En 2025, chaque heure d’arrêt machine coûte en moyenne 18 000€ aux industries manufacturières, selon une étude de Deloitte. Pourtant, des entreprises de renommée mondiale comme Tesla ou L’Oréal ont réussi à réduire leurs temps d’indisponibilité de 60 % en digitalisant leur approche de la maintenance.
Mais comment ces géants ont-ils réussi cette transformation et comment d’autres industries peuvent elles passer d’une logique corrective à une maintenance proactive ?
Les pannes non planifiées représentent jusqu’à 20 % des coûts de production, un impact financier significatif pour les entreprises. Parmi les causes récurrentes des arrêts imprévus, on retrouve les défaillances mécaniques (30 % des cas, par exemple, les roulements usés) et les erreurs humaines (15 %, comme des mauvais réglages ou des oublis).
En outre, les enjeux réglementaires, comme la norme ISO 55000 qui exige une traçabilité complète des interventions, rendent la gestion de la maintenance encore plus complexe.
La clé de la réduction des temps d’arrêt maintenance réside dans l’adoption de technologies avancées comme les capteurs intelligents, les systèmes de gestion de maintenance assistée par ordinateur (GMAO) avec intelligence artificielle et les protocoles IoT standardisés.
Ces outils permettent non seulement de mieux comprendre l’état des équipements, mais aussi de prévenir les pannes avant qu’elles ne surviennent, transformant ainsi la maintenance industrielle en un processus proactif et beaucoup plus efficace.
Table of Contents
1. Les Causes des Temps d’Arrêt et Leur Impact
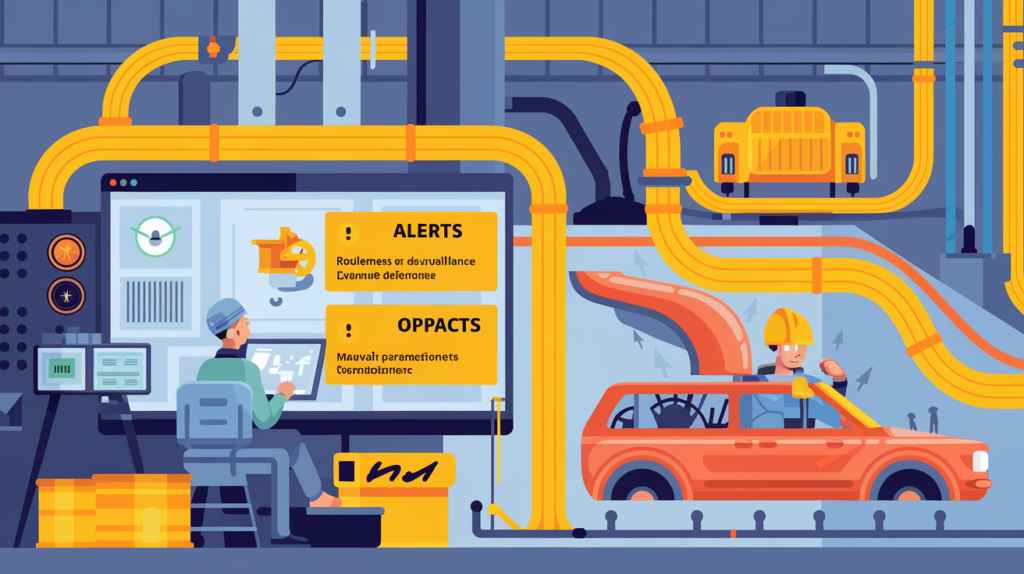
a. Analyse des Causes Racines
Les temps d’arrêt machine dans l’industrie sont principalement causés par des défaillances mécaniques et des erreurs opérationnelles, des facteurs qui affectent à la fois la performance et la rentabilité des entreprises.
Défaillances mécaniques :
L’usure des composants mécaniques est la principale cause des pannes dans de nombreuses industries. Par exemple, dans le secteur des pompes industrielles, 40 % des pannes sont dues à des roulements défectueux (SKF).
Ces défaillances entraînent des arrêts imprévus et des coûts de réparation élevés, mais aussi une dégradation des performances du matériel et de la productivité globale. Une panne de compresseur Atlas Copco dans une usine de production peut coûter jusqu’à 45 000€ en pièces de remplacement, en plus des 12 heures d’arrêt nécessaires à la réparation. Ce type de panne peut non seulement affecter la production, mais aussi compromettre les délais de livraison et l’engagement envers les clients.
