En 2025, les coûts de maintenance industrielle représentent jusqu’à 15% du chiffre d’affaires des manufacturiers (McKinsey). Pourtant, des géants comme Renault ou Danone ont réussi à réduire ces dépenses de 40% grâce à l’intégration de l’IA et de l’IoT. Comment Optimisation des Coûts de Maintenance Industrielle sans compromettre la productivité ?
Problématique :
- Enjeux financiers : Une panne critique peut coûter jusqu’à 260 000€/heure dans l’aéronautique (Deloitte).
- Ressources limitées : 65% des responsables maintenance manquent de données cruciales pour prioriser les interventions (Gartner).
- Nouvelles réglementations : L’introduction de la taxe carbone oblige les entreprises à repenser l’efficacité énergétique de leurs équipements.
Solution teaser :
L’optimisation des coûts passe par une approche intégrée qui combine des GMAO intelligentes, des technologies IoT avancées, et l’intelligence artificielle pour une gestion proactive de la maintenance.
Table of Contents
1. Pourquoi les Coûts de Maintenance Explosent-ils en 2025 ?
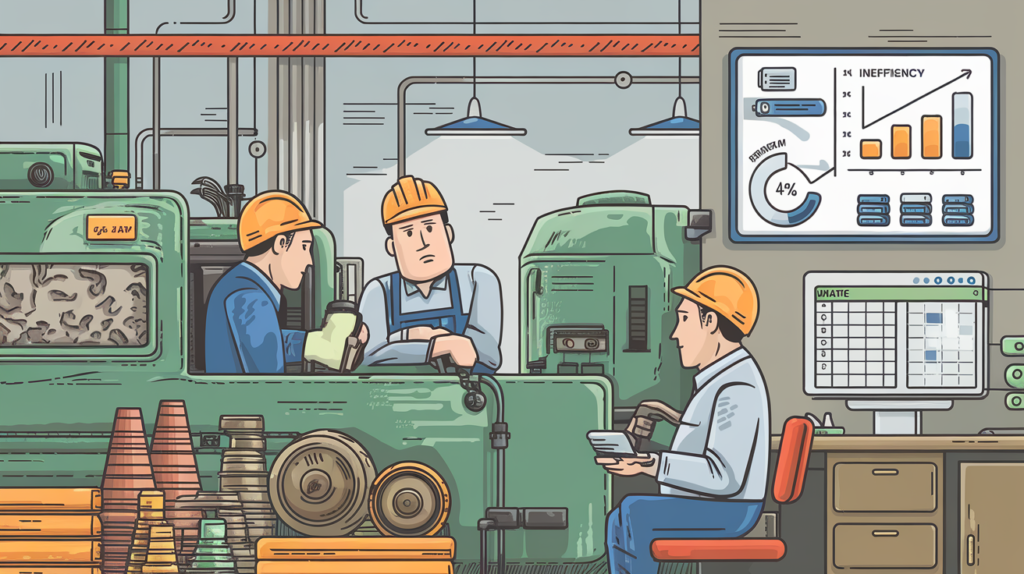
a. Causes structurelles
- Vieillissement des parcs machines : En Europe, 60% des équipements industriels ont plus de 20 ans, et beaucoup n’ont pas été rénovés ou remplacés à temps (Eurostat). Le manque d’investissement dans la modernisation des équipements contribue à l’augmentation des coûts de maintenance.
- Exemple concret : Une usine sidérurgique espagnole consacre jusqu’à 2 millions d’euros par an à la maintenance de pièces obsolètes, ce qui représente un poids financier considérable et une baisse de la compétitivité à long terme.
- Pannes récurrentes :
- Coûts directs : Les pannes régulières entraînent des coûts élevés en main-d’œuvre et en pièces de rechange. Par exemple, un moteur Siemens SIMOTICS peut coûter 25 000€, sans compter les frais associés à l’interruption de la production.
