La maintenance autonome est en passe de devenir un élément clé dans la gestion industrielle moderne. Ce concept repose sur l’implication directe des opérateurs dans l’entretien de base de leurs équipements, permettant non seulement d’améliorer la productivité, mais aussi de garantir un meilleur maintien des machines sur le long terme.
Elle s’intègre dans le cadre plus large de la Maintenance Productive Totale (TPM), une méthode de gestion visant à maximiser l’efficacité des équipements tout en réduisant les arrêts imprévus. Dans cet article, nous explorerons les fondements de la maintenance autonome, ses avantages, ainsi que les stratégies de mise en œuvre réussies, le tout illustré par des exemples concrets tirés du terrain.
Table of Contents
Les Fondements de la Maintenance Autonome
1. Concept et Objectifs
La maintenance autonome consiste à transférer une partie des responsabilités d’entretien des équipements aux opérateurs. Ceux-ci sont formés pour effectuer des inspections de base, des nettoyages réguliers, et de petites interventions sur les machines qu’ils utilisent quotidiennement. L’objectif principal est de prévenir la détérioration des équipements, ce qui permet non seulement de réduire les coûts de maintenance corrective, mais aussi d’améliorer la disponibilité des machines.
Dans une usine automobile, par exemple, l’introduction de la maintenance autonome a permis à une équipe d’opérateurs de prendre en charge le nettoyage et l’inspection régulière des robots de soudure. Résultat ? Une réduction de 15 % des pannes imprévues et une amélioration notable des performances des équipements sur une période de six mois.
2. Les Avantages de la Maintenance Autonome
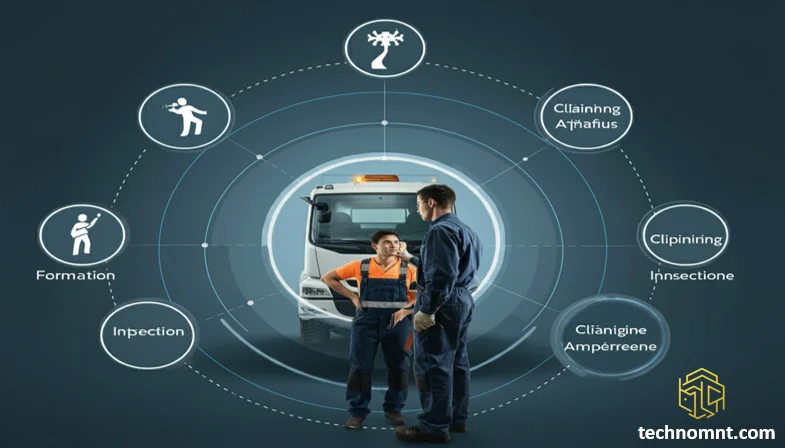
La mise en œuvre de la maintenance autonome présente plusieurs avantages :
- Amélioration de la performance des équipements : En prenant soin des tâches de maintenance de base, les opérateurs contribuent à réduire les arrêts non planifiés et à prolonger la durée de vie des machines.
- Réduction des temps d’arrêt imprévus : La détection précoce des anomalies permet d’intervenir rapidement avant qu’un dysfonctionnement majeur ne survienne.
- Renforcement de la culture de qualité et de sécurité : Les opérateurs deviennent plus conscients de l’importance de la maintenance et de la sécurité, ce qui améliore globalement les conditions de travail.
- Développement d’un sentiment d’appartenance et de responsabilité : Lorsque les opérateurs participent directement à l’entretien des machines, ils se sentent davantage impliqués dans le bon fonctionnement de l’usine.
Mise en Œuvre de la Maintenance Autonome
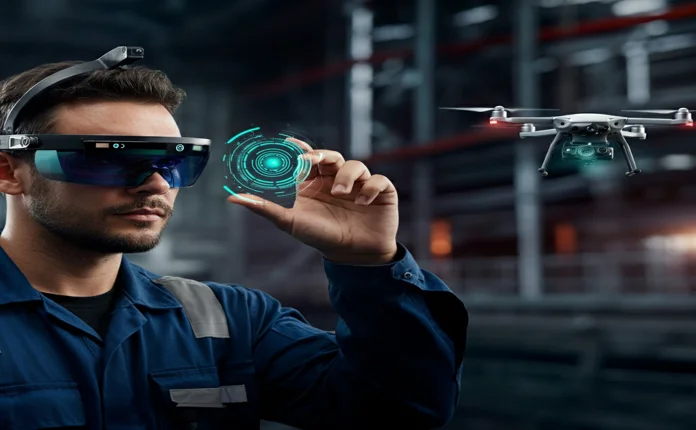
1. Étapes Clés pour une Mise en Œuvre Réussie
Pour une transition efficace vers la maintenance autonome, il est essentiel de suivre plusieurs étapes :
- Formation des Opérateurs : Les opérateurs doivent être formés aux techniques de maintenance de base, incluant le nettoyage, la lubrification, et les inspections visuelles. Par exemple, dans une usine textile, un programme de formation spécifique a été mis en place pour apprendre aux opérateurs à inspecter et ajuster les machines à tisser. Cette initiative a permis de réduire de 20 % les coûts de maintenance externe.
- Nettoyage et Inspection Initiaux : Avant de commencer la maintenance autonome, une évaluation complète de l’état des équipements doit être réalisée. Cela permet de repérer les besoins immédiats de maintenance. Une entreprise de production de boissons a ainsi pu identifier des problèmes de lubrification sur ses lignes de mise en bouteille, évitant des arrêts prolongés.
