En 2024, les entreprises industrielles sont confrontées à des défis croissants pour optimiser la performance de leurs équipements et minimiser les temps d’arrêt. Adopter une stratégie de maintenance efficace est essentiel pour garantir la continuité des opérations, réduire les coûts et améliorer la sécurité. Cet article explore en profondeur les 7 stratégies de maintenance industrielle efficaces, afin d’aider les professionnels à choisir l’approche la plus adaptée à leurs besoins.
Table of Contents
1. Maintenance Réactive : L’Intervention Après Panne
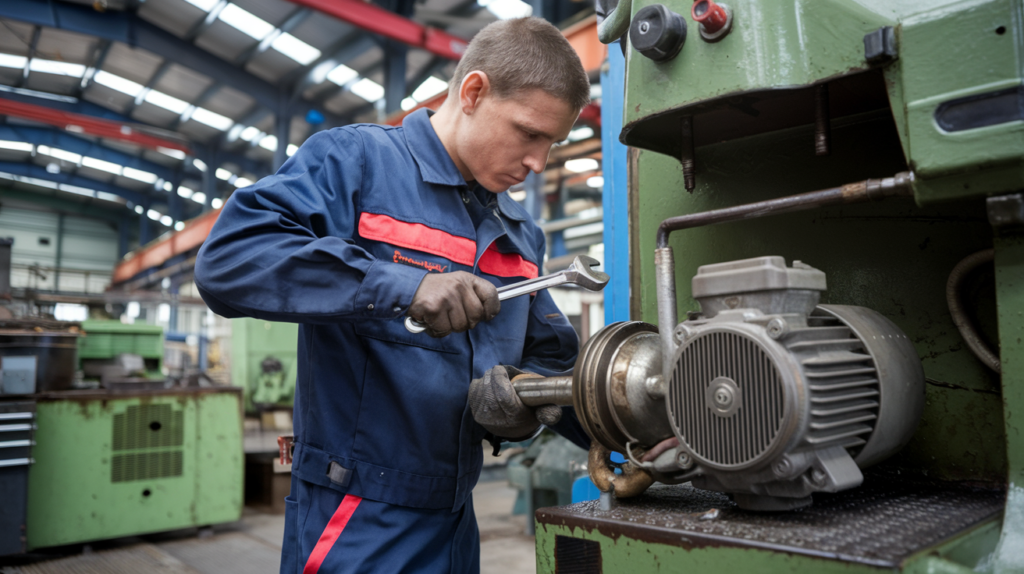
En 2024, la maintenance réactive reste l’une des stratégies les plus utilisées dans de nombreuses industries, malgré ses inconvénients évidents. Souvent adoptée par défaut dans les entreprises où les budgets sont limités, elle consiste à attendre qu’une machine tombe en panne avant d’intervenir pour la réparer. Cela signifie que les équipes de maintenance n’effectuent aucune inspection régulière ni action préventive. L’objectif principal est de restaurer le fonctionnement normal de l’équipement le plus rapidement possible.
Qu’est-ce que la Maintenance Réactive ?
La maintenance réactive, également appelée maintenance corrective, est une approche simple où aucune mesure n’est prise tant qu’un problème ne se présente pas. Par exemple, un moteur de pompe dans une centrale électrique qui cesse de fonctionner serait réparé ou remplacé seulement après l’incident. Cette méthode repose donc sur la réactivité et non sur l’anticipation.
Points clés de la maintenance réactive :
- Pas de planification anticipée.
- Intervention seulement après qu’une panne soit détectée.
- Absence de surveillance conditionnelle ou d’inspections régulières.
Avantages de la Maintenance Réactive
- Faibles Coûts Initiaux
- L’un des principaux avantages de la maintenance réactive est l’absence d’investissement initial. Il n’est pas nécessaire de mettre en place des systèmes de surveillance, ni d’acheter des capteurs coûteux. Cette stratégie convient donc aux entreprises qui cherchent à minimiser leurs dépenses immédiates.
