La fiabilité et la maintenance des matériels industriels jouent un rôle crucial dans la performance globale des entreprises. Ces concepts permettent de minimiser les interruptions de production, de prolonger la durée de vie des équipements et de réduire les coûts liés aux pannes. Mais comment différencier la gestion des équipements réparables et non réparables, et quelles sont les meilleures stratégies à adopter ? Cet article vous propose une exploration approfondie de ces thématiques avec des exemples concrets pour mieux comprendre leur importance.
Table of Contents
Fiabilité et Maintenance des Matériels Industriels Réparables et Non Réparables
Comprendre la Fiabilité des Équipements Industriels
La fiabilité d’un équipement se définit comme sa capacité à fonctionner sans défaillance pendant une durée donnée dans des conditions précises. Cette notion est cruciale pour garantir la performance et la rentabilité des systèmes industriels. Elle repose sur plusieurs facteurs clés :
Facteurs Clés de la Fiabilité
Conception et Fabrication
Des équipements bien conçus, utilisant des matériaux de qualité, présentent une meilleure fiabilité. Cela inclut l’ingénierie de précision, l’utilisation de composants robustes et la validation rigoureuse des designs.
Exemple concret : Les roulements à billes de haute précision fabriqués par SKF sont réputés pour leur durée de vie exceptionnelle, grâce à des processus de fabrication avancés et à l’utilisation de matériaux comme l’acier trempé.
Conditions d’Utilisation
Une utilisation en dehors des spécifications techniques peut rapidement diminuer la fiabilité d’un équipement. Cela inclut des facteurs comme les charges excessives, les températures extrêmes ou une mauvaise installation.
Exemple concret : Un moteur électrique conçu pour une charge maximale de 100 kW, s’il est surchargé régulièrement à 120 kW, risque de surchauffer, entraînant une défaillance prématurée.
Maintenance Préventive
Les inspections et interventions régulières permettent de prévenir les pannes en identifiant et en corrigeant les anomalies avant qu’elles ne deviennent critiques. Cela inclut des actions comme le remplacement des pièces usées, la lubrification des composants mobiles et le nettoyage des systèmes.
Exemple concret : Une pompe hydraulique dans une usine chimique, inspectée mensuellement et entretenue selon un calendrier rigoureux, peut prolonger sa durée de vie de plusieurs années.
Indicateurs de Fiabilité

MTBF (Mean Time Between Failures)
Le MTBF, ou temps moyen entre deux pannes, est un indicateur clé pour évaluer la fiabilité d’un équipement. Plus le MTBF est élevé, plus l’équipement est fiable.
Exemple : Une machine de production avec un MTBF de 500 heures subira en moyenne une panne toutes les 500 heures d’utilisation.
Taux de Défaillance
Le taux de défaillance représente la probabilité qu’une panne survienne sur une période donnée. Cet indicateur est souvent exprimé en pourcentage ou en fréquence annuelle.
Exemple : Un système électronique ayant un taux de défaillance de 2 % par an signifie que, sur 100 unités, 2 devraient tomber en panne chaque année.
En résumé, comprendre et maîtriser les facteurs de fiabilité est essentiel pour garantir une performance optimale et minimiser les interruptions dans les processus industriels. Une attention particulière doit être accordée à la conception, à l’utilisation et à la maintenance des équipements pour maximiser leur durée de vie et leur efficacité.
Différence entre Matériels Réparables et Non Réparables
Matériels Réparables
Ce sont des équipements pour lesquels les pannes peuvent être corrigées en remplaçant ou en réparant les composants défectueux. Ces matériels jouent un rôle crucial dans les systèmes industriels complexes, où le remplacement total est coûteux ou techniquement difficile.
Caractéristiques :
- Coûts de maintenance souvent élevés : Les réparations nécessitent des compétences spécialisées, des outils spécifiques et des pièces détachées de qualité.
- Dépendance à des pièces de rechange : Les délais de livraison des pièces peuvent influencer la disponibilité de l’équipement.
Exemple concret : Les pompes hydrauliques utilisées dans les systèmes de refroidissement industriels nécessitent un entretien régulier et des réparations fréquentes, notamment pour remplacer les joints ou les pistons endommagés.
Matériels Non Réparables
Ces équipements sont conçus pour être remplacés directement en cas de panne. Ils sont souvent plus simples et économiques, ce qui les rend adaptés à des systèmes où la réparation n’est pas justifiée économiquement.
Caractéristiques :
- Coûts de remplacement fixes : Contrairement aux réparations, le coût est prévisible et peut être intégré dans le budget.
- Cycle de vie prédictible : Ces matériels sont généralement utilisés jusqu’à leur fin de vie prévue, sans intervention intermédiaire.
Exemple concret : Les fusibles dans un tableau électrique ou les roulements jetables utilisés dans des machines à usage unique. Par exemple, un roulement dans une chaîne de production alimentaire est souvent remplacé après un certain nombre de cycles pour éviter tout risque de contamination.