- Coûts indirects : Les pannes non maîtrisées affectent la réputation des entreprises et entraînent des pénalités de retard, notamment dans des secteurs sensibles comme l’automobile, où des retards de livraison peuvent coûter des millions d’euros en amendes.
b. Facteurs technologiques
- Données non exploitées : Bien que les équipements modernes soient souvent équipés de capteurs IoT, seulement 12% des données générées sont effectivement analysées et exploitées pour prendre des décisions éclairées (Capgemini). Cette sous-exploitation des données empêche une gestion proactive des pannes et l’optimisation des ressources.
- Outils obsolètes : Le recours excessif aux feuilles Excel et à des méthodes manuelles entraîne une planification inefficace. Une étude PwC a révélé que ces pratiques conduisent à 22% d’erreurs de planification, augmentant ainsi les coûts et les risques liés à la maintenance.
C. Impact environnemental
- Surconsommation énergétique : Des équipements mal entretenus consomment jusqu’à 18% d’énergie en plus, ce qui augmente la facture énergétique des entreprises (ADEME). Cette inefficacité énergétique non seulement pèse sur les coûts de maintenance, mais est également incompatible avec les objectifs environnementaux de réduction des émissions de CO2. Un entretien régulier et optimisé est essentiel pour améliorer l’efficacité énergétique et réduire les dépenses globales.
2. 5 Stratégies pour Optimiser vos Coûts de Maintenance en 2025
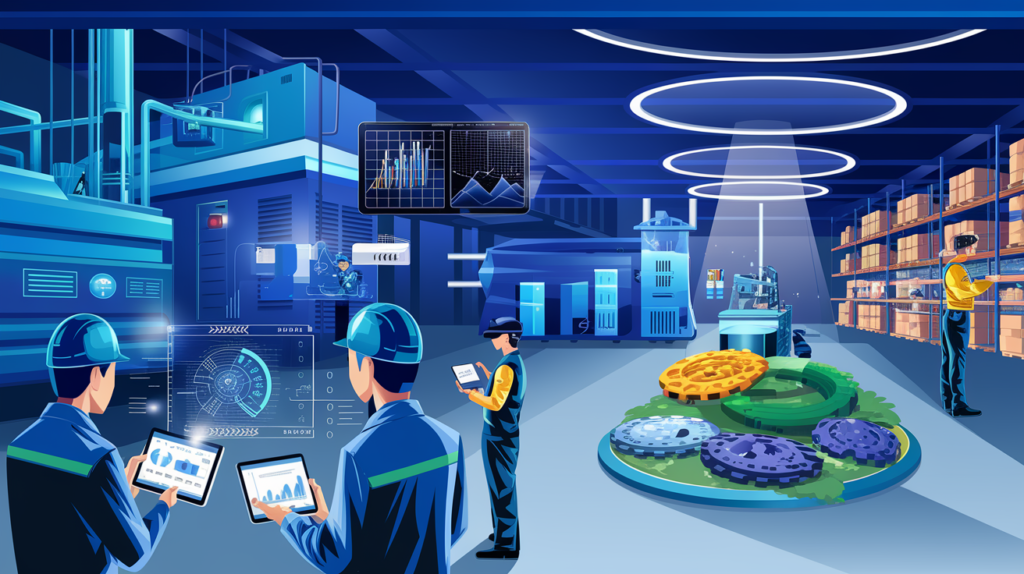
a. Adopter un GMAO avec IA Intégrée
Un système de Gestion de Maintenance Assistée par Ordinateur (GMAO) avec intelligence artificielle (IA) intégrée permet d’optimiser considérablement la gestion des équipements en anticipant les pannes et en maximisant la productivité.
- Fonctionnalités clés :
- Planification dynamique : Les calendriers sont ajustés en temps réel en fonction des priorités et des données disponibles, comme l’exemple de SAP Maintenance Connection.
- Analytique prédictive : Grâce à des algorithmes comme Random Forest, les pannes peuvent être anticipées avec une précision supérieure à 90%, permettant ainsi une gestion proactive.
- ROI : Les solutions cloud telles que Fiix, à partir de 150€/utilisateur/mois, montrent un retour sur investissement en moins de 14 mois, ce qui en fait une solution économique et efficace à long terme.
b. Passer à la Maintenance Prédictive
La maintenance prédictive repose sur l’analyse des données issues des capteurs IoT pour prévoir les défaillances avant qu’elles ne se produisent, réduisant ainsi les coûts imprévus.
