Un plan de maintenance efficace est un élément essentiel pour garantir la durabilité, la fiabilité et la performance optimale des équipements industriels. Que ce soit dans l’industrie manufacturière, les infrastructures publiques ou les services de santé, une stratégie bien conçue permet de minimiser les coûts, d’améliorer la sécurité et d’augmenter la productivité. Dans cet article, nous allons explorer en profondeur les étapes, les outils et les meilleures pratiques pour créer un plan de maintenance performant.
Table of Contents
1. Qu’est-ce qu’un plan de maintenance ?
Un plan de maintenance est un document stratégique qui définit les actions nécessaires pour garantir la continuité et la fiabilité du fonctionnement des équipements, machines et infrastructures d’une organisation. Il s’agit d’un outil essentiel pour optimiser la performance des actifs, réduire les coûts d’exploitation et prévenir les interruptions non planifiées. Voici les principaux éléments qu’il englobe :
- Les tâches de maintenance préventive : Ce type de maintenance vise à éviter les pannes en planifiant des actions régulières comme l’inspection des équipements, le nettoyage, le graissage, ou encore le remplacement des pièces susceptibles de s’user avec le temps. Par exemple, dans une usine, cela pourrait inclure la vérification mensuelle des courroies de transmission ou le remplacement programmé des filtres à air.
- Les interventions correctives : Ces interventions sont réalisées lorsque des pannes ou dysfonctionnements imprévus surviennent. Elles nécessitent une réparation immédiate pour limiter les arrêts de production. Par exemple, le remplacement d’un moteur défectueux dans une chaîne de production suite à une panne soudaine.
- La maintenance prédictive : Grâce aux technologies modernes, ce type de maintenance repose sur des données collectées en temps réel via des capteurs ou des logiciels spécialisés. Ces données permettent de prévoir les défaillances potentielles avant qu’elles ne surviennent. Par exemple, une entreprise peut surveiller la température et les vibrations d’un roulement pour détecter une anomalie avant qu’elle ne provoque une panne.
Un plan de maintenance efficace repose sur une approche méthodique, intégrant une analyse approfondie des besoins spécifiques de l’organisation, des caractéristiques des équipements, et des objectifs de performance. Il doit également inclure un calendrier clair et des responsabilités bien définies pour chaque tâche. En outre, l’utilisation d’outils numériques, tels que les logiciels de GMAO (Gestion de Maintenance Assistée par Ordinateur), peut considérablement améliorer la planification et le suivi des actions de maintenance.
2. Pourquoi est-il important d’avoir un plan de maintenance ?
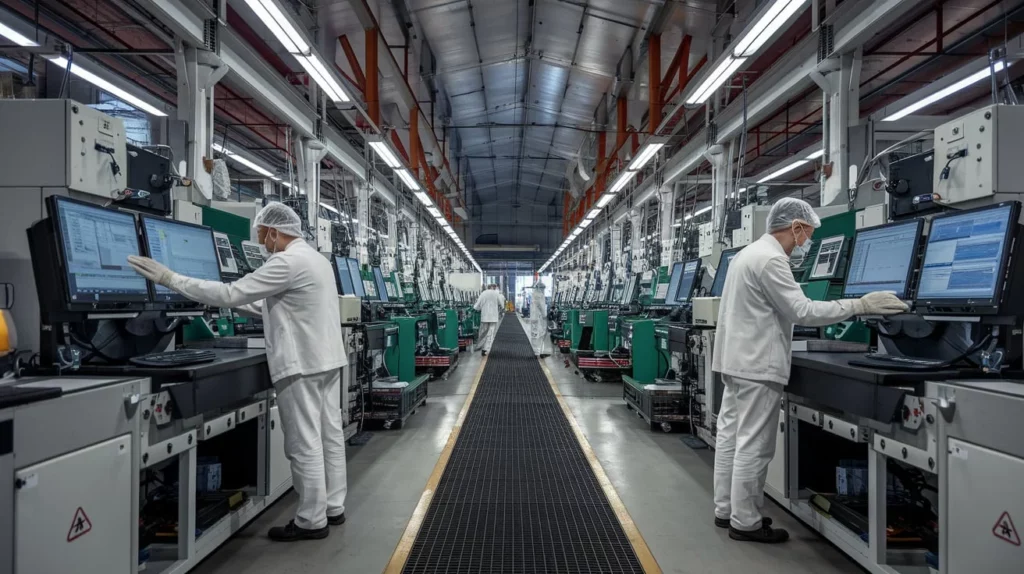
Voici quelques raisons clés :
- Réduction des temps d’arrêt : Une bonne planification permet d’éviter les pannes inattendues en identifiant et en résolvant les problèmes potentiels avant qu’ils ne deviennent critiques. Par exemple, une usine automobile qui effectue des contrôles réguliers sur ses chaînes d’assemblage peut minimiser les interruptions de production.
