Dans le monde industriel moderne, comment entretenir des machines industrielles de manière efficace est un enjeu stratégique majeur pour les entreprises. Un entretien optimisé garantit non seulement une productivité et une qualité de production constantes, mais il contribue aussi à la sécurité des travailleurs et à la durabilité des équipements.
Table of Contents
Importance de l’entretien des machines industrielles
a. Un levier clé pour la productivité et la sécurité
L’entretien régulier des machines industrielles est essentiel pour assurer une production fluide et sécurisée. Une maintenance bien planifiée permet de réduire les pannes imprévues, qui peuvent entraîner des arrêts coûteux et perturber l’ensemble de la chaîne de production.
✅ Optimisation du temps de production : Une étude de McKinsey révèle que les arrêts non planifiés peuvent réduire l’efficacité des usines de 15 à 20 %. Un entretien préventif limite ces interruptions et améliore le rendement global.
✅ Réduction des accidents de travail : Les dysfonctionnements des équipements sont une source majeure d’accidents industriels. Selon l’Occupational Safety and Health Administration (OSHA), près de 30 % des accidents en milieu industriel sont liés à un mauvais entretien des machines.
b. Un impact direct sur la durée de vie des équipements
Un programme de maintenance structuré prolonge la durée de vie des machines et préserve leur performance optimale.
🔧 Économie sur les coûts de remplacement : D’après l’Association of Equipment Manufacturers (AEM), une machine bien entretenue peut voir sa durée de vie prolongée de 20 à 40 %, réduisant ainsi les investissements en nouveaux équipements.
🔧 Préservation des performances mécaniques : L’usure naturelle des composants est inévitable, mais une lubrification régulière, des ajustements précis et des contrôles périodiques garantissent une productivité stable et une consommation énergétique optimisée.
Un entretien efficace repose donc sur une stratégie proactive, combinant maintenance préventive, surveillance en temps réel et formation continue des équipes.
1. Comprendre les types de machines industrielles
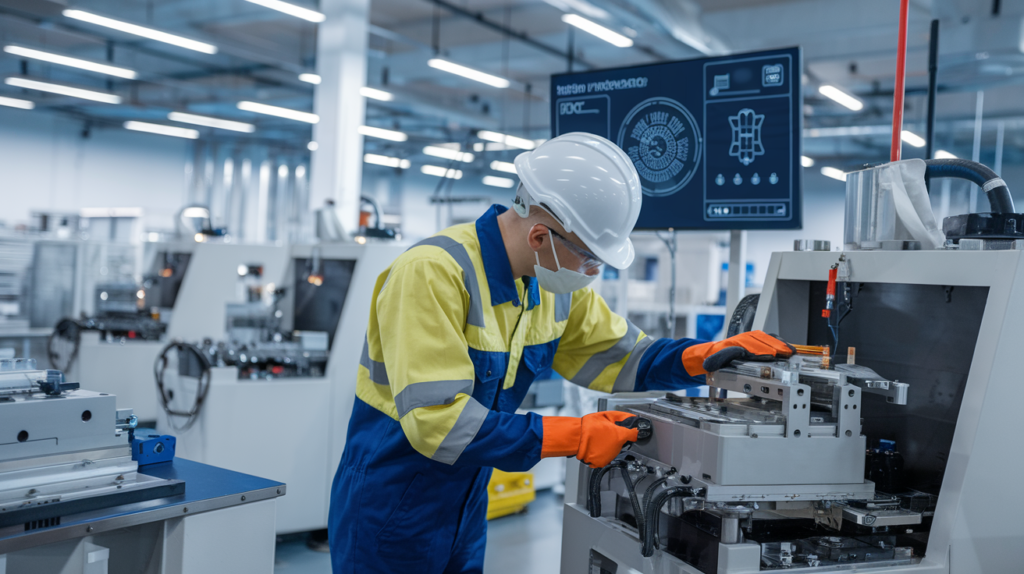
Avant de détailler les stratégies d’entretien, il est crucial de connaître les différents types de machines industrielles et leurs particularités. Chaque catégorie d’équipement présente des exigences spécifiques en termes de maintenance, influençant directement leur performance et leur durabilité.
