En 2025, une gestion inefficace des équipements industriels est l’une des principales causes de pannes, entraînant des coûts élevés et des interruptions de production. Pourtant, des entreprises comme Schneider Electric ont réduit leurs temps d’arrêt de 15 % grâce à une approche digitalisée et optimisée.
Pourquoi la gestion des équipements industriels est-elle cruciale ?
🔹 Coûts cachés : Chaque panne non anticipée peut coûter des milliers d’euros par heure aux industries manufacturières.
🔹 Vieillissement des machines : En Europe, une grande partie des équipements industriels a plus de 15 ans, augmentant les risques de défaillances.
🔹 Exigences réglementaires : Les normes ISO 55000 et les directives européennes récentes imposent une traçabilité numérique accrue.
Vers une gestion optimisée des équipements industriels
L’intégration des capteurs IoT, des GMAO intelligents et des jumeaux numériques révolutionne la gestion des équipements industriels. Ces technologies permettent une surveillance en temps réel, une maintenance prédictive et une allocation efficace des ressources, transformant ainsi la gestion des actifs en un véritable levier de compétitivité.
Les Enjeux de la Gestion des Équipements Industriels en 2025
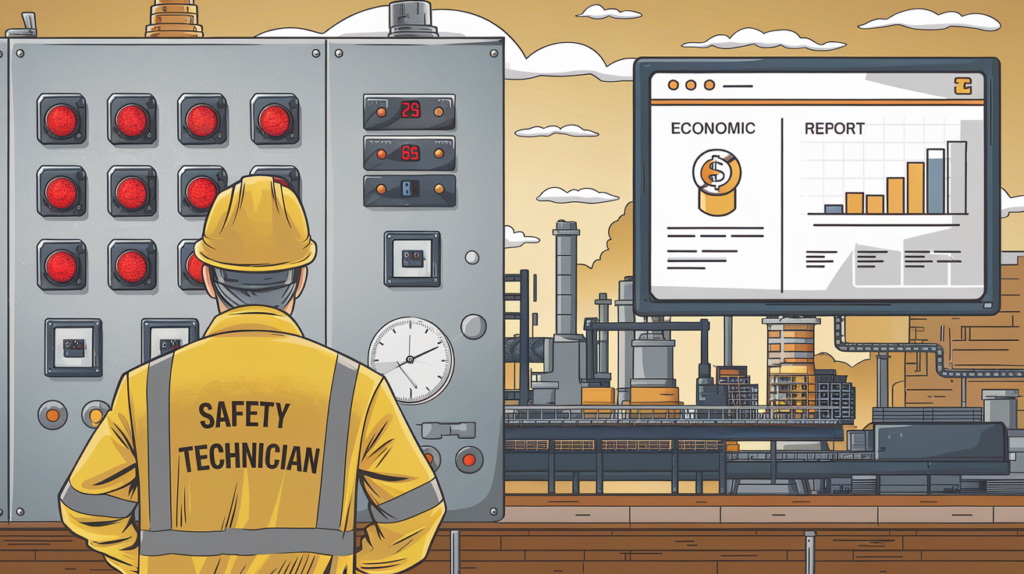
En 2025, la gestion des équipements industriels est confrontée à des défis majeurs qui influencent directement la performance et la compétitivité des entreprises.
a. Défis opérationnels
- Temps d’arrêt imprévus : Les pannes non planifiées peuvent coûter jusqu’à 1,5 million d’euros par an pour une PME manufacturière, selon une étude de PwC. Par exemple, une interruption de 8 heures sur une chaîne d’embouteillage chez Coca-Cola, due à une défaillance du convoyeur, a entraîné une perte estimée à 120 000 €.
- Maintenance réactive : Actuellement, 68 % des interventions de maintenance sont correctives, contre seulement 20 % en maintenance prédictive, d’après Gartner. Cette approche réactive augmente les risques de pannes et les coûts associés.
b. Problématiques technologiques
- Silos de données : Environ 60 % des informations des machines sont stockées dans des systèmes non connectés, limitant la visibilité et l’analyse globales (Capgemini).
- Interopérabilité limitée : L’intégration de machines anciennes, datant des années 1990, avec des protocoles modernes tels que OPC UA ou MQTT, pose des défis significatifs en matière de compatibilité et de communication.
c. Durabilité et Responsabilité Sociétale des Entreprises (RSE)
- Consommation énergétique : Des équipements mal entretenus peuvent augmenter les émissions de CO₂ de 22 %, selon l’ADEME. Cette surconsommation énergétique va à l’encontre des objectifs de durabilité et des engagements RSE des entreprises.