- Allongement de la durée de vie des équipements : En effectuant des entretiens réguliers, les machines restent en bon état, ce qui prolonge leur durée de vie. Par exemple, dans le secteur agricole, un entretien préventif des tracteurs et des équipements de récolte réduit leur usure prématurée et améliore leur efficacité.
- Sécurité accrue : Des inspections régulières permettent d’identifier les risques potentiels pour les employés et l’environnement, garantissant ainsi un lieu de travail plus sûr. Par exemple, des inspections fréquentes des systèmes électriques dans une usine chimique réduisent les risques d’incendie ou d’explosion.
- Optimisation des coûts : Les interventions planifiées sont généralement moins coûteuses que les réparations d’urgence. En effet, les pannes imprévues nécessitent souvent des interventions rapides et coûteuses. Par exemple, une entreprise textile qui a mis en place un plan de maintenance préventive a réduit ses coûts d’entretien de 30 % en deux ans en évitant les réparations d’urgence coûteuses.
Ces avantages montrent que l’élaboration d’un plan de maintenance bien structuré est une étape essentielle pour toute organisation souhaitant maximiser la performance de ses équipements et réduire ses coûts opérationnels.
3. Étapes pour élaborer un plan de maintenance efficace
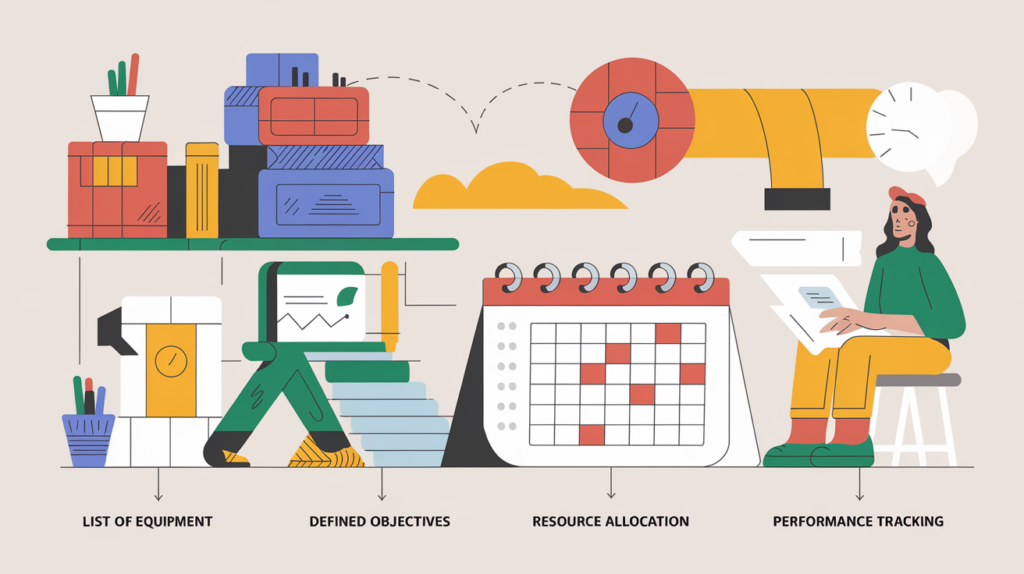
3.1. Identifier les équipements critiques
Commencez par dresser une liste complète de vos équipements. Cette étape est essentielle pour identifier les priorités et élaborer un plan de maintenance adapté. Classez les équipements en fonction de leur criticité en tenant compte des critères suivants :
- Impact sur la production : Analysez si une panne de cet équipement arrête complètement ou partiellement la production. Par exemple, dans une ligne de production agroalimentaire, une panne du convoyeur principal peut interrompre toute la chaîne.