Erreurs opérationnelles :
Les erreurs humaines sont également une source significative de temps d’arrêt. Les mauvais paramétrages des machines, tels que des températures incorrectes sur des fours industriels ou des erreurs dans les commandes de production, peuvent entraîner des dysfonctionnements graves.
Dans l’industrie de la métallurgie ou de la production de verre, par exemple, une erreur dans le réglage de la température d’un four peut endommager des lots entiers de produits, provoquant non seulement des pannes, mais aussi des pertes matérielles et des coûts de redémarrage élevés.
b. Coûts Directs et Indirects
Les coûts associés aux temps d’arrêt ne se limitent pas à la réparation ou à la perte de production immédiate. Ils englobent également des conséquences financières à long terme qui peuvent affecter la rentabilité de l’entreprise.
Perte de production :
Le coût des arrêts non planifiés peut être astronomique. Par exemple, dans une usine de montage automobile de Renault, un jour d’arrêt de la ligne de production peut entraîner une perte de 1,2 million d’euros en chiffre d’affaires.
Cela s’explique par la nature très fluide des chaînes de production automobile, où chaque minute d’arrêt perturbe toute la chaîne logistique, entraînant des retards et des coûts supplémentaires liés à la remise en marche des équipements.
Pénalités clients :
Les pénalités financières liées aux délais de livraison sont également un facteur non négligeable. Dans des secteurs tels que l’aéronautique, les retards peuvent avoir des conséquences juridiques et financières sérieuses.
Par exemple, des retards dans la livraison de pièces de moteurs peuvent entraîner des amendes pouvant atteindre 5 % du contrat total. Ces pénalités peuvent non seulement affecter la rentabilité d’un projet, mais aussi nuire à la relation avec le client et à la réputation de l’entreprise.
c. Données Sectorielles
Certaines industries sont particulièrement sensibles aux arrêts imprévus, avec des impacts financiers majeurs en cas de panne.
Secteur pharmaceutique :
Dans l’industrie pharmaceutique, les temps d’arrêt liés aux nettoyages CIP/SIP (Clean-In-Place/Sterilize-In-Place) non optimisés représentent jusqu’à 80 % des temps d’arrêt. Selon la FDA, des arrêts dus à des procédures de nettoyage inefficaces ou mal calibrées peuvent entraîner des perturbations de la production, des pertes financières considérables, et des risques pour la conformité réglementaire.
Un nettoyage inefficace non seulement allonge les temps d’arrêt, mais augmente également les risques de contamination croisée, affectant la qualité des produits fabriqués.
Secteur de l’énergie :
Dans le secteur énergétique, particulièrement pour des entreprises comme EDF, les turbines à gaz représentent une partie essentielle de la production d’énergie. Lorsque ces turbines sont à l’arrêt pour maintenance ou cause de panne, le coût peut être extrême.
Par exemple, un jour d’arrêt d’une turbine à gaz coûte 250 000€ à EDF, sans compter les effets sur l’approvisionnement en énergie. Ce coût est aggravé par la nécessité de maintenir un approvisionnement stable en électricité, ce qui augmente les pressions sur les autres générateurs et les coûts opérationnels globaux.