Pour surmonter ces défis, l’adoption de technologies telles que les capteurs IoT, les systèmes de gestion de maintenance assistée par ordinateur (GMAO) intelligents et les jumeaux numériques est essentielle. Ces outils permettent une surveillance en temps réel, une maintenance prédictive et une meilleure allocation des ressources, transformant ainsi la gestion des actifs en un avantage concurrentiel.
5 Stratégies pour une Gestion Optimisée en 2025
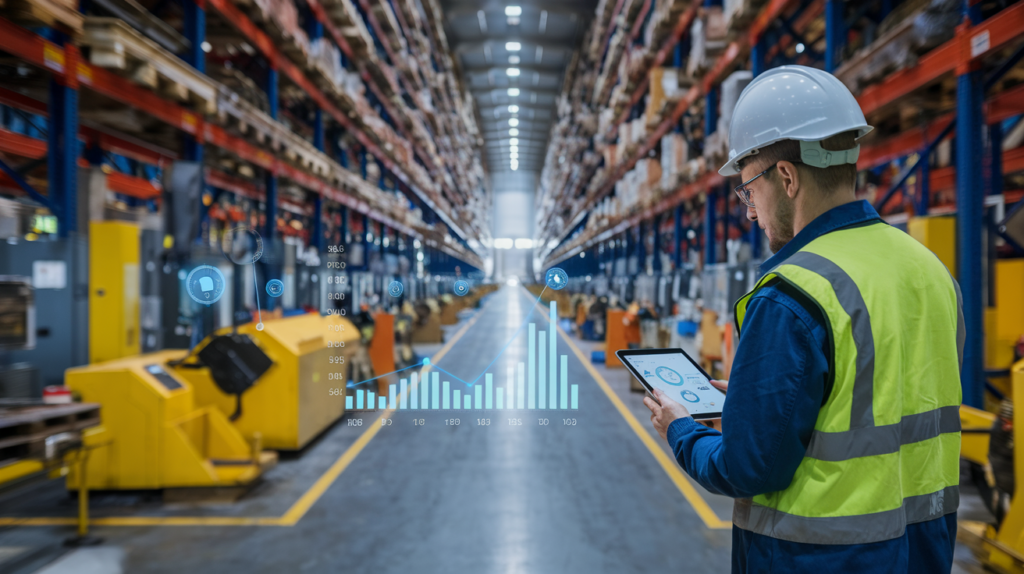
Face aux défis opérationnels et technologiques, une gestion efficace des équipements industriels repose sur des stratégies avancées combinant digitalisation, maintenance intelligente et formation. Voici les leviers incontournables pour optimiser votre gestion en 2025.
1. Digitalisation via l’IoT Industriel
L’Internet des Objets (IoT) transforme la maintenance en permettant une surveillance en temps réel et une anticipation des pannes.
🔹 Capteurs connectés pour une détection avancée
- Vibrations : L’utilisation d’accéléromètres Emerson CSI 2140 sur les compresseurs industriels permet d’identifier les déséquilibres et usures précoces, réduisant ainsi les risques de panne critique.
- Température : Les caméras thermiques FLIR A700, déployées sur les fours industriels, détectent les variations anormales de chaleur, évitant ainsi les surchauffes et les pertes énergétiques.
🔹 Protocoles clés pour une intégration fluide
- MQTT (Message Queuing Telemetry Transport) : Ce protocole léger et rapide permet une transmission efficace des données en basse latence, idéale pour la surveillance de pompes en temps réel ou la gestion d’alertes instantanées.
- OPC UA (Open Platform Communications Unified Architecture) : Standard incontournable pour la sécurisation et l’interopérabilité des échanges entre machines hétérogènes, notamment pour l’intégration d’équipements anciens avec des solutions modernes.
2. Adoption de GMAO Nouvelle Génération
Les logiciels de Gestion de Maintenance Assistée par Ordinateur (GMAO) évoluent avec des fonctionnalités avancées qui automatisent et optimisent la maintenance.
🔹 Fonctionnalités indispensables
- Maintenance prédictive : Les algorithmes d’intelligence artificielle, notamment Random Forest, permettent d’anticiper les défaillances avec une précision supérieure à 90 %, réduisant les interventions d’urgence et prolongeant la durée de vie des équipements.