- Fréquence des pannes : Identifiez les équipements sujets à des défaillances fréquentes. Ces données peuvent être collectées via des historiques de maintenance ou des rapports d’interventions précédentes. Par exemple, un compresseur d’air utilisé en continu dans une usine chimique peut présenter des pannes régulières si son entretien est négligé.
- Coût de remplacement ou de réparation : Évaluez si l’équipement est coûteux à réparer ou à remplacer. Les machines spécialisées, comme les robots industriels, nécessitent souvent des interventions coûteuses et des pièces difficiles à obtenir.
Exemple concret : Dans une centrale électrique, les turbines sont des équipements critiques, car leur panne peut provoquer un arrêt complet de la production d’énergie. Un programme de maintenance préventive sur ces turbines, incluant des inspections régulières et le remplacement anticipé des pièces usées, peut éviter des interruptions coûteuses.
Cette classification vous aidera à hiérarchiser les actions de maintenance et à allouer efficacement vos ressources.
3.2. Définir les objectifs du plan
Posez des objectifs clairs, réalistes et mesurables afin de guider efficacement votre plan de maintenance. Ces objectifs doivent être adaptés aux besoins spécifiques de votre organisation et alignés sur vos priorités stratégiques. Voici quelques exemples :
- Réduire les temps d’arrêt de 20 % d’ici la fin de l’année : Cela peut être réalisé en identifiant les causes principales des interruptions et en mettant en place des actions correctives ciblées.
- Augmenter la fiabilité des équipements de 15 % : Utilisez des indicateurs comme le MTBF (Mean Time Between Failures) pour suivre l’évolution de la fiabilité de vos équipements après l’implémentation du plan.
- Réduire les coûts de maintenance de 10 % : Analysez les données historiques pour identifier les interventions coûteuses et priorisez les actions préventives pour éviter des réparations imprévues.
Exemple concret : Une entreprise de production pharmaceutique a réduit ses temps d’arrêt de 25 % en adoptant une approche axée sur la maintenance préventive, notamment grâce à des inspections mensuelles systématiques.
3.3. Créer un calendrier de maintenance
Établissez un planning détaillé pour structurer et anticiper les interventions de maintenance. Ce calendrier doit inclure :
- Les inspections périodiques : Planifiez des vérifications régulières pour identifier les problèmes potentiels avant qu’ils ne deviennent critiques.
- Les remplacements préventifs de pièces : Anticipez les défaillances en remplaçant les pièces avant qu’elles n’atteignent leur limite d’usure. Par exemple, le remplacement des roulements dans une machine de production tous les six mois.
- Les évaluations des performances des équipements : Intégrez des contrôles réguliers pour mesurer l’efficacité des machines, comme le suivi des consommations énergétiques ou des taux de production.
Outil recommandé : Utilisez un logiciel de GMAO (Gestion de Maintenance Assistée par Ordinateur) pour automatiser le suivi et la planification des interventions. Ces outils permettent de centraliser les données, de générer des alertes automatiques et d’améliorer la coordination entre les équipes.
Un calendrier bien conçu garantit une exécution efficace et évite les oublis, tout en maximisant la disponibilité des équipements.
3.4. Allouer les ressources nécessaires
Une planification réussie nécessite une allocation judicieuse des ressources humaines, matérielles et financières. Voici les étapes clés pour garantir une mise en œuvre efficace :
- Identifier les compétences requises : Analysez les besoins spécifiques pour chaque type d’intervention. Par exemple, la maintenance d’un équipement complexe comme un robot industriel peut nécessiter des techniciens spécialisés.
- Former les équipes : Assurez-vous que vos techniciens disposent des connaissances nécessaires en proposant des formations régulières sur les nouvelles technologies et les meilleures pratiques de maintenance.