- Rapidité d’Intervention
- Lorsque la panne survient, les équipes de maintenance sont généralement prêtes à intervenir immédiatement. Les actions sont alors directes et ciblées pour résoudre le problème identifié sans autre analyse préalable.
- Moins de Planification Complexe
- La maintenance réactive simplifie la gestion, car il n’est pas nécessaire de planifier des arrêts pour entretien. Cela peut convenir aux petites entreprises avec des ressources limitées et des équipements facilement remplaçables.
Inconvénients de la Maintenance Réactive
- Coûts de Réparation Élevés
- Les réparations d’urgence sont souvent plus coûteuses que les interventions planifiées. Par exemple, remplacer un composant de manière imprévue peut nécessiter des frais supplémentaires pour des pièces en urgence, et l’indisponibilité des techniciens peut retarder les réparations.
- Interruption de la Production
- L’un des plus grands inconvénients de cette approche est le risque d’arrêts imprévus. Lorsque des équipements critiques tombent en panne, la production peut s’arrêter complètement, ce qui peut entraîner des pertes financières importantes. Dans une usine de fabrication, par exemple, une panne de compresseur d’air pourrait immobiliser l’ensemble de la ligne de production.
- Risque de Détérioration de l’Équipement
- La maintenance réactive ne s’attaque pas aux causes sous-jacentes des pannes. Par conséquent, des défaillances répétitives peuvent survenir, entraînant une usure prématurée des composants et une durée de vie réduite des machines.
Exemple Concret
Dans une entreprise de fabrication de pièces automobiles, la maintenance réactive est souvent utilisée pour les petits équipements auxiliaires comme les pompes à eau de refroidissement. Ces pompes ne sont pas surveillées de manière proactive, et lorsqu’une pompe tombe en panne, l’équipe de maintenance est appelée pour la remplacer.
Cependant, une panne de pompe pendant les heures de production peut entraîner des arrêts coûteux et affecter l’efficacité globale de l’usine. Un arrêt imprévu d’une seule heure pourrait coûter des milliers d’euros en termes de perte de production et de pénalités pour retard de livraison.
Quand Utiliser la Maintenance Réactive ?
La maintenance réactive peut être une bonne option pour les équipements non critiques ou lorsque le coût de la réparation est faible. Par exemple, dans une petite usine de fabrication, des ventilateurs ou des luminaires défectueux peuvent être réparés ou remplacés sans impact majeur sur la production.
Exemples d’applications idéales :
- Appareils et équipements non essentiels (ventilateurs, compresseurs auxiliaires).
- Entreprises avec des budgets de maintenance limités.
- Situations où le coût de l’arrêt de la machine est négligeable.
Recommandations
Bien que la maintenance réactive soit simple à mettre en œuvre, elle doit être utilisée avec prudence. Pour les équipements critiques, il est fortement recommandé de la combiner avec des stratégies préventives ou conditionnelles afin de minimiser les risques. Une bonne approche pourrait être de surveiller les machines les plus importantes à l’aide de capteurs et d’utiliser la maintenance réactive uniquement pour les machines secondaires.
Conseils pour optimiser la maintenance réactive :
- Garder un stock de pièces de rechange pour les composants susceptibles de tomber en panne.
- Former le personnel de maintenance pour des interventions rapides et efficaces.
- Analyser les pannes répétitives et mettre en place des actions correctives pour éviter leur récurrence.
==> En résumé, la maintenance réactive peut être efficace dans certains contextes, notamment pour des équipements non critiques et lorsque les budgets sont serrés. Cependant, cette stratégie présente des limitations importantes, surtout dans des environnements industriels complexes où l’interruption de la production peut entraîner des pertes financières significatives. Pour maximiser l’efficacité de vos opérations de maintenance, il est essentiel d’évaluer soigneusement vos besoins et d’intégrer des éléments de maintenance préventive ou prédictive lorsque cela est possible.
