Dans le paysage industriel moderne, la maintenance technologique joue un rôle crucial pour assurer la pérennité et la compétitivité des entreprises. Elle ne se limite plus à la simple réparation des équipements défectueux, mais englobe désormais un ensemble de meilleures pratiques en maintenance technologique, visant à optimiser les performances, réduire les coûts et prolonger la durée de vie des actifs technologiques.
Table of Contents
Importance de la maintenance technologique
La maintenance technologique est devenue un pilier essentiel de la stratégie opérationnelle des entreprises. Elle permet non seulement de prévenir les pannes coûteuses, mais aussi d’améliorer la qualité des produits, d’augmenter la sécurité des travailleurs et de réduire l’impact environnemental des activités industrielles.
Définition et rôle dans l’industrie moderne
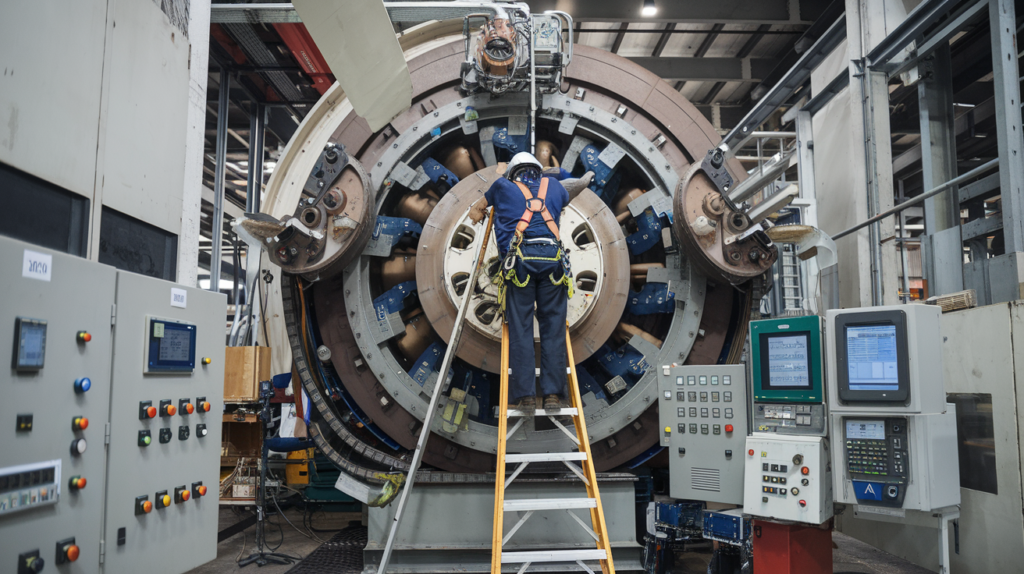
La maintenance technologique se définit comme l’ensemble des actions techniques, administratives et de gestion destinées à maintenir ou rétablir un équipement dans un état lui permettant d’accomplir sa fonction requise. Dans l’industrie moderne, elle s’étend à tous les domaines technologiques, des machines de production aux systèmes informatiques.
Impact sur la productivité et la rentabilité
Une maintenance efficace a un impact direct sur la productivité et la rentabilité des entreprises. Selon une étude menée par le cabinet Deloitte en 2023, les entreprises qui investissent dans des pratiques de maintenance avancées constatent une augmentation moyenne de 12% de leur productivité et une réduction de 18% des coûts opérationnels.
1. Comprendre le cycle de vie des équipements
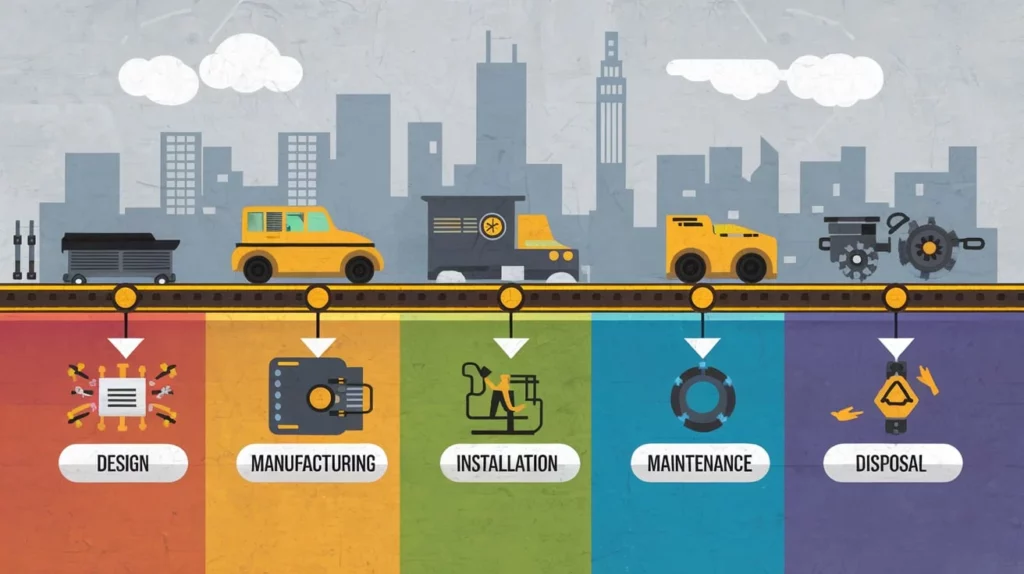
Pour mettre en place une stratégie de maintenance efficace, il est crucial de comprendre le cycle de vie complet des équipements technologiques.
