La Total Productive Maintenance (TPM) est une approche stratégique visant à maximiser la productivité des équipements tout en impliquant l’ensemble des employés dans l’amélioration continue. Contrairement aux méthodes traditionnelles, la TPM ne se limite pas aux équipes de maintenance ; elle inclut tous les opérateurs, favorisant ainsi une culture de responsabilisation et de collaboration pour atteindre une efficacité maximale. Cet article détaillé vous guidera à travers les principes de la TPM, ses piliers essentiels, ses avantages, ainsi que des exemples concrets d’application en industrie.
Table of Contents
Qu’est-ce que la Maintenance Productive Totale (TPM) ?
La TPM est une méthode de gestion de la maintenance qui vise à éliminer les pannes, les arrêts non planifiés, et les défauts de qualité, tout en augmentant l’efficacité des machines. Cette approche proactive repose sur l’idée que chaque employé, du technicien à l’opérateur, doit contribuer activement à la maintenance et à l’amélioration des équipements.
Origine de la TPM
La TPM a été développée dans les années 1960 par Nippondenso, un fournisseur clé de Toyota, dans le cadre du Toyota Production System (TPS). L’objectif initial était de minimiser les temps d’arrêt et de maximiser la fiabilité des machines pour soutenir une production juste-à-temps (JAT). Aujourd’hui, la TPM est adoptée par de nombreuses industries à travers le monde, allant de la fabrication automobile à l’industrie pharmaceutique.
Les 8 Piliers de la TPM : Fondements de l’Amélioration Continue

La Maintenance Productive Totale (TPM) repose sur huit piliers fondamentaux qui permettent d’atteindre une performance optimale en associant tous les employés à l’amélioration continue. Ces piliers sont les bases sur lesquelles repose une gestion proactive de la maintenance industrielle. Dans cet article, nous approfondissons chaque pilier pour comprendre son rôle, ses avantages, et les pratiques concrètes qui en garantissent le succès.
1. Maintenance Autonome : Implication des Opérateurs dans la Maintenance Quotidienne
La maintenance autonome consiste à responsabiliser les opérateurs pour qu’ils effectuent des tâches simples de maintenance telles que le nettoyage, la lubrification, et les inspections visuelles. Cela vise à améliorer la connaissance des machines par ceux qui les utilisent quotidiennement.
Objectifs
- Réduire les pannes mineures en détectant rapidement les anomalies.
- Renforcer la collaboration entre les opérateurs et les techniciens de maintenance.
- Alléger la charge des équipes de maintenance pour qu’elles puissent se concentrer sur des interventions complexes.
Exemples Pratiques
- Mise en place de checklists quotidiennes pour les inspections des machines.
- Formation des opérateurs à reconnaître les signes d’usure, comme des vibrations anormales ou des fuites d’huile.
- Utilisation de codes couleurs sur les équipements pour indiquer les zones à surveiller ou à entretenir.
2. Maintenance Planifiée : Prédire et Prévenir les Pannes
La maintenance planifiée implique l’organisation d’interventions régulières basées sur l’analyse des données historiques des équipements. L’objectif est d’éviter les arrêts imprévus et de prolonger la durée de vie des machines.
Avantages
- Minimisation des arrêts de production grâce à une anticipation des besoins en maintenance.
- Réduction des coûts liés aux réparations d’urgence.
- Meilleure gestion des stocks de pièces de rechange.
Outils Utilisés
- Logiciels de GMAO (Gestion de Maintenance Assistée par Ordinateur) pour suivre les interventions.
- Analyse des tendances des indicateurs tels que le MTBF (Mean Time Between Failures) et le MTTR (Mean Time To Repair).
Exemple
Une entreprise peut programmer un remplacement des courroies de transmission tous les 6 mois, en s’appuyant sur les recommandations du fabricant et les données de performance enregistrées.
3. Amélioration Focalisée (Kaizen) : Résolution des Problèmes à la Racine
L’amélioration focalisée repose sur le concept japonais du Kaizen, qui signifie « changement pour le mieux ». Il s’agit d’identifier les causes profondes des pertes et de mettre en place des solutions durables.
Étapes Clés
- Identifier les problèmes critiques affectant la performance des équipements.