2. Maintenance Préventive : Prévenir Plutôt que Guérir
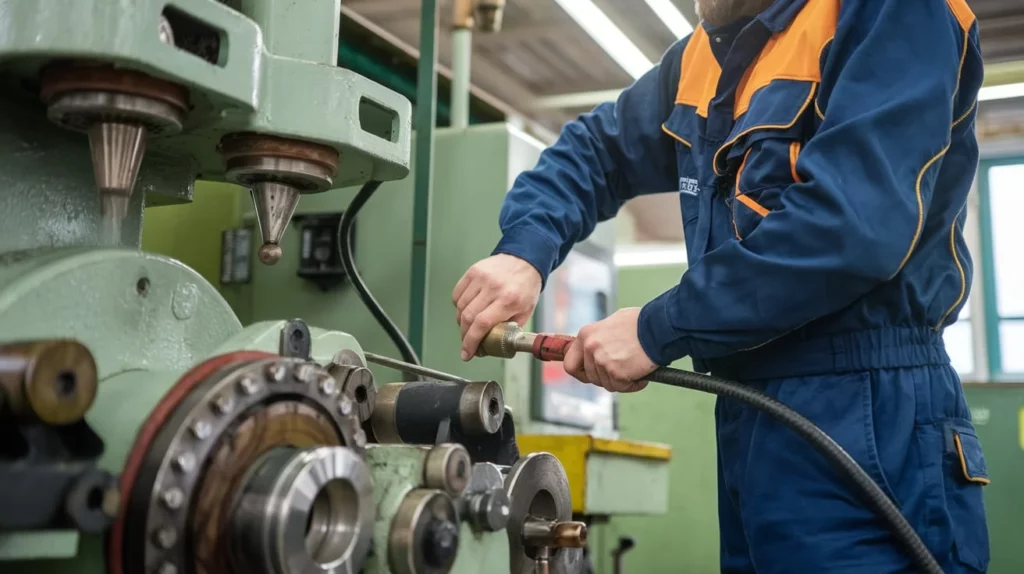
La maintenance préventive est une stratégie proactive de gestion des équipements industriels qui repose sur des interventions planifiées et régulières pour éviter les pannes imprévues. Contrairement à la maintenance réactive, qui intervient après une défaillance, la maintenance préventive vise à minimiser les risques en prenant des mesures préventives avant que des défaillances ne surviennent.
Définition de la Maintenance Préventive
La maintenance préventive consiste à effectuer des contrôles, des inspections et des entretiens réguliers sur les équipements, indépendamment de leur état actuel. Les interventions sont programmées sur la base d’un calendrier établi ou en fonction des heures de fonctionnement des machines. L’objectif principal est de prévenir les pannes potentielles et de maintenir les machines en bon état de fonctionnement.
Points clés de la maintenance préventive :
- Basée sur un calendrier ou sur des données d’utilisation (heures de fonctionnement).
- Implique des inspections, des lubrifications, des ajustements et des remplacements de pièces avant que les problèmes n’apparaissent.
- Nécessite une bonne gestion et une planification rigoureuse.
Avantages de la Maintenance Préventive
- Réduction des Pannes Imprévues
- En effectuant des inspections régulières, la maintenance préventive permet de détecter les signes d’usure ou de fatigue des composants avant qu’ils ne causent une panne majeure. Par exemple, dans une usine de production chimique, le remplacement régulier des joints et des filtres peut empêcher les fuites dangereuses.
- Amélioration de la Fiabilité et Allongement de la Durée de Vie des Équipements
- Les interventions planifiées aident à maintenir les équipements en bon état, prolongeant ainsi leur durée de vie utile. Par exemple, une maintenance préventive sur une turbine d’éolienne, incluant la vérification des roulements et des systèmes de lubrification, peut augmenter considérablement sa durée de fonctionnement.
- Optimisation des Coûts à Long Terme
- Bien que la maintenance préventive puisse sembler coûteuse à court terme, elle permet de réaliser des économies importantes à long terme en réduisant les coûts de réparation d’urgence et en minimisant les interruptions de production. Selon certaines études, les entreprises peuvent économiser jusqu’à 30 % en adoptant une approche préventive par rapport à une approche réactive.