- Stocker les pièces de rechange essentielles : Maintenez un inventaire des pièces critiques pour éviter les retards lors des réparations. Par exemple, une usine de production alimentaire peut conserver en stock des courroies et des roulements pour ses convoyeurs.
- Utiliser les bons outils : Investissez dans des équipements adaptés pour faciliter les interventions. Cela inclut les outils mécaniques, électriques ou encore des appareils de diagnostic comme les analyseurs vibratoires.
3.5. Suivre et évaluer les performances
La mise en place d’un suivi régulier permet d’ajuster le plan de maintenance pour atteindre les objectifs fixés. Utilisez des KPI (Indicateurs Clés de Performance) pour mesurer l’efficacité des actions :
- MTBF (Mean Time Between Failures) : Cet indicateur mesure la fiabilité des équipements en calculant le temps moyen entre deux pannes successives. Une augmentation du MTBF indique une meilleure performance.
- MTTR (Mean Time to Repair) : Il mesure le temps moyen nécessaire pour réparer un équipement. Une diminution du MTTR reflète une amélioration de l’efficacité des équipes de maintenance.
- Taux de disponibilité des équipements : Ce pourcentage indique le temps pendant lequel une machine est opérationnelle par rapport au temps total. Par exemple, une disponibilité de 95 % dans une ligne de production automobile est souvent un objectif minimal.
Exemple concret : Une entreprise pétrochimique a utilisé le MTBF et le MTTR pour identifier les équipements problématiques, ce qui a permis de réduire les pannes de 30 % en un an.
Ces indicateurs, associés à un suivi régulier, garantissent une optimisation continue du plan de maintenance et un retour sur investissement accru.
4. Outils pour optimiser votre plan de maintenance
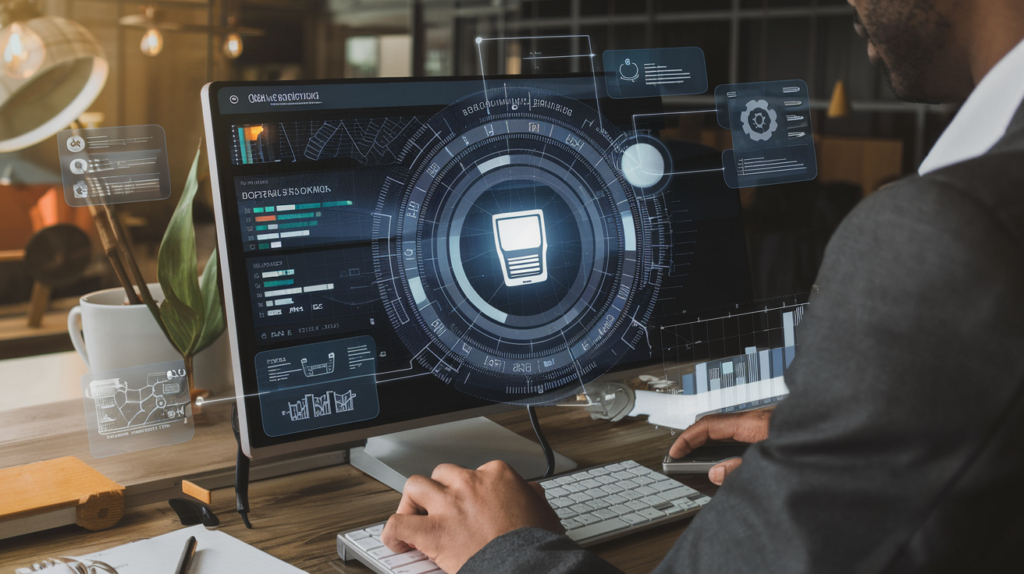
4.1. Logiciels de GMAO
Les logiciels de Gestion de Maintenance Assistée par Ordinateur (GMAO) sont des outils indispensables pour structurer et automatiser votre plan de maintenance. Ils permettent de :
- Planifier les interventions : Les logiciels comme Fiix ou UpKeep facilitent la création de calendriers détaillés pour les tâches préventives et correctives.