- Gestion des stocks automatisée : Intégration d’API pour un réapprovisionnement automatique des pièces détachées. Par exemple, les pièces SKF peuvent être commandées via SAP Ariba, garantissant une disponibilité continue.
🔹 Top solutions GMAO pour 2025
- IBM Maximo : Recommandé pour les grandes industries comme l’énergie et la pharmaceutique, ce logiciel intègre l’IA et l’IoT pour une gestion avancée des actifs.
- Fiix by Rockwell : Une solution cloud accessible à 150 €/utilisateur/mois, adaptée aux PME cherchant à digitaliser leur maintenance sans infrastructure lourde.
3. Jumeaux Numériques (Digital Twins)
L’adoption des jumeaux numériques permet de simuler et d’optimiser le cycle de vie des équipements avant même qu’ils ne rencontrent de problèmes.
🔹 Cas d’usage concrets
- Simulation de l’usure des turbines : Siemens SGT-800 utilise un double numérique pour prévoir l’évolution des contraintes mécaniques et ajuster les plans de maintenance de façon proactive.
- Optimisation des cycles de maintenance : General Electric a réduit ses coûts de maintenance de 25 % en exploitant la simulation des scénarios de défaillance et l’analyse prédictive.
4. Formation aux Outils Numériques
L’efficacité d’une stratégie de gestion des équipements industriels repose aussi sur les compétences des équipes techniques.
🔹 Solutions innovantes pour une montée en compétences rapide
- Réalité virtuelle : L’usage du casque Oculus Quest 3 permet de former les techniciens aux interventions complexes via des simulations immersives, limitant les risques d’erreurs sur le terrain.
- Plateformes e-learning : Des outils comme Docebo offrent des parcours de formation personnalisés et interactifs, facilitant l’adoption des nouvelles technologies en maintenance.
5. Approche Lean et TPM (Total Productive Maintenance)
L’application des principes du Lean Manufacturing et de la TPM optimise la performance des équipements tout en impliquant les opérateurs.
🔹 Bonnes pratiques pour une maintenance proactive
- Méthodologie 5S : Structurer les zones de maintenance en réduisant le gaspillage et en facilitant l’accès aux outils essentiels.
- Maintenance autonome (AM – Autonomous Maintenance) : Former les opérateurs à effectuer des contrôles quotidiens et des actions préventives pour limiter les pannes imprévues.
==> La gestion optimisée des équipements industriels en 2025 repose sur une convergence entre technologies avancées, automatisation et montée en compétences. L’intégration de l’IoT, des GMAO intelligentes et des jumeaux numériques permet d’améliorer la disponibilité des équipements, de réduire les coûts et d’augmenter la productivité. Les entreprises qui sauront adopter ces stratégies auront un avantage concurrentiel majeur.
Technologies Clés pour 2025
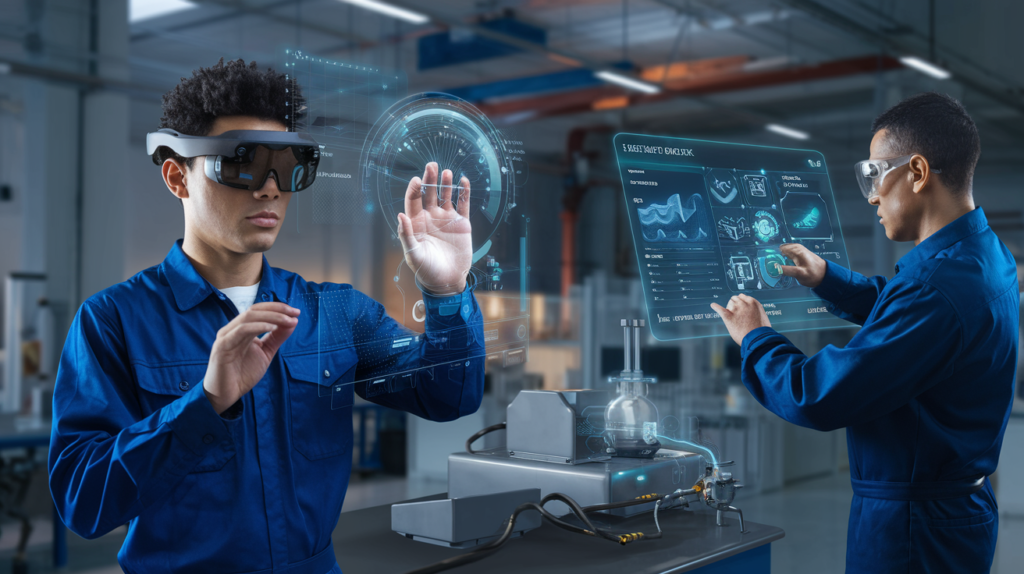
En 2025, plusieurs technologies clés transforment la gestion des équipements industriels, améliorant l’efficacité, la traçabilité et la maintenance.