Inconvénients de la Maintenance Préventive
- Coût d’Entretien Plus Élevé
- Les interventions régulières et planifiées peuvent entraîner des coûts supplémentaires, notamment si elles sont réalisées sur des équipements encore en bon état. Par exemple, remplacer systématiquement une courroie de transmission qui pourrait encore fonctionner quelques mois supplémentaires entraîne des dépenses inutiles.
- Complexité de la Planification et Risque de Sur-Maintenance
- Déterminer le moment idéal pour effectuer des interventions préventives est une tâche complexe qui nécessite une analyse approfondie des données historiques et des conditions d’utilisation des équipements. Une mauvaise planification peut entraîner des arrêts inutiles et une sur-maintenance, augmentant ainsi les coûts sans réel bénéfice.
- Besoin de Ressources Humaines et Matérielles
- La maintenance préventive nécessite une équipe de maintenance bien formée et des ressources suffisantes pour effectuer les inspections et les réparations régulières. Cela implique également de disposer d’un stock de pièces de rechange, ce qui peut être contraignant pour certaines entreprises.
Exemple Concret
Dans l’industrie agroalimentaire, les chaînes de production doivent être maintenues dans des conditions optimales pour éviter toute contamination et garantir la qualité des produits. Par exemple, une usine de transformation de viande planifie des nettoyages approfondis et des contrôles sanitaires réguliers de ses machines pour prévenir toute défaillance. Grâce à cette approche préventive, l’usine peut éviter des arrêts coûteux dus à des pannes d’équipements critiques, comme les mélangeurs ou les broyeurs.
En revanche, l’absence de maintenance préventive dans une telle usine pourrait entraîner des défaillances imprévues, mettant en péril non seulement la production mais aussi la sécurité alimentaire.
Bonnes Pratiques pour la Maintenance Préventive
- Utiliser une systeme GMAO (Gestion de Maintenance Assistée par Ordinateur)
- Une GMAO est un outil essentiel pour planifier, suivre et optimiser les activités de maintenance préventive. Elle permet de centraliser l’historique des interventions, de suivre les heures d’utilisation des machines et de programmer automatiquement les inspections nécessaires. Par exemple, une entreprise qui utilise une GMAO peut recevoir des notifications lorsqu’il est temps de vérifier les roulements de ses machines, ce qui minimise le risque de sur-maintenance.
- Analyser les Données Historiques
- Utiliser les données des pannes passées pour affiner les intervalles d’entretien est crucial. Par exemple, si une pièce spécifique a tendance à s’user après 1 000 heures d’utilisation, il peut être plus judicieux de planifier son remplacement après 900 heures pour éviter une panne imprévue.
- Former le Personnel de Maintenance
- La formation régulière des équipes de maintenance est essentielle pour assurer des inspections efficaces. Les techniciens doivent être capables de reconnaître les signes précurseurs de défaillances, tels que des vibrations anormales ou des changements de température.
- Mettre en Place un Programme de Lubrification
- La lubrification des composants est une partie importante de la maintenance préventive, surtout pour les machines à haute vitesse. Par exemple, dans une usine de fabrication de papier, la lubrification régulière des roulements et des arbres rotatifs est essentielle pour éviter les défaillances coûteuses.
==> La maintenance préventive est une stratégie incontournable pour les entreprises qui cherchent à optimiser la fiabilité de leurs équipements et à minimiser les interruptions de production. Bien qu’elle nécessite un investissement initial plus important et une planification rigoureuse, ses avantages à long terme sont indéniables. En combinant cette approche avec des technologies modernes comme la GMAO, les entreprises peuvent maximiser l’efficacité de leur programme de maintenance et améliorer significativement leur retour sur investissement.
3. Maintenance Prédictive : Prédire les Pannes Grâce aux Données
La maintenance prédictive représente une approche moderne et proactive pour l’entretien des équipements. Elle repose sur l’utilisation de capteurs, d’algorithmes d’analyse de données et de logiciels avancés pour surveiller en continu l’état des machines et prévoir les pannes avant qu’elles ne surviennent.