2. 5 Stratégies pour Réduction des temps d’arrêt maintenance en 2025
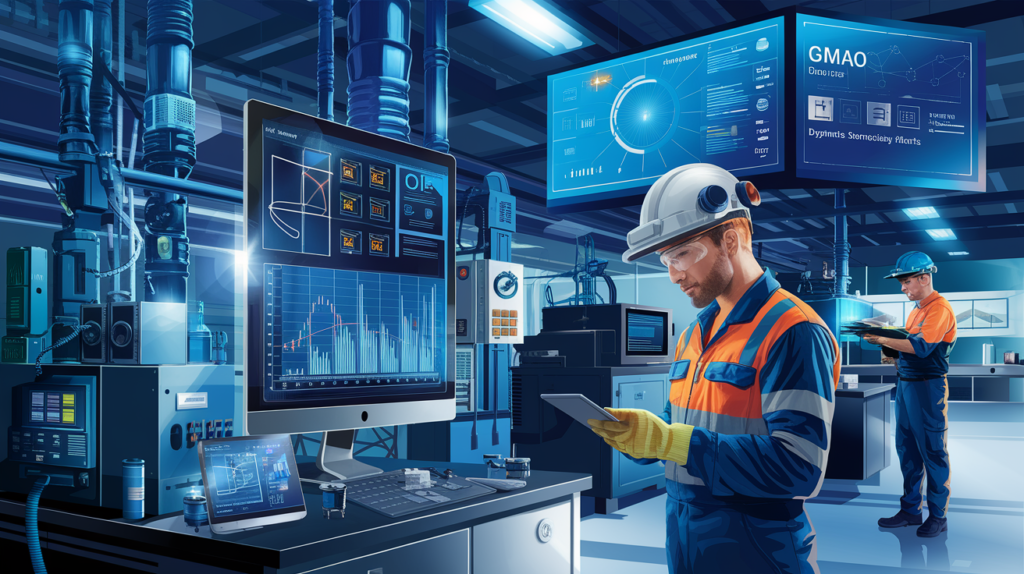
Les temps d’arrêt imprévus restent l’un des plus grands défis pour les entreprises industrielles. Heureusement, avec l’évolution des technologies et des stratégies modernes de maintenance, il existe plusieurs solutions qui permettent de réduire ces interruptions coûteuses. Voici cinq stratégies clés pour minimiser les temps d’arrêt en 2025.
a. Maintenance Prédictive via l’IA
La maintenance prédictive fait appel à des technologies avancées pour anticiper les pannes avant qu’elles ne surviennent. L’utilisation de l’intelligence artificielle (IA) et des capteurs intelligents permet de surveiller en continu l’état des équipements, afin de prévoir les défaillances et d’intervenir avant que des pannes majeures ne se produisent.
Technologies clés :
- Capteurs vibratoires : Par exemple, le modèle Emerson CSI 2140 utilise des capteurs vibratoires pour détecter des anomalies dans les machines. Ce système permet d’identifier des problèmes jusqu’à 72 heures avant la panne, donnant ainsi aux techniciens un temps précieux pour planifier une intervention.
- Algorithmes prédictifs : Les algorithmes comme Random Forest, utilisés dans le secteur de l’énergie par TotalEnergies, permettent de prédire les pannes avec une précision de 93% pour des équipements comme les pompes. Ces algorithmes analysent des données historiques et en temps réel pour identifier des patterns anormaux et ainsi prévenir les défaillances.
ROI : L’étude de Rockwell Automation montre que l’utilisation de la maintenance prédictive permet de réduire de 40% les pannes imprévues, entraînant une réduction significative des coûts d’arrêt et des maintenances non planifiées.
b. GMAO avec Planification Intelligente
Les logiciels de gestion de maintenance assistée par ordinateur (GMAO) jouent un rôle essentiel dans l’optimisation des interventions de maintenance. En combinant la GMAO avec des fonctionnalités intelligentes, les entreprises peuvent réduire les temps d’arrêt en planifiant mieux les interventions et en surveillant les équipements en temps réel.
Fonctionnalités indispensables :
- Calendriers dynamiques : Des systèmes comme IBM Maximo ajustent les plannings de maintenance en temps réel, en fonction de l’usure des machines. Ce processus garantit que la maintenance est effectuée uniquement lorsque nécessaire, et non de manière excessive ou trop tardive.
- Alertes automatisées : Les notifications push permettent d’alerter immédiatement les techniciens lorsque les seuils critiques (température, vibrations, pression, etc.) sont atteints. Ces alertes permettent des interventions immédiates avant qu’une panne ne se produise.
Exemple : Schneider Electric, en utilisant sa solution EcoStruxure, a réussi à réduire ses temps d’arrêt de 35% grâce à une gestion intelligente de ses équipements et à une planification proactive des tâches de maintenance.
c. Formation aux Outils Numériques
Les outils numériques, y compris la réalité virtuelle (VR), révolutionnent la formation des techniciens et permettent de réduire considérablement les erreurs humaines et les délais de réparation. En 2025, les programmes de formation sont de plus en plus interactifs et immersifs, ce qui permet aux techniciens de se familiariser avec des équipements complexes sans risquer des erreurs sur le terrain.