- Élimination des Sources de Contamination : Un environnement de travail propre est crucial pour éviter les pannes. Dans une usine de production d’acier, par exemple, l’élimination régulière de la poussière et des débris autour des fours a permis de prolonger la durée de vie des capteurs de température.
- Établissement de Normes de Lubrification et d’Inspection : Des protocoles clairs doivent être mis en place pour garantir que chaque machine reçoit l’entretien approprié à intervalles réguliers. Dans une entreprise de fabrication de papier, la mise en place d’un protocole de lubrification hebdomadaire a permis d’augmenter de 10 % la productivité des presses.
- Surveillance et Inspection Continue : La maintenance autonome repose sur une surveillance constante des machines par les opérateurs. Des outils comme les fiches de suivi visuel peuvent être utilisés pour signaler les anomalies. Une usine de montage de véhicules utilise des tableaux d’affichage à chaque poste de travail pour indiquer l’état des équipements en temps réel.
- Amélioration Continue : La maintenance autonome est un processus évolutif. Les retours des opérateurs doivent être intégrés dans les stratégies de maintenance pour affiner et optimiser les procédures au fil du temps.
2. Outils et Technologies pour la Maintenance Autonome
Avec l’avènement de nouvelles technologies, la maintenance autonome se dote d’outils performants pour améliorer l’efficacité des interventions. Les plateformes de gestion de maintenance assistée par ordinateur (GMAO), comme celles proposées par Limble CMMS, permettent de planifier et suivre les opérations de maintenance en temps réel. Les opérateurs peuvent utiliser des applications mobiles pour enregistrer les interventions et signaler les dysfonctionnements.
L’Internet des Objets (IoT) joue également un rôle crucial en permettant de collecter des données en temps réel sur l’état des équipements. Par exemple, des capteurs placés sur des compresseurs d’air dans une usine chimique permettent de surveiller la pression et de prévenir toute surchauffe. L’intelligence artificielle (IA) peut analyser ces données pour prédire les pannes et recommander des actions correctives avant que des problèmes ne surviennent.
Études de Cas et Exemples Pratiques
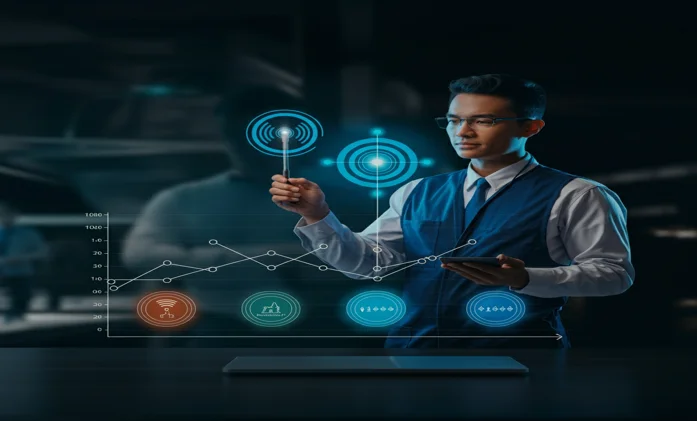
Exemples de Mise en Œuvre Réussie
Plusieurs entreprises ont réussi à adopter la maintenance autonome avec des résultats impressionnants :
- Toyota : Pionnier dans l’application de la maintenance autonome, Toyota a intégré cette approche dans son système de production dès les années 70. Les opérateurs sont non seulement responsables du bon fonctionnement des machines, mais aussi de leur maintenance quotidienne, ce qui a permis à l’entreprise de minimiser les pannes et d’améliorer sa productivité.
- Unilever : Cette multinationale a également adopté la maintenance autonome dans plusieurs de ses sites de production. Les opérateurs de ses usines alimentaires sont formés à inspecter et entretenir les machines, ce qui a permis de réduire de 25 % les interventions de maintenance non planifiées en l’espace de deux ans.
Témoignages d’Opérateurs
Jean-Pierre, opérateur dans une usine de production de cosmétiques, témoigne : “Depuis que nous avons commencé à entretenir nous-mêmes nos machines, je me sens plus impliqué dans le processus de production. Nous sommes désormais capables de repérer les problèmes avant qu’ils ne deviennent critiques, ce qui fait toute la différence.”
Perspectives d’Avenir
La maintenance autonome continue d’évoluer, notamment grâce à l’intégration des technologies de l’Industrie 4.0. L’utilisation croissante de capteurs intelligents, couplée à l’analyse des données en temps réel, permet de rendre les interventions de maintenance plus précises et efficaces. De plus, les drones et les robots autonomes sont déjà utilisés dans certains secteurs, comme l’énergie ou la logistique, pour effectuer des inspections dans des zones difficiles d’accès.
Conclusion
La maintenance autonome représente une avancée significative dans le domaine de la gestion industrielle. En responsabilisant les opérateurs, elle permet non seulement de prolonger la durée de vie des équipements, mais aussi de réduire les coûts de maintenance et d’améliorer la productivité. Cependant, sa mise en œuvre nécessite une formation adéquate et un suivi rigoureux pour garantir son efficacité à long terme. Les entreprises qui adoptent cette approche ont tout à gagner en termes de performance et de compétitivité dans un environnement industriel de plus en plus exigeant.
Annexes
Ressources Supplémentaires : Augmentir, SafetyCulture.
Glossaire des Termes Techniques : TPM, GMAO, IoT, etc.