- Gérer les stocks de pièces de rechange : Ces outils assurent une visibilité en temps réel sur les niveaux de stock, évitant les ruptures.
- Suivre l’historique des maintenances : L’historique complet des interventions aide à comprendre les défaillances récurrentes et à ajuster le plan.
Exemple concret : Une entreprise agroalimentaire utilisant Fiix a pu réduire ses coûts de maintenance de 15 % en optimisant ses stocks et en planifiant mieux ses interventions.
4.2. Capteurs IoT
Les capteurs connectés (IoT) jouent un rôle clé dans la maintenance prédictive en collectant des données en temps réel sur l’état des équipements. Ces données permettent d’intervenir avant qu’une panne ne survienne.
- Surveillance des paramètres critiques : Les capteurs mesurent des variables comme la température, les vibrations, ou la pression.
- Anticipation des pannes : En détectant des anomalies, les équipes peuvent agir préventivement.
Exemple : Une usine automobile utilise des capteurs IoT pour surveiller les vibrations et la température des machines. Grâce à ces données, elle a réduit les pannes imprévues de 25 %.
4.3. Analyse des données
L’analyse des données historiques et en temps réel est essentielle pour optimiser les performances des équipements et prévenir les problèmes.
- Identifier les tendances : L’analyse permet de repérer des schémas récurrents dans les pannes ou les défaillances.
- Prédire les besoins de maintenance : Les algorithmes avancés peuvent prévoir les moments où une intervention sera nécessaire.
Exemple concret : Une entreprise de production d’énergie a analysé les données de ses turbines et a réduit ses coûts de maintenance de 20 % grâce à une meilleure planification.
En combinant ces outils, vous pouvez transformer votre plan de maintenance en un système hautement efficace et réactif.
5. Bonnes pratiques pour un plan de maintenance réussi
5.1. Impliquer toutes les parties prenantes
La réussite d’un plan de maintenance repose sur une collaboration étroite entre tous les acteurs concernés :
- Les opérateurs : Leur connaissance quotidienne des équipements est précieuse pour identifier les problèmes potentiels.
- Les techniciens : Ils apportent leur expertise technique pour planifier et exécuter les interventions.
- Les gestionnaires : Ils s’assurent que les ressources nécessaires (budget, outils, personnel) sont disponibles et optimisées.
Exemple concret : Une usine 5.1. Impliquer toutes les parties prenantes
La réussite d’un plan pharmaceutique a mis en place des réunions hebdomadaires entre opérateurs et techniciens pour échanger sur les performances des équipements. Cette approche a permis de réduire les temps d’arrêt de 18 %.
5.2. Former régulièrement les équipes
La formation continue est essentielle pour maintenir un haut niveau de compétence et s’adapter aux nouvelles technologies :
- Sessions de formation technique : Pour maîtriser les nouvelles machines ou outils de diagnostic.
- Ateliers sur les logiciels de GMAO : Pour utiliser efficacement les outils numériques.
- Simulations de pannes : Pour améliorer la réactivité face aux imprévus.
5.3. Mettre à jour le plan régulièrement
Un plan de maintenance n’est pas figé. Il doit évoluer pour rester pertinent :
- Intégrer les nouvelles technologies : Par exemple, ajouter des capteurs IoT ou adopter des outils d’analyse avancée.
- Analyser les retours d’expérience : Utilisez les données des interventions passées pour affiner le plan.
- Adapter aux nouveaux objectifs : Si les priorités de l’entreprise changent, le plan doit suivre.
En appliquant ces bonnes pratiques, votre plan de maintenance deviendra un outil stratégique pour optimiser les performances de vos équipements et garantir la continuité des opérations.
6. Conclusion
Élaborer un plan de maintenance efficace demande une analyse approfondie, une planification minutieuse et l’utilisation d’outils adaptés. En investissant dans un tel plan, vous garantissez la fiabilité et la longévité de vos équipements, tout en optimisant vos coûts et votre productivité.
Pour approfondir vos connaissances, consultez des ressources fiables comme Maintenance World ou SafetyCulture.