- Capteurs IoT avancés :
- Accéléromètres Emerson CSI 2140 pour surveiller les vibrations des compresseurs.
- Thermographes FLIR pour détecter les surchauffes des équipements.
- Étude de cas : TotalEnergies a mis en place des technologies de surveillance vibratoire, permettant de réduire ses coûts de maintenance de 28% grâce à une gestion proactive des défaillances.
C. Optimiser la Gestion des Stocks
La gestion des stocks est un levier clé pour réduire les coûts de maintenance. L’automatisation du réapprovisionnement garantit une disponibilité immédiate des pièces essentielles sans maintenir des stocks excessifs.
- Réapprovisionnement intelligent :
- Intégration API avec les fournisseurs pour la commande automatique de pièces de rechange critiques, comme les roulements SKF.
- Exemple concret : Michelin a réussi à réduire ses stocks de pièces de 35% grâce à l’utilisation d’EcoStruxure, une solution IoT intelligente de gestion de la chaîne d’approvisionnement.
d. Former les Équipes aux Outils Numériques
La formation continue des équipes à l’utilisation des outils numériques est indispensable pour garantir une gestion efficace des équipements.
- Outils de formation innovants :
- Réalité virtuelle pour simuler des interventions complexes et améliorer l’apprentissage pratique des techniciens.
- Plateformes LMS (Learning Management Systems) telles que Docebo, permettant une formation à distance et à la demande.
- Impact sur les coûts : Des équipes bien formées et à jour sur les nouvelles technologies peuvent résoudre les problèmes plus rapidement, réduisant ainsi les temps d’arrêt et les erreurs humaines.
e. Intégrer l’Économie Circulaire
L’adoption d’une approche circulaire dans la gestion des pièces de rechange permet de réaliser des économies importantes tout en réduisant l’impact environnemental.
- Réutilisation des pièces :
- Utilisation de plateformes d’échange de composants usagés, comme Bosch Rexroth Reman, pour récupérer des pièces et composants reconditionnés à coût réduit.
- Impact : L’intégration de l’économie circulaire permet des économies pouvant aller jusqu’à 50% sur les pièces critiques, tout en contribuant à la durabilité et à la réduction des déchets industriels.
Ces stratégies permettent aux entreprises de moderniser leur approche de maintenance et d’optimiser leurs coûts en tirant parti des nouvelles technologies, tout en garantissant une performance élevée et durable.
3. Technologies Clés pour Réduire les Coûts en 2025
En 2025, les entreprises industrielles ont à leur disposition une gamme de technologies de pointe permettant de réduire les coûts de maintenance, d’améliorer la fiabilité des équipements et d’optimiser l’efficacité opérationnelle. Voici quatre technologies clés qui transforment la manière dont les entreprises gèrent la maintenance.
a. Intelligence Artificielle Générative
L’intelligence artificielle générative, telle que ChatGPT-4, permet de transformer les données brutes en rapports de maintenance rédigés en langage naturel, facilitant la prise de décision et la communication au sein des équipes.
- Avantages : Cette technologie réduit le temps nécessaire pour générer des rapports détaillés, permettant aux techniciens de se concentrer sur des tâches à plus forte valeur ajoutée.
- Cas concret : Schneider Electric utilise l’IA générative pour analyser les données des transformateurs et prioriser les interventions de maintenance, réduisant ainsi les temps d’intervention et augmentant la durée de vie de ses équipements. Cette solution permet à l’entreprise d’optimiser la maintenance prédictive et d’améliorer l’efficacité des opérations.
b. Jumeaux Numériques (Digital Twins)
Les jumeaux numériques sont des répliques virtuelles d’équipements physiques qui permettent de simuler leur fonctionnement dans des conditions réelles et d’anticiper les défaillances avant qu’elles ne surviennent.
- Simulation d’usure : Les modèles 3D de turbines GE sont utilisés pour tester des scénarios de défaillance. Ces simulations permettent de prévoir les zones à risque, de tester des actions correctives et de planifier les interventions en amont.