Phases du cycle de vie
- Acquisition
La phase d’acquisition est le point de départ du cycle de vie d’un équipement. Elle comprend la sélection, l’achat et l’installation du matériel. Une attention particulière doit être portée aux spécifications techniques et à la compatibilité avec les systèmes existants.
- Utilisation
C’est la phase principale du cycle de vie, durant laquelle l’équipement remplit sa fonction. La performance et la fiabilité de l’équipement pendant cette phase dépendent grandement de la qualité de la maintenance effectuée.
- Maintenance
La maintenance intervient tout au long de la phase d’utilisation. Elle peut être préventive, corrective ou prédictive, selon les besoins et la nature de l’équipement.
- Fin de vie
Cette phase marque la fin de l’utilisation de l’équipement, soit par obsolescence, soit par usure. Elle implique le démantèlement, le recyclage ou la mise au rebut de l’équipement.
Évaluation des besoins en maintenance à chaque phase
À chaque phase du cycle de vie, les besoins en maintenance évoluent. Par exemple, pendant la phase d’acquisition, l’accent est mis sur la planification de la maintenance future. Durant la phase d’utilisation, les activités de maintenance préventive et corrective sont primordiales. En fin de vie, la maintenance se concentre sur la maximisation de la valeur résiduelle de l’équipement.
2. Établissement d’une stratégie de maintenance efficace
Une stratégie de maintenance bien conçue est essentielle pour optimiser la performance des équipements tout en minimisant les coûts.
Types de maintenance
Maintenance préventive
La maintenance préventive vise à réduire la probabilité de défaillance ou de dégradation d’un équipement. Elle est planifiée à intervalles réguliers, basés sur le temps ou l’utilisation.
Exemple réel : Toyota, leader mondial de l’industrie automobile, a mis en place un système de maintenance préventive appelé “Total Productive Maintenance” (TPM). Cette approche a permis à l’entreprise de réduire ses temps d’arrêt de production de 35% et d’augmenter sa productivité de 25% sur une période de trois ans.
Maintenance corrective
La maintenance corrective intervient après la détection d’une panne. Elle vise à remettre l’équipement en état de fonctionnement le plus rapidement possible.
Maintenance prédictive
La maintenance prédictive utilise des données en temps réel et des algorithmes d’apprentissage automatique pour prédire les défaillances avant qu’elles ne se produisent. Elle permet d’optimiser les interventions et de réduire les temps d’arrêt non planifiés.
Exemple réel : General Electric a développé un système de maintenance prédictive pour ses turbines à gaz utilisées dans les centrales électriques. Ce système, basé sur l’analyse de données en temps réel, a permis de réduire les temps d’arrêt imprévus de 5% et d’économiser environ 200 millions de dollars par an en coûts de maintenance.
Choix de la stratégie adaptée à l’équipement
Le choix de la stratégie de maintenance dépend de plusieurs facteurs,notamment:
- La criticité de l’équipement
- Le coût de remplacement
- Les conséquences d’une défaillance
- La disponibilité des pièces de rechange
- Les ressources humaines disponibles
Une approche hybride, combinant différents types de maintenance industrielle, est souvent la plus efficace pour optimiser les performances et les coûts.
