La Total Productive Maintenance (TPM) est une composante essentielle du lean manufacturing, visant à optimiser l’efficacité opérationnelle tout en assurant une gestion proactive des équipements. Ce système stratégique permet de réduire les pertes, améliorer la fiabilité des machines et maximiser la production. Cet article explore en détail la méthodologie de la TPM et son rôle clé dans le lean manufacturing, en mettant en lumière ses principes fondamentaux, ses avantages concrets et son impact significatif sur la productivité et la qualité des processus de fabrication.
Table of Contents
Total Productive Maintenance (TPM) : Définition et Objectifs
La Total Productive Maintenance (TPM) est une approche structurée qui vise à maximiser l’efficacité des équipements tout en intégrant les principes du lean manufacturing, tels que l’élimination des gaspillages. Développée pour garantir une production fluide et sans interruption, la TPM repose sur la collaboration active de tous les employés, des opérateurs de machines aux responsables de maintenance.
Objectifs de la TPM dans le Lean Manufacturing : Détails et Explications
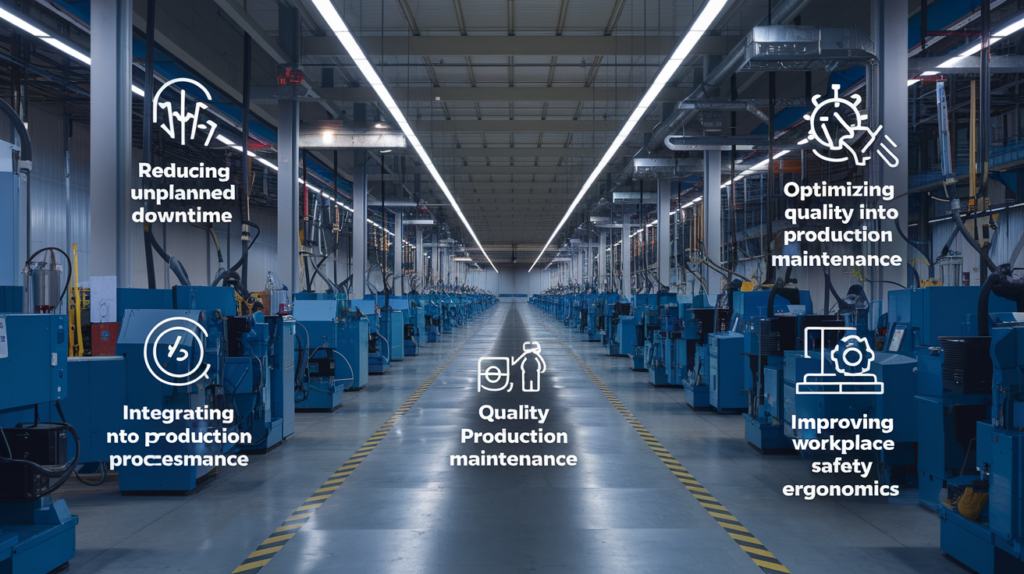
La Total Productive Maintenance (TPM) joue un rôle crucial dans la philosophie du lean manufacturing. Son intégration vise à atteindre une efficacité maximale des processus de production tout en réduisant les pertes et en garantissant un environnement de travail sûr et de qualité. Voici une exploration approfondie des principaux objectifs de la TPM dans le cadre du lean manufacturing.
1. Réduire les pannes pour limiter les arrêts imprévus
Les pannes non planifiées constituent une source majeure de gaspillage dans la production. Chaque arrêt de machine engendre non seulement une perte de temps, mais aussi des coûts additionnels liés à la réparation, au réapprovisionnement en matériaux endommagés ou à la gestion des retards de livraison.
- Approche proactive de la TPM :
La TPM met l’accent sur des inspections régulières et des actions préventives, comme le remplacement anticipé de pièces usées, afin d’éviter les défaillances critiques. - Avantages directs :
Une réduction drastique des pannes améliore la fluidité des opérations et la productivité globale. Par exemple, dans une usine automobile, la maintenance préventive a permis de réduire les arrêts imprévus de 50 %, augmentant ainsi la capacité de production. - Outils utilisés :
- Maintenance conditionnelle (basée sur des données en temps réel, comme les vibrations ou la température des équipements).
- Maintenance autonome (petites vérifications effectuées directement par les opérateurs).
2. Optimiser les performances des équipements grâce à une maintenance proactive
Dans le lean manufacturing, chaque machine doit fonctionner à son plein potentiel pour éviter les gaspillages liés aux performances réduites. La TPM cherche à exploiter la capacité maximale de chaque équipement sans pour autant accélérer son usure.