- Gains : Selon une étude de Gartner, l’utilisation des jumeaux numériques permet de réduire de 20% les temps d’arrêt grâce à une meilleure anticipation des pannes et à la gestion proactive des interventions.
c. Blockchain pour la Traçabilité
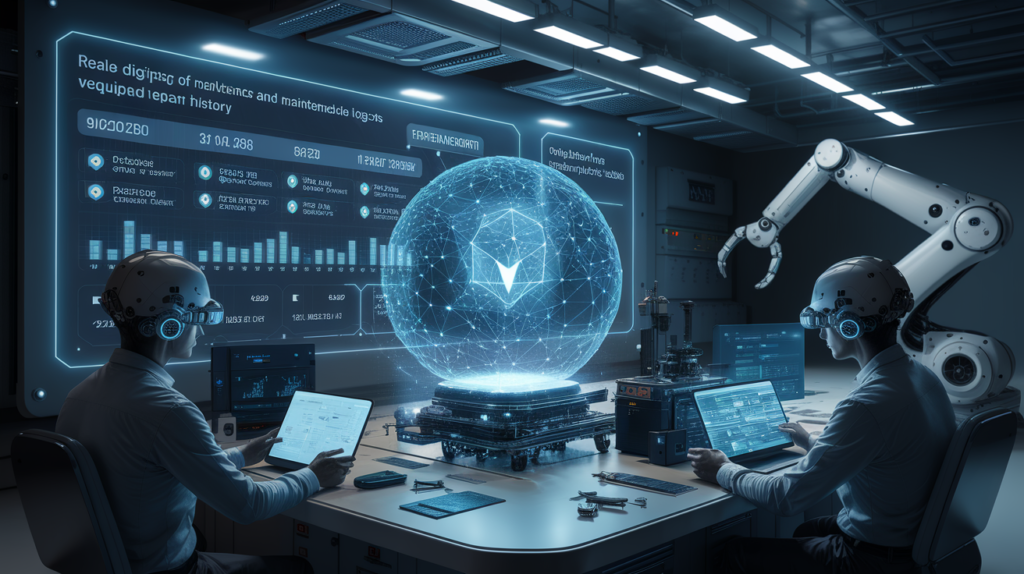
La blockchain améliore la traçabilité des opérations de maintenance en garantissant la transparence et la sécurité des données tout au long du cycle de vie des équipements.
- Audits automatisés : Des solutions comme VeChain permettent de garantir l’authenticité des historiques de maintenance en enregistrant chaque intervention de manière immuable. Cela facilite les audits et assure une meilleure gestion des équipements en fin de vie, tout en réduisant les risques d’erreur humaine.
- Avantages : La blockchain offre une méthode fiable et sécurisée pour suivre l’historique des réparations, des pièces remplacées et des coûts associés, permettant ainsi de mieux contrôler les budgets de maintenance.
d. Edge Computing
L’edge computing permet de traiter les données directement sur le lieu de leur collecte, réduisant ainsi la latence et la dépendance aux systèmes centralisés.
- Traitement local : Les passerelles Siemens MindConnect offrent un traitement des données localisé qui permet de réduire la latence de 70% dans des environnements industriels comme les mines.
- Gains : Grâce à l’edge computing, les entreprises peuvent prendre des décisions en temps réel, améliorer la réactivité face aux pannes et diminuer le besoin de communication continue avec des serveurs distants. Cela permet non seulement d’optimiser les coûts de maintenance, mais aussi de maintenir les équipements en fonctionnement plus longtemps, ce qui se traduit par des économies substantielles.
Ces technologies avancées, combinées à une gestion proactive, permettent aux entreprises de rester compétitives tout en réduisant efficacement leurs coûts de maintenance.
4. Études de Cas Concrets
Les études de cas illustrent comment des entreprises de différents secteurs parviennent à optimiser leurs coûts de maintenance tout en améliorant leur efficacité grâce aux technologies avancées. Voici deux exemples concrets de succès.
a. Secteur Automobile : Renault-Nissan
- Problème : Renault-Nissan faisait face à une perte de 18% de leur temps en maintenance corrective, impactant la productivité et les coûts de fonctionnement.