Classification des machines industrielles
✅ Machines à commande numérique (CNC)
Les machines CNC, utilisées pour l’usinage de haute précision, intègrent des composants électroniques et mécaniques sophistiqués. Leur entretien repose sur :
- La vérification régulière des capteurs et des logiciels de contrôle.
- La lubrification des guides et des vis à billes pour éviter l’usure prématurée.
- La calibration périodique pour garantir une précision optimale.
✅ Machines de production en série
Employées dans les chaînes de montage et les usines automatisées, ces machines nécessitent une maintenance rigoureuse pour éviter tout ralentissement du processus de fabrication. Les points d’attention incluent :
- Le nettoyage et le remplacement des pièces d’usure (courroies, roulements, moteurs).
- Le contrôle des capteurs et automates assurant la synchronisation des tâches.
- La gestion des vibrations et du bruit qui peuvent signaler une anomalie mécanique.
✅ Équipements de manutention
Chariots élévateurs, convoyeurs, ponts roulants et autres systèmes de manutention nécessitent une maintenance axée sur la sécurité et la fiabilité. Les actions essentielles incluent :
- L’inspection des freins, des batteries et des circuits hydrauliques.
- Le contrôle des chaînes, rouleaux et systèmes de levage pour prévenir les risques d’accidents.
- L’étalonnage des capteurs de charge pour éviter les surcharges dangereuses.
Spécificités d’entretien selon le type de machine
Chaque type d’équipement requiert une approche adaptée :
- Machines CNC : Calibration et mises à jour logicielles fréquentes.
- Machines de production : Surveillance des systèmes automatisés et maintenance préventive stricte.
- Équipements de manutention : Vérifications des éléments de sécurité et contrôles hydrauliques réguliers.
Bien comprendre ces classifications permet d’adopter des stratégies d’entretien ciblées, réduisant ainsi les risques de panne et optimisant la productivité des machines.
2. Établir un plan d’entretien préventif
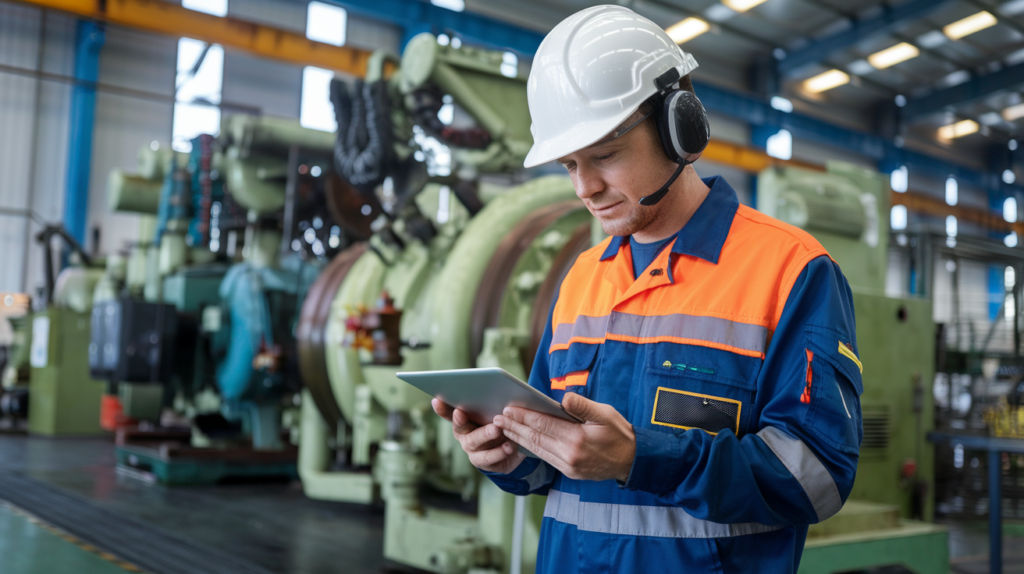
Un plan d’entretien préventif bien structuré est la clé pour assurer la fiabilité et la longévité des machines industrielles. Il permet d’anticiper les pannes, d’éviter les arrêts imprévus et d’optimiser la performance des équipements.