3. Mise en œuvre des meilleures pratiques
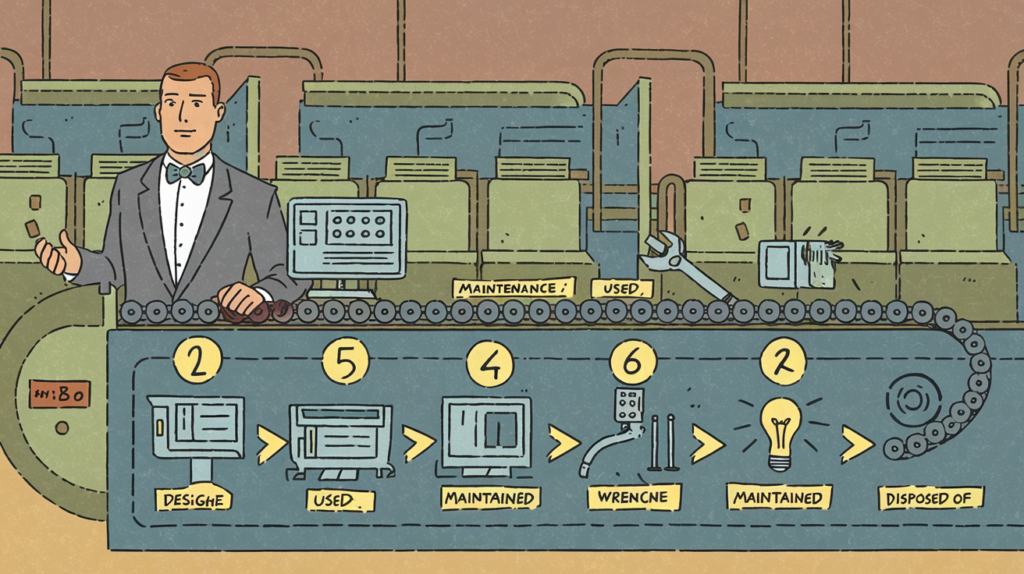
La mise en œuvre efficace des meilleures pratiques de maintenance technologique repose sur l’adoption de normes reconnues et la mise en place de procédures rigoureuses.
Normes et standards internationaux
ISO 55000 (Gestion des actifs)
La norme ISO 55000 fournit un cadre pour la gestion efficace des actifs physiques tout au long de leur cycle de vie. Elle met l’accent sur l’alignement des objectifs de maintenance avec les objectifs stratégiques de l’entreprise.
Exemple réel : Scottish Water, l’entreprise publique responsable de l’approvisionnement en eau en Écosse, a adopté la norme ISO 55000 pour sa gestion d’actifs. Cette mise en œuvre a permis à l’entreprise de réduire ses coûts opérationnels de 20% tout en améliorant la qualité de ses services.
Autres normes pertinentes
D’autres normes importantes incluent :
- ISO 14224 (Collecte et échange de données de fiabilité et de maintenance)
- EN 15341 (Indicateurs de performance clés pour la maintenance)
- IATF 16949 (Système de management de la qualité pour l’industrie automobile)
Documentation et procédures
Importance de la documentation précise
Une documentation précise et à jour est essentielle pour une maintenance efficace. Elle permet de :
- Standardiser les procédures
- Faciliter la formation des nouveaux employés
- Assurer la conformité réglementaire
- Améliorer la traçabilité des interventions
Exemples de procédures efficaces
- Procédure d’inspection quotidienne
- Protocole de maintenance préventive
- Processus de gestion des pièces de rechange
- Procédure d’analyse des causes racines en cas de panne
4. Utilisation des technologies modernes
L’intégration des technologies modernes dans les pratiques de maintenance offre de nouvelles opportunités pour améliorer l’efficacité et réduire les coûts.
Outils numériques pour la gestion de la maintenance
Logiciels de gestion de maintenance assistée par ordinateur (GMAO)
Les systèmes GMAO permettent de centraliser toutes les informations relatives à la maintenance, de planifier les interventions et de suivre les indicateurs de performance.
Exemple réel : La SNCF, la compagnie ferroviaire nationale française, a déployé un système GMAO pour gérer la maintenance de son parc de trains. Ce système a permis de réduire les retards liés à la maintenance de 30% et d’augmenter la disponibilité des trains de 15%.
Internet des objets (IoT) et capteurs intelligents
L’IoT permet de collecter des données en temps réel sur l’état des équipements, facilitant ainsi la mise en place de stratégies de maintenance prédictive.
Avantages des technologies émergentes
Réduction des coûts
L’utilisation de technologies avancées permet de réduire les coûts de maintenance en optimisant les interventions et en prolongeant la durée de vie des équipements.
Amélioration de la réactivité
Les technologies modernes permettent une détection plus rapide des anomalies et une intervention plus rapide, réduisant ainsi les temps d’arrêt.