Définition
La maintenance prédictive consiste à analyser des données collectées en temps réel par des capteurs placés sur les équipements. Ces données incluent des paramètres tels que les vibrations, la température, la pression, et l’usure. L’objectif est de détecter les anomalies et d’intervenir avant que des défaillances ne surviennent, réduisant ainsi les interruptions imprévues.
Points clés de la maintenance prédictive :
- Utilisation des données en temps réel pour évaluer l’état des machines.
- Prédiction des pannes basée sur des modèles statistiques et des algorithmes de machine learning.
- Réduction de la fréquence des interventions de maintenance, limitant ainsi la sur-maintenance.
Avantages de la Maintenance Prédictive
- Réduction des Coûts de Maintenance
- Contrairement à la maintenance préventive, où des interventions régulières sont planifiées, la maintenance prédictive n’intervient que lorsque cela est nécessaire, évitant les coûts inutiles. Par exemple, une entreprise manufacturière utilisant des capteurs de vibration peut identifier les problèmes avant qu’un roulement ne casse, réduisant ainsi les coûts de réparation.
- Diminution des Arrêts Non Planifiés
- Grâce à l’analyse en temps réel, les équipes de maintenance peuvent intervenir avant que des problèmes critiques ne surviennent, ce qui permet de maintenir la continuité de la production. Par exemple, dans une centrale électrique, les capteurs surveillent la température des turbines et alertent les techniciens si une surchauffe est détectée.
- Optimisation de la Durée de Vie des Équipements
- La maintenance prédictive permet de maximiser l’utilisation des pièces jusqu’à leur fin de vie réelle, sans remplacement prématuré. Cela prolonge la durée de vie des composants critiques et améliore le retour sur investissement.
Inconvénients de la Maintenance Prédictive
- Investissement Initial Élevé
- La mise en place d’une infrastructure de maintenance prédictive nécessite des capteurs avancés, des logiciels de surveillance et des plateformes d’analyse de données, ce qui représente un investissement important, surtout pour les petites entreprises.
- Besoin d’Expertise Technique
- L’analyse et l’interprétation des données collectées demandent des compétences spécialisées. Les équipes de maintenance doivent être formées à l’utilisation des logiciels de surveillance et à la compréhension des résultats des analyses.
Exemple Concret
Dans une aciérie, des capteurs mesurent en continu la vibration des moteurs des machines de laminage. Une augmentation inhabituelle des vibrations peut indiquer un déséquilibre dans les roulements. Plutôt que d’attendre la panne, les techniciens peuvent intervenir et remplacer les roulements avant qu’ils ne cassent, évitant ainsi une défaillance majeure qui pourrait arrêter la production pendant plusieurs heures.
Conseil Pratique
Investir dans une plateforme IoT (Internet des Objets) connectée aux capteurs permet de centraliser et d’analyser les données en temps réel, facilitant ainsi une maintenance prédictive efficace.
4. Maintenance Conditionnelle : Une Approche Basée sur l’État des Équipements
La maintenance conditionnelle, ou maintenance sur état, repose sur la surveillance en temps réel des paramètres de fonctionnement des équipements pour décider quand intervenir. Elle combine les avantages de la maintenance préventive et prédictive.
Définition
La maintenance conditionnelle implique de surveiller l’état des machines via des capteurs qui mesurent des paramètres critiques comme la température, la pression, ou les vibrations. Les interventions sont déclenchées uniquement si une anomalie est détectée, ce qui permet de limiter les arrêts inutiles.
Avantages de la Maintenance Conditionnelle
- Interventions Ciblées
- Les réparations sont effectuées seulement lorsque des signes d’usure ou de défaillance sont détectés, réduisant ainsi le risque de sur-maintenance.
- Optimisation des Ressources
- Les équipes de maintenance peuvent se concentrer sur les équipements qui nécessitent une attention immédiate, ce qui permet une meilleure allocation de la main-d’œuvre et des pièces de rechange.