Réalité Virtuelle (VR) :
Les simulateurs VR, tels que ceux disponibles sur Oculus Quest 3, permettent aux techniciens de s’entraîner à des réparations complexes dans un environnement virtuel. Cela leur permet d’acquérir de l’expérience sans risquer d’endommager l’équipement réel.
Cas d’usage : Siemens Energy utilise la VR pour former ses techniciens à la maintenance des turbines. Cette méthode a réduit les erreurs de maintenance et a permis de former plus de techniciens en moins de temps.
d. Standardisation des Procédures
La standardisation des procédures permet de rendre les processus de maintenance plus efficaces et prévisibles, réduisant ainsi les temps d’arrêt.
Méthodes Lean :
- SMED (Single-Minute Exchange of Die) est une méthode Lean qui vise à réduire le temps de changement d’outils à moins de 10 minutes. Cette technique est cruciale pour les industries qui doivent effectuer fréquemment des changements d’outils sur leurs lignes de production.
Exemple : Toyota applique avec succès la méthode SMED sur ses lignes de montage, ce qui lui a permis de réduire ses temps d’arrêt de 50%. En standardisant les processus de maintenance et de changement d’outils, Toyota assure une production continue et évite les arrêts imprévus.
e. IoT et Edge Computing
L’Internet des objets (IoT) et le edge computing (calcul en périphérie) sont deux technologies clés pour améliorer la gestion des données et les processus de maintenance. Ces technologies permettent de collecter et d’analyser des données en temps réel à partir des machines, ce qui permet une intervention plus rapide et plus précise.
Protocoles :
- MQTT : Ce protocole de communication léger permet une transmission rapide des données avec une latence inférieure à 50 ms. Il est idéal pour connecter des capteurs IoT aux systèmes de maintenance et assurer une surveillance en temps réel.
- OPC UA : Ce protocole est utilisé pour connecter des machines anciennes et nouvelles au sein du même réseau, permettant ainsi de collecter des données depuis une grande variété d’équipements, qu’ils soient récents ou plus anciens.
Traitement local :
Le Siemens MindConnect utilise des passerelles IoT pour analyser les données localement sans avoir besoin de les envoyer vers le cloud. Cela réduit les délais de traitement et permet d’agir rapidement en cas de détection de problèmes sur les équipements.
3. Outils et Technologies Clés en 2025
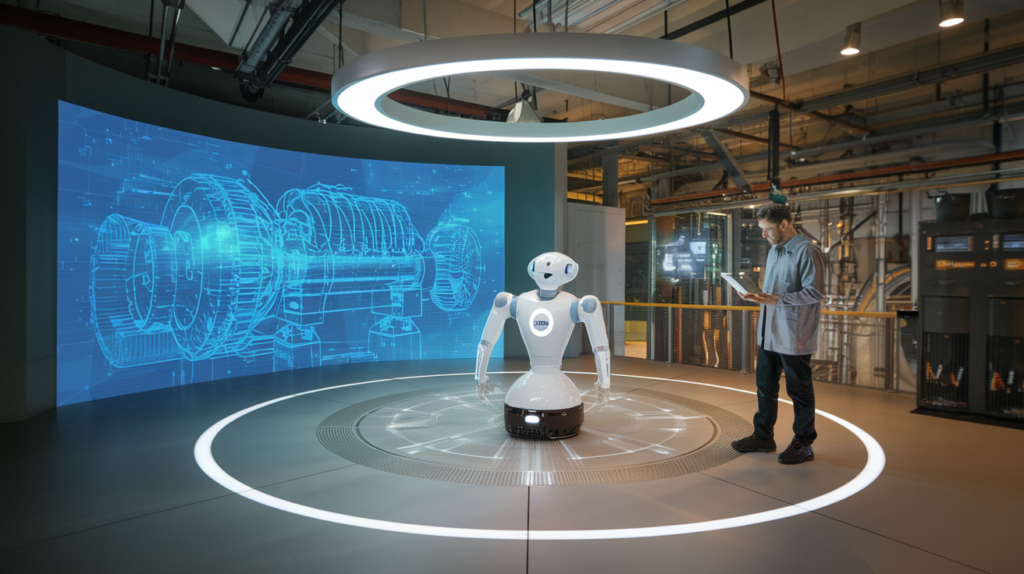
L’optimisation de la maintenance industrielle en 2025 repose sur des outils et technologies de pointe. Ces solutions permettent non seulement de réduire les temps d’arrêt, mais aussi d’améliorer la précision, la réactivité et la fiabilité des opérations de maintenance. Voici quatre technologies clés qui façonnent le paysage de la maintenance industrielle.
a. Jumeaux Numériques (Digital Twins)
Les jumeaux numériques sont des répliques virtuelles d’équipements physiques, créées à partir de données en temps réel. Ils permettent de simuler et d’analyser le comportement des machines et des systèmes, ce qui aide à anticiper les pannes, optimiser les performances et prolonger la durée de vie des équipements.
