Imaginez une usine en pleine production où une machine essentielle tombe soudainement en panne, paralysant toute la chaîne de production et entraînant des pertes financières massives. Ce type de scénario, autrefois considéré comme inévitable, peut désormais être évité grâce aux avancées en maintenance industrielle, un ensemble de pratiques visant à assurer le bon fonctionnement des équipements au sein des entreprises.
Aujourd’hui, les outils technologiques en maintenance révolutionnent ce domaine, transformant la manière dont les entreprises gèrent leurs actifs en améliorant l’efficacité, en réduisant les coûts et en augmentant la fiabilité des équipements. Cette évolution n’est pas seulement une amélioration, mais une véritable révolution qui redéfinit les standards de l’industrie. Découvrez comment ces innovations façonnent l’avenir de la maintenance industrielle et pourquoi elles sont essentielles pour toute entreprise cherchant à rester compétitive.
Table of Contents
Partie 1 : L’Évolution de la Maintenance Industrielle
De la Maintenance Corrective à la Maintenance Prédictive
Évolution Historique des Pratiques de Maintenance
Au cours des dernières décennies, la maintenance industrielle a considérablement évolué. Historiquement, les entreprises adoptaient une approche réactive, où l’on attendait qu’un équipement tombe en panne avant d’intervenir. Cette méthode, connue sous le nom de maintenance corrective, entraînait des temps d’arrêt imprévus et des coûts élevés.
Les Limites de la Maintenance Corrective et Préventive
La maintenance corrective, bien qu’indispensable dans certaines situations, posait de nombreux défis, notamment en termes de coûts imprévus et d’interruptions de production. Pour pallier ces problèmes, la maintenance préventive a été introduite, basée sur des calendriers d’entretien réguliers. Cependant, cette méthode avait aussi ses limites, car elle ne prenait pas en compte l’état réel des équipements, ce qui pouvait conduire à des interventions inutiles ou à des pannes non anticipées.
L’Émergence de la Maintenance Prédictive
C’est dans ce contexte que la maintenance prédictive a émergé, révolutionnant le secteur. En utilisant des capteurs avancés et des algorithmes d’analyse de données, les entreprises peuvent désormais anticiper les pannes avant qu’elles ne surviennent. Cette méthode permet non seulement de réduire les temps d’arrêt, mais aussi d’optimiser les coûts en intervenant uniquement lorsque cela est nécessaire, basant les décisions sur l’état réel des équipements.
Statistique Clé : Selon une étude de Gartner, les entreprises qui adoptent la maintenance prédictive réduisent en moyenne de 25 % leurs coûts de maintenance et augmentent la durée de vie de leurs équipements de 20 %.
Partie 2 : Les Principaux Outils Technologiques en Maintenance
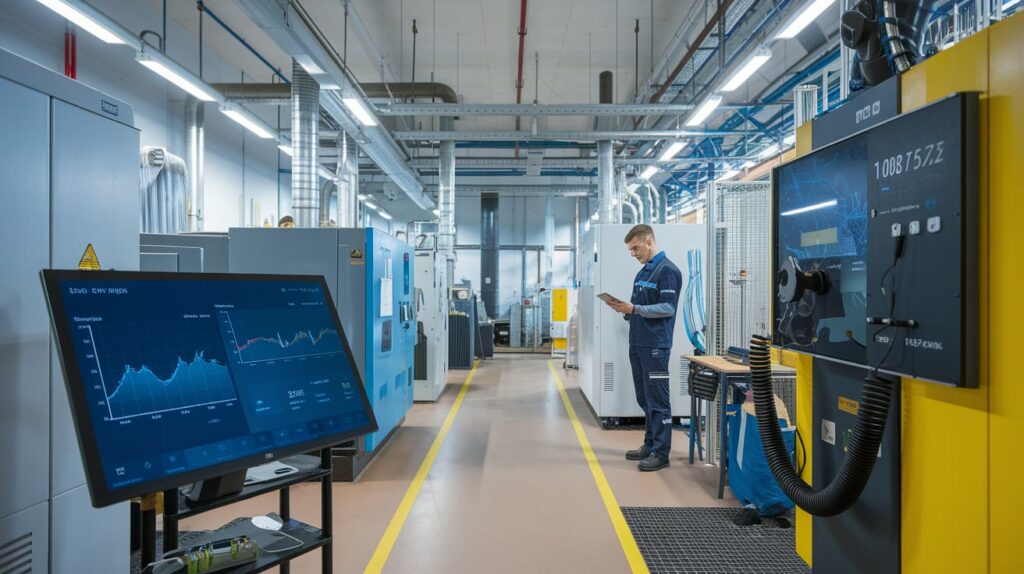
Les GMAO (Gestion de la Maintenance Assistée par Ordinateur)
Fonctionnalités Clés : Planification, Suivi des Interventions, Gestion des Stocks