- Optimisation des performances :
La TPM utilise des outils tels que l’OEE (Overall Equipment Effectiveness) pour surveiller trois aspects essentiels :- Disponibilité : Minimiser les temps d’arrêt.
- Performance : Garantir que les machines fonctionnent à leur vitesse optimale.
- Qualité : Produire sans défaut.
- Exemple concret :
Une ligne d’embouteillage qui perdait 10 % de sa capacité en raison de micro-arrêts a vu ses performances augmenter de 15 % après l’introduction de routines de maintenance autonome et conditionnelle. - Résultat attendu :
Une machine bien entretenue consomme moins d’énergie, produit moins de déchets et offre un meilleur rendement.
3. Intégrer la qualité dans les processus de production en éliminant les défauts à la source
Le lean manufacturing repose sur le principe de la qualité dès la première fois (Right First Time). La TPM soutient cet objectif en s’assurant que les équipements produisent sans erreurs.
- Identification des causes racines :
La TPM encourage l’analyse systématique des causes des défauts, souvent dus à des machines mal calibrées, à l’usure des composants ou à des conditions de fonctionnement inappropriées. - Contrôles qualité intégrés :
- Intégration de capteurs pour détecter les anomalies (par exemple, variations de température ou de pression).
- Audits réguliers pour évaluer la performance des équipements.
- Impact sur les coûts :
En éliminant les défauts à la source, les entreprises évitent les retouches coûteuses, les retours clients ou la perte de réputation liée à des produits défectueux.
4. Améliorer la sécurité et l’ergonomie sur les postes de travail
Dans un environnement lean, la sécurité n’est pas un simple complément mais un impératif pour garantir une production durable et fiable.
- Réduction des risques d’accidents :
Les inspections régulières et les actions de maintenance préviennent les défaillances soudaines pouvant causer des blessures. Par exemple :- Les freins défectueux sur une presse industrielle peuvent être détectés et corrigés avant qu’ils ne provoquent un accident grave.
- Amélioration des conditions de travail :
Les efforts de la TPM se concentrent également sur l’ergonomie. Cela inclut :- Réduire les mouvements inutiles des opérateurs en optimisant la disposition des machines.
- Utiliser des équipements bien entretenus pour réduire les vibrations ou le bruit excessif, souvent sources de fatigue ou de maladies professionnelles.
- Avantages organisationnels :
- Diminution des absences liées aux accidents ou à la santé.
- Meilleure satisfaction des employés, favorisant leur implication dans le processus.
- Exemple pratique :
Une usine textile a réaménagé ses stations de travail pour réduire les mouvements répétitifs des opérateurs, entraînant une réduction de 30 % des troubles musculo-squelettiques.
Les Piliers de la Total Productive Maintenance : Une Base Solide pour le Lean Manufacturing
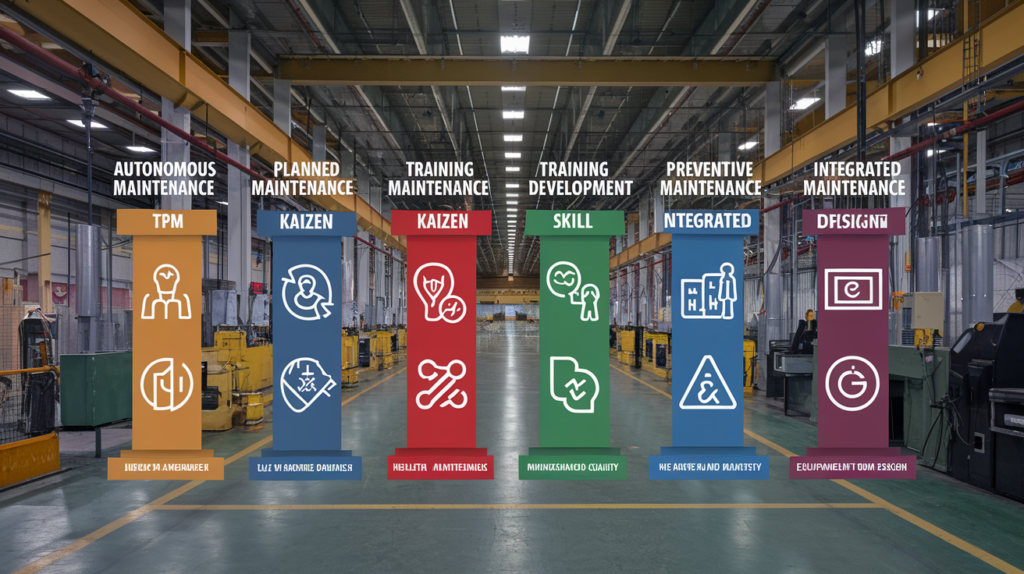
La total productive maintenance lean manufacturing repose sur huit piliers fondamentaux qui s’alignent parfaitement avec les principes du lean manufacturing. Ces piliers forment une méthodologie complète pour éliminer les pertes, maximiser la disponibilité des équipements et assurer une gestion proactive des ressources.