Inconvénients
- Complexité de la Surveillance
- La mise en place d’un système de maintenance conditionnelle nécessite des capteurs avancés et une surveillance continue des données, ce qui peut être coûteux et complexe.
- Fiabilité des Données
- La qualité des données collectées est essentielle. Des capteurs défectueux peuvent envoyer des alertes erronées, entraînant des interventions inutiles.
Exemple Concret
Dans une raffinerie de pétrole, des capteurs surveillent la pression dans les tuyaux. Si la pression dépasse une certaine limite, une alerte est envoyée aux techniciens pour inspecter et vérifier l’état des vannes, réduisant ainsi le risque de fuites dangereuses.
5. Maintenance Proactive : Identifier et Résoudre les Causes Racines
La maintenance proactive se concentre sur l’élimination des causes racines des pannes récurrentes en utilisant une analyse approfondie des défaillances.
Définition
La maintenance proactive vise à identifier et à corriger les causes sous-jacentes des pannes répétées, plutôt que de simplement réparer les défaillances. Elle s’appuie sur des techniques d’analyse des causes racines et sur des audits réguliers des processus.
Avantages
- Réduction des Défaillances Répétitives
- En traitant les problèmes à la source, la maintenance proactive empêche les défaillances de se reproduire.
- Amélioration Continue
- L’analyse régulière des équipements permet d’apporter des améliorations continues, augmentant ainsi la fiabilité et la performance.
Inconvénients
- Nécessite une Analyse Détaillée
- Les équipes doivent être formées pour réaliser des analyses approfondies, ce qui demande du temps et des compétences spécifiques.
6. Maintenance TPM (Total Productive Maintenance) : Une Approche Collective

La Total Productive Maintenance (TPM) est une méthode de gestion de la maintenance qui repose sur une implication collective de tous les employés, des opérateurs aux cadres. L’objectif principal de la TPM est d’éliminer les pertes et les inefficacités dans la production en responsabilisant l’ensemble des équipes, contribuant ainsi à une amélioration continue des performances des équipements.
Définition
La TPM intègre la maintenance dans la culture de l’entreprise, faisant de la performance des équipements une responsabilité partagée par tous. Cette approche inclut des programmes de formation pour les opérateurs afin qu’ils puissent effectuer des tâches de maintenance de base (nettoyage, inspection, lubrification) et signaler rapidement les anomalies. Les équipes de maintenance interviennent pour les réparations complexes, mais le rôle des opérateurs est essentiel pour la surveillance quotidienne et l’identification précoce des problèmes.
Les 8 Piliers de la TPM
La TPM s’articule autour de 8 piliers fondamentaux, chacun visant à éliminer des pertes spécifiques :
- Maintenance Autonome : Les opérateurs effectuent des tâches simples de maintenance et d’inspection pour détecter rapidement les anomalies.
- Amélioration Continue (Kaizen) : Des initiatives d’amélioration sont mises en place pour optimiser l’efficacité des équipements et des processus.
- Maintenance Planifiée : Les interventions sont programmées en fonction des données de performance pour minimiser les interruptions.
- Formation et Développement des Compétences : Formation continue des opérateurs et techniciens pour développer leurs compétences en maintenance.
- Gestion Précoce des Équipements : Intégration des aspects de maintenance dès la conception des nouveaux équipements pour faciliter leur entretien.
- Sécurité, Santé et Environnement : Priorité à la sécurité et à la réduction des risques d’accidents.
- Qualité Intégrée : Surveillance des équipements pour garantir une production sans défauts.
- Efficacité Globale des Équipements (OEE) : Mesure de l’efficacité des équipements pour identifier les pertes et améliorer la productivité.
Avantages de la TPM
- Réduction des Pannes
- En impliquant les opérateurs dans l’entretien quotidien, la TPM permet une détection précoce des anomalies, avant qu’elles ne deviennent des pannes majeures. Les petites interventions (nettoyage, lubrification) sont réalisées régulièrement, ce qui réduit les risques de défaillance. Par exemple, dans une usine de fabrication automobile, les opérateurs nettoient et inspectent les machines tous les jours, détectant les premiers signes d’usure des pièces.