En conclusion, la distinction entre matériels réparables et non réparables repose sur des critères économiques, techniques et stratégiques. Chaque type a ses avantages et ses limites, et leur choix dépend des exigences spécifiques de l’industrie concernée.
Strégies de Maintenance Adaptées

Maintenance Préventive
La maintenance préventive consiste à effectuer des actions planifiées pour éviter les pannes et maintenir les équipements en bon état de fonctionnement. Cette approche repose sur un calendrier défini en fonction des recommandations des fabricants ou de l’analyse des données historiques.
Avantages :
- Réduction significative des interruptions imprévues, permettant une continuité des opérations.
- Allongement de la durée de vie des équipements grâce à une prise en charge proactive.
- Amélioration de la sécurité des opérateurs et des installations.
Exemple concret : Une entreprise de fabrication de verre planifie le nettoyage et le remplacement des filtres des fours tous les six mois. Cette intervention régulière permet de prévenir les obstructions et d’éviter des pannes coûteuses qui pourraient perturber la production.
Maintenance Corrective
La maintenance corrective intervient après qu’une panne soit survenue. Elle vise à réparer ou à remplacer les éléments défectueux pour remettre les équipements en service. Bien que cette stratégie soit simple, elle peut entraîner des conséquences négatives en termes de productivité.
Avantages :
- Simplicité de gestion, car aucune planification préalable n’est nécessaire.
- Adaptée aux équipements non critiques ou à faible coût de remplacement.
Inconvénients :
- Temps d’arrêt non planifié pouvant perturber les opérations.
- Coûts potentiellement élevés en cas de défaillance majeure.
Exemple concret : Lorsqu’un moteur électrique brûlé sur une chaîne de production tombe en panne, il est remplacé pour permettre une reprise rapide de l’activité.
Maintenance Conditionnelle
La maintenance conditionnelle repose sur la surveillance en temps réel de l’état des équipements. Cette stratégie utilise des capteurs et des outils d’analyse pour détecter les signes précurseurs de défaillance et intervenir uniquement lorsque cela est nécessaire.
Avantages :
- Optimisation des coûts de maintenance en réduisant les interventions inutiles.
- Intervention au moment opportun, limitant les arrêts non prévus.
- Amélioration de la précision dans la détection des problèmes.
Exemple concret : Une usine utilise des capteurs IoT pour surveiller les vibrations des machines. Si une augmentation anormale des vibrations est détectée, une intervention est planifiée pour éviter une panne imminente, évitant ainsi des coûts élevés de réparation ou de remplacement.
Cas Pratique : Gestion des Pannes dans une Usine de Transformation Alimentaire
Dans une usine de transformation alimentaire, où les marges de production sont étroites et les exigences de qualité strictes, il est impératif que les équipements critiques, tels que les tapis roulants et les machines d’emballage, fonctionnent en continu sans interruption. Toute panne non planifiée peut entraîner des pertes financières importantes et compromettre la sécurité alimentaire. Voici les étapes détaillées suivies pour optimiser la maintenance :
Analyse des Données
L’analyse des données historiques est une étape fondamentale pour comprendre les causes des pannes et anticiper les problèmes futurs.
- Historique des pannes : Un registre détaillé des pannes est maintenu, incluant les causes, la durée des interruptions et les solutions apportées. Cette base de données permet d’identifier les tendances récurrentes.
- MTBF (Mean Time Between Failures) : Le calcul du temps moyen entre deux pannes pour chaque équipement fournit une estimation claire de la fiabilité. Par exemple, si une machine d’emballage présente un MTBF de 300 heures, des actions préventives peuvent être planifiées avant ce seuil.
Mise en Place de Capteurs
L’intégration de capteurs intelligents permet une surveillance en temps réel des équipements critiques.
- Capteurs de température : Installés sur les moteurs et les roulements, ils permettent de détecter une surchauffe, indicateur potentiel d’une défaillance imminente.
- Capteurs de vibration : Utilisés pour surveiller les variations anormales des vibrations des machines, ces capteurs peuvent alerter en cas de déséquilibre ou d’usure mécanique.
Exemple concret : Un tapis roulant équipé de capteurs de vibration envoie une alerte lorsqu’une anomalie est détectée. Cela permet à l’équipe de maintenance d’intervenir avant que la panne ne se produise.
Actions Préventives
Des actions régulières sont mises en œuvre pour éviter les défaillances :
- Lubrification hebdomadaire des convoyeurs : Cette tâche essentielle réduit l’usure des pièces mobiles et améliore l’efficacité énergétique des systèmes.
- Inspection visuelle : Une inspection hebdomadaire permet de détecter des signes de détérioration tels que des fissures, des fuites ou des pièces mal alignées.
Plan de Réparation
Un plan de réparation structuré garantit une intervention rapide et efficace en cas de panne :
- Constitution d’un stock de pièces critiques : Des pièces essentielles, telles que des courroies, des roulements et des moteurs, sont stockées sur place pour réduire les temps d’arrêt.