a. Intelligence Artificielle Générative
- ChatGPT-4 : Des entreprises comme Schneider Electric utilisent des chatbots basés sur ChatGPT pour améliorer la productivité des employés et les interactions avec les clients. aibusiness.com
- AutoML : Les algorithmes d’apprentissage automatique automatisé permettent d’adapter en temps réel les modèles prédictifs, optimisant ainsi la maintenance préventive et réduisant les temps d’arrêt imprévus.
b. Blockchain pour la Traçabilité
- Applications :
- Historiques de maintenance inviolables : Bien que la plateforme TradeLens développée par Maersk et IBM ait été interrompue en 2023, la technologie blockchain continue d’être explorée pour assurer une traçabilité sécurisée des opérations de maintenance dans diverses industries. maersk.com
- Suivi des pièces reconditionnées : Des entreprises comme Bosch Rexroth utilisent la blockchain pour garantir l’authenticité et le suivi des composants reconditionnés, assurant ainsi leur qualité et leur conformité aux normes.
c. Edge Computing
- Avantages :
- Traitement des données localement : L’utilisation de passerelles telles que Siemens MindConnect permet de traiter les données directement sur site, réduisant la latence à environ 20 millisecondes et améliorant la réactivité des systèmes de surveillance.
- Exemple : Dans les mines de Rio Tinto, le edge computing est utilisé pour la surveillance en temps réel des convoyeurs, permettant une détection rapide des anomalies et une maintenance proactive.
d. Réalité Augmentée (AR)
- Casques HoloLens 2 :
- Affichage des schémas techniques : Les techniciens peuvent visualiser des schémas et des instructions en surimpression lors des interventions, facilitant ainsi les réparations complexes.
- Assistance à distance : Grâce à la visioconférence intégrée, les experts peuvent fournir un support en temps réel aux techniciens sur le terrain, améliorant l’efficacité et réduisant les erreurs.
L’intégration de ces technologies clés en 2025 permet aux industries d’améliorer la gestion de leurs équipements, d’accroître la productivité et de garantir une traçabilité optimale.
Études de Cas Concrets
Voici deux études de cas illustrant l’application de technologies avancées dans la gestion des équipements industriels :
a. Michelin (Secteur Manufacturier)
- Problème : Une part importante du temps de production était perdue en raison de réparations urgentes sur les presses à pneus.
- Solution : Michelin a déployé des capteurs IoT pour surveiller en temps réel l’état des équipements et a intégré ces données dans un système de gestion de maintenance assistée par ordinateur (GMAO).
- Résultats : Cette approche a permis une réduction significative des pannes et une amélioration de l’efficacité opérationnelle.
b. Sanofi (Secteur Pharmaceutique)
- Problème : Sanofi faisait face à des défis de conformité avec la FDA concernant les processus de stérilisation.
- Solution : L’entreprise a mis en place des jumeaux numériques pour simuler les cycles de stérilisation, permettant d’optimiser les processus et d’anticiper les éventuelles non-conformités.
- Résultats : Cette initiative a conduit à une réduction notable des audits correctifs et à une amélioration de la conformité réglementaire.
Ces exemples démontrent l’impact positif de l’intégration de technologies telles que l’IoT et les jumeaux numériques dans la gestion des équipements industriels.
Tendances Futures (2025-2030)
Entre 2025 et 2030, plusieurs tendances émergentes transformeront la gestion des équipements industriels :
IA Auto-Adaptative
Les algorithmes d’intelligence artificielle deviendront capables d’ajuster automatiquement les seuils d’alerte en fonction des conditions opérationnelles, améliorant ainsi la maintenance prédictive. Par exemple, des plateformes comme Google Vertex AI facilitent le développement de modèles d’IA adaptatifs pour diverses applications industrielles.