Les systèmes GMAO sont aujourd’hui incontournables dans la gestion de la maintenance industrielle. Ils offrent une large gamme de fonctionnalités, telles que la planification des interventions, le suivi des réparations en temps réel, et la gestion des stocks de pièces détachées. Par exemple, une GMAO peut anticiper les besoins en pièces et éviter les ruptures de stock, garantissant ainsi la continuité des opérations.
Choix d’une GMAO Adaptée
Le choix d’une GMAO doit être adapté aux besoins spécifiques de l’entreprise. Il est essentiel de tenir compte de la taille de l’entreprise, de la complexité des équipements, et des fonctionnalités requises. Par exemple, une petite entreprise avec des besoins simples pourrait opter pour une GMAO facile à utiliser, tandis qu’une grande entreprise avec des besoins complexes pourrait nécessiter une solution plus robuste avec des capacités avancées d’analyse de données.
Étude de Cas : SKF, un leader mondial dans les solutions d’ingénierie, a déployé une GMAO avancée pour suivre en temps réel l’état de plus de 10 000 machines dans ses usines à travers le monde, réduisant ainsi les temps d’arrêt de 30 %.
L’IoT (Internet des Objets) dans la Maintenance
Capteurs Connectés pour la Collecte de Données
L’Internet des Objets (IoT) transforme la manière dont les données sont collectées et utilisées en maintenance industrielle. Les capteurs IoT installés sur les équipements permettent de surveiller en temps réel leur état de fonctionnement. Ces capteurs mesurent divers paramètres tels que les vibrations, la température, et l’humidité, et transmettent ces données à un système central pour analyse.
Applications : Surveillance de l’État des Équipements, Détection des Anomalies
Grâce à l’IoT, il est possible de surveiller en permanence l’état des équipements et de détecter rapidement les anomalies. Par exemple, si un capteur détecte une température anormale dans un moteur, une alerte est immédiatement envoyée aux techniciens, permettant une intervention rapide avant que le problème ne s’aggrave.
Citation d’Expert : “L’IoT n’est pas seulement un ajout technologique, c’est un catalyseur de transformation pour la maintenance industrielle,” déclare John Smith, CTO chez Tech Innovations.
L’Intelligence Artificielle et le Machine Learning
Analyse Prédictive des Données
L’intelligence artificielle (IA) et le machine learning jouent un rôle crucial dans l’analyse des données collectées par les capteurs IoT. Ces technologies permettent d’identifier des tendances et des modèles dans les données, prédisant ainsi les pannes potentielles. Par exemple, un algorithme de machine learning peut analyser les données de vibrations d’un équipement et prévoir une défaillance imminente.
Optimisation des Plans de Maintenance
L’IA permet également d’optimiser les plans de maintenance en ajustant les interventions en fonction des prévisions. Cette approche permet non seulement de réduire les coûts, mais aussi d’améliorer la disponibilité des équipements. Les entreprises peuvent ainsi passer d’une maintenance planifiée à une maintenance entièrement prédictive.