- Amélioration de l’Engagement des Employés
- La TPM favorise une culture d’amélioration continue et de responsabilisation. Les opérateurs ne sont plus simplement des utilisateurs des machines, mais deviennent des acteurs actifs de leur maintenance. Cela augmente leur engagement et leur motivation, car ils voient directement l’impact de leur travail sur la fiabilité des équipements.
- Augmentation de l’Efficacité Globale des Équipements (OEE)
- La TPM vise à améliorer l’OEE, un indicateur clé qui mesure l’efficacité des équipements en prenant en compte la disponibilité, la performance, et la qualité. Une augmentation de l’OEE signifie une meilleure productivité, moins de temps d’arrêt, et moins de défauts de production.
- Réduction des Coûts de Maintenance
- En intégrant la maintenance aux tâches quotidiennes des opérateurs, la TPM diminue les besoins en interventions coûteuses. Les petites réparations et ajustements sont effectués avant qu’ils n’entraînent des défaillances graves, réduisant ainsi les coûts de réparation et d’immobilisation des machines.
- Meilleure Communication et Collaboration
- La TPM améliore la communication entre les opérateurs et les équipes de maintenance. Les problèmes sont signalés rapidement et traités efficacement, créant une atmosphère de travail collaborative. Les réunions régulières de TPM permettent aux équipes de discuter des problèmes rencontrés, des améliorations possibles, et des succès obtenus.
Inconvénients de la TPM
- Nécessite un Engagement de Toute l’Organisation
- La mise en œuvre de la TPM demande une implication totale de tous les niveaux de l’entreprise, du personnel de production aux cadres dirigeants. Si l’engagement n’est pas global, la méthode perd en efficacité.
- Temps et Formation Initiale
- L’intégration de la TPM peut être longue et nécessite une formation importante des opérateurs. La transition vers une nouvelle culture de maintenance peut également rencontrer des résistances, surtout dans les entreprises où les pratiques de maintenance traditionnelles sont bien ancrées.
Exemple Concret de TPM
Dans une entreprise agroalimentaire, la TPM a été mise en place pour réduire les arrêts de production dus aux pannes des convoyeurs. Les opérateurs ont été formés à la maintenance autonome, incluant le nettoyage et l’inspection des bandes transporteuses. Grâce à ces inspections régulières, les opérateurs ont pu identifier et signaler des signes d’usure sur les roulements avant qu’ils ne se brisent, évitant ainsi des arrêts de production coûteux.
Conseil Pratique
Pour réussir la mise en œuvre de la TPM, commencez par former vos opérateurs aux bases de la maintenance autonome et introduisez progressivement les autres piliers. Organisez des sessions de feedback régulières pour encourager la communication et l’amélioration continue. En investissant dans la formation et en encourageant la collaboration, vous maximiserez les résultats de la TPM.
7. Maintenance Basée sur l’IA : L’Innovation Technologique
La maintenance basée sur l’intelligence artificielle (IA) représente une avancée majeure dans la gestion des équipements industriels. Grâce à des algorithmes sophistiqués et à l’analyse des données en temps réel, l’IA est capable de prédire les pannes avant qu’elles ne se produisent, optimisant ainsi la maintenance et réduisant les coûts.
Définition
La maintenance basée sur l’IA combine des données de capteurs, des technologies de machine learning et des modèles prédictifs pour surveiller l’état des équipements. L’IA apprend à partir de vastes ensembles de données historiques et détecte des anomalies invisibles à l’œil humain ou aux méthodes traditionnelles de surveillance. Ce type de maintenance est souvent intégré à des systèmes IoT (Internet des Objets) qui permettent une collecte continue des données.
Avantages
- Précision des Prédictions
- Les modèles d’IA utilisent des algorithmes d’apprentissage automatique qui s’améliorent avec le temps, augmentant la précision des prédictions. L’IA identifie des schémas complexes dans les données, permettant d’anticiper des pannes potentielles avant même qu’elles ne présentent des signes visibles.