1. Maintenance autonome : L’implication des opérateurs
La maintenance autonome place les opérateurs au centre des activités de maintenance. Leur rôle dépasse la simple exploitation des machines et inclut des tâches essentielles comme :
- Le nettoyage régulier des équipements pour prévenir l’accumulation de poussière et de débris.
- Les inspections visuelles afin de détecter des anomalies (bruits inhabituels, vibrations, fuites).
Bénéfices clés :
- Réduction des pannes mineures grâce à une détection précoce des problèmes.
- Renforcement de la responsabilité des opérateurs, qui deviennent des acteurs actifs de la maintenance.
Exemple concret :
Dans une usine de production alimentaire, les opérateurs effectuant des inspections quotidiennes ont réduit les pannes de 25 % en détectant des problèmes avant qu’ils ne s’aggravent.
Source : How to Implement Autonomous Maintenance
2. Maintenance planifiée : Une organisation proactive
La maintenance planifiée vise à anticiper les besoins en maintenance et à allouer les ressources de manière efficace. Cela inclut :
- Des calendriers d’entretien établis en fonction des cycles d’utilisation des équipements.
- Une priorisation des interventions en fonction de leur impact potentiel sur la production.
Avantages :
- Réduction des interruptions imprévues.
- Optimisation des coûts en évitant des réparations urgentes souvent plus coûteuses.
Exemple d’application :
Une entreprise métallurgique a intégré des outils de planification automatisés pour coordonner les maintenances, réduisant les temps d’arrêt imprévus de 30 %.
Source : Planned Maintenance in TPM
3. Améliorations continues (Kaizen) : La quête de l’excellence
Le Kaizen, qui signifie “amélioration continue” en japonais, est un pilier central dans le lean manufacturing et la TPM. Il s’agit de :
- Identifier les zones d’inefficacité (temps d’arrêt, pertes de ressources).
- Impliquer les équipes dans la recherche de solutions pragmatiques et durables.
Impact :
- Optimisation continue des performances des machines et des processus.
- Adoption d’une culture d’innovation au sein des équipes.
Cas pratique :
Dans une usine électronique, le Kaizen a permis de réduire le temps de changement d’outils de 20 % grâce à une réorganisation des postes de travail.
Source : Kaizen and Continuous Improvement
4. Formation et développement des compétences : Investir dans le capital humain
La TPM met un accent particulier sur la formation des opérateurs et des techniciens. Cela inclut :
- Des sessions de formation pour comprendre le fonctionnement des machines.
- Des ateliers pratiques pour apprendre à identifier et résoudre les problèmes courants.
Pourquoi c’est important :
- Un personnel compétent réduit les erreurs humaines et améliore la maintenance autonome.
- La montée en compétences favorise l’engagement des équipes.
Exemple :
Une entreprise de textile a formé ses opérateurs à utiliser un système de surveillance en temps réel, ce qui a amélioré la détection des anomalies et réduit les temps de réponse.
Source : Case Study: Employee Training Impact on TPM
5. Maintenance préventive : Prévenir plutôt que guérir
La maintenance préventive se concentre sur des interventions régulières pour éviter les pannes. Cela comprend :
- Les inspections périodiques (vérifications mécaniques, électriques, etc.).
- Le remplacement programmé des pièces avant qu’elles ne s’usent complètement.
Résultats attendus :
- Augmentation de la durée de vie des équipements.
- Réduction des arrêts coûteux dus à des défaillances majeures.
Exemple d’efficacité :
Dans une usine chimique, la maintenance préventive a permis d’augmenter la disponibilité des équipements critiques de 85 % à 95 %.
Source : Preventive Maintenance Best Practices
6. Qualité intégrée : Produire sans défaut
Ce pilier vise à intégrer des contrôles qualité directement dans les processus de production. Cela comprend :
- L’utilisation de capteurs pour surveiller les paramètres critiques (pression, température, etc.).