Fréquence des entretiens
La fréquence des opérations de maintenance dépend de plusieurs facteurs : l’intensité d’utilisation, l’environnement de travail et l’importance stratégique de l’équipement. Un plan d’entretien efficace repose sur :
✅ Inspections visuelles quotidiennes : Identification rapide des anomalies visibles (fuites, vibrations anormales, usure des composants).
✅ Nettoyages hebdomadaires : Dépoussiérage, vérification des filtres et élimination des résidus pouvant nuire aux performances.
✅ Vérifications mensuelles des systèmes : Contrôle approfondi des éléments mécaniques et électroniques (capteurs, moteurs, roulements).
✅ Révisions annuelles complètes : Remplacement des pièces d’usure, mise à jour des logiciels de contrôle et recalibrage des équipements.
Checklist d’entretien préventif
Une checklist détaillée permet de standardiser les opérations et d’assurer qu’aucun élément essentiel n’est oublié. Voici quelques points fondamentaux :
📌 Vérifications visuelles et fonctionnelles
- Inspection des niveaux de fluides (huiles, liquides hydrauliques).
- Contrôle des courroies, chaînes et engrenages pour détecter l’usure.
- Test des systèmes de sécurité (boutons d’arrêt d’urgence, capteurs de proximité).
📌 Lubrification et nettoyage
- Graissage des roulements et axes mobiles pour éviter le frottement excessif.
- Nettoyage des systèmes d’aération et de refroidissement pour prévenir la surchauffe.
Exemple réel : Toyota et le Total Productive Maintenance (TPM)
Toyota, leader mondial de l’industrie automobile, a mis en place une stratégie de maintenance préventive appelée Total Productive Maintenance (TPM). Ce système repose sur :
🔹 L’implication des opérateurs dans l’entretien de premier niveau.
🔹 Une approche proactive pour éviter les pannes avant qu’elles ne surviennent.
🔹 L’utilisation d’indicateurs de performance pour mesurer l’efficacité de la maintenance.
En appliquant un plan d’entretien préventif structuré, les entreprises peuvent réduire leurs coûts de maintenance, améliorer la sécurité et prolonger la durée de vie de leurs équipements industriels.
3. Techniques d’entretien spécifiques
L’application de techniques d’entretien précises est essentielle pour assurer la longévité et l’efficacité des machines industrielles. Parmi ces techniques, la lubrification, le nettoyage approfondi et l’utilisation de technologies avancées jouent un rôle clé.
Lubrification des machines
La lubrification est une étape fondamentale pour limiter l’usure et éviter la surchauffe des composants mécaniques.
✅ Choix des lubrifiants adaptés
Le type de lubrifiant doit être sélectionné en fonction des conditions de fonctionnement (température, charge, vitesse). On distingue :
- Huiles minérales et synthétiques : adaptées aux roulements et engrenages.
- Graisses industrielles : recommandées pour les paliers lents et fortement chargés.
- Lubrifiants secs (graphite, PTFE) : idéals pour les environnements où l’huile est proscrite.
✅ Méthodes d’application efficaces
L’efficacité de la lubrification dépend aussi de son mode d’application :
- Manuelle : Utilisation de pistolets à graisse ou burettes pour les petites machines.
- Systèmes centralisés : Application automatique sur des points précis pour les machines complexes.
- Micro-lubrification : Réduction de la consommation tout en optimisant la répartition du lubrifiant.
Nettoyage approfondi
Un entretien efficace passe également par un nettoyage régulier, essentiel pour éliminer les résidus qui pourraient endommager les composants.
✅ Importance du nettoyage régulier
- Évite l’accumulation de poussières métalliques et de résidus huileux.
- Réduit les risques de surchauffe et d’encrassement des circuits hydrauliques.