- Utiliser des outils tels que le diagramme d’Ishikawa ou l’analyse des 5 Pourquoi pour en déterminer les causes profondes.
- Impliquer des équipes multidisciplinaires pour développer et tester des solutions.
Résultats Attendus
- Réduction des pertes énergétiques ou matérielles.
- Optimisation des cycles de production.
- Augmentation de la satisfaction des opérateurs grâce à un environnement de travail amélioré.
4. Contrôle Initial : Anticiper les Problèmes Dès l’Installation
Le contrôle initial intervient lors de l’achat ou de l’installation de nouveaux équipements. Il permet d’identifier les sources potentielles de défaillance avant leur mise en service.
Principes
- Configurer correctement les paramètres des machines selon les spécifications techniques.
- Former les équipes à l’utilisation et à l’entretien des nouveaux équipements.
- Mettre en place un suivi rigoureux pour détecter les anomalies précoces.
Exemple
Lors de l’installation d’une nouvelle ligne de production, une entreprise effectue un banc d’essai pour vérifier la précision des réglages, suivi d’une inspection régulière au cours des premières semaines.
5. Formation et Développement des Compétences : Un Personnel Polyvalent
La formation continue des employés est essentielle pour qu’ils puissent effectuer leurs tâches avec efficacité et sécurité. Ce pilier vise à développer des compétences polyvalentes et à instaurer une culture de la maintenance proactive.
Objectifs
- Créer une main-d’œuvre autonome capable d’effectuer des diagnostics rapides.
- Réduire les erreurs humaines grâce à une meilleure compréhension des équipements.
- Favoriser un environnement d’apprentissage continu.
Exemples de Formation
- Sessions sur les techniques de diagnostic et d’analyse des pannes.
- Programmes de certification en maintenance prédictive.
- Ateliers sur l’utilisation des outils modernes tels que les capteurs IoT.
6. Sécurité, Santé et Environnement (SHE) : Priorité au Bien-être et à la Durabilité
La TPM intègre des pratiques visant à garantir la sécurité des employés tout en minimisant les impacts environnementaux. Cela inclut une analyse proactive des risques et la mise en œuvre de mesures de prévention.
Actions Clés
- Installation de systèmes de sécurité comme des interrupteurs d’arrêt d’urgence.
- Formation des employés sur les procédures d’évacuation et la manipulation des produits chimiques.
- Réduction de l’empreinte carbone grâce à des machines plus efficaces énergétiquement.
Résultat
Un environnement de travail plus sûr et conforme aux réglementations environnementales, ce qui contribue à améliorer la satisfaction et la fidélisation des employés.
7. Gestion de la Qualité : Assurer une Production Conforme
La gestion de la qualité dans le cadre de la TPM vise à éliminer les défauts de fabrication et à garantir que les équipements produisent des pièces conformes aux spécifications.
Outils Clés
- SPC (Statistical Process Control) pour surveiller les variations dans le processus.
- AMDEC (Analyse des Modes de Défaillance, de leurs Effets et de leur Criticité) pour identifier les risques potentiels.
Exemple
Dans une usine d’embouteillage, l’utilisation de capteurs pour détecter les fluctuations de température dans les systèmes de pasteurisation permet de maintenir la qualité constante des produits.
8. Efficacité des Équipements (OEE) : Mesurer et Améliorer la Performance
L’OEE (Overall Equipment Effectiveness) est un indicateur clé pour évaluer l’efficacité globale des machines. Il prend en compte :
- La disponibilité : temps de fonctionnement réel par rapport au temps total prévu.
- La performance : vitesse de production réelle comparée à la vitesse optimale.
- La qualité : proportion de produits conformes.
Avantages
- Identifier rapidement les goulots d’étranglement.
- Prioriser les investissements dans les zones à faibles performances.
- Mesurer l’impact des initiatives TPM sur la productivité.
Exemple
Une ligne de production ayant une disponibilité de 90 %, une performance de 95 %, et une qualité de 98 % aura un OEE de 83,61 %. Cet indicateur peut ensuite servir de référence pour identifier des pistes d’amélioration.