5. Formation et développement des compétences
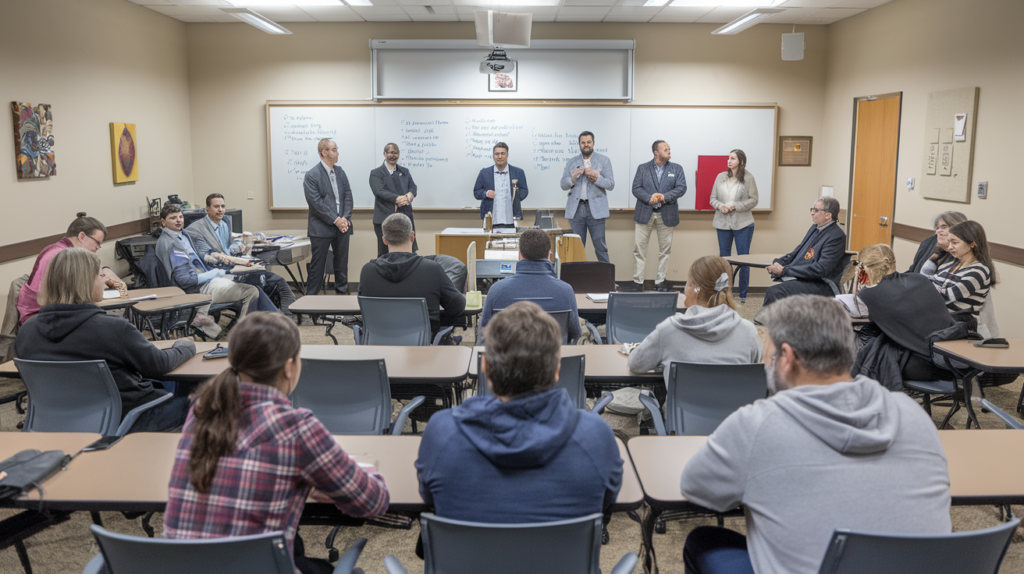
L’efficacité de la maintenance technologique repose en grande partie sur les compétences et l’engagement du personnel.
Importance de la formation continue
La formation continue est essentielle pour maintenir les compétences du personnel à jour face aux évolutions technologiques rapides. Elle permet également d’améliorer la sécurité et la qualité des interventions.
Programmes de formation recommandés
- Formation aux nouvelles technologies de maintenance
- Certification en gestion des actifs (par exemple, certification IAM)
- Formation à l’analyse des données pour la maintenance prédictive
- Cours sur les normes et réglementations en vigueur
Développement d’une culture de maintenance au sein de l’entreprise
La création d’une culture de maintenance implique :
- La sensibilisation de tous les employés à l’importance de la maintenance
- L’encouragement du partage des connaissances et des bonnes pratiques
- La reconnaissance des contributions individuelles à l’amélioration de la maintenance
Exemple réel : Procter & Gamble a mis en place un programme de formation appelé “Integrated Work Systems” (IWS) qui met l’accent sur l’implication de tous les employés dans la maintenance. Ce programme a permis à l’entreprise d’augmenter sa productivité de 20% et de réduire ses coûts de maintenance de 30%.
6. Analyse et amélioration continue
L’amélioration continue est un pilier essentiel des meilleures pratiques en maintenance technologique.
Indicateurs clés de performance (KPI)
Les KPI permettent de mesurer l’efficacité des pratiques de maintenance. Quelques exemples de KPI importants :
- Temps moyen entre les pannes (MTBF)
- Temps moyen de réparation (MTTR)
- Disponibilité des équipements
- Coût de maintenance par unité produite
Mesure de l’efficacité des pratiques de maintenance
La mesure régulière des KPI permet d’identifier les domaines d’amélioration et d’ajuster les stratégies de maintenance en conséquence.
Retour d’expérience et ajustements
Importance du feedback pour l’amélioration
Le retour d’expérience des techniciens de maintenance et des opérateurs est crucial pour identifier les problèmes récurrents et les opportunités d’amélioration.
Exemple réel : Airbus a mis en place un système de retour d’expérience appelé “Maintenance Error Decision Aid” (MEDA) pour analyser les erreurs de maintenance et améliorer ses processus. Ce système a permis de réduire les erreurs de maintenance de 50% sur une période de cinq ans.
Conclusion
Dans un environnement industriel en constante évolution, l’adoption de ces meilleures pratiques en maintenance technologique n’est plus une option, mais une nécessité. Les entreprises qui investissent dans l’optimisation de leurs processus de maintenance seront mieux positionnées pour relever les défis futurs, améliorer leur compétitivité et assurer leur croissance à long terme.
Il est temps pour chaque entreprise d’évaluer ses pratiques actuelles de maintenance technologique et d’élaborer un plan d’action pour les améliorer. Cela peut commencer par une analyse approfondie des processus existants, suivie de l’identification des domaines d’amélioration prioritaires. En mettant en œuvre progressivement ces meilleures pratiques, les entreprises peuvent s’attendre à des gains significatifs en termes d’efficacité opérationnelle, de réduction des coûts et d’amélioration de la qualité.
L’avenir appartient aux entreprises qui sauront tirer parti de ces meilleures pratiques pour transformer leur approche de la maintenance technologique en un véritable avantage concurrentiel.