- Améliore la précision des capteurs et des systèmes électroniques.
✅ Techniques recommandées selon le type de machine
- Aspiration industrielle : Idéale pour les poussières fines et copeaux métalliques.
- Dégraissage à base de solvants : Recommandé pour les machines exposées aux huiles et graisses.
- Nettoyage cryogénique (glace carbonique) : Solution avancée pour éliminer les impuretés sans laisser de résidus chimiques.
Exemple réel : Siemens et son programme de lubrification avancé
Siemens, acteur majeur de l’industrie, a mis en place un programme de lubrification avancé pour ses turbines à gaz. Ce programme repose sur :
🔹 L’utilisation de lubrifiants haute performance réduisant l’usure des composants.
🔹 Des systèmes de dosage précis permettant une application homogène et efficace.
🔹 Une optimisation des intervalles de maintenance, entraînant :
✔ 30% de réduction de la consommation de lubrifiant.
✔ 25% d’augmentation de l’intervalle entre les entretiens majeurs.
En appliquant ces techniques d’entretien spécifiques, les industriels peuvent améliorer la fiabilité de leurs équipements, optimiser leur rendement et réduire leurs coûts de maintenance.
4. Surveillance et diagnostic des machines
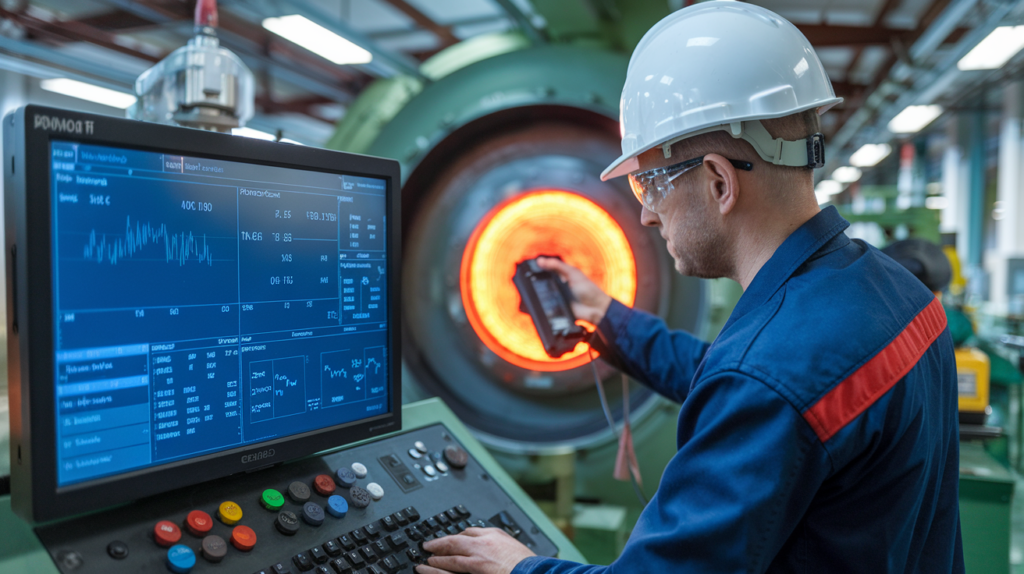
Une maintenance efficace repose sur une surveillance continue et un diagnostic précoce des problèmes afin d’éviter les pannes imprévues et coûteuses. L’intégration de technologies comme l’IoT et l’analyse des données permet d’améliorer la fiabilité et la productivité des équipements.
Mise en place d’un système de monitoring
L’adoption d’un système de surveillance en temps réel permet de détecter les anomalies avant qu’elles ne deviennent critiques.
✅ Utilisation de capteurs IoT pour le suivi en temps réel
Les capteurs IoT (température, vibration, pression, humidité…) offrent :
- Une collecte continue des données sur l’état des machines.
- Des alertes automatiques en cas de dépassement des seuils critiques.
- Une visibilité à distance, réduisant la nécessité d’inspections physiques fréquentes.