==> Les huit piliers de la TPM constituent un cadre solide pour transformer la manière dont les entreprises gèrent leurs équipements. En intégrant la maintenance dans chaque aspect des opérations et en responsabilisant tous les employés, la TPM devient un levier essentiel pour augmenter la productivité, améliorer la qualité, et réduire les coûts. Sa mise en œuvre demande du temps et des efforts, mais les résultats, tant en termes de performance que de satisfaction des employés, en valent largement la peine.
Les Avantages de la TPM pour l’Industrie
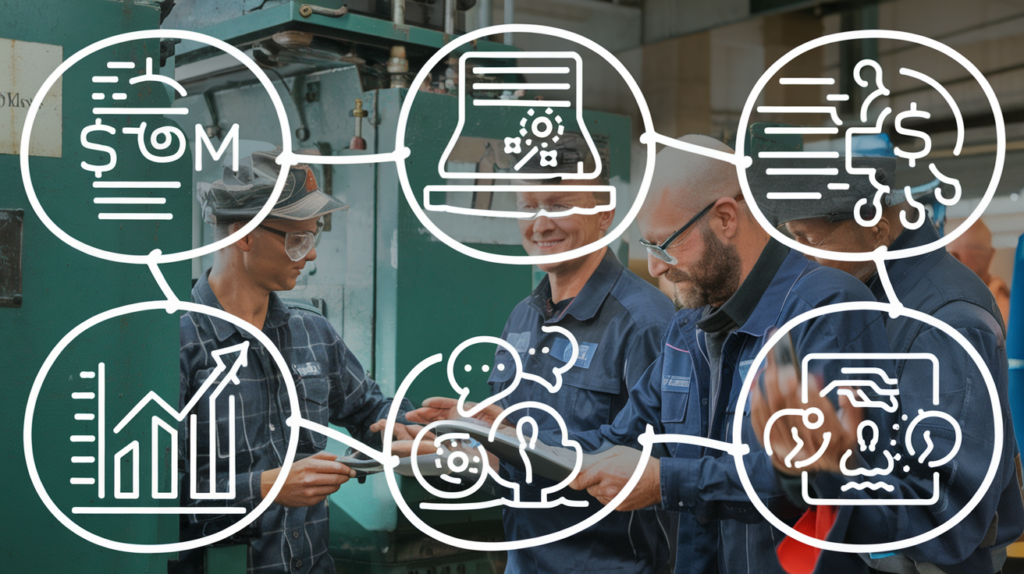
L’implémentation de la Maintenance Productive Totale (TPM) offre une multitude de bénéfices tangibles pour les entreprises industrielles. Elle ne se limite pas à la réduction des pannes ; elle transforme profondément les pratiques de gestion, l’implication des équipes, et la performance globale. Explorons en détail ces avantages et leur impact stratégique.
1. Réduction des Coûts : Une Maintenance Proactive et Efficace
La TPM adopte une approche proactive qui cible la prévention des pannes et la limitation des pertes. Cela se traduit directement par une diminution des coûts à plusieurs niveaux.
Principaux Gains Financiers
- Diminution des coûts de réparation grâce à une maintenance préventive efficace.
- Réduction des pertes liées à des produits défectueux ou hors normes.
- Optimisation des stocks de pièces détachées, évitant les achats en urgence souvent plus onéreux.
Exemple Pratique
Une entreprise de fabrication de composants électroniques a réduit de 25 % ses coûts de maintenance en adoptant des pratiques de TPM, notamment grâce à un suivi régulier des équipements critiques.
2. Amélioration de la Productivité : Des Machines Toujours Disponibles
L’un des objectifs principaux de la TPM est de minimiser les arrêts non planifiés, permettant ainsi d’augmenter la disponibilité des équipements.
Résultats Obtenus
- Augmentation du taux d’utilisation des machines, maximisant ainsi leur rendement.
- Réduction des temps d’arrêt grâce à une planification rigoureuse des interventions.
- Meilleure coordination entre les équipes grâce à des processus standardisés.
Indicateur Clé
Le Taux de Rendement Synthétique (OEE) est souvent utilisé pour mesurer cette amélioration. Une usine ayant un OEE initial de 65 % peut atteindre 85 % après une mise en œuvre réussie de la TPM.
3. Engagement des Employés : Une Culture de Responsabilité Partagée
La TPM place les employés au cœur de ses pratiques, leur offrant l’opportunité de participer activement à la maintenance et à l’amélioration continue des processus.