- La mise en place d’audits réguliers pour garantir la conformité des produits.
Avantages :
- Réduction des défauts et des retouches.
- Amélioration de la satisfaction client grâce à des produits de haute qualité.
Cas d’application :
Dans une ligne de production de composants automobiles, l’ajout de capteurs de contrôle a permis de réduire les taux de rejet de 10 %.
Source : Integrated Quality Management in Manufacturing
7. Santé et sécurité : Garantir un environnement sûr
La TPM met un accent particulier sur la sécurité et l’ergonomie. Cela passe par :
- L’élimination des risques liés à des équipements défectueux.
- La création de postes de travail adaptés pour réduire les troubles musculo-squelettiques.
Impact direct :
- Diminution des accidents du travail.
- Amélioration du bien-être et de la productivité des opérateurs.
Exemple concret :
Une entreprise pharmaceutique a réduit les accidents de 40 % en intégrant des formations régulières sur la sécurité et en modernisant ses équipements.
Source : Safety in Pharmaceutical Manufacturing
8. Gestion des équipements dès leur conception : Prévoir la maintenabilité
La TPM commence dès la conception des machines. Cela inclut :
- Intégrer des critères de maintenabilité et de fiabilité dès la phase de conception.
- Collaborer avec les fabricants pour garantir un accès facile aux pièces et composants critiques.
Avantages :
- Réduction des coûts de maintenance sur le long terme.
- Meilleure adaptation des équipements aux besoins spécifiques de l’entreprise.
Exemple :
Une usine d’emballage a collaboré avec un fournisseur pour concevoir une ligne de production plus facile à entretenir, ce qui a réduit de 20 % les coûts de maintenance annuels.
Source : Designing Maintainable Machinery
Les Avantages Concrets de la TPM en Lean Manufacturing
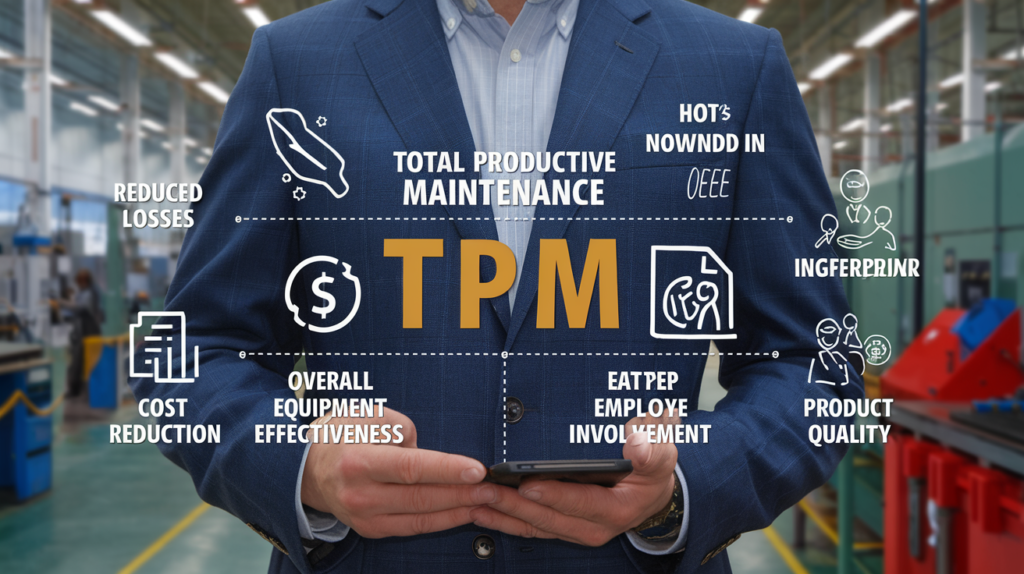
La Total Productive Maintenance (TPM), lorsqu’elle est intégrée aux principes du lean manufacturing, génère des bénéfices mesurables qui impactent positivement l’ensemble de la chaîne de production. Voici une analyse approfondie des principaux avantages qu’elle offre :
1. Réduction des pertes : Une chasse systématique
La TPM se concentre sur l’identification et la réduction des six grandes pertes liées à la production :
- Pannes : Interruptions causées par des défaillances d’équipement.
- Temps de réglage et de changement : Délais nécessaires pour ajuster les machines.
- Arrêts mineurs et ralentissements : Perturbations courtes mais fréquentes.
- Défauts de production : Rejets ou retouches nécessaires sur des produits non conformes.