✅ Plateformes de supervision connectées
Ces plateformes centralisent les données des capteurs et permettent :
- Une visualisation en temps réel des performances des équipements.
- Un historique des données pour mieux comprendre l’évolution des machines.
- Une intégration avec la GMAO pour planifier les interventions.
Analyse des données pour anticiper les pannes
L’exploitation des données collectées permet de passer d’une maintenance corrective à une maintenance prédictive.
✅ Importance de la maintenance prédictive
- Anticipation des défaillances avant qu’elles ne surviennent.
- Optimisation des ressources, en évitant des interventions inutiles.
- Réduction des temps d’arrêt et amélioration du rendement global des machines.
✅ Techniques de diagnostic avancées
- Analyse vibratoire : Détecte les déséquilibres et les usures prématurées.
- Thermographie infrarouge : Identifie les surchauffes anormales.
- Analyse des huiles : Détecte la présence de particules métalliques révélant l’usure.
- IA et Machine Learning : Prédiction des pannes grâce aux modèles basés sur l’historique des données.
Exemple réel : Caterpillar et son système Cat® Product Link™
Caterpillar, leader des équipements de construction, a développé Cat® Product Link™, un système de surveillance à distance permettant :
🔹 Un suivi précis des performances des machines via des capteurs connectés.
🔹 Une réduction de 40% des temps d’arrêt imprévus, grâce à l’anticipation des défaillances.
🔹 Une augmentation de 15% de la productivité en optimisant l’utilisation des équipements.
Grâce à ces solutions de surveillance intelligente, les entreprises industrielles peuvent considérablement améliorer la fiabilité de leurs équipements et réduire leurs coûts de maintenance.
5. Formation et sensibilisation du personnel
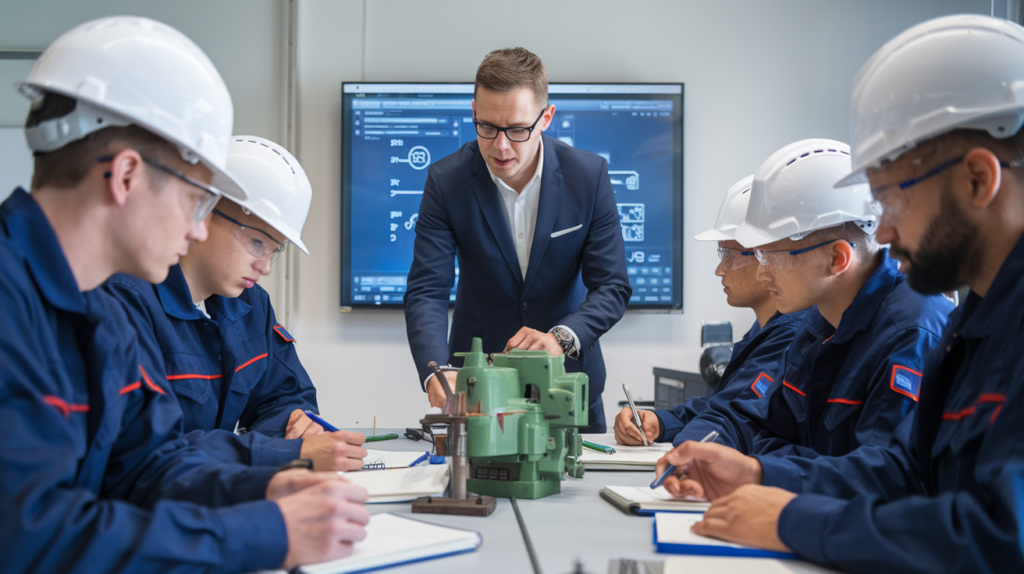
Un personnel bien formé est un maillon essentiel d’une stratégie de maintenance efficace. La formation continue et la sensibilisation aux bonnes pratiques permettent d’éviter les erreurs humaines et d’améliorer la fiabilité des équipements.
Programmes de formation continue
Un bon programme de formation doit être structuré et adapté aux besoins spécifiques de l’entreprise.