Statistique Clé : Selon McKinsey & Company, l’intégration de l’IA dans la maintenance prédictive peut réduire les coûts d’intervention de 10 à 15 %.
La Réalité Augmentée et Virtuelle
Assistance à Distance des Techniciens
La réalité augmentée (RA) et la réalité virtuelle (RV) offrent des outils puissants pour l’assistance à distance. Les techniciens peuvent utiliser des lunettes de RA pour visualiser les instructions de réparation superposées directement sur les équipements, tandis que les experts à distance peuvent guider les interventions en temps réel.
Formation et Simulation
La RV est également utilisée pour la formation des techniciens. Grâce à des simulations immersives, les techniciens peuvent s’entraîner sur des équipements virtuels, acquérant ainsi des compétences sans risquer d’endommager des machines réelles. Cette méthode est particulièrement utile pour les équipements complexes ou coûteux.
Étude de Cas : Siemens utilise la réalité augmentée pour former ses techniciens dans des environnements virtuels, réduisant les coûts de formation de 20 % et améliorant la rétention des connaissances de 30 %.
Partie 3 : Les Bénéfices de l’Utilisation des Outils Technologiques en Maintenance
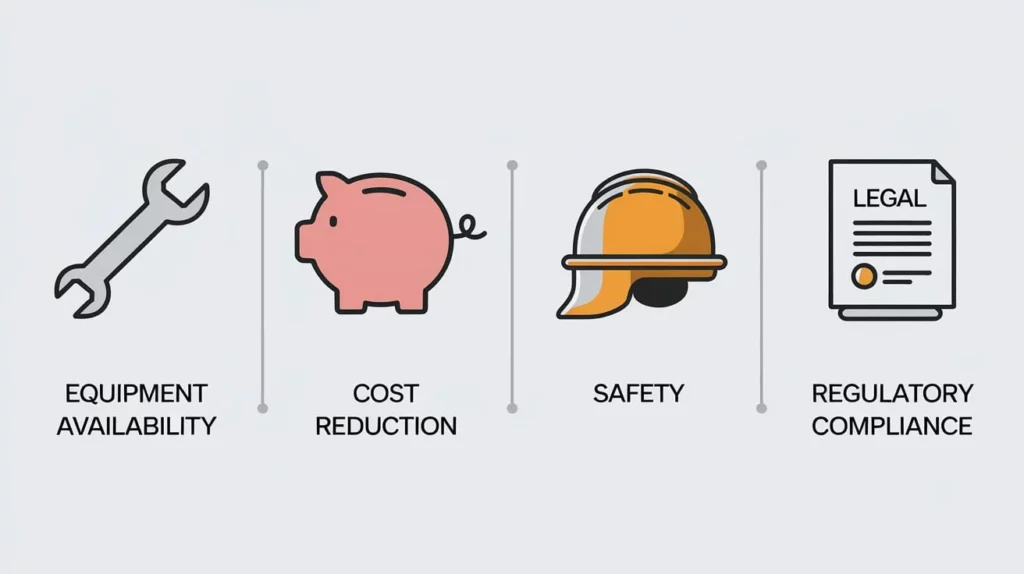
Amélioration de la Disponibilité des Équipements
Réduction des Temps d’Arrêt
L’utilisation des outils technologiques en maintenance permet de réduire significativement les temps d’arrêt des équipements. Par exemple, la maintenance prédictive, en anticipant les pannes, permet de planifier les interventions de manière à minimiser les interruptions de production.
Augmentation de la Durée de Vie des Actifs
En surveillant constamment l’état des équipements et en intervenant de manière proactive, il est possible d’augmenter la durée de vie des actifs industriels. Les entreprises peuvent ainsi retarder les investissements dans de nouveaux équipements, tout en maintenant une performance optimale.