Exemple pratique :
Une entreprise de fabrication de boissons a identifié que 20 % de ses pertes provenaient de temps de changement d’outils. En mettant en œuvre des pratiques TPM, ces pertes ont été réduites à 10 %.
Source : Reducing Losses with TPM
2. Amélioration de l’OEE : Maximiser l’efficacité des équipements
L’OEE (Overall Equipment Effectiveness) est un indicateur clé qui mesure :
- La disponibilité : Temps où l’équipement est opérationnel.
- La performance : Rapidité et efficacité des machines.
- La qualité : Proportion de produits conformes sans retouches.
En combinant TPM et lean manufacturing, les entreprises atteignent des niveaux d’OEE significativement plus élevés.
Illustration :
Dans une usine automobile, l’OEE est passé de 65 % à 85 % après la mise en œuvre d’une maintenance autonome et préventive.
Source : Improving OEE with TPM
3. Réduction des coûts : Une maintenance moins coûteuse
En adoptant une approche proactive, la TPM diminue la fréquence et l’intensité des interventions correctives, qui sont souvent :
- Imprévisibles.
- Coûteuses en temps et en main-d’œuvre.
Les économies réalisées se traduisent par :
- Une réduction des coûts de réparation.
- Une diminution des stocks de pièces de rechange inutilisées.
Cas concret :
Une entreprise de fabrication d’équipements électroniques a réduit ses coûts de maintenance de 25 % grâce à un calendrier de maintenance planifiée.
Source : Cost Reduction with Proactive Maintenance
4. Implication des employés : Un moteur de motivation
La TPM favorise l’engagement des employés en :
- Encourageant leur participation active dans la maintenance quotidienne.
- Valorisant leur expertise technique à travers des formations continues.
Cette approche améliore la satisfaction des employés, qui deviennent des acteurs clés dans l’amélioration des processus.
Exemple pratique :
Dans une usine textile, la formation des opérateurs à la maintenance autonome a augmenté leur sentiment d’appartenance et réduit le taux de turnover de 15 %.
Source : Employee Engagement in TPM
5. Meilleure qualité des produits : Une réduction des défauts
En intégrant des inspections régulières et des contrôles qualité dans le processus de production, la TPM diminue considérablement :
- Les défauts de fabrication.
- Les retouches coûteuses et chronophages.
Bénéfices directs :
- Des produits conformes dès la première production.
- Une amélioration de la satisfaction des clients.
Exemple :
Une entreprise pharmaceutique a réduit ses défauts de production de 30 % en mettant en place un contrôle qualité intégré dans sa TPM.
Source : TPM for Quality Improvement
Étapes pour Implémenter la TPM dans une Démarche Lean
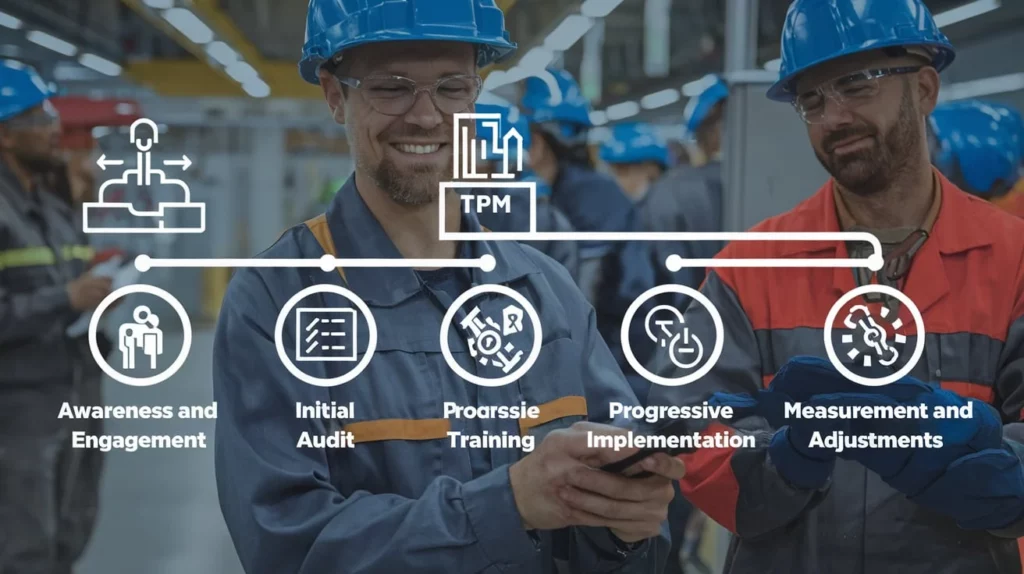
La mise en œuvre de la Total Productive Maintenance (TPM) dans un contexte de lean manufacturing nécessite une stratégie planifiée et méthodique. Voici les étapes essentielles pour intégrer efficacement la TPM tout en alignant les objectifs sur les principes du lean.