Bienfaits pour les Équipes
- Renforcement des compétences grâce à des formations continues.
- Sentiment de contribution accrue, améliorant la satisfaction et la motivation des employés.
- Collaboration renforcée entre les opérateurs et les techniciens de maintenance.
Exemple Concret
Dans une usine de fabrication automobile, l’implication des opérateurs dans la maintenance autonome a permis de réduire de 30 % les délais nécessaires pour identifier et résoudre les pannes mineures.
4. Qualité Améliorée : Réduction des Déchets et des Défauts
En assurant une performance optimale des équipements, la TPM contribue à maintenir des standards élevés de qualité.
Avantages Concrets
- Réduction des produits non conformes grâce à une meilleure stabilité des processus.
- Limitation des rebuts et des reprises, diminuant ainsi le gaspillage.
- Amélioration de la satisfaction des clients grâce à des produits conformes aux spécifications.
5. Sécurité et Environnement : Un Impact Positif et Responsable
En intégrant des pratiques de sécurité et des initiatives environnementales, la TPM garantit un environnement de travail sûr et durable.
Impacts Clés
- Réduction des accidents du travail grâce à des équipements bien entretenus.
- Meilleure gestion des déchets industriels, alignée avec les réglementations environnementales.
- Contribution à l’image de marque de l’entreprise en tant qu’acteur responsable.
6. Adaptabilité et Innovation : Préparer l’Avenir
En adoptant les principes de la TPM, les entreprises deviennent plus résilientes face aux défis et opportunités futurs.
Bénéfices Long Terme
- Meilleure capacité à intégrer des technologies modernes, comme l’IoT et la maintenance prédictive.
- Réduction des cycles d’apprentissage pour les nouveaux employés grâce à des processus documentés et optimisés.
- Positionnement compétitif renforcé dans un marché en constante évolution.
==> La TPM n’est pas simplement une méthode de maintenance, mais un levier stratégique pour transformer les performances industrielles. En combinant des coûts réduits, une productivité accrue, et un engagement renforcé des équipes, elle offre aux entreprises une solution durable et rentable. Que ce soit pour améliorer la qualité, sécuriser l’environnement de travail, ou adopter les technologies de demain, la TPM s’impose comme un atout essentiel pour les industries modernes.
Mise en Œuvre de la TPM : Étapes Clés
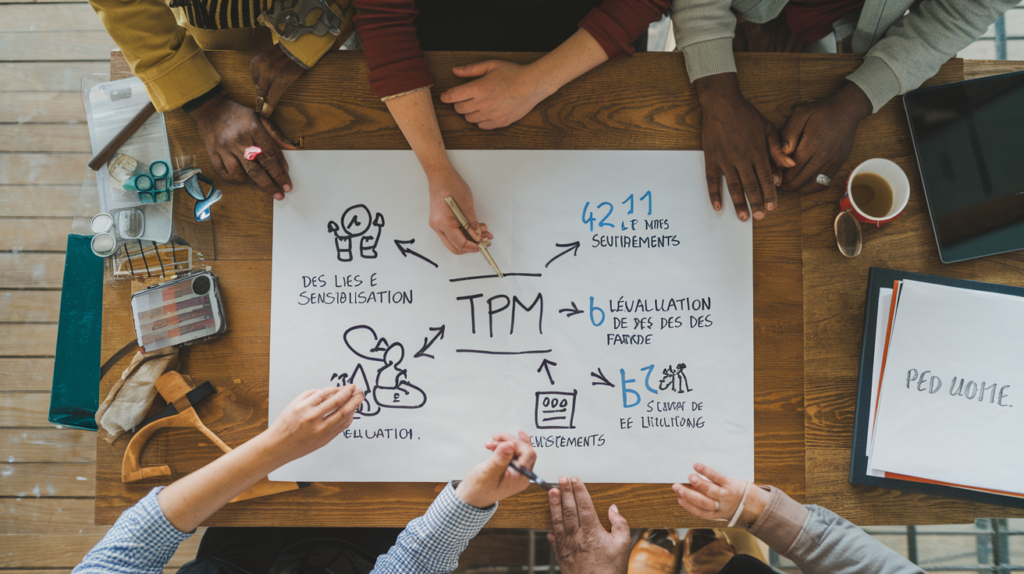
Mettre en place la Maintenance Productive Totale (TPM) dans une organisation industrielle demande une planification rigoureuse et une implication active de tous les acteurs. Cette démarche vise à créer une culture de responsabilité partagée et à optimiser la performance des équipements. Voici les étapes essentielles pour assurer une mise en œuvre efficace de la TPM.