Statistique Clé : D’après une étude de PwC, les entreprises qui adoptent la maintenance prédictive peuvent prolonger la durée de vie de leurs actifs jusqu’à 20 %.
Optimisation des Coûts
Réduction des Coûts de Maintenance
Les Outils technologiques en maintenance permettent de réduire les coûts de maintenance en évitant les réparations inutiles et en optimisant les interventions. Par exemple, une GMAO peut aider à planifier les interventions de manière à réduire les coûts de main-d’œuvre et les dépenses en pièces détachées.
Meilleure Gestion des Stocks
La gestion des stocks de pièces détachées est également optimisée grâce aux Outils technologiques en maintenance. En suivant en temps réel l’utilisation des pièces, les entreprises peuvent éviter les surstocks ou les ruptures, réduisant ainsi les coûts associés au stockage et à l’indisponibilité des pièces.
Amélioration de la Sécurité
Détection Précoce des Risques
Les technologies telles que l’IoT et l’IA permettent de détecter précocement les risques liés aux équipements, réduisant ainsi le nombre d’accidents du travail. Par exemple, un capteur IoT peut détecter une surchauffe dans un équipement, déclenchant une alerte avant qu’un incendie ne se produise.
Réduction des Accidents du Travail
En réduisant les risques d’accidents par une surveillance constante et des interventions rapides, les outils technologiques Outils technologiques en maintenance contribuent à améliorer la sécurité des employés. Les entreprises peuvent ainsi réduire les coûts associés aux accidents et améliorer leur réputation en matière de sécurité.
Citation d’Expert : “Les technologies de surveillance en temps réel sont essentielles pour prévenir les incidents avant qu’ils ne se transforment en catastrophes,” affirme Lisa Williams, experte en sécurité industrielle chez SafeTech.
Prise de Décision Plus Éclairée
Données Fiables pour une Meilleure Planification
Les données collectées et analysées par les Outils technologiques en maintenance fournissent une base solide pour la prise de décisions stratégiques. Les managers peuvent utiliser ces informations pour planifier les interventions, optimiser l’utilisation des ressources, et améliorer la performance globale de l’entreprise.
Optimisation des Ressources
Grâce à une meilleure visibilité sur l’état des équipements et les besoins en maintenance, les entreprises peuvent optimiser l’allocation des ressources, réduisant ainsi les gaspillages et augmentant l’efficacité opérationnelle.
Partie 4 : Cas d’Utilisation et Exemples Concrets
Dans l’Industrie Manufacturière
Maintenance Prédictive sur les Lignes de Production
Dans l’industrie manufacturière, la maintenance prédictive est utilisée pour surveiller les lignes de production et prévenir les pannes. Par exemple, une entreprise automobile peut utiliser des capteurs pour surveiller en temps réel l’état des robots de soudage, évitant ainsi les interruptions de production.
Optimisation de la Maintenance des Outillages
L’utilisation des Outils technologiques en maintenance permet également d’optimiser la maintenance des outillages, réduisant ainsi les coûts de réparation et les temps d’arrêt. Les entreprises peuvent ainsi maximiser la disponibilité des équipements et améliorer leur productivité.
Dans le Secteur de l’Énergie
Surveillance des Éoliennes
Dans le secteur de l’énergie, l’IoT et l’IA sont utilisés pour surveiller les éoliennes et détecter les anomalies avant qu’elles ne causent des pannes. Par exemple, des capteurs installés sur les pales des éoliennes peuvent détecter des vibrations anormales, permettant une intervention rapide.
Maintenance Prédictive des Réseaux Électriques
Les technologies de maintenance prédictive sont également appliquées aux réseaux électriques pour prévenir les pannes et optimiser la distribution d’énergie. Par exemple, les opérateurs de réseau utilisent l’IA pour analyser les données des capteurs et prédire les pannes de transformateurs.