- Solution : L’entreprise a déployé IBM Maximo couplé avec des capteurs IoT pour une gestion plus proactive et intelligente de la maintenance. Cette solution a permis d’automatiser la collecte des données en temps réel et de déclencher des alertes dès qu’un problème potentiel était détecté.
- Résultats : En 18 mois, Renault-Nissan a réduit ses coûts de maintenance de 32% grâce à une gestion plus efficace des équipements. Le retour sur investissement (ROI) a été atteint en seulement 10 mois, prouvant l’efficacité rapide de cette solution pour les entreprises cherchant à optimiser leurs processus.
b. Secteur Pharma : Sanofi
- Problème : Sanofi rencontrait des problèmes récurrents de non-conformités avec la FDA, notamment des actions correctives fréquentes dues à une gestion de maintenance non optimisée, ce qui entrainait des risques de retards et des coûts supplémentaires.
- Solution : Sanofi a mis en place une GMAO SAP intégrant la traçabilité conforme à la norme 21 CFR Part 11, garantissant la sécurité des données et l’authenticité des interventions. Cette solution permettait une meilleure gestion des pièces de rechange et des interventions de maintenance avec une traçabilité complète.
- Résultats : Grâce à la mise en œuvre de cette GMAO avancée, Sanofi a réduit de 50% le nombre d’audits et d’actions correctives, ce qui a permis de minimiser les risques de non-conformité et d’améliorer la performance globale des équipements.
Ces études de cas démontrent que l’intégration des technologies avancées dans la maintenance permet de réduire les coûts, d’améliorer la conformité et de maximiser l’efficacité, quels que soient le secteur d’activité et les défis spécifiques.
5. Tendances 2025 : Ce Qui Va Changer
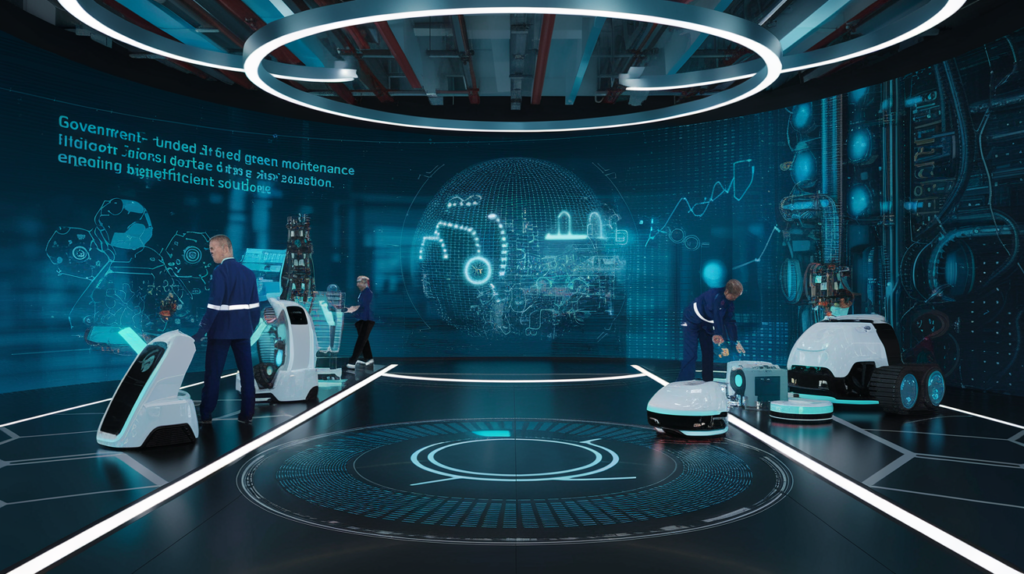
L’année 2025 s’annonce comme un tournant pour la maintenance industrielle, avec l’émergence de nouvelles technologies et tendances qui redéfiniront les pratiques traditionnelles et offriront des solutions innovantes pour optimiser les coûts et améliorer la productivité.