- Réduction des Coûts de Maintenance
- En prévoyant les défaillances, la maintenance basée sur l’IA permet de planifier des interventions ciblées, évitant ainsi les réparations coûteuses et les arrêts non planifiés. Les entreprises peuvent ainsi réduire leurs coûts opérationnels tout en augmentant la durée de vie des équipements.
- Optimisation de la Disponibilité des Équipements
- Les données analysées par l’IA fournissent des indicateurs précis de l’état des machines, permettant de minimiser les interruptions de production. Les interventions sont réalisées au moment optimal, évitant les temps d’arrêt imprévus et augmentant la productivité.
- Amélioration de la Fiabilité
- L’IA contribue à une maintenance proactive, identifiant non seulement les anomalies, mais aussi les causes profondes des défaillances. Cela aide à mettre en œuvre des actions correctives avant que les problèmes ne surviennent, améliorant ainsi la fiabilité globale des systèmes.
Inconvénients
- Investissement Initial Élevé
- L’implémentation de la maintenance basée sur l’IA nécessite un investissement conséquent dans les capteurs, l’infrastructure de collecte de données, et les logiciels d’analyse. Cependant, ces coûts initiaux peuvent être compensés par des économies réalisées sur le long terme.
- Complexité de Mise en Œuvre
- L’intégration de l’IA dans les processus de maintenance requiert une expertise technique et des compétences en science des données. Les équipes doivent être formées pour interpréter les résultats et ajuster les modèles en fonction des évolutions des équipements.
- Qualité des Données
- Le succès de la maintenance basée sur l’IA dépend de la qualité et de la quantité des données collectées. Des données erronées ou insuffisantes peuvent entraîner des prédictions inexactes, augmentant le risque d’interventions inutiles ou de pannes non détectées.
Exemple Concret
Dans une ferme éolienne, les turbines sont équipées de capteurs mesurant divers paramètres tels que les vibrations, la température, et la vitesse de rotation. L’IA analyse ces données en temps réel et détecte des schémas anormaux de performance, par exemple une légère augmentation des vibrations. Cette anomalie pourrait indiquer une usure des roulements. Avant que la défaillance ne devienne critique et n’entraîne l’arrêt de la turbine, une intervention est planifiée, permettant ainsi de maintenir la production d’électricité sans interruption.
Bonnes Pratiques
- Investir dans une Infrastructure IoT Solide
- Connectez vos équipements à une plateforme IoT pour faciliter la collecte et l’analyse des données en temps réel. Une infrastructure IoT bien conçue garantit que l’IA dispose des données nécessaires pour effectuer des prédictions précises.
- Former les Équipes à l’Analyse des Données
- La maintenance basée sur l’IA nécessite une collaboration entre les équipes de maintenance et les experts en analyse de données. Assurez-vous que vos techniciens comprennent comment interpréter les alertes et prendre des décisions basées sur les prédictions.
- Suivre et Affiner les Modèles d’IA
- Les algorithmes d’IA doivent être régulièrement mis à jour et ajustés pour s’adapter aux nouvelles données. Le suivi des performances des modèles permet d’améliorer continuellement la précision des prédictions.
==> La maintenance basée sur l’IA est une approche novatrice et prometteuse qui transforme la manière dont les entreprises gèrent leurs actifs. En anticipant les défaillances, elle permet d’optimiser la maintenance, de réduire les coûts et d’augmenter la disponibilité des équipements. Malgré les défis liés à l’investissement initial et à la complexité de mise en œuvre, les bénéfices à long terme en font une stratégie incontournable pour les industries modernes.
Conclusion
En 2024, la combinaison de plusieurs stratégies est souvent la clé d’une maintenance efficace. Les nouvelles technologies, comme l’IA et l’IoT, offrent des possibilités sans précédent pour améliorer la prédiction des pannes et optimiser les opérations. La clé est de choisir la stratégie la plus adaptée à vos équipements et à votre environnement de production.
Quelle stratégie adopterez-vous cette année ?