Applications :
- Simulation de l’usure d’une turbine GE 9HA.02 : Les jumeaux numériques permettent de simuler l’usure des turbines dans des conditions spécifiques, offrant ainsi une vision précise des moments où des révisions doivent être effectuées. Cette approche permet de planifier la maintenance de manière proactive, en évitant des arrêts non planifiés.
- Optimisation des cycles de maintenance chez Rolls-Royce : Rolls-Royce utilise des jumeaux numériques pour optimiser les cycles de maintenance de ses moteurs d’avion. Cette technologie a permis une réduction de 25% des arrêts imprévus, grâce à une gestion plus précise des révisions et de l’usure des composants.
b. IA Générative
L’intelligence artificielle générative a fait des progrès remarquables ces dernières années. Cette technologie utilise des modèles avancés, tels que ChatGPT-4, pour générer des rapports et des analyses de maintenance en langage naturel, facilitant ainsi la gestion et la compréhension des données complexes issues des capteurs.
Applications :
- ChatGPT-4 : L’IA générative peut analyser de grandes quantités de données de capteurs et générer des rapports de maintenance détaillés, en langage compréhensible par les équipes. Cela simplifie le travail des techniciens et des gestionnaires de maintenance, tout en assurant un suivi précis des interventions.
Cas concret : Saint-Gobain a automatisé 80% de ses compte-rendus d’intervention grâce à l’IA générative, réduisant ainsi considérablement le temps de traitement des rapports et améliorant l’efficacité des équipes de maintenance.
c. Robots Collaboratifs (Cobots)
Les robots collaboratifs (cobots) sont des robots conçus pour travailler aux côtés des opérateurs humains, plutôt que de les remplacer. Ces robots sont particulièrement utiles dans les environnements industriels où ils peuvent effectuer des tâches répétitives, de surveillance ou d’inspection sans se fatiguer, tout en augmentant la sécurité et la productivité.
Applications :
- Universal Robots UR10 : Ce robot collaboratif est utilisé pour effectuer des inspections régulières des équipements, détecter des anomalies et alerter les équipes de maintenance en cas de problème. Il est conçu pour travailler sans interruption, offrant une surveillance continue.
Exemple : Bosch utilise des cobots dans ses usines pour surveiller les convoyeurs. Ces robots inspectent les équipements 24/7 et détectent les anomalies avant qu’elles ne causent des arrêts prolongés ou des dommages majeurs.
d. Blockchain pour la Traçabilité
La blockchain est utilisée pour garantir une traçabilité inviolable des données de maintenance. En enregistrant toutes les interventions et réparations dans une chaîne de blocs sécurisée, cette technologie offre une visibilité totale sur l’historique des équipements, tout en assurant la sécurité et la transparence des informations.
Avantages :
- Historiques de maintenance inviolables : La blockchain permet de stocker les historiques de maintenance de manière décentralisée et immuable. Cela garantit que les informations relatives aux réparations, remplacements de pièces et tests de performance sont accessibles à tout moment, sans possibilité de manipulation.
Exemple : VeChain utilise la blockchain pour assurer la traçabilité des opérations de maintenance sur les avions d’Airbus. Cela permet de suivre les pièces reconditionnées en temps réel, réduisant ainsi les risques d’erreurs humaines et améliorant la gestion des stocks.
4. Études de Cas Concrets
L’adoption des technologies modernes dans les processus de maintenance a permis à plusieurs entreprises de réduire leurs temps d’arrêt et d’améliorer leur efficacité opérationnelle. Voici deux exemples concrets de secteurs ayant utilisé des solutions innovantes pour résoudre leurs problèmes de maintenance.
a. Secteur Automobile : Tesla
Problème :
Tesla faisait face à des temps d’arrêt récurrents sur ses robots de soudage dans ses usines de production. Ces arrêts imprévus étaient causés par des pannes de machines qui interrompaient la production, ce qui entraînait des retards et des pertes financières importantes.