a. IA Auto-adaptative : Algorithmes auto-entraînés (ex : Google AutoML)
L’IA auto-adaptative représente une avancée majeure dans la maintenance industrielle. Les algorithmes auto-entraînés, comme ceux proposés par Google AutoML, permettent aux systèmes d’analyse de données de s’améliorer en temps réel sans nécessiter une intervention humaine constante. Ces algorithmes pourront ajuster leurs modèles en fonction de l’évolution des données, offrant ainsi une capacité de prédiction plus précise et une réactivité accrue aux défaillances imminentes des équipements.
b. Maintenance Autonome : Robots Collaboratifs (Cobots)
Les robots collaboratifs, ou cobots, feront une entrée plus marquée dans le domaine de la maintenance en 2025. Ces robots seront capables d’effectuer des réparations simples, comme le serrage de boulons ou le remplacement de pièces, tout en travaillant aux côtés des techniciens humains. Cette collaboration entre l’homme et la machine permettra de réduire les erreurs, d’augmenter la vitesse des interventions et d’améliorer la sécurité en réduisant le risque d’accidents lors des interventions complexes.
c. Subventions Vertes : Aides Gouvernementales pour les GMAO Réduisant l’Empreinte Carbone
Les politiques environnementales seront de plus en plus intégrées dans la gestion de la maintenance. En 2025, les entreprises pourront bénéficier de subventions et d’aides gouvernementales pour l’adoption de GMAO (Gestion de Maintenance Assistée par Ordinateur) qui contribuent à la réduction de l’empreinte carbone. Ces solutions, souvent basées sur l’IoT et l’analyse des données, permettent d’optimiser l’utilisation des ressources, de prolonger la durée de vie des équipements et de réduire la consommation d’énergie, tout en soutenant les objectifs de durabilité.
Ces tendances soulignent une convergence entre technologie, durabilité et performance, et offriront aux entreprises des moyens innovants pour renforcer leur compétitivité tout en répondant aux enjeux environnementaux de demain.
FAQ
Q1 : Quel est le coût moyen d’un logiciel GMAO ?
R : Le coût d’un logiciel GMAO varie selon le type de déploiement. Pour une solution cloud, il peut osciller entre 50€ et 150€ par utilisateur par mois. En revanche, pour une solution on-premise, les prix peuvent atteindre jusqu’à 50 000€ pour une licence avec des frais d’installation supplémentaires.
Q2 : Comment convaincre ma direction d’investir dans une GMAO ?
R : Pour convaincre votre direction, mettez en avant des études de cas et des retours sur investissement rapides. Par exemple, l’étude de Danone qui a économisé 1,2 million d’euros par an grâce à l’implémentation d’une GMAO. Un ROI clair et rapide est souvent un argument convaincant.
Q3 : Quelles sont les fonctionnalités essentielles d’une GMAO ?
R : Les fonctionnalités clés incluent la gestion des ordres de travail, la planification et la programmation des maintenances préventives, la gestion des stocks de pièces, le suivi des coûts et des performances, ainsi que l’intégration avec des systèmes IoT pour la maintenance prédictive.
Q4 : Combien de temps faut-il pour déployer une GMAO ?
R : Le déploiement d’une GMAO peut prendre de quelques semaines à plusieurs mois, en fonction de la taille de l’entreprise, du type de solution choisie et de la complexité de l’intégration avec les systèmes existants.
Q5 : Est-ce que la GMAO peut vraiment réduire les coûts de maintenance ?
R : Oui, une GMAO bien implémentée peut réduire considérablement les coûts en optimisant la planification des interventions, en prévenant les pannes imprévues et en permettant un suivi plus précis des dépenses liées à la maintenance.
Conclusion
Optimiser les coûts de maintenance industrielle en 2025 ne se limite plus à une simple gestion des ressources. C’est un véritable défi stratégique, nécessitant l’intégration de technologies avancées. En combinant des solutions telles que la GMAO, l’IA prédictive et l’économie circulaire, les entreprises leaders comme L’Oréal et Airbus réussissent à transformer la maintenance d’un centre de coûts en un véritable levier de compétitivité. L’innovation et la flexibilité seront les clés pour relever ces défis et garantir la rentabilité et la performance à long terme. Pour rester compétitif, il est essentiel d’adopter ces technologies et de suivre une approche proactive pour anticiper et réduire les coûts de maintenance.