✅ Sensibilisation aux bonnes pratiques d’entretien
- Identifier et signaler les signes précoces de défaillance.
- Appliquer correctement les procédures de lubrification et de nettoyage.
- Maîtriser l’utilisation des outils de diagnostic et des logiciels de GMAO.
✅ Formations adaptées aux différents niveaux
- Techniciens de maintenance : Diagnostic des pannes, réparations, réglages.
- Opérateurs de machines : Vérifications de routine, signalement des anomalies.
- Responsables de maintenance : Planification, suivi des indicateurs de performance (KPI).
✅ Utilisation des nouvelles technologies
- Simulations en réalité augmentée (AR/VR) pour des formations immersives.
- E-learning et webinaires interactifs pour une formation flexible et continue.
Création d’une culture de sécurité et de maintenance
Une entreprise qui valorise la sécurité et la maintenance préventive crée un environnement plus productif et plus fiable.
✅ Encourager l’implication de tous
- Intégrer des routines d’entretien quotidiennes dans les tâches des opérateurs.
- Organiser des réunions régulières sur la maintenance et les retours d’expérience.
- Mettre en place un système de remontée des anomalies simple et efficace.
✅ Valoriser la maintenance comme un investissement
- Récompenser les équipes qui respectent les bonnes pratiques d’entretien.
- Mesurer et partager les résultats concrets : baisse des pannes, réduction des coûts.
Exemple réel : SKF et son programme de formation “SKF Certified Maintenance Partner”
SKF, leader mondial dans la fabrication de roulements, a développé un programme de formation avancé qui a permis :
🔹 Une réduction de 30% des coûts de maintenance, grâce à une meilleure anticipation des pannes.
🔹 Une augmentation de 20% de la disponibilité des équipements, en optimisant l’entretien préventif.
🔹 Une montée en compétence des techniciens, leur permettant d’intervenir plus efficacement.
Former et sensibiliser son personnel à la maintenance industrielle est un levier stratégique pour améliorer la productivité et prolonger la durée de vie des équipements.
6. Gestion des pièces de rechange et approvisionnement
Une gestion efficace des pièces de rechange est un facteur clé pour minimiser les temps d’arrêt et garantir la continuité des opérations industrielles. Une mauvaise gestion peut entraîner des retards coûteux et affecter la performance globale de l’usine.
Stratégies d’approvisionnement efficaces
Pour optimiser l’approvisionnement, il est essentiel de mettre en place une gestion intelligente des stocks et des relations solides avec les fournisseurs.
✅ Gestion des stocks de pièces critiques
- Identifier les pièces essentielles susceptibles de provoquer un arrêt de production en cas de panne.
- Déterminer des seuils de stock minimum pour éviter les ruptures.
- Utiliser des systèmes de gestion automatisés (GMAO, ERP) pour suivre les niveaux de stock en temps réel.
✅ Méthodes d’approvisionnement optimisées
- Juste-à-temps (JIT) : Réduction des stocks en ne commandant que lorsque c’est nécessaire.
- Stratégie ABC : Classification des pièces en fonction de leur criticité (A = très critique, B = moyenne, C = non critique).
- Gestion prédictive : Utilisation des données de maintenance prédictive pour commander les pièces avant qu’une panne ne survienne.
Partenariats avec des fournisseurs fiables
Une relation de confiance avec des fournisseurs spécialisés est essentielle pour assurer la qualité et la disponibilité des pièces.
✅ Choisir des fournisseurs réactifs et spécialisés
- Sélectionner des fournisseurs offrant des délais de livraison courts et fiables.
- Travailler avec des partenaires capables de fournir des pièces sur mesure ou en urgence.
✅ Mise en place de contrats d’approvisionnement
- Accords de maintenance avec les fabricants : Certains fournisseurs offrent des contrats de maintenance incluant l’approvisionnement en pièces détachées.
- Stocks consignés : Le fournisseur stocke les pièces dans l’usine et facture uniquement celles utilisées.
