits.
- Assurances moins chères : Moins de risques = primes réduites.
Ces bénéfices concrets montrent comment l’IoT améliore la rentabilité et l’efficacité des opérations industrielles.
Chez Ford, l’utilisation de l’IoT dans leur usine de moteurs de Valence en Espagne a permis de réduire les temps d’arrêt de 15%. Quand on sait que chaque minute d’arrêt peut coûter des milliers d’euros, on comprend vite l’intérêt !
Conclusion : l’IoT, c’est maintenant ou jamais
L’IoT dans la maintenance industrielle, ce n’est pas du futur lointain. C’est aujourd’hui, et ça change la donne pour de nombreuses entreprises. Que vous ayez un petit atelier ou une grande usine, il y a sûrement une façon d’utiliser l’IoT pour améliorer vos opérations.
Bien sûr, ce n’est pas toujours facile à mettre en place. Il y a des défis à relever, des investissements à faire. Mais quand on voit les résultats chez des géants comme Michelin, Harley-Davidson ou Petrobras, on se dit que ça vaut le coup d’y réfléchir sérieusement.
Alors, prêt à faire entrer vos machines dans l’ère numérique ? L’IoT, c’est un peu comme avoir une boule de cristal pour votre usine. Ça ne prédit pas l’avenir, mais ça vous donne un sacré coup d’avance. Et dans l’industrie d’aujourd’hui, avoir un coup d’avance, ça peut faire toute la différence.