1. Sensibilisation et Formation : Impliquer et Mobiliser les Équipes
La première étape de la mise en œuvre de la TPM consiste à familiariser tous les employés avec ses principes fondamentaux et à souligner son importance pour l’entreprise.
Actions à Entreprendre
- Séances de sensibilisation : Organiser des ateliers pour expliquer les objectifs et les bénéfices de la TPM.
- Formation ciblée : Former les opérateurs, techniciens et managers sur leurs rôles respectifs dans le cadre de la TPM.
- Communication interne : Utiliser des supports comme des affiches, des vidéos ou des newsletters pour maintenir l’engagement.
Résultat Attendu
Une meilleure compréhension de la TPM et une adhésion accrue des employés, favorisant leur implication dans le processus.
2. Évaluation des Équipements : Identifier les Priorités
Une analyse approfondie des équipements existants est cruciale pour déterminer lesquels nécessitent une attention particulière.
Étapes Clés
- Audit des équipements : Évaluer l’état actuel des machines en termes de fiabilité, disponibilité et performance.
- Analyse des données historiques : Examiner les pannes, arrêts et coûts de maintenance pour identifier les points faibles.
- Classification des équipements critiques : Prioriser les machines ayant un impact direct sur la production.
Outils Utiles
- Matrices de criticité pour classer les équipements.
- Analyse de Pareto pour identifier les pannes les plus fréquentes.
3. Déploiement Progressif des Piliers : Une Approche Structurée
La TPM repose sur huit piliers fondamentaux. Leur déploiement doit se faire progressivement pour assurer une adoption fluide et efficace.
Méthodologie
- Maintenance autonome : Initier les opérateurs aux tâches de maintenance de base.
- Maintenance planifiée : Établir un calendrier d’entretien préventif.
- Amélioration focalisée (Kaizen) : Mettre en place des groupes de travail pour résoudre les problèmes spécifiques.
- Contrôle initial : Standardiser les procédures pour les nouveaux équipements.
- Formation continue : Développer les compétences à travers des programmes réguliers.
- Sécurité et environnement : Intégrer des mesures pour garantir un environnement de travail sûr.
- Gestion de la qualité : Utiliser des outils comme le 5 Why ou le diagramme d’Ishikawa.
- Efficacité des équipements (OEE) : Suivre les performances à l’aide de cet indicateur clé.
Résultat Attendu
Une intégration progressive et efficace des pratiques TPM dans le quotidien de l’entreprise.
4. Suivi et Mesure des Résultats : Valider l’Impact de la TPM
Pour garantir le succès de la TPM, il est indispensable de mesurer régulièrement les progrès réalisés et de les comparer aux objectifs fixés.
Indicateurs Clés
- OEE (Overall Equipment Effectiveness) : Mesurer la disponibilité, la performance et la qualité des équipements.
- Taux de pannes : Suivre la fréquence et la gravité des arrêts.
- Temps moyen entre deux pannes (MTBF) : Évaluer la fiabilité des machines.
- Temps moyen de réparation (MTTR) : Analyser l’efficacité des interventions.
Processus de Suivi
- Revues périodiques : Organiser des réunions pour examiner les résultats et identifier les zones à améliorer.
- Boucles de rétroaction : Encourager les employés à partager leurs observations pour affiner les pratiques.
- Communication des succès : Diffuser les réussites pour maintenir la motivation.
La mise en œuvre de la TPM est un processus qui exige une approche méthodique, une communication claire et un engagement collectif. En suivant ces étapes, les entreprises peuvent non seulement améliorer la performance de leurs équipements, mais aussi transformer leur culture organisationnelle en faveur de l’excellence opérationnelle.