Cobots de Maintenance
Les robots collaboratifs, ou “cobots”, joueront un rôle croissant dans les tâches de maintenance. Des entreprises telles qu’Universal Robots développent des cobots capables d’effectuer des inspections autonomes, réduisant ainsi la charge de travail humaine et améliorant la précision des diagnostics.
5G Industriel
La connectivité ultra-rapide offerte par la 5G permettra aux usines intelligentes de bénéficier de communications en temps réel entre machines et systèmes. Des solutions comme le réseau privé Nokia DAC offrent une infrastructure dédiée pour des applications industrielles critiques, améliorant la réactivité et la flexibilité des opérations.
Gestion Écologique
Les préoccupations environnementales inciteront les industries à adopter des logiciels capables de calculer l’empreinte carbone des interventions de maintenance. Par exemple, Dassault Systèmes propose des outils pour évaluer et réduire l’impact environnemental des opérations industrielles, contribuant ainsi à des pratiques plus durables.
Ces tendances reflètent une évolution vers des opérations industrielles plus intelligentes, autonomes et respectueuses de l’environnement.
FAQ
Q1 : Quel est le coût moyen d’un système IoT pour la gestion des équipements ?
R : Le coût d’un système IoT industriel varie en fonction de la complexité et de l’échelle du déploiement. Selon une étude, pour 100 000 objets connectés déployés, l’entreprise déboursera en moyenne 1,25 dollar par mois et par appareil. Les dépenses sont réparties entre les réseaux de communication (33 à 50 % du budget total) et la gestion des capteurs à distance.
Q2 : Comment intégrer des machines anciennes dans un système moderne ?
R : Pour connecter des machines anciennes à des systèmes modernes, il est possible d’utiliser des capteurs rétrocompatibles et des passerelles IoT. Par exemple, des capteurs peuvent être installés sur des machines plus anciennes pour surveiller des paramètres clés, et les données collectées peuvent être transmises via des passerelles IoT vers des systèmes de gestion modernes.
Q3 : Quels sont les avantages de la maintenance prédictive dans la gestion des équipements industriels ?
R : La maintenance prédictive permet d’anticiper les défaillances des équipements en analysant des données en temps réel, ce qui réduit les temps d’arrêt non planifiés. Selon une étude de Senseye, les industries manufacturières subissent en moyenne 27 heures d’arrêt par mois, avec un coût horaire de 450 000 euros. La maintenance prédictive peut significativement réduire ces coûts en prévoyant les pannes avant qu’elles ne surviennent.
Q4 : Comment la 5G influence-t-elle les usines intelligentes ?
R : La 5G offre une connectivité ultra-rapide et une faible latence, ce qui est essentiel pour les usines intelligentes. Elle permet une communication en temps réel entre les machines, les capteurs et les systèmes de contrôle, améliorant ainsi l’efficacité opérationnelle et la flexibilité de la production. Des solutions comme le réseau privé Nokia DAC fournissent une infrastructure dédiée pour des applications industrielles critiques.
Q5 : Qu’est-ce qu’un jumeau numérique et comment est-il utilisé dans l’industrie ?
R : Un jumeau numérique est une réplique virtuelle d’un objet physique ou d’un système. Dans l’industrie, il est utilisé pour simuler, analyser et optimiser les performances des équipements. Par exemple, une entreprise peut créer un jumeau numérique d’une turbine pour surveiller son état en temps réel, prévoir les besoins de maintenance et améliorer son efficacité opérationnelle.
Conclusion
En 2025, la gestion des équipements industriels nécessite une intégration harmonieuse entre technologies avancées et stratégies éprouvées. L’adoption de solutions telles que l’Internet des Objets (IoT), l’Intelligence Artificielle (IA) et les jumeaux numériques permet de réduire les coûts, de se conformer aux normes en vigueur et d’accroître la productivité.
Pour approfondir ces thématiques, nous vous invitons à consulter notre guide comparatif des 10 meilleurs outils de gestion industrielle en 2025. Ce guide offre une analyse détaillée des solutions les plus performantes du marché, adaptées à divers besoins industriels.
De plus, ne manquez pas notre webinaire exclusif intitulé “Maintenance Connectée : Optimisez la Performance et Prévoyez l’Avenir”, qui se tiendra prochainement. Ce webinaire abordera les dernières tendances en matière de maintenance connectée et fournira des clés concrètes pour améliorer vos processus industriels.
En combinant ces ressources, vous serez mieux équipé pour transformer la gestion de vos actifs en un avantage concurrentiel durable.