Exemple réel : Rolls-Royce et l’intelligence artificielle pour la gestion des pièces
Rolls-Royce a développé un système de gestion des pièces de rechange basé sur l’IA pour son activité de moteurs d’avion. Résultats obtenus :
🔹 Réduction des stocks de pièces de 30%, grâce à une meilleure prévision des besoins.
🔹 Amélioration de 15% de la disponibilité des pièces critiques, réduisant ainsi les délais de réparation.
🔹 Optimisation des coûts d’approvisionnement, évitant les surstocks inutiles tout en garantissant une disponibilité immédiate.
En intégrant des stratégies intelligentes de gestion des pièces de rechange, les entreprises peuvent améliorer leur efficacité opérationnelle et réduire les arrêts imprévus.
7. Documentation et traçabilité des interventions
Une documentation rigoureuse des interventions de maintenance est indispensable pour assurer un suivi efficace, améliorer les pratiques et optimiser la gestion des équipements industriels.
Importance de la documentation
📌 Enregistrement des interventions effectuées
- Chaque opération doit être consignée avec :
✅ La date et l’heure de l’intervention.
✅ La description des actions réalisées (réparations, réglages, tests).
✅ Les pièces remplacées et les consommables utilisés.
✅ Les observations techniques et les recommandations pour la maintenance future.
📌 Avantages d’un bon suivi documentaire
✅ Anticipation des pannes récurrentes en identifiant les problèmes fréquents.
✅ Facilitation des audits et conformité aux normes ISO et réglementations industrielles.
✅ Meilleure planification des interventions en évitant les opérations inutiles.
Utilisation des logiciels de gestion de maintenance (GMAO)
Une GMAO (Gestion de Maintenance Assistée par Ordinateur) est un outil essentiel pour une gestion optimisée.
✅ Centralisation des informations
- Accès rapide à l’historique des interventions sur chaque équipement.
- Planification automatisée des maintenances préventives.
- Suivi des indicateurs de performance (KPI) pour optimiser la maintenance.
✅ Traçabilité améliorée
- Suivi des niveaux de stock des pièces détachées.
- Gestion des demandes d’intervention en temps réel.
- Analyse des causes des pannes et des tendances d’usure.
Exemple réel : La SNCF et la GMAO pour la maintenance ferroviaire
La SNCF a déployé un système GMAO avancé pour la maintenance de ses trains. Résultats obtenus :
🔹 Réduction de 30% des retards liés aux interventions de maintenance.
🔹 Augmentation de 15% de la disponibilité des trains grâce à un suivi optimisé.
🔹 Amélioration de la réactivité des équipes techniques, réduisant le temps d’immobilisation du matériel roulant.
👉 En intégrant une documentation structurée et un outil GMAO performant, les entreprises industrielles peuvent gagner en efficacité, réduire les coûts et prolonger la durée de vie de leurs équipements.
Conclusion
Dans un environnement industriel de plus en plus compétitif, l’adoption d’une approche proactive de la maintenance n’est plus une option, mais une nécessité. Les entreprises qui investissent dans l’optimisation de leurs pratiques d’entretien des machines industrielles seront mieux positionnées pour relever les défis futurs, améliorer leur productivité et assurer leur croissance à long terme.
Il est temps pour chaque entreprise d’évaluer ses pratiques actuelles d’entretien des machines industrielles et d’élaborer un plan d’action pour les améliorer. Cela peut commencer par une analyse approfondie des processus existants, suivie de l’identification des domaines d’amélioration prioritaires. En mettant en œuvre progressivement ces meilleures pratiques, les entreprises peuvent s’attendre à des gains significatifs en termes d’efficacité opérationnelle, de réduction des coûts et d’amélioration de la qualité.
L’avenir appartient aux entreprises qui sauront transformer leur approche de l’entretien des machines industrielles en un véritable avantage concurrentiel. Commencez dès aujourd’hui à mettre en place ces pratiques d’entretien efficaces pour assurer la pérennité et la performance de vos équipements industriels.