5. Exemples Concrets d’Application de la TPM
Industrie Automobile
Dans une usine de fabrication automobile, la TPM a permis de réduire les temps d’arrêt de 30 % en formant les opérateurs à effectuer des inspections régulières et en utilisant l’OEE pour identifier les zones d’amélioration.
Industrie Agroalimentaire
Une entreprise agroalimentaire a mis en œuvre la TPM pour améliorer la qualité de ses produits, réduisant ainsi les défauts de 20 % grâce à une maintenance préventive renforcée et une meilleure gestion de la qualité.
Les Défis de l’Implémentation de la TPM
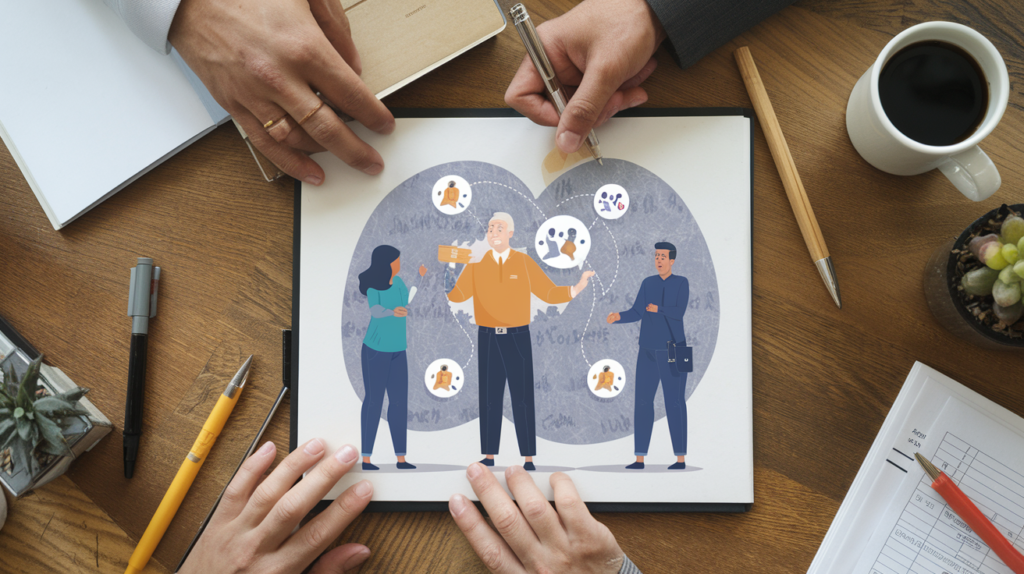
L’adoption de la Maintenance Productive Totale (TPM) est une démarche stratégique qui peut transformer les performances industrielles. Cependant, elle s’accompagne de défis majeurs à surmonter pour garantir son succès. Identifier ces obstacles et mettre en place des solutions adaptées est essentiel pour maximiser l’impact de la TPM.
1. Résistance au Changement : Le Premier Obstacle à Franchir
La TPM implique une réorganisation des méthodes de travail et un changement culturel au sein de l’entreprise. Cela peut entraîner des réticences, en particulier chez les employés habitués aux pratiques traditionnelles.
Raisons de la Résistance
- Manque de compréhension : Les employés peuvent percevoir la TPM comme une charge supplémentaire ou une remise en question de leurs compétences.
- Peur de l’inconnu : La mise en œuvre de nouveaux outils ou processus peut créer des inquiétudes sur leur maîtrise.
- Inertie organisationnelle : Les entreprises ayant une structure rigide peuvent avoir du mal à intégrer des pratiques collaboratives.
Solutions pour surmonter ce défi
- Communication claire : Expliquer les objectifs et les bénéfices concrets de la TPM pour les employés et l’entreprise.
- Implication précoce : Faire participer les équipes dès les premières étapes de la mise en œuvre pour favoriser leur adhésion.
- Programmes de formation : Offrir un accompagnement ciblé pour développer les compétences nécessaires à la TPM.
2. Manque de Ressources : Temps, Budget et Expertise
L’implémentation de la TPM demande des investissements initiaux en termes de formation, d’équipement et de temps.
Problèmes Fréquents
- Budget limité : Certaines entreprises, notamment les PME, peuvent hésiter à consacrer des ressources à une transformation perçue comme coûteuse.