Solution :
Tesla a déployé des capteurs IoT de la marque Banner Engineering pour surveiller en temps réel l’état des équipements. En complément, l’entreprise a intégré un système GMAO (Gestion de Maintenance Assistée par Ordinateur), avec le logiciel Fiix, pour centraliser et optimiser la gestion de la maintenance. Cette combinaison de capteurs IoT et de GMAO a permis de collecter des données sur les machines, de prédire les pannes et d’organiser la maintenance de manière proactive.
Résultats :
- Réduction de 55% des arrêts imprévus grâce à la maintenance prédictive et proactive.
- Retour sur investissement (ROI) en seulement 6 mois grâce à la réduction des coûts liés aux temps d’arrêt et à l’optimisation de la productivité.
b. Secteur Agroalimentaire : Danone
Problème :
Dans ses usines de production, Danone faisait face à des temps de nettoyage CIP (Cleaning In Place) excessivement longs. Chaque ligne de production nécessitait jusqu’à 8 heures de nettoyage, ce qui ralentissait considérablement la production et augmentait les coûts opérationnels.
Solution :
Danone a opté pour l’optimisation des processus de nettoyage grâce à des jumeaux numériques de Dassault Systèmes. Ces modèles numériques ont permis de simuler et d’optimiser les cycles de nettoyage, en ajustant les paramètres en temps réel pour réduire la durée des opérations tout en maintenant les normes de sécurité et d’hygiène.
Résultats :
- Réduction du temps de nettoyage de 8 heures à 3 heures par ligne.
- Économie annuelle de 900 000€ en coûts opérationnels, grâce à l’amélioration de l’efficacité du nettoyage et à la réduction des interruptions de production.
5. Tendances Futures (2025-2030)
L’avenir de la maintenance industrielle s’annonce prometteur avec l’arrivée de technologies encore plus avancées, permettant des gains d’efficacité et de réactivité inégalés. Voici quelques-unes des principales tendances à surveiller dans les cinq prochaines années.
5G Industriel
La 5G va transformer la manière dont les machines et les systèmes industriels communiquent. Les réseaux privés, comme ceux développés par Nokia DAC, offriront une connectivité ultra-rapide et fiable, permettant de connecter des milliers de capteurs IoT en temps réel, même dans des environnements complexes. Cette évolution facilitera la surveillance continue des machines critiques, permettant une détection instantanée des anomalies et une intervention proactive avant que des pannes graves ne se produisent.
Maintenance Autonome
Les robots collaboratifs (cobots) deviendront de plus en plus sophistiqués et capables de réaliser des réparations simples, comme le serrage de boulons ou l’ajustement de paramètres. Ces cobots autonomes seront équipés de capteurs et de logiciels d’IA pour effectuer des tâches de maintenance préventive ou réactive sans intervention humaine directe. Ils travailleront en toute sécurité à côté des opérateurs, réduisant ainsi les risques de blessures et améliorant l’efficacité globale de l’équipe de maintenance.
IA Auto-Adaptative
L’intelligence artificielle continuera à évoluer vers des systèmes auto-adaptatifs, comme ceux basés sur Google Vertex AI, qui ajustent automatiquement les seuils d’alerte et les paramètres de maintenance en fonction des nouvelles données collectées. Ces algorithmes auto-entraînés seront capables d’analyser des volumes de données plus importants et plus complexes, permettant une prise de décision en temps réel, une détection plus précise des anomalies et une optimisation continue des stratégies de maintenance.
Ces innovations promettent de redéfinir la gestion des équipements et de renforcer la compétitivité des entreprises dans les années à venir.
FAQ
Q1 : Quel budget prévoir pour un projet de réduction des temps d’arrêt ?
R : Le budget pour un projet de réduction des temps d’arrêt varie en fonction de la taille de l’entreprise et des technologies choisies. Pour une PME utilisant une solution cloud, le budget peut commencer à partir de 20 000€. En revanche, pour les grands groupes intégrant des technologies avancées comme l’IoT et l’IA, les coûts peuvent atteindre 500 000€ ou plus. Ce budget couvre généralement les capteurs, les logiciels de GMAO, ainsi que les coûts de formation et d’intégration.