Dans le Secteur du Transport
Maintenance Prédictive des Trains et des Avions
Dans le secteur du transport, la maintenance prédictive est essentielle pour garantir la sécurité et la fiabilité des moyens de transport. Par exemple, les compagnies aériennes utilisent des capteurs IoT pour surveiller en temps réel l’état des moteurs d’avion, permettant de prévenir les pannes en vol.
Statistique Clé : Selon Airbus, l’utilisation de la maintenance prédictive a permis de réduire de 30 % les coûts de maintenance des avions et d’améliorer leur disponibilité opérationnelle de 20 %.
Partie 5 : Les Défis et les Perspectives
Les Défis de l’Implémentation
Coûts d’Investissement
L’implémentation des outils technologiques en maintenance nécessite des investissements initiaux importants. Cependant, ces coûts sont souvent compensés par les économies réalisées à long terme grâce à l’optimisation des interventions et la réduction des temps d’arrêt.
Qualité des Données
La qualité des données collectées est cruciale pour le succès de la maintenance prédictive. Des données incomplètes ou incorrectes peuvent mener à des prédictions erronées, compromettant ainsi l’efficacité des interventions.
Résistance au Changement
L’introduction de nouvelles technologies en maintenance peut rencontrer de la résistance de la part des employés. Il est important de prévoir des programmes de formation et de sensibilisation pour faciliter l’adoption de ces outils.
L’Avenir de la Maintenance Industrielle
Intégration des Jumeaux Numériques
Les jumeaux numériques, qui sont des répliques virtuelles des équipements physiques, joueront un rôle de plus en plus important dans la maintenance industrielle. Ils permettront de simuler et de tester les interventions avant de les appliquer sur les équipements réels, réduisant ainsi les risques et optimisant les performances.
Développement de l’Intelligence Artificielle Explicable
L’IA explicable, qui permet de comprendre et d’interpréter les décisions prises par les algorithmes, sera essentielle pour renforcer la confiance dans les systèmes de maintenance prédictive. Cette transparence permettra aux entreprises de mieux gérer leurs opérations et d’améliorer la prise de décision.
Collaboration Homme-Machine
L’avenir de la maintenance industrielle verra une collaboration accrue entre les hommes et les machines. Les technologies telles que la réalité augmentée et l’intelligence artificielle permettront aux techniciens de travailler plus efficacement, en s’appuyant sur les recommandations des systèmes automatisés.
Conclusion
Les Outils technologiques en maintenance transforment la maintenance industrielle en apportant une efficacité accrue, une réduction des coûts et une fiabilité améliorée des équipements. De la GMAO à l’IoT, en passant par l’IA et la réalité augmentée, ces innovations ne sont plus un simple avantage compétitif mais une nécessité pour toute entreprise souhaitant optimiser ses opérations et rester en tête de son secteur.
L’adoption de ces technologies est un investissement stratégique qui non seulement réduit les risques, mais assure également une gestion plus proactive et éclairée des actifs industriels. Pour les entreprises prêtes à embrasser cette transformation, l’avenir s’annonce prometteur, marqué par une collaboration homme-machine toujours plus étroite et des innovations comme les jumeaux numériques qui redéfiniront encore davantage les pratiques de maintenance. Il est donc temps d’agir et de se positionner en pionnier dans cette nouvelle ère de la maintenance industrielle.
Sources
- Gartner : Statistiques sur la Maintenance Prédictive
https://www.gartner.com - SKF : Étude de Cas sur l’Implémentation d’une GMAO
https://www.skf.com - McKinsey & Company : Avantages de l’IA dans la Maintenance
https://www.mckinsey.com - Siemens : Utilisation de la Réalité Augmentée
https://www.siemens.com - PwC : Statistiques sur la Durée de Vie des Actifs
https://www.pwc.com - SafeTech : Expert en Sécurité Industrielle
https://www.safetech.com - Airbus : Statistiques sur la Maintenance Prédictive
https://www.airbus.com