- Manque de temps : Les équipes opérationnelles peuvent être déjà surchargées, rendant difficile l’allocation de temps pour des initiatives TPM.
- Pénurie d’expertise : L’absence de connaissances techniques sur la TPM peut ralentir sa mise en œuvre.
Approches Recommandées
- Évaluation préalable : Identifier les besoins spécifiques de l’entreprise pour optimiser les investissements.
- Priorisation progressive : Déployer les piliers de la TPM étape par étape pour éviter de surcharger les équipes.
- Appui externe : Faire appel à des consultants ou experts pour guider la transition.
3. Difficulté à Maintenir l’Engagement sur le Long Terme
Une fois la TPM lancée, le défi réside dans la pérennisation des efforts. Sans suivi rigoureux, les bonnes pratiques peuvent s’effriter avec le temps.
Risques
- Retour aux anciennes habitudes : En l’absence d’une culture TPM forte, les employés peuvent revenir aux anciennes méthodes de travail.
- Manque de motivation : Si les bénéfices de la TPM ne sont pas visibles rapidement, l’enthousiasme peut diminuer.
- Problèmes de leadership : Une direction insuffisamment impliquée peut compromettre l’initiative.
Stratégies pour Assurer la Durabilité
- Suivi régulier : Mettre en place des indicateurs de performance comme l’OEE pour mesurer les progrès.
- Reconnaissance des réussites : Valoriser les efforts individuels et collectifs pour maintenir la motivation.
- Leadership fort : Impliquer les managers dans la promotion des pratiques TPM au quotidien.
4. Difficulté d’Intégration avec les Processus Existants
Adapter la TPM aux systèmes et procédures en place peut représenter un défi, surtout dans les entreprises dotées de processus complexes.
Enjeux
- Incompatibilité avec les outils existants : Les systèmes de gestion ou logiciels utilisés peuvent ne pas être adaptés aux principes de la TPM.
- Rigidité organisationnelle : Certaines structures d’entreprise peuvent limiter la flexibilité nécessaire à l’intégration de la TPM.
Solutions
- Diagnostic initial : Analyser les processus existants pour repérer les incompatibilités.
- Adaptation personnalisée : Modifier les pratiques TPM pour les aligner sur les spécificités de l’entreprise.
- Automatisation : Intégrer des technologies comme la GMAO (Gestion de Maintenance Assistée par Ordinateur) pour simplifier la mise en œuvre.
5. Mesure et Évaluation des Résultats : Une Complexité Sous-Estimée
Sans un suivi précis des performances, il devient difficile de prouver l’efficacité de la TPM et d’ajuster les initiatives en conséquence.
Défis
- Indicateurs mal définis : L’absence de métriques claires peut empêcher une évaluation objective.
- Données insuffisantes : Les systèmes en place peuvent ne pas collecter les informations nécessaires pour mesurer l’impact de la TPM.
Recommandations
- Définir des KPI spécifiques : Utiliser des indicateurs comme le MTTR (Mean Time to Repair) ou l’OEE pour suivre les progrès.
- Adopter des outils modernes : Intégrer des solutions numériques pour collecter et analyser les données en temps réel.
- Boucles de rétroaction : Ajuster les pratiques TPM en fonction des résultats obtenus.
===>L’implémentation de la TPM est une aventure complexe mais riche en opportunités. En anticipant ces défis et en adoptant des solutions adaptées, les entreprises peuvent transformer leur organisation et atteindre des niveaux de performance inégalés. Une préparation minutieuse, un engagement continu et une communication efficace sont les clés pour surmonter les obstacles et tirer le meilleur parti de la TPM.
Conclusion
La Maintenance Productive Totale (TPM) est une stratégie incontournable pour les entreprises cherchant à maximiser l’efficacité de leurs équipements et à améliorer la qualité de leurs produits. En intégrant l’ensemble des employés dans le processus de maintenance et en adoptant une approche proactive, la TPM transforme la culture d’entreprise et génère des gains de performance significatifs. Les résultats parlent d’eux-mêmes : des machines plus fiables, une productivité accrue et une satisfaction client améliorée.
Adopter la TPM n’est pas seulement une question de maintenance ; c’est une décision stratégique pour toute organisation qui souhaite rester compétitive dans le secteur industriel.