- Équipe de maintenance formée : Les techniciens sont formés pour effectuer des réparations rapides et minimiser l’impact sur la production.
Exemple concret : Lorsqu’une machine d’emballage tombe en panne, une courroie de rechange est immédiatement disponible, permettant une remise en service en moins de 30 minutes.
En résumé, la combinaison d’une analyse approfondie des données, de l’utilisation de capteurs intelligents et de la mise en œuvre de stratégies préventives et correctives permet à l’usine de transformation alimentaire de maintenir une production fluide et de répondre aux exigences strictes de qualité et de sécurité.
Intégration de la Technologie dans la Maintenance
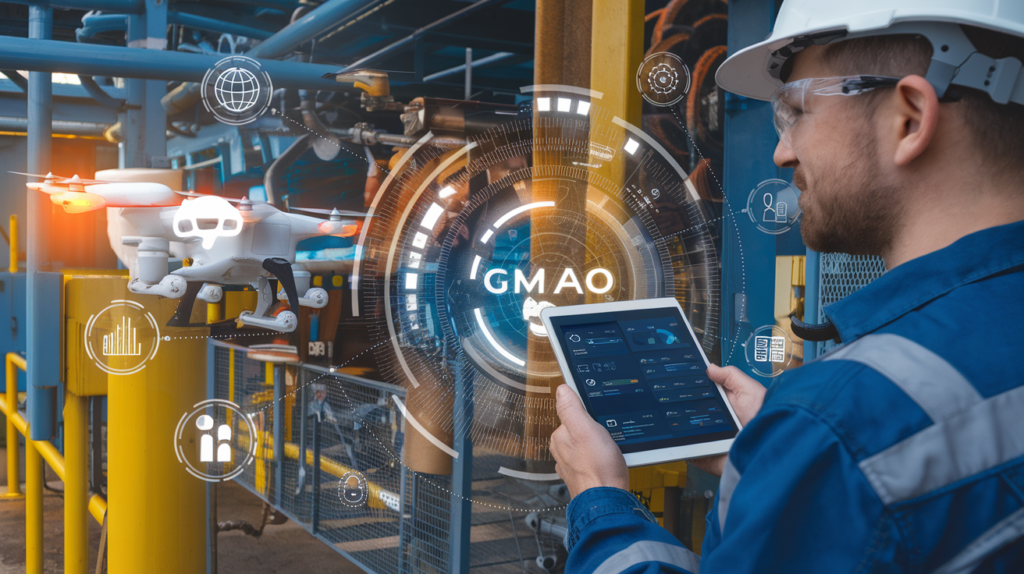
IoT et Maintenance Prédictive
L’Internet des objets (IoT) transforme la maintenance en connectant les équipements à des systèmes intelligents de surveillance et d’analyse en temps réel. Grâce à des capteurs embarqués, il est possible de recueillir des données précises sur l’état des machines et de prévoir les pannes avant qu’elles ne surviennent.
Exemple concret : General Electric utilise des capteurs IoT pour surveiller les turbines éoliennes. Les données collectées, telles que les vibrations et la température, sont analysées en temps réel pour identifier les signes précurseurs de défaillances, réduisant ainsi les interruptions imprévues et augmentant l’efficacité énergétique.
Intelligence Artificielle
L’IA révolutionne la maintenance industrielle en offrant des capacités avancées d’analyse de données. En exploitant le machine learning, les systèmes d’IA peuvent prédire les défaillances, optimiser les calendriers de maintenance et réduire les coûts.
Exemple concret : IBM Watson est largement utilisé pour analyser les données de capteurs dans les usines. Par exemple, dans une raffinerie pétrolière, Watson peut détecter des anomalies subtiles dans les pressions ou les températures, prévoyant des défaillances potentielles des équipements critiques.
Logiciels de GMAO (Gestion de Maintenance Assistée par Ordinateur)
Les outils de GMAO permettent de planifier, suivre et optimiser toutes les activités de maintenance. Ces logiciels centralisent les informations sur les équipements, gèrent les stocks de pièces détachées et génèrent des rapports détaillés pour une meilleure prise de décision.
Exemple concret : Le logiciel SAP PM est utilisé dans de grandes industries comme l’aéronautique pour gérer les actifs industriels. Il permet de suivre en temps réel l’état des machines, d’organiser les interventions et d’optimiser les coûts grâce à une planification précise.
Conclusion
La fiabilité et la maintenance des matériels industriels, qu’ils soient réparables ou non, sont essentielles pour garantir la performance et la compétitivité des entreprises. En combinant des stratégies adaptées, une surveillance conditionnelle et les nouvelles technologies, il est possible de réduire les coûts, d’améliorer la productivité et d’assurer la durabilité des équipements. Pour aller plus loin, n’hésitez pas à explorer des outils spécialisés et à consulter des experts du domaine.
Ressources Utiles :