1. Sensibilisation et Engagement : Poser les Fondations
La première étape consiste à mobiliser les équipes en communiquant clairement :
- Les objectifs stratégiques de la TPM.
- Les bénéfices attendus pour l’entreprise et pour les employés (réduction des efforts inutiles, meilleure ergonomie, etc.).
Il est crucial d’obtenir l’adhésion des décideurs (direction) et des opérateurs, car leur implication directe est la clé du succès.
Exemple : Une entreprise automobile a organisé des ateliers de sensibilisation pour ses équipes, en expliquant comment la TPM allait simplifier leur travail tout en augmentant l’efficacité.
2. Audit Initial : Identifier les Points de Faiblesse
L’étape suivante consiste à réaliser un diagnostic approfondi des équipements et des processus pour repérer :
- Les principales sources de pertes (pannes, temps d’arrêt, défauts).
- Les écarts entre les performances actuelles et les objectifs.
Cet audit repose sur l’analyse de données historiques (temps d’arrêt, taux de défauts) et des observations terrain.
Exemple pratique : Une usine agroalimentaire a découvert que 30 % de ses arrêts provenaient de mauvais réglages lors des changements de produit.
3. Formation : Renforcer les Compétences des Équipes
Une fois les problématiques identifiées, il est nécessaire de former les équipes sur :
- Les compétences techniques (maintenance autonome, diagnostic des pannes).
- Les concepts du lean manufacturing (Kaizen, élimination des gaspillages).
Ces formations doivent être adaptées aux rôles spécifiques des opérateurs et des techniciens.
Bénéfices : Les employés deviennent des acteurs proactifs, capables de détecter et de résoudre rapidement les problèmes.
4. Mise en Œuvre Progressive : Une Approche par Priorités
L’intégration des pratiques de TPM doit être progressive, en ciblant d’abord les processus les plus critiques.
- Déployez les piliers (maintenance autonome, maintenance planifiée, etc.) étape par étape.
- Implémentez des changements mesurables avant de les généraliser à d’autres zones de l’usine.
Exemple : Une entreprise textile a démarré par la maintenance autonome sur ses machines les plus sollicitées, avant de l’étendre à l’ensemble des équipements.
5. Mesure et Ajustements : Évaluer pour Améliorer
Une fois la TPM mise en œuvre, il est crucial de suivre les performances à l’aide d’indicateurs clés, notamment :
- OEE (Overall Equipment Effectiveness) : Pour mesurer l’amélioration de la disponibilité, de la performance et de la qualité.
- Taux de pannes : Pour identifier les progrès réalisés et les zones nécessitant des ajustements.
Utilisez ces données pour affiner les stratégies et maintenir l’engagement des équipes.
Illustration concrète : Une usine de plasturgie a constaté une augmentation de 20 % de son OEE après six mois de mise en œuvre, grâce à des ajustements réguliers basés sur les indicateurs. (Source : Lean.org, étude de cas sur l’OEE)
Exemple supplémentaire : Une entreprise automobile a observé une réduction de 30 % de ses arrêts non planifiés en appliquant les principes de maintenance planifiée et autonome, avec un suivi précis des indicateurs de performance. (Source : TPM.com, étude de cas sur la TPM en industrie automobile)
Total Productive Maintenance et Lean Manufacturing : Cas Pratique
Dans une entreprise de fabrication électronique, la mise en place conjointe de la TPM et du lean manufacturing a permis de :
- Réduire les temps d’arrêt de 40 %,
- Améliorer l’OEE de 20 %,
- Diminuer les coûts de maintenance de 30 %.
Ces résultats ont été obtenus grâce à une maintenance autonome bien appliquée et à un programme de formation efficace. Vous pouvez consulter un exemple similaire détaillé sur Lean Production.
Conclusion : Pourquoi Adopter la TPM dans le Lean Manufacturing ?
La Total Productive Maintenance (TPM) est un levier indispensable pour atteindre l’excellence opérationnelle dans le lean manufacturing. En réduisant les gaspillages, en impliquant les équipes et en optimisant les équipements, la TPM aide les entreprises à rester compétitives sur des marchés exigeants.