Q2 : Comment mesurer l’efficacité des actions mises en place ?
R : L’efficacité des actions de réduction des temps d’arrêt peut être mesurée à l’aide de deux indicateurs clés de performance :
- MTTR (Mean Time To Repair) : Il s’agit du temps moyen nécessaire pour réparer une machine après une panne. Une réduction du MTTR indique une meilleure réactivité des équipes de maintenance.
- MTBF (Mean Time Between Failures) : Cet indicateur mesure le temps moyen entre deux pannes successives. Un MTBF plus élevé signifie une plus grande fiabilité des équipements et une maintenance préventive efficace.
Q3 : Comment la maintenance prédictive contribue-t-elle à la réduction des temps d’arrêt ?
R : La maintenance prédictive, grâce à l’utilisation de capteurs et d’algorithmes d’intelligence artificielle, permet d’anticiper les pannes avant qu’elles ne se produisent. Cela réduit les arrêts imprévus en permettant des interventions proactives sur les équipements, minimisant ainsi les interruptions de production et les coûts associés.
Q4 : Quels outils technologiques sont les plus efficaces pour réduire les temps d’arrêt ?
R : Les outils les plus efficaces pour réduire les temps d’arrêt incluent les systèmes de Gestion de Maintenance Assistée par Ordinateur (GMAO), l’utilisation de jumeaux numériques, et l’intégration de capteurs IoT pour la surveillance en temps réel. Ces technologies permettent de suivre l’état des machines, de planifier les interventions, et de prendre des décisions éclairées basées sur des données réelles.
Q5 : Quelle est la durée moyenne pour voir un retour sur investissement (ROI) dans un projet de réduction des temps d’arrêt ?
R : Le retour sur investissement (ROI) d’un projet de réduction des temps d’arrêt dépend de la taille du projet et des technologies mises en œuvre. En moyenne, les entreprises peuvent voir un ROI en 6 à 12 mois lorsqu’elles mettent en place des solutions telles que l’IoT, la maintenance prédictive, ou une GMAO efficace.
Q6 : Quels sont les principaux défis à surmonter pour réduire efficacement les temps d’arrêt ?
R : Les principaux défis incluent la résistance au changement des équipes de maintenance, le coût initial des technologies nécessaires (comme les capteurs IoT et l’IA), ainsi que l’intégration des nouvelles solutions dans les systèmes existants. De plus, le manque de formation adéquate des techniciens peut également freiner l’efficacité des projets de réduction des temps d’arrêt.
Q7 : Comment la formation du personnel influence-t-elle la réduction des temps d’arrêt ?
R : Une formation continue et spécialisée permet aux techniciens de mieux comprendre les équipements et d’utiliser efficacement les outils numériques (comme les GMAO et les capteurs IoT). Un personnel bien formé est capable d’identifier plus rapidement les signes de dysfonctionnement, d’effectuer des réparations plus efficaces et de prévenir les pannes, réduisant ainsi les temps d’arrêt de manière significative.
Q8 : Comment la standardisation des procédures aide-t-elle à réduire les temps d’arrêt ?
R : La standardisation des procédures, en particulier avec des méthodologies comme le SMED (Single-Minute Exchange of Die), permet de rationaliser les processus de maintenance. En standardisant les étapes et en utilisant des outils et techniques éprouvés, les entreprises peuvent effectuer des réparations plus rapidement, réduisant ainsi les temps d’arrêt et améliorant la productivité.
Conclusion (150 mots)
Réduire les temps d’arrêt en maintenance n’est plus une simple option, mais une nécessité pour toute entreprise désireuse de rester compétitive en 2025. En intégrant des technologies avancées telles que l’IA prédictive, l’IoT et les méthodes Lean, des leaders comme Michelin ou Schneider Electric démontrent que ces défis peuvent être transformés en réelles opportunités d’optimisation. Pour vous aussi, faire ce pas vers une maintenance plus efficace et plus proactive est à portée de main. Téléchargez notre guide comparatif des 10 meilleurs outils de réduction des temps d’arrêt et rejoignez notre masterclass “Maintenance 5.0” pour explorer les solutions les plus innovantes et adaptées à votre secteur. Ensemble, faisons de la réduction des temps d’arrêt un levier de performance durable et